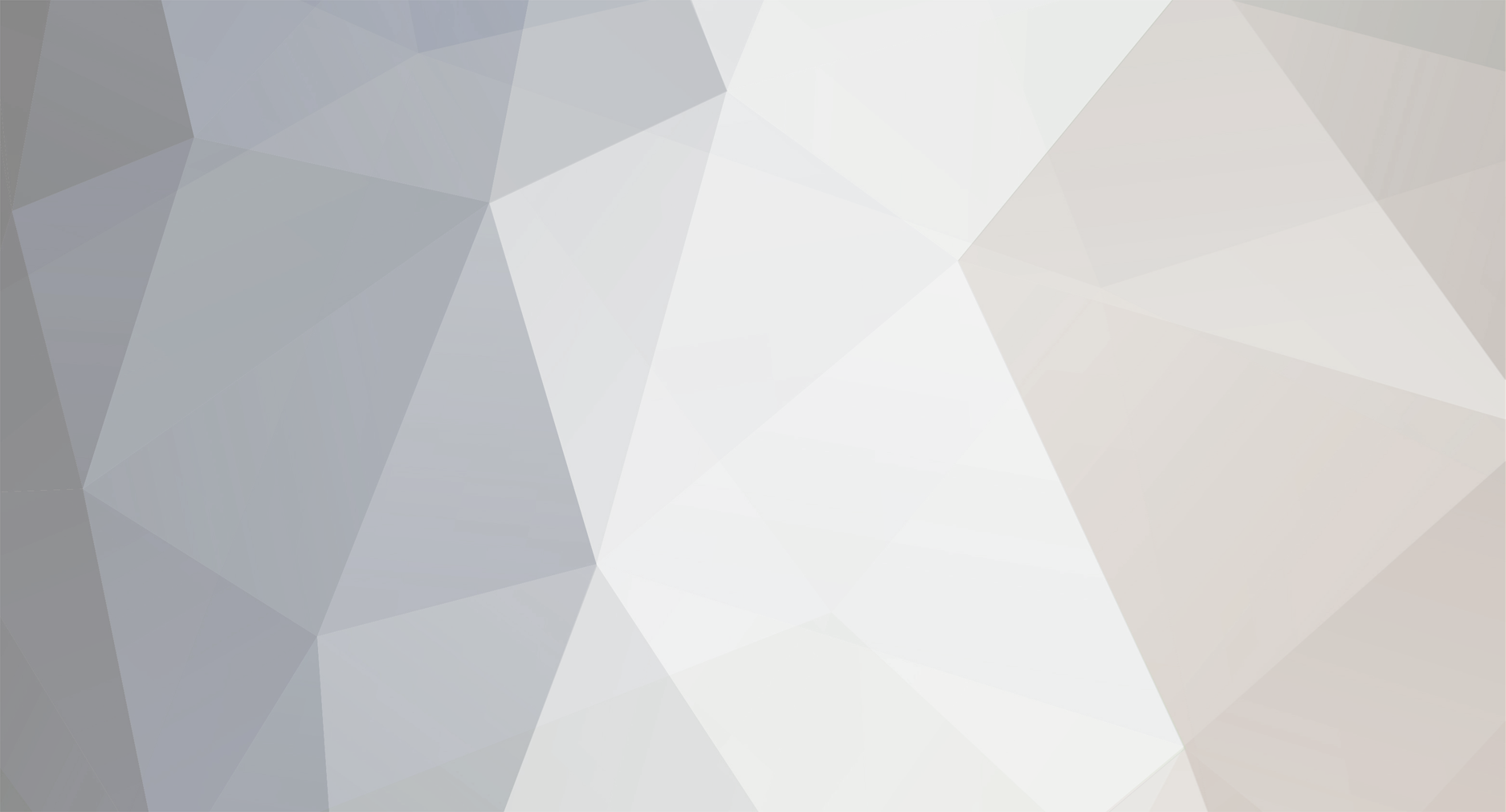
David Herbert
Members-
Posts
926 -
Joined
-
Last visited
-
Days Won
9
Content Type
Profiles
Forums
Gallery
Blogs
Events
Articles
Store
Downloads
Everything posted by David Herbert
-
I have an idea that SG iron was invented / first used just after WW1 but I probably should have looked it up before writing this! David
-
May be they were inspired by the WW2 Malta camoflage scheme but got carried away. David
-
Steve, I think that I would try to exactly reverse the forces that bent the shaft in the first place: make a sleive/bending handle for the part of the shaft that was protected by being clamped inside the bit that drives it, and support it only where the bearings supported it. If you heat it it will only bend where the heat is, instead of gradually between the end of the sleive and the bearing. Fortunatly it is not very bent and is probably fairly soft steel so you are very unlikely to crack it. I think you will be suprised how easy it is to get it right. Mind you that press does look tempting... David
-
Looks to me like the idea was that the nut was bound to wear so lets make it easy to remake it with primative facilities and no machining. Briliantly simple to just block up anywhere the white metal could run out and heat up the nut housing till the old thread melted, add a bit more to make up for the wear, let it cool, clean it and put it all back together. The one problem is stopping it sticking to the screw but if lamp black works, great. "My steering has too much slack in it, I must find a plumber!" David
-
Looks like there is a seccond one beside it in one photo. David
-
Loading tracked vehicles
David Herbert replied to David Herbert's topic in Transporters & Wreckers (All Nations)
Here's another one, that has been posted on Russian Trucks Forum. I think this guy is very brave but it does show what can be done if the driver and the man on the truck work together properly. It also helps having no fear! The bed of that truck is not exactly oversize and is a long way off the ground. David -
hmvf news Adding Videos to Posts
David Herbert replied to Marmite!!'s topic in About HMVF & Forum Rules
Briliant ! At last some instructions that a normal person can understand. Now I will test it to see if I can make it work too. Thanks, David Some time later: Amazing... It worked for me! -
These comments relate to auto boxes in general, not to your truck specificaly, but auto boxes need to know how hard the vehicle is being driven as well as how fast it is going so that they can decide which gear to be in and how aggresively to engage the next gear. There will be signals from both the input and the output shafts of the gearbox to tell it the engine and road speeds and it will find out how hard the engine is working from the throttle position and posibly from inlet manifold pressure. If either these last two are giving wrong signals the result is either too soft or too hard shifts. Modern cars use the computer to set the engine revs to exactly the speed needed for the new gear so the clutches can be engaged without any shock or sliping but older car and most truck and AFV autos do it the old fashioned way and engage them regardless so they have to adapt to the wildly varying conditions from one gear change to another. It sounds to me as if your box thinks you are driving flat out all the time. Kick down is a rather seperate subject as it is to make the gearbox go into the lowest safe gear immediatly and as you say is usually engaged at almost full throttle only. This is seperate to the need to know how hard the engine is working. Hope this helps a bit. David
