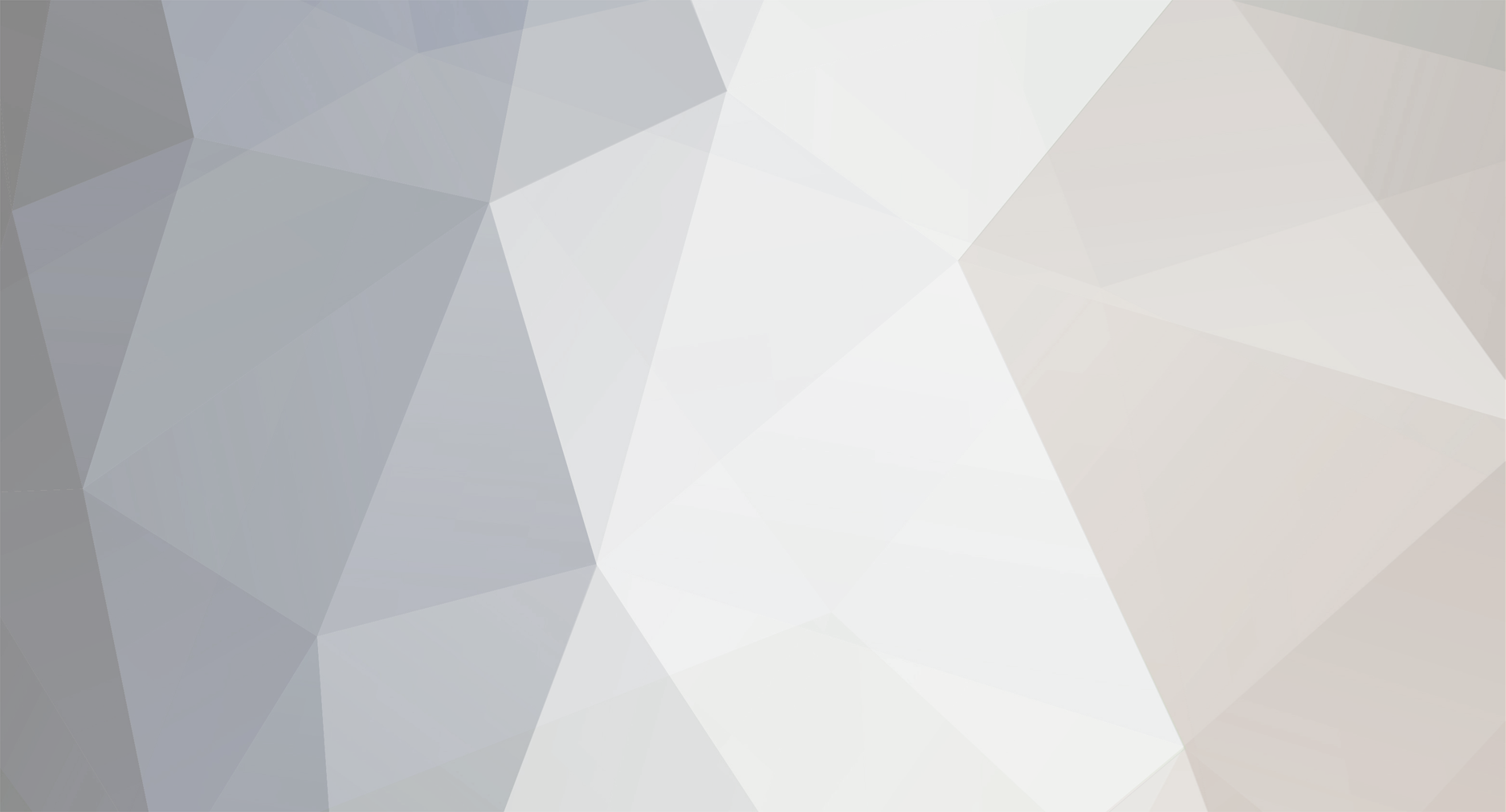
Tamber
Members-
Posts
236 -
Joined
-
Last visited
Content Type
Profiles
Forums
Gallery
Blogs
Events
Articles
Store
Downloads
Everything posted by Tamber
-
I only had a little cutting torch, so I only needed a little fire extinguisher; that's how it works, right? I did my best to block any fire or molten metal reaching wiring (or rubber fuel line; that would have been exciting!) with a scrap piece of ally plate. Fire extinguisher was kept close to hand at all times, too. I'm trying to keep my spirits up and keep going at it; as long as I'm still taking steps forward, even little ones, I'm still making progress. It's definitely helping that the days are getting longer, and the weather has stayed nice for a few days.
