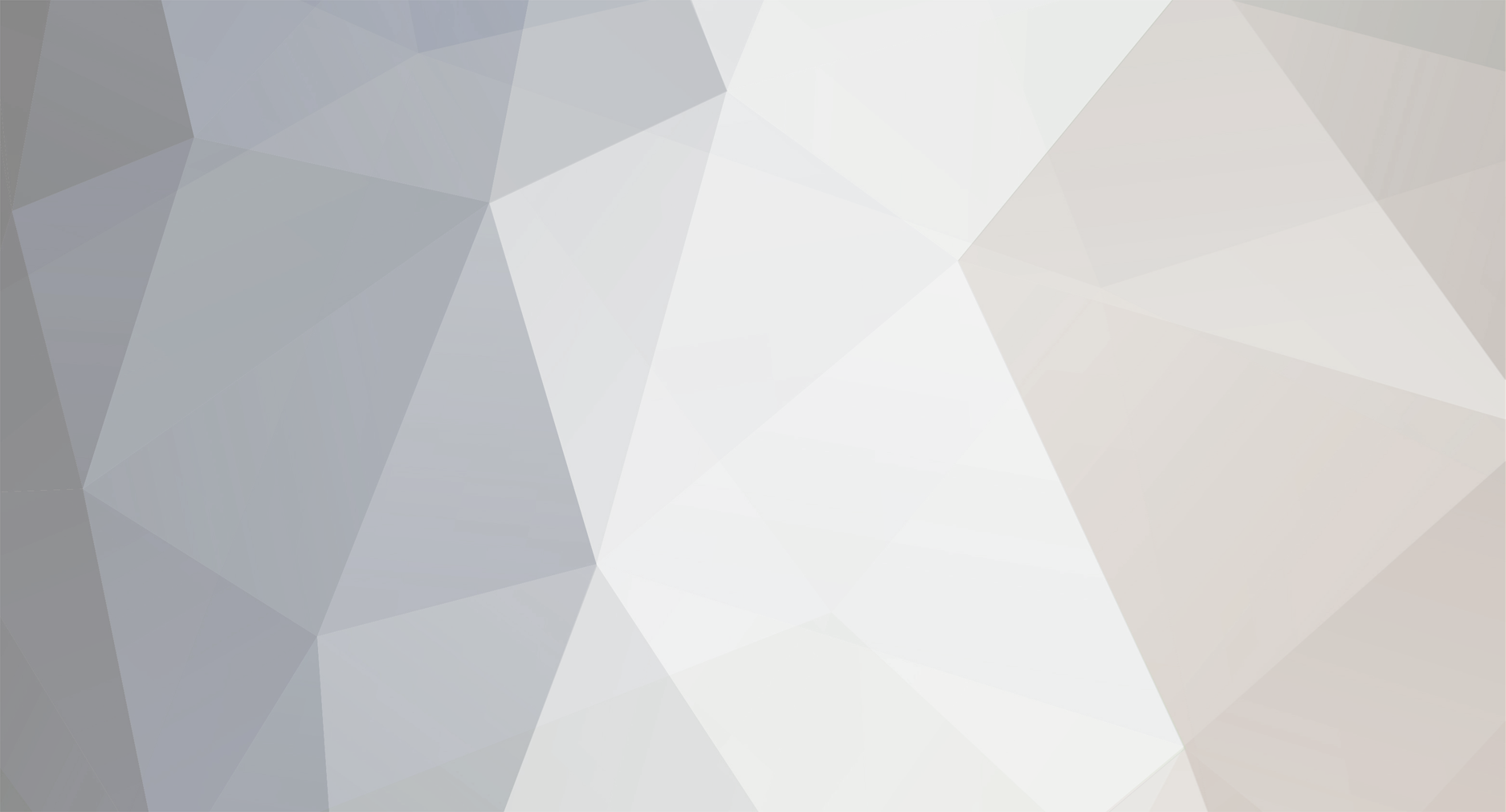
Tamber
Members-
Posts
236 -
Joined
-
Last visited
Content Type
Profiles
Forums
Gallery
Blogs
Events
Articles
Store
Downloads
Everything posted by Tamber
-
Okay! So, it's been a bit since I last updated, I know; I reckon it's about time for an update on where things are at the moment. Leading directly on from my last post: I quit my job. They said to take the truck with me, too, but they'd buried it three deep in the yard anyway, as they do. 🙄 They were also supposed to be completely out of that building & yard by Christmas. Then by the end of January this year. I'm sure you can imagine how well that's gone. I still need to find somewhere that's a more permanent home for the RL, as a few seemingly-promising leads have blown away in the wind. (New job doesn't have space in their yard for me to move it down on in there, and it's probably for the best anyway. Wears a bit thin constantly being at work, even when not at work. 😁) Anyway, let's get back on with the truck update. 😁 February 2019 Went to move 'er out to a slightly drier patch of the yard, while there was still a clear path out from behind the dead van. This'll do: Late March 2019 Had a burst of energy, so went to attack the brakes again, starting with that awful job I made of the rear axle line. Much better. And while I was at it, let's continue with the piping! Some supports and pipe clamps will come, in time. Early April 2019 Brake shoes back on the OSR. They're still exactly the same, done nothing with them yet, so they'll have to come back off again to be re-lined as needed. After wrestling with the wheels, I went and looked for some nice easy jobs to do... ideally lying down in the shade under the truck. Checked & topped up the front axle, and the NSF tracta joint. The OSF, which has the most leakage -- I've got replacement seals for both sides, but considering that I might have to move the truck on short notice, I didn't want to really tear into anything that would render it immobile for any considerable amount of time -- also has a level plug that was apparently tightened by the Hulk. Ugly, eh? Early June... The rest of my struggling with the brakes, from the day after -- when most of the visible work got done -- didn't end up in that video, because my editor was becoming clumsy and struggling with the footage I'd already loaded into it. I'll probably make a part 2 with all of that stuff in. Maybe. ...in about a month, at the speed I edit video. Anyway, more brake stuff happened! More specifically, I fit those two front brake cylinders, plumb them up, and get the system properly filled with brake fluid. I also sorta bled it, but managed to destroy my cheapie vacuum bleeder by having the little fluid-trap pot end up upside down, and the pump pulled fluid in, which just wrecked the O-rings. I also re-fitted the brake shoes on the nearside, as well, so that the cylinders have some resistance to push against. All those shoes will have to come back off again at some point, either to be cleaned up (where they're of adequate thickness and not contaminated) or to be re-lined. At that point, I'll properly clean & check the drums to see if any of them need resurfacing, and how close they are to end-of-life spec. (I have just found that The XMod has 2 sets of what appears to be the right brake shoes, judging by what I can see in the pictures, amongst some other useful parts. However, the Bedford category has RL and MK stuff mixed together, so I'm holding off on any big parts until I can confirm they're actually the appropriate parts (If anyone has a list of NSNs for RL parts, like the clutch, and brake shoes/brake shoe kit, I'd love to cross-check against it! 