-
Nice bit of soldering Dan. I would have worried that the brass plates would have moved a bit while they were being soldered but you obviously got it right. I assume that the plain copper pipe is an overflow from inside the top of the header tank. I do hope that you can find an engine before you get a chance to make one from scratch but at the rate you are going I wonder! Do you have any decent photos of the correct engine so we know what to look out for? David
-
Alternative use for a Morris Quad winch
David Herbert replied to Paul Grimshaw's topic in British Vehicles
" I put some heavy gear oil in" Please don't say that you used an EP grade oil. It will attack the bronze very quickly and the surface will break up within weeks. David -
Dan, The header tanks look great! Not sure about the plywood core plates though - they will be a bugger to solder to I reckon. Best wishes David
-
I would be concerned that the cracking is more extensive than you can see. It is obviously caused by fatigue from the clutch being pulled in and out rather than the torque and if that bit cracked how far behind is the rest? Are you sure it is weldable? I wonder if it is quite a high carbon steel to give an almost spring steel and if so you could be causing more cracks by welding. If it is easy to file it may well be weldable in which case I would consider cutting out the centre about an inch outside the bolts so as to get away from the area that has failed. Weld a disk of say 10mm mild steel in flush with the front (concave) face with a nice big mig weld on the inside first, then grind out the joint on the front and fill with more mig weld. Then the inside face of the new bit can be machined back to the correct shape to fit on the flange having centred it from the outside of the pressing. The holes can be drilled using the flange as a guide. The centre will then be a little thicker than originaly so should be tougher. It shouldn't be too hard to find someone with a big enough lathe to skim and bore the new centre and if set up carefully it will be dead true. If on the other hand it is hard I think I would tend to leave it and drive gently. Good luck David
-
Cromwell Track links, A big thanks to Adrian for his help!!
David Herbert replied to Old Git's topic in Tracked vehicles
That is pretty impressive. I wish I was that good with autocad! Did you include the tapers that allow the pattern to be removed from the mould? If you plan to make them in metal, full size or 1/6, it will be much easier if there is draw as in the real ones. I expect you know that there was an earlier version of that track with the three recesses in the road face of the grouser joined up to form a deep slightly wiggly groove all the way accross the running face. This gave more grip and was lighter but wore down quicker and rapidly gave way to the pattern you have made. Please tell us how the 3D printing works and how you will translate this into metal. David -
seen this one before?