-
So! I did indeed get to roll my generator and grinders out; I got what I could with the 7", but it turned out to be too bulky and I switched to the 4"... which turned out to still be too tricky to get in at some parts. And that resulted in me finally collecting a sufficiently circular Tuit, then heading up to the local hobbyweld supplier for a bottle of oxygen. (I have had a small set of burning gear for *years*, but never gotten around to heading out and picking up the oxy cylinder. ) This is where I left off after last week: Today, however, there was fire; and progress happened. I'm now getting much closer to having sufficient grot removed that I can start putting metal back in, which will be an amazing feeling; because as it is, I feel more like the scrap-man, I'm doing that much cutting! And the pile of scrap from these last two outings: I'm getting closer and closer to having that new bit of box section welded in place; whereupon I can see what space I have left to wiggle a rubber body-mount into, in place of the original, and will have a place to start building the floor back out from. Thankfully, the floor is pretty solid for the most part; around the rear and side of the passenger seat is where it's the worst, but there's enough of it left that I can work back from. I'll claw this back, one piece at a time! Might not be quick, nor particularly pretty; but it'll be solid. I can always come back and re-do the uglier parts in the future, when I've gotten better at the job and improved my skill. But, for now, "ugly & solid" is better than "gaping hole"
-
Just chiming in with an agreement on this: Generally, I believe, the harder the material you're drilling, the shallower the point/included angle. It really isn't always as easy and clear-cut as one would like with spark tests, test-drilling, etc... It's almost like the material's out to get you, sometimes! (You'd think, by now, I'd be able to recognise AR plate vs mild steel plate; working in a shop that does a lot of both, but I have mostly learnt to recognise it by how it nigh-instantly dulls the bit when I start drilling into it, after profiling it out, etc, etc. ) Good to know the methods for spotting armour plate, though; just in case!
-
Alrighty then! Since I'm doing my best to power on through burn-out at work sapping my will to live work on this hulk, I've dragged myself back onto the forum! The driver's door has been re-re-welded in places (Apparently, my inner reinforcement bar was not stuck where I thought it had stuck, so broke free and pulled a few little holes in the door skin in the process. Sigh.), and the tab for the bottom of the mirror arm has been welded on. I've also treated half of the inner surfaces of the door with rust converter, so I have to follow that up to the other side, and then go back in with some paint. Then I can put that back together, and re-fit it to the truck, which looks a little silly without it. L...ast week, I think? (It all blurs together), I did some more chopping and hacking of the rotten cab structure. Decided to do a video in a different style, a sort of faux time-lapse method; involving videoing it, then speeding up all the tedious bits to make them marginally less tedious. It did not work very well. Nevertheless, here it is: I don't think I'll continue that style of video, it's just too mind-numbing to edit and watch. Currently, the plan is -- weather, light, and mood permitting -- to roll my generator out to the old gal and finish removing that rotted-out section with a full-size angle grinder. Then I'll do my best to clean out & apply rust converter and paint to the inside of the other section where it doesn't appear to be as bad, before cutting a length of replacement box section to length and welding it in. It's just too cold and wet to be rolling around underneath the truck, in all the puddles, bending brake line.
-
Wow, there's certainly some stuff in there!