😁)) For now, though, there's a hint of braking if I pump the brakes a lot, which is a good sign. I just need to get more fluid, and either a helper, or another (better) vacuum bleeder (and not draw fluid up into it. )... Early July July sorta became electricals month. Just minor things, a couple of worklamps... ...an isolator switch... (I wasn't entirely sure where to put it, and maybe accessible from the outside would've been better; but it'll do just fine there, since I can see it/grab it from the driver's seat, in the event that anything goes horribly wrong.) Still need to extend the alternator wiring to be on the battery side of it, to ensure it fully kills power while running, but it's good for the time being. Anyway, at this point, I should note that thing about my ex-work having to be out of that yard by January? Well, by this point, the housing developers are getting a bit miffed at all the stuff still piled up around the industrial estate -- including stuff like truck-mounted equipment that was dumped near the original building they were working out of -- and have started condensing the stockpile of crap into that one yard. I got there one day, and found the RL boxed in. 😁 Not ideal... On the electrical front, I re-ran some wires that were -- quite frankly -- routed stupidly the first time. I know better now, so I've fixed it. And then I loomed it all with PVC loom tape. (Not the same as electrical tape; it won't turn into a giant gooey mess after 6 months.) And then, a jail-break happened.😁 Sadly, these shenanigans weren't caught on video, because I forgot to put my video camera on charge. Such is life. Anyway, an escape was made to a different place to park. That about does it for now, I'm in stockpile/scheme mode again. I managed to make the wiper motor twitch a bit while I was playing with wiring, and went to investigate the linkage. One of the wiper spindles is seized up, and the other one turns out to have a bound up and twisted linkage. Unfortunately, I found out about the bound up linkage after I'd disconnected the link bar from the seized up spindle, and the next attempt to move the wiper motor pulled the other spindle out of the rusted roof metal. Ah well, it needed fixing anyway, right? 😁 Currently in two minds about those spindles, and need to do a little measuring before I decide what route to go. Either way, the roof has to be repaired to be able to take the loads that the wipers will impose, so that needs to be done no matter what; but whether I repair the spindles, or re-engineer something similar but from a different vehicle/manufacturer, depends on how easy it is to get appropriate-sized wiper arms and whatnot. But the wiper motor still works, which is nice. Just have to do a minor repair where the mounting screw for the cover is snapped off in the stalk for the switch, and it should be perfectly serviceable. It's the little things, yanno? 🙂
-
I'm looking forward to the door going back on, and getting glass into it. No idea when that'll be, but eventually. Grabbed a spare hour or so after work on Sunday to start trying to get that underside infill put in, and start getting the bottom part of the door back to the right profile. It's pretty close in one spot, but still a good amount of persuasion required to get it back to where it should be. That's my fault for leaving it stood up in the workshop, where it's taken a bit of a beating being near the welding supplies bench. Some truck-shuffling in the yard at work (bloody brand-new LF with dead batteries that's been there for 4 months has been moved!) has left some room on slightly drier and firmer ground in front of the RL, so I'm tempted to try shift it forward out of the lake so that I can get to do a bit on the brake lines. Starting to write up the list of things that need to happen before I can get sorta-functional brakes on at least one axle, even if I have to stick the old shoes back in for now, just so I have an idea of what I might need to sort out in what order. (Starting with seals, before I end up with fluid everywhere. 😁) It remains to be seen whether or not something else gets shuffled into that space before I get there, though. 😁 New ball-bearings and a shaft-seal for the compressor should be arriving Soon™, hopefully within the next few days; then I should be good for another crack at that. (At least the crankshaft can go back in...) I think I've also managed to source some piston rings, so I can replace the oil-control ring I broke; but we'll see how that goes when they get here.