David Herbert replied to Steifbear's topic in Transporters & Wreckers (All Nations)
I think that the surrounds of the radiator grilles started life as the tops of two doors from some 40s or 50s car - very creative. Who can recognise the car? David -
How far is he going with that? Looks like a long road! David
-
Terry, As far as I can see the core of your oil pump drive casting is not positively fixed in the mold. Is that true and so what holds it from moving? It obviously cast ok but I can't see how! I think that one thing that makes your patterns look so good is the precission of the joints. I presume that you machine cut the individual pieces as far as you can and use very well seasioned timber so it doesn't move after it has been cut. Your attention to detail is quite inspiring, I think you should have your own thread called: How to do things that other people aspire to, and really well. The etched plates are beautiful too. When you have the engine done, will you be making the rest of the Lombard tractor to go with it or will it be an exhibit in its own rite? David
-
The sign leaning against the front of Bovvies AC might be a hint to the mark! Yes they are rather impressive, and a much better driving position than many armoured cars of the period which tend to be like driving a pillar box. They are indeed built out of Matador bits with as few mods as possible. One effect of this is that (I believe) the transfer box is standard Matador but turned round to accept the drive shaft coming from the engine at the back. As a result the AC normaly drives only on the front axle, engaging four wheel drive brings in the rear as well. I have briefly driven the IWM Dorchester ACV which had not at that point been restored, only 'got going'. It was lovely to drive, very forgiving and not at all intimidating. Also much more responsive than I expected. I enjoyed that day! David
-
restoration CVRT Sabre Turned Around ...
David Herbert replied to PDonovan's topic in Blogs of MV restorations
Nice bit of shunting and camera work. Its not easy to do a job and film it yourself too - you keep forgeting to move the camera or turn it on and off. The thing that most impresses me is that in an obviously built up area no one was sufficently curious to come and watch - does this happen every day on your estate ? David -
It is I think a modification of an extremly expensive off road buggy for disabled people. That is itself a development of the self balancing two wheeled electric buggy that you stand up to drive, holding onto handlebars with which you steer it (can't think of the name). You lean back or forwards to tell it to go or stop and the computer sorts out the ballancing to keep the wheels under the C of G. As you can see in the photo there is no way it can be ballanced with the guy on the back so I think that he has been photoshoped on. I don't think that the creator was American somehow! David
-
I think he used a Pattern Makers lathe. They have a flexible section in the bed that you set to the radius that you want. If turning a small radius bent cylinder you have to keep the speed down or it will thrash about a bit. Hope this helps David
-
From your photos it looks like the drum on the NZ starter shaft is considerably eccentric to the shaft. How would that work? Presumably it is not some sort of harmonic ballancer? David
-
LARCs moved from Pounds yard.
David Herbert replied to Rick W's topic in Battlefields, museums, monuments and memorials.
I think you will find that GM 6-71s are convertable from LH turn to RH turn and LH supercharger or RH. The blocks are machined with all the holes and pads for any configuration and are then built up as needed. Most parts are not actually handed, just assembled differently, and almost everything is still available commercially. The biggest mistake people make is not removing plugs from oilways and replacing them where they need to be. Vickers got into trouble with the Shervic project because they were using Sherman M4A2 bits to build heavy crawler tractors but only needed single engines. As they were starting with Sherman twin sets they had to convert half the engines they had to the opposite hand. No one had told them about the plugged oilways. There was actually a GM quad set with four 6-71s driving into a gear case and one shaft out to drive a pump or generator or similar but I think that the LARC has one at each wheel station rather than four in a clump. David -
Your method of establishing TDC assumes that the cylinder C/L goes through the crank C/L. On older engines it was not uncommon for the cylinder to be offset a bit so that the force of combustion pressed more verticaly on the crank, reducing side thrust on the piston. The forces on the compression stroke were much less so a compromise could be made. An offset would make a difference to TDC as the crank would need to be turned towards the cylinder so that a line drawn through the crankshaft C/L, through the crank C/L and through the gugeon pin C/L was straight. Not a big difference but measurable. Idealy of course you put a depth stop through a spark plug hole and turn the crank either way till the piston comes up and meets the stop. Mark both the stop points on the flywheel and half way between is TDC. However this will be a little hard in this case! It seems to me that with the changes to compression ratio from the different bore, better fits of valves and pistons and better petrol, any original specs are not going to be ideal anyway. To a large extent you will be able to compensate with the ign timing anyway. It is nice to see the project moving forward, I think your public feel involved as we are treated to a bolt by bolt account rather than "this is what I started with, here it is done". Thank you for the considerable time that must go into posting each new development. David