-
It is possible to MIG aluminium without a spool gun or push-pull (We do so daily at work.), but using either a spool-gun or push-pull makes life easier if it's available. Ideally, though, aluminium is welded using AC; it will work with your standard DC welder as used for steel, but the welds will be sooty, and generally not as neat/clean as ones done under AC. As for changes to run aluminium wire: Change the liner out to a smooth teflon one, as opposed to the wound one used for steel (It also helps to try feed the liner in so it's as close to the rollers as possible, to minimise the unsupported length of wire so the soft aluminium wire doesn't kink and bird-nest. It probably still will, at the slightest provocation, though.); run a little less pressure on the rollers, to avoid squashing the wire; and keep the torch lead as straight as possible. Oh, and keep the swear jar handy, because it probably will scrunch the wire up for seemingly no reason.
-
For a giggle, some more progress on the door: MIG'd by the tack-tack-tack method. There were a few blow-throughs. Done with stick. A few holes were where I was using 1.6mm rods that are mostly flux and spite, which meant longer arc times to deposit metal; turned out to be easier to use 2.5mm rods on the same power setting... probably because they were putting more metal down so could actually build it up quicker, and reduce the amount of heat I put in. While welding with MIG is quicker, it's the set-up time that gets me. Sometimes it's just easier to set up my little suitcase stick set than it is to hunt down a working MIG welder that isn't in use, chase down a 3-phase extension (or two... or three... depending on how far away the nearest socket is) and perhaps a Y-splitter, and get it all hooked up before someone runs away with the welder. Not the prettiest, especially where trying to build up gaps, but it's solid now. Once again putting the age-old phrase to work: A grinder and paint, makes me the welder I ain't. Primed up to stop it rusting away while I figure out how best to attack cleaning out & treating the innards. Fine tuning and filling to come when I know it's all back in shape enough that it won't require any prying or persuasion that would crack the filler out.
-
Bedford 3-Ton/4-Ton (RL) Field Artillery Tractor
Tamber replied to Tamber's topic in British Vehicles
It's amazing how much stuff turns up, when y'say you can't find something! -
Bedford 3-Ton/4-Ton (RL) Field Artillery Tractor
Tamber replied to Tamber's topic in British Vehicles
That's not me, not even under a different name. Doesn't seem like he had much luck hunting them down, either! Were they used to test some sort of invisibility generator for artillery tractors, or something? Thanks! That's a nice little picture... at least proves they weren't invisible to cameras. Attached, for some semblance of reference -- I guess -- are the figures from the EMER supplement. -
There really doesn't seem to be a whole lot of information out there about the RL Field Artillery Tractors, unless I'm missing something really obvious. My first run-in with any mention of the RL in a FA tractor role was stumbling across supplement 5 in EMER F-172, issued May 1962: "BODY, TRACTOR, 3 TON, FIELD ARTILLERY, 4 x 4, BEDFORD, MODELS RLF and RLW" Wikipedia makes mention of them in a single bullet-point: The EMER supplement lists them as "a quantity of Cargo vehicles [...] converted to the Field Arty. role; [...] conversion effected by REME." (I would like to attach the 6 page PDF of the supplement, but don't know if that'd be frowned upon.) In summary, however: A locking device on the cab left-hand door, to lock the door in the open position A grip handle above the left-hand door. Modified towing attachment bracket to strengthen and lower the towing hook Stowage cabinets added on both sides. The upper cabinets' compartment doors replacing the two forward body panels; and stowage cabinets slung under the body platform. Additionally, a pair of "normal MT stowage boxes are located at the body front" on the left-hand side, and a cabinet between the body front and cab rear on the right-hand side. Doors in the body sides, with steps. (On the RLW, metal steps provided on the right-hand side, but only a tread in the lid of the underslung cabinet on the left-hand side.) Fuel-can carrier from LHS and tool-box from RHS both removed. Spare wheel mounted on a pedestal on the front of the body, removed down a folding ramp thing on the LHS. Bench seating, for members of the gun crew (presumably), at the rear of the vehicle body on the RLW conversions Does anyone have any pictures of these in use? Any interesting stories about one? *grin*
-
A thought, for those bearing housings; if they turn out to not be quite lined up enough, an option is to phone about for a company that does mobile line-boring. It's a pretty common operation in heavy equipment repairs, and they can set up to machine it in-situ. (Feel free to disregard this if you already knew, but it's good to have options just in case.)