-
And, just so I've got something useful to bump this topic over, I have gotten some more progress on the driver's door. The infill/strengthener piece at the bottom of the door, in particular. It's being made out of two pieces, to begin with, since I didn't have a big enough single piece to do the whole lot in one go. I was catching a lot of flack for the tin-bashing, though; too noisy for some of my co-workers. 😁 Probably could've repaired the original, but it's quite lacy in parts and I fancied giving a go to bashing one up myself. After all, that's mostly why I embarked on this project, and why I'm not adverse to re-visiting some parts and finishing them up better/differently once I've had more practise. Which I will be doing with part of the outer door skin repair patch, which I really should've made up in two parts rather than try to do it all in one. Live and learn. Hopefully, once I get this piece finished up and fitted, I can give the door innards a coat of paint, then refit the door to the truck rather than have it sitting around in the workshop; which will be a bit of a boost because parts will be going back on again. Goodness knows I need the boost...
-
As might be evidenced by the lack of updates, this project has almost completely stalled for now. I'm still collecting parts, and trying to put things together, though. (Who woulda thunk that work moving to a bigger workshop would make it harder for me to haul the truck in from time to time?) Current little bit of progress to be made is that I've flexible brake hoses made up. They've been made with M12x1.0 ends on them, and I have matching union nuts for the hard-line, so I can at least get that one little step closer once it's no longer a swimming-pool underneath the truck.
-
I've done a few other little bits and bats since the last update, mostly just putting wiring back together post-'fire' and connecting both beacons up so they now work on the switch. Oh, and some little brackets and whatnot so that can mount a second gauge (Well, so that I can put the air pressure gauge back where it belongs, and still have the tachometer.) along with a hazard switch; now the hazard lights work on a switch, rather than having to twist wires together. I still need to tweak the bracket for the indicator switch, because it doesn't fit where I first planned it, but that's not the end of the world. All the wiring will be tidied up when it's closer to being completed. The compressor's been broken down a bit further, and I've got a bearing separator on order so that I can pull the ball-bearings off the compressor crankshaft. The ball-bearings seemed okay at first, but I've noticed that one of the front ones was beginning to feel (and sound) a bit crunchy, so I'm going to replace all three. Somewhere, I have a notebook with all the measurements I've made. The bores are both in great shape, not tapered or ovalled; and... I'll have to go dig the notebook up to run through the numbers for the crankshaft, but the rods certainly don't feel loose on the crank after giving the crank journals a gentle polishing. I've also run through the various threads that needed cleaning up (Mostly 1/4UNF; the thread on the nose of the crank is 1/2" BSF, and I'll need to get a new castle nut for that, but I don't see that causing much bother; and the thread for the filler is 3/4" BSP which is handy since I have hydraulic blanks spare in that size. ) And I've also gotten a little bit more welding done, mostly just adding some support to the battery tray to stiffen things up. The air-tank carrier was also tacked in place, so that it can be welded fully at a later date. It's not much fun working in a yard that's slowly turning into a mud-pit, though. It's not the worst I've had to work in, but it's still distinctly less than pleasant when you're slopping and sliding around trying to move through the work area; it's too much like site-work at my day-job! Also, I keep catching myself on the legs of those metal screens all the time! :grr: It is amazingly frustrating, working out in the back of a car-park!
-
Yup, barely gotten started on it yet; this is just the tear-down to find out how bad it is. I do enjoy my suffering. 😁 I certainly don't think it's so far gone as to be irreparable. Certainly not by the standards of some members of this fine forum, who could probably rebuild it if all that was left was the broken filler cap! 😁 The other rod is as bad as the first, no great surprises there. I also cracked open the Drawer of Excessive Precision* for my micrometers and did a quick bit of measuring. The rod journals seem to be within the realm of cleaning up sufficiently with a bit of polishing; the big end bearings having taken the brunt of the damage as expected, being white metal. The machinists precision G-clamps gave me some numbers (I'm majority metric, so bear with me! 😁) : №1 rod journal: 22.22mm, №1 big end (vertical, i.e. in line with the rod): 22.5mm. Clearance of 0.28mm, or ~11thou. №2 rod journal: 22.3mm, №2 big end: 22.45mm. Clearance of ~0.15mm, or a midges under 6thou. Big ends are just a touch out of spec. I'll see what the crankshaft mics out to after I've polished the journals, I can live with it being a hair undersized so long as I can get the rods to match it. I still need to finish tearing the compressor down fully, measuring the bores and whatnot, but so far it looks otherwise to be pretty good. I'll just keep on keeping on, for now. (I also have a couple of weeks booked off work, in the hope that I can put some more time in on the Bedford; so naturally it's going to rain constantly until I run out of time, I'm sure~) (* Above the Drawer of Insufficient Precision, which houses all my hammers and other tools of "Fit, damn you")
-
Teardown time! Not pretty, but cleaned up pretty easily and there's no scoring in the bores. The check-valves all seem to work quite nicely, and I cleaned out the passageways as best as I could. One of the bolts holding the inlet manifold down has a pretty gacked thread, so I've got a tap on order to chase the threads in the head just to make sure, and I'll get some new bolts on order. (1/4" UNF, so nothing particularly exotic.) I also had to break up the remains of the filler cap, since it seemed to have bonded itself into the threads and was stubbornly refusing to rotate. (I'd drilled two holes through it so that I could use circlip pliers to try unwind it. It bent the circlip pliers, then the edges of the holes started to break up.) Very careful -- almost surgical -- chipping with a thin chisel, and picks... A tap for chasing the threads in the filler cap is also on its way. (1" 14TPI, as best I can tell.) Salvaged the dipstick, though! Should be able to re-use that in the new filler cap, with any luck. The wash-out with petrol, and new oil, got rid of a good bit of water and oil that was lurking in the passageways, and the bulk of the grot on the inside of the case. That's what was left in the sump. Also lurking there is the remains of the filler plug. Sludge vs Industrial Jetwash: Jetwash wins. Concerningly, the little relief valve on the oil pump looked like it was stuck open. It's also picked up a few fragments of the plastic filler knob after my previous precision removal process, but it was already showing signs of problems even before then. The back-side of the other part to this relief valve had a much older-looking deposit built up on it, and it was wedged open. It's a pretty clever little mechanism, this oil pump. The shaft of the eccentric is the pump piston, and it's hollow -- with a little brass orifice in the end -- so that the pressurised oil squirts up it and is forced into the crankshaft; the pressure relief is a flat plate over a drilling, held down by two little screws with springs, such that once the pressure reaches its limit, it lifts the plate and squirts out. Nice piece of design and engineering. Unfortunately, a combination of that contaminated oil and a completely-bypassing oil pump has not done the crankshaft or con-rods any good. I ran out of time today to investigate further, but there is discolouration on the crank, and the big end of the №1 rod is scored up pretty badly. I haven't removed the №2 rod yet, but I expect it to be more of the same. I will investigate further tomorrow. For now, I'll remain optimistic.
-
The compressor is currently on my workbench, having had the sump washed out with petrol to break up the sludge a bit more, and new oil put in it to circulate for a while to flush out any more lurking water/petrol/grot. I've also jet-washed the outsides to de-sludge the unit -- since it was spreading slime to everything it touched -- and will be aiming to do a bit more of a tear-down, in-depth inspection, and thorough cleaning over the weekend, if work doesn't get too crazy. It's amazing how much time it takes to get the compressor out of its hidey-hole!