-
Not a great deal to report, since my last post, unfortunately. Work has been causing me a lot of stress, which significantly reduces my desire to be anywhere near the damn place to work on it... ("You can't be stressed, you only work five days a week!") And it's not helped that we've moved to a different unit on the estate while the old one is being demolished, with the easy route (300 ft or so) blocked off by demolition-company fencing, turning it into about a third of a mile walk between toolbox and truck. (Which isn't so bad, except for when you're on your twentieth trip after forgetting something...) However, I've also spent the last two weeks on holiday in Canada, which has done wonders for stress reduction. It's not exactly done wonders for my wallet, though, but I have enough bits to be getting on with while the balance recovers somewhat. Between my last post, and my leaving for my jaunt across the ocean: I took the driver's door off and started repairs of where the mirror arm was torn off. Still some tweaking to do to take a dip out where the spreader plate I added on the inside (so that the load where that mirror mounts to the door-skin, is spread across a bit more area.) has pulled the sheet metal in somewhat; and a little at the top of the patch-piece where the return has gotten a little misshapen. Nothing some quality time with a hammer and some implements of leverage can't fix. I also need to de-rust/treat, and paint, the inside of the door; as well as finish up the repairs to where the bottom edge was rotted away. It's getting closer to where it should be, though. The Bedford got towed to a different yard, which brings it a bit closer to the workshop. Downside -- because of course there's one -- being that the yard is smaller, so it'll be buried behind more stuff. Got quite a bit of attention, rolling slowly around the front of the industrial estate with hazards flashing, which was nice. My brother, normally stuck on 2-wheels, was properly chuffed with himself after parking the truck in the given space considering the biggest thing he'd driven previously (only for a short duration... and off the public highway, of course, yer 'onour) was a VW Beetle. I got some wire-brushing and painting (well, primer, but it counts) done around the vicinity of the rear towing hitch. I was planning on continuing that when I got back, but the snow is making me reconsider. I also uncovered a grease nipple while wire-wheeling the towing hitch, which was nice. Furthermore, I have discovered that someone who previously owned the truck does not appear to believe in the holding power of bolts... Yup, welded round! There's also a few nuts that have been welded, and a few spots where the Harvey Frost gear has been welded to the chassis. A couple of hours of wire-brushing and painting later, and it's starting to look a lot better. Surprising how long these things seem to take when the wind is determined to blow through you, rather than around you. Oh, and when someone keeps cutting your extension lead powering the battery charger for the cordless tools... (I swear, if someone made a TV documentary about my workplace, nobody would believe it wasn't all made up for the cameras.) Another fun discovery was that the hitch appears to have perhaps gotten rather worn out at one point, and repaired Something tells me this truck may not have lived an easy life. I've gotten a 25ft length of cupro-nickel brake pipe in, and some 1/2-20 brake pipe nuts, so I can start on making up brake pipes. It remains to be seen whether or not my flaring tool will handle this stuff, or whether or not I'll have to upgrade to a better one. (I, of course, love an excuse to buy new tools, but...)
-
From an article about an email from the ICRC, who govern the use of the red cross: So general first aid kits are white cross on green, because -- strictly speaking -- it's not legal for them to be a red cross. There's a lot of stuff knocking around that does have a red cross on it, though, and it's pretty much impossible for the ICRC to police every single occurrence of it.
-
That seems pretty reasonable, and it's a good solution to the problem!