-
Went to change the oil in the compressor the other day, and was scratching my head over where the filler's supposed to be. It's very definitely meant to be right there, but it looks like it's met with an unfortunate end. And, on the note of unfortunate ends, the whole truck very nearly met one a couple of weeks back. I hooked up the battery as normal so that I could tinker some with the wiring (and make another attempt at getting the engine to fire, just to see if it's possible to limp it to the workshop & back.), I'd just gotten into the driver's seat and had my hand on the key when the oil pressure warning light started to glow dimly, getting brighter and brighter. "Well, that's weird", thinks I, then I start to hear crackling and the cab fills up with smoke. The cab is covered with a tarpaulin, so I'm at this point inside a big plastic bag with the smoke from burning wiring being blown in from the open passenger's door. It's amazing just how long it feels like it takes to undo a battery terminal while the truck's trying to set itself on fire! Anyway, it turns out that the flexible metal conduit from around the battery positive cable had scooted up at some point until it was just barely touching the ring terminal and it was grounding out on the chassis. It wasn't making a good enough contact to cause noticeable sparks when I connected the negative lead to the battery, but enough that the conduit got pretty hot! Once it cooled down enough to touch, I pulled it out and the battery cable inside the conduit was looking pretty ugly. Got lucky with that; the only damage was a length of battery cable, and some melted insulation on a couple of other wires nearby that I've mostly repaired. (Mostly! I keep forgetting to take my box of repair terminals with me.) That could've been much worse! 😲 Now for something more relaxing; this evening's tinkering with the new front brake cylinders. These are some new old-stock that I got off the bay of E, so I figured I'd best open them up and see what the innards looked like. The first one I popped open looked to be the oldest, going off the appearance of the box, and all the innards are covered in a sticky substance that may at once point have been a lubricant or preservative. There's also something funny about one of those cup seals... Well, it turns out that cup seal that looks funny is harbouring a hitchhiker! 😮 All the seals -- in both cylinders -- feel fantastic, they're like they're still brand new! (I'll still pay the seals shop a visit, though.) And now, the cylinder bore... This is the worst of the two, and the bulk of it is the slightly congealed sticky substance. There was some very slight discolouration of the bore in the middle where the seals would ride in use, but it disappeared after a quick brush through with the brake cylinder hone. There's no pitting or rust, so these have turned out fantastic. Also, I got some motivation back... It's no great leap, but hearing it spit and crackle has lifted my spirits. It aent'nt ded yet.
-
Ticked another item off the list! That bracket I needed to modify, got modified; and, with some jiggery-pokery everything got shoved into place and hot-metal glued. Only stitch welded on this side, because I needed to leave room for the nuts to go on. (And it was tight even as it was; the flange on the nut was pressed up against the box section.) If I were smarter and thought things out better, I would have started that leftmost one from where the tack was, so it'd consume it rather than leaving an ugly glob. Something for me to remember next time, I suppose. Looks slightly less bad with some paint on it. However, it really just needs to be stronger than the two M10 bolts that hold it down to the chassis, or the rubber of the mounts. And since it's fully welded across the back (which was a bit of an uncomfortable procedure, curled up like a cat halfway across the engine cover and in front of the passenger's seat.), it should be plenty strong enough. I am thinking I might go back and add some gussets to it, just in case. I'm hoping to push myself to get at least a little bit done every week, even if it's not much. Did find myself staring up at the cab roof and quietly wondering what in the hell I got myself into. 2 years + 8 months, and I've barely scratched the surface. I put most of that down to my pace of work, or lack thereof, honestly...
-
I think my tape measure is out of calibration, that must be what it is! 😁 I'm quite pleased with that air-tank installation, myself; there was quite a bit of head-scratching, trying to figure out where to put them so that they wouldn't look too out of place. Once the storage box is back on behind the cab, they should be nearly invisible but it should still be fairly easy to get to the air-tank drain taps.
-
Today's mini-update: Some cab mounts! Mostly! Kinda! The rear mount is a pair of universal engine/gearbox mounts on a plate that bolts to the original cab mount. The upper part of that mount is where it all fell to pieces a bit. Apparently I wasn't quite accurate enough in my measurements, because it... didn't really fit. Those holes are meant to line up with the studs in the top of the mounts, and the upright flange was intended to then weld to the box section to spread the load a little bit. It does go on backwards just fine, though, so I'll do some trimming -- remove that upright -- and go from there. Not a great deal of progress today, but the cab is now sat on a mount rather than perching on some box section across the chassis. I also went out to my local engineering supplier and picked up some bolts for reattaching the door hinges to the door, so that I'm prepared for when the driver's door is ready to go back on, seeing as it's about 75% complete. Really would like to be making progress faster than this, especially with the looming workshop move (3 months, apparently! AAAA!), but work seems intent on running me into the ground as hard as possible every week... 😆 Currently looking into options for renting a small-ish industrial unit, perhaps. We'll see how things go on that front.
-
In a surprising fit of productivity, I booked last weekend off, and got something done on the old gal. The driver's door isn't perfect, but it's a damn sight better than it was before. Still a good bit to do before I can call it good enough to go back on. Might have to cut a bit back out of the top edge of the repair patch and re-make it, but it is solid even if it's ugly. I am somewhat throwing myself in at the deep end with the sheet metal bashing, to be honest; it's not something I've done a great lot of and I'm not so good at it, but I can always revisit parts I'm not happy with, as my skill improves. Something a bit more up my alley was mounting up two 'new' (to me, anyway) air tanks. All of the material, barring the tank straps themselves, was originally destined for scrap; so I think I've done quite nicely with it. The two tanks came off a pair of DAFs that were being chopped up by a local haulage firm (because it's apparently cheaper to buy a used truck, strip it down and sell/scrap what's left over, than to buy spare parts. Madness.) and are a bit overkill for the needs of the RL, but I'll certainly have no shortage of air! The channel was originally a single piece of box section out of the scrap skip that was just about the right length, then sliced longways; and the tanks are protected from rubbing on the edges of the bracket by short lengths of cut rubber air-hose left over from a job. Total cost to me: £5 for a tank drain valve that then got pinched for another job, so I'll have to buy another one. Bah. The bracket is as follows: (Sack-truck not included. 😁) And it fits in under the body, here: ("I said: IT FITS UNDER THE BODY!") And then, with a lot of head-bashing, rolling around on the gravel, getting crud in my eyes, removing linkages to give me room... Two air tanks: Still a long way to go, yet, but at least parts are starting to go back on; rather than just get ripped off. I have no comment regarding it taking 5 hours, and a minor concussion, to fit two air tanks and a bracket. 🤐 I keep meaning to write out a list of all the things I need to do to get this truck finished, but it's a little daunting at the moment.
-
You're correct there in that a modern wheel won't bolt straight up, and I went into that knowing such. This was mostly to get an idea of spacing, and whether or not it was even close to fitting. I'd done some measuring, but there's nothing quite like bolting it up and seeing it with one's own eyes. The way I look at it is, I'm going to have to spend money whichever way I go on this project; whether it's getting tubes & tyres for the original wheels, or having modern wheels re-engineered to fit the old truck then getting tyres for those. At least tyres for the modern wheels should be easier to get, particularly at short notice in the worst case. Either way I go with that, I'm not intending to modify the truck, so it can all be put back to original if someone else further down the line decides to do that. Regarding the rubber boot, I'm afraid I haven't the foggiest. (As I understand it, it's not particularly a seal but more of a dust & moisture cover to prevent grot getting into the back of the master cylinder.) Hopefully John's post helps you find the part you're hunting!
-
Thanks! No idea how I manglaged that. 😁
-
For what little it's worth, I use OpenShot for editing my video; I'm not really sure how it compares to other video editing software for ease of use, and it can be an exercise in patience as the amount of video loaded into it gets larger.