-
Indicator switch fitted, but not yet wired, since I forgot just how easily the outer part of the column rotates; might have to come up with some other solution for mounting the indicator switch where I want it to be. I'll burn that bridge when I get to it. I also managed to put last weekend, and this bank holiday Monday, to good use; extracting the wheel cylinder from the front, and temporarily reassembling everything on that corner so I could pinch my axle stand for doing the rears. First little job of the day, separate the drum from the hub, to make it easier to work on the hub. I believe the marketing phrase to use here is "* Some sequences shortened." Plenty of use of the 2-1/2 lb hammer involved shifting that. Drum stowed in a side-locker, along with the others. All going according to plan so far. Some finagling with sockets, and spanners, and a little use of the small hammer of precision adjustment managed to extract the banjo bolt feed into the brake cylinder; and that funny valve-looking thing... Turns out to be just some sort of offset adaptor to go from the 1/2-20 flexible line, to the banjo bolt. And it has a hollow socket type of arrangement that sits over one of the studs holding the brake cylinder on. Anyway, moving on... bits 'fell off'. Once again taking some persuading to do so. It's almost like these parts haven't been removed in quite some time! The whole arrangement sits like so: No pictures of the rest of the day, but it was mostly slinging the hub back on and refitting the bearing lock-nuts, then hefting the wheel and spacer into place; so I could take the jack and stand out from under the front, lift the rear, and remove those wheels. And around rolled the bank holiday Monday, whereupon I didn't get a great deal of pictures, but there wasn't much to take a picture of; other than my frustrated tongue-stuck-out-in-concentration expression while I tried to juggle the expander and brake cylinder together on the axle, and hold them against spring pressure, while trying to rotate the bolt (it was originally a pair of studs with nuts, but I figured bolts would be easier. More fool me.) with a spare finger. ...Obviously, I was already short of hands enough as it was, so there are no pictures of my expression. Which is probably for the best. However, I did get this nice snap of the results of a few hours' progress in the morning. Some cleaning of the axle required! :wow: Then I went to re-fit the offside wheels to do the little jackstand shuffle across to the nearside and repeat the process; and broke my shovel trying to lift the outer wheel on. :mad: However, someone was smiling on me (for some reason. Maybe because they were laughing so hard at me hitting myself in the face with the handle of the shovel as it snapped off? :undecided: ), because there turned out to be a length of beat up aluminium tube laying around that was the perfect size to hammer over the socket on the shovel. It's now a lightweight racing shovel. The other side was very much like the first, but the other way around. Also, since I had discovered that I didn't need to take the hub off to fit the expander, I didn't jack it anywhere near as high, so I should have a lot less trouble refitting the wheels. Of course, now I've said that... :blush:
-
More little bits and pieces Some indicators, for one. Waiting on the switch, which hopefully might be delivered some time tomorrow. Keen-eyed viewers may also notice the front hub is mostly off (Just clamped by the brake shoes on the inside of the drum); this is to extract the front brake cylinder, which is turning into a little more of an ordeal than first expected. There's a strange valve type of thing on the port, that appears to also be fastened to one of the mounting bolts for the cylinder and is restricting access just a little. I'll have to get some pictures of it next time I'm down at the yard. While I'm in there, I'm also going to change the hub seal and clean out the marmite that may have at one point been grease. Yuck! Then I can put the hub, spacer, and wheel back on... so I can retrieve my axle stand and go fit the rear brake cylinders, which paves the way for some fluid plumbing.
-
Maybe three, at most, in short stints of plodding about the industrial estate. Pretty sure the fuel usage is measured in gallons per mile, too. :-D
-
restoration New project - Mk 1 Knocker 6x6
Tamber replied to ArtistsRifles's topic in Blogs of MV restorations
Screw-in exhaust-port filters are pretty common pneumatic parts. If those ports are BSP, then http://www.accltd.com/products.asp?recnumber=4506 might be a good starting place, perhaps? (Or your preferred local hose & fittings trade counter. ) -
Nice bit of out of the box thinking, getting that curvature just right like that!
-
I took advantage of the nice weather this afternoon to get some more little bits and pieces done. For starters, I evicted the brake master cylinder from my toolbox locker and mounted that back on the chassis; it's still got all its protective blanks and cap on, and is filled up with fluid to hopefully absorb any moisture that might end up inside (It should reduce the likelihood of water building up at low-spots, and I can flush that fluid out as needed.) Depending on how my brake re-fit goes, I might end up fitting the brake servo without the air assist, just to provide the linkages to give me at least manual brakes. (Since it should only be one air-line, and the mounting bolts, to take it back off when I figure out how I'm attacking the assist valve.) I won't really need to fit it until I get the rear brake cylinders on and that rear circuit piped up, though. I've also been doing a bunch of measuring of fittings and pipe (It appears that it's pretty much all 1/2-20UNF and 5/16" pipe.) for new brake lines; as well as stripping out old brake and air lines. Not much that leads to many pretty pictures, unfortunately; though I have discovered that the thread on the air lines is mildly interesting. It appears to be a BSC thread: 7/8-26 with a 60° thread angle. Not sure that information is really useful to anyone, but there we go. Also, I certainly won't be winning any competitions for speed on getting this thing done.