-
Now, I didn't get a great lot done last week, when I stuck on an Überbräcket at the back for another twirly light amongst some other puttering about The Überbräcket, named because it's only holding up a twirly light the same as the one on the roof, yet I made it out of a piece of 10mm (3/8"-ish) steel that I had laying around that was the right size, and severely welded it. It's not bloody coming off without taking the crane with it, I think! Our victim, after a little marking out: After some weldering: It feels surprisingly high up; but that plate is just about eye level if you're stood on the bed of the truck. Well, as long as you're short, like me. And with the twirly stuck on it... Not too worried about it not really being visible from the left hand side, it's mostly just to act as a 'repeater' to the rear of the truck, where the jib blocks the view to the one on the roof. Anyway, the lesson here is: if you see a chunk of something getting chucked in the scrap bin that looks useful, snag it and put it in your overflowing box of "Might be useful, that" bits. Then, maintain your hoard jealously, just in case you might need those bits; which inevitably happens just after you throw them out... Some other trinkets while I was re-exploring the side lockers... This has got a bit of age on it! Fairly sure it's older than I am, anyway. And it has not aged terribly well... Looks pretty cool, though. On more practical matters... I think I have a solution to the brake servo valve. Rather than try re-engineer the internals of the original valve, my current plan is to take an off-the-shelf part and use it kinda as it's intended to be used. I've gotten myself a foot brake valve from a DAF CF (but they're all fairly similar, really. It's fundamentally the same valve as has been used for decades.), and the intent is to fabricate a bracket that mounts it up near the brake pedal such that I can fit a little push-rod from the existing pedal linkage to operate the valve exactly as it is in the air-braked truck. There will be some careful measuring & design going on to get things in the right place to produce the correct throw on the foot-brake valve, relative to the pedal movement. Wheely silly bits... While I was fiddling about last week, I also did some playing about with a modern truck wheel that was laying about nearby. (I think it belonged to the bus company that was here before.) Gloss black would look good. As good as it looks, there's some slight clearance issues. Some faffing about with measuring offsets, widths, etc. ensues. Currently trying to work out what I can get away with, wheel-wise, that lets me fit a fairly standard (modern) on/off M+S type tyre. This 'test wheel' is a 22.5x7.50 and some brief searching tells me that the more normal modern truck wheel is a 22.5x8.25, so I'll try find one of those to check with. Oh, and the offset of the wheel I was testing with puts the inner lip of the wheel hard up against the track rod end, which is less than ideal. I don't think I want that to self-clearance... (And yes, I know the track rod end needs a new boot; it's on the list!) I have a total of 250mm from the mounting face on the hub, to the tie rod end interference; so I shall have to hunt down another wheel, ideally without tyre, and do some more measuring. And to bring you fully up to date... A video, wherein there is some weldening, I look like Darth Vader (black helmet, with a hideous blotchy pink thing inside :D), and some painting. https://www.youtube.com/watch?v=_Ze9Giv40XA (I would've done the embed thing, but I can't remember how to make the video show up on the page and I've already spent too much time faffing with it! It's been a long week, and it's only a Monday for me!) Yes, my shiny dome got sunburnt. Yes, it hurts. Yes, I should've worn a hat.
-
That's definitely an option. So far, it doesn't seem to be too bright, and it points away from eye-line when on anyway; we'll see how it works out. In other news items, I did some work! It involved cooking for a little bit in the sun. A little bit of drilling and metal-sticking later, I had this; which was sprayed with weld-through primer. And that fine bit of engineering fits... ...here! This surprisingly only a little jiggery-pokery involved in getting it to fit; mostly in shortening the weld-through tab on the near-side until it fit with the not-exactly-stock battery box. And, a major milestone reached today, with the first metal going back in, in a long time. Still quite a bit more welding to do, particularly on the near-side where it's only tacked into place for now due to access being slightly restricted by cabling; however, with a bit more welding on the offside, I got it to the point I could lift the cab up off the chassis by jacking it by the end of the new cross-member, which is a good sign. This was the result of about 4 or so hours, including about an hour spent trying to get the generator to start, because the battery was flat and I didn't have any jump-leads. However, progress was made, today.
-
The front panels cleaned up quite nicely, which was a relief, especially considering the paint on the grille was coming off in huge flakes right down to bare metal! Definitely got lucky in that it was still metal, and wasn't just blowing away in the wind! 😁 I might be at it for some time! 😁 The recent stretch of nice weather is definitely helping give more time to get things done, I just now need to start getting things done. Speaking of small progress... Rear brake pipes on the axle finally fully connected up, with the unions I was waiting on. (Automec was the supplier this time.) Rest of the system to follow. ...also some cleaning and painting of that axle, because it looks hideous! And a little switch panel. The ends of the switches illuminate when they're switched on, to serve as the tell-tales. 3 yellow, one blue for the fog light. (I have my suspicions that the blue one may be too bright, from using a similar one at work that was -- as per bloody usual with blue LEDs -- retina-searingly bright. If that turns out to be the case, I'll install a resistor to drop the brightness a little. Or a lottle.) Proper labels will follow when I decide how I want to label it. Self-adhesive labels just seem a bit naff, so it might have to be little brass plates. 😁 This picture also shows the state that the roof is in. I had previously scuffed off all the flaking paint, and shot a quick coat of red primer just to make it easier to see what was going on and what needed fixing. One piece at a time, and all that.