-
question Downloads from the RLC Archive
Tamber replied to Tamber's question in I may be stupid, but......
Trying it without plugins is definitely a good idea! Unfortunately, a completely bare browser doesn't help either. I get the same downloads page, sans a clickable link; and if I dig out the link and follow it manually, I still get the same "Your download was successful" page without having anything downloaded. Worth a try, though... And just confuses me even more; since the site must work, because other people are using it and presumably managing to get their chassis number research results downloaded. (Does seem to be only the chassis number wotsits; I've successfully managed to download contract record pages before.) EDITx2: More thinking... Maybe this just means they haven't found a record for it yet? -
The scene of today's antics. :-D (Welder has a length of light chain wrapped through the handle, and a cable-tie to lock the chain off. I really need to get myself some longer welding leads than the ones that came with it...) Edit: When I said antics, I meant it! :-D I didn't get any pictures of the original brackets, or how they were welded. But here's a nice close in shot of where one used to be, now with the lump of weld ground off. New brackets stuck on slightly lower down on the jib. The new location protects the lights a bit better, since they're now sat behind the top section of the jib, and the brackets themselves help shield the lights a little from the rear, just in case. The original ones were mounted on top of that double-thickness flange in the foreground. (Thankfully, they were easy enough to remove, because they were only welded on one side. Sufficient enough for a light-bracket, though, but I like to overbuild a little...) Not the prettiest weld I've ever done, but not too shabby for being done while standing on the A-frame. It's still more than enough for a light-bracket. It should be able to withstand some abuse... :-D A productive-enough couple of hours, all in all.
-
question Downloads from the RLC Archive
Tamber replied to Tamber's question in I may be stupid, but......
I have NoScript, but it's set to allow everything from the rlc archive (and anything that page needs to load); same with adblock, it's set to be completely off on that site just in case it's blocking something. I get no notifications of a pop-up being blocked, either. t'is a proper headscratcher. -
Well, I've tried a few different ways now, and I'm going to have to admit I'm defeated, and ask to see if I can figure out what I'm doing wrong. I have made chassis-number research requests on the RLC Archive, and these are listed in my downloads section; but under the "download" heading on the list, there is nothing to click. Looking at the page source for that section, there is a link there, but the link text is all spaces. (So there's nothing visible to click.) If I follow that link, I get a page that says my download was successful, but... nothing actually downloads. I've tried it in Firefox, Chrome, Edge, IE7, and IE8; on both Windows and Linux, and it doesn't seem to have made a difference either way. Beginning to feel like a bit of a buffoon by now... :mad:
-
Time for another little twitch of life, I think. Honestly, I've not gotten a great deal done; but little bits, here and there. I've made up some brackets to hold lights (tail, brake, and indicator) at the top of the jib. In that vein, the old smashed lights and brackets have been removed; and I've run the cabling for both those lights, and the O/S light cluster. (Plus, bulbs have been fitted!) Since it was also buried in the yard behind a(nother ) crippled wagon, I also went and hunted down a generator so I can run power-tools and my little welder (Which it does; I can't go for crazy power, but I'm not exactly welding massive steel plates together...) since I wouldn't be able to move it over to the workshop. Naturally, three days after I get the genny, the wagon blocking me in... gets dragged into the workshop to have the transporter gear stripped from it. Typical! Still, here's hoping that I should be able to get more done, with power available over on the far side of the compound. I've measured up -- yet again -- for steel to start on putting metal back into the cab, so I should start getting material midweek, funds permitting.