-
Miniature update, just to note that I'm still here and still making tiny bits of progress! Been struggling a little for motivation recently, but I'm trying to keep pushing onwards on little things that I can see. The list of bits: The gearbox oil was changed. A little thing, but it did need it. No signs of anything horrific in the old oil, which is good news. Next on the list for a fluid change is probably the transfer case. A little more brake pipe has appeared on the rear axle. Some blood was spilt in the process, but I've been informed that's actually for good luck. 😁 Yes, I am going to have to join those with M-M unions. I'm not quite good enough to do the whole run in one go, yet. It has quite a circuitous route to follow, and bending this diameter pipe without kinking it takes some practise. It's certainly easier with 3/16" pipe, for sure! I have enough hard-line left to do only about 90% of the run from the rear flexible pipe, to the master cylinder, naturally. So I'll have to order another length, and use the existing material to plumb the fronts. (Especially considering my material loss rates! I'm getting better at not kinking it while just trying to adjust it that last little bit, though.) I also need to do some hunting around to find somewhere I can get to make up the flexible lines with the 1/2UNF ends, once I'm confident I have the right length worked out. Some cleaning and painting has happened. Not the most vital thing, but it needs doing, and it's a visible improvement that helps with the motivation. with some elbow-grease, wire brushes, and sandpaper, became (I will be replicating the markings once it's painted proper.) Moving forwards, I started knocking off the flaky paint and grime, with the intent of just priming up the areas that were at risk of showing bare metal. Well, then I started getting a little carried away with the brush, since it looked so good! It definitely shows up the areas that need serious attention, though. Which, in a way, is a good thing. The grille really was flaking quite badly, so since I was apparently painting the whole damn truck that day, I decided I'd just carry on with that. Big chunks of paint were coming off, right down to bare metal, so it really did need it to protect against the elements Wire brush in a drill, and a little scraping, cleared this quite well. It really didn't take much to dislodge those big flakes. ...followed up by rust treatment. Kurust, in this case, which is my preferred rust converter. Then, when that dried off, a coat of red-oxide primer followed. Much better! I fitted a new beacon on the roof. It doesn't have quite the same look to it as the old Lucas one, but it has the advantage of working; and it'll do the job quite adequately, once I get it wired in. Fitting that also reminded me just how rough the roof is. Plenty of sheet metal work ahead of me yet, and I really do need to pick up the pace a little, I know. I've stripped the tyre inflater down, cleaned out a lot of grunge, and rebuilt it... and it still leaks air straight through from the output side. Need to dig back into it and see what I can do about that. Not sure whether it's just that the conical rubber portion of the valve is so hard with age that it's not sealing properly against the valve seat, or whether there's something I've missed about how it works. So, unfortunately, it's the same old sad story of not having gotten a lot done. To add further insult, we've had glorious weather for nearly two weeks up here, and rather than spending that time working on the RL, I've been having to fix my car to get it to pass the MOT! (Corrosion and brake pipes, seems to be a bit of a running theme at the moment.) Bah! 🙄
-
Now, this is just a thought from someone with no experience of a Ferret, but... I would have to wonder if the gains would be worth the extra heat, complexity, and stress on the engine. Heat very quickly becomes a problem on a significant number of vehicles modified by turbo or supercharging, even when they're not as heavy and covered in armour plate! And that's even before getting into the question of space limitations within the engine bay. And if you did get a worthwhile increase in power, that's putting more stress on the rest of the drive-train. (etc etc) Fuel injection is within the realm of possibility, and I am admittedly a fan of it (When it's not a locked up, un-diagnosable black box, anyway...), but again I'd wonder about the value of the gains one might see from that conversion. Perhaps if you're using a Ferret as a daily driver, you could eke out a bit more fuel efficiency?
-
Modern vehicle wiring, as mentioned, tends to be engineered down to a spec; as thin a wire as the manufacturer can get away with (Helps shave costs, weight, and makes it easier to fit the not-insignificant amounts of cable required for all the gubbins that manufacturers cram into a modern vehicle.) , and designing to avoid long runs that need to transmit high current (To allow the use of smaller cable, etc.) Older vehicle wiring tends to be simpler, and do things that result in long runs that have to carry a high current; for example, headlights, powered directly via the switch... And it's those types of cable runs that could potentially stand to benefit from thicker cable; others, like low-wattage lights, I'd say keeping it the original size is probably better simply from the standpoint of saving money on wire. (I say this, having a not insignificant collection of wire spools already. Vehicle wiring is kinda my thing, in case you couldn't tell.) So my 'simple' answer is: It depends. Headlight wiring, starter solenoid wiring, etc? Go to a slightly bigger cable. Something like sidelight wiring? Unless there's a measurable voltage drop or the lights are dimmer than they should be, using the same size cable will be fine.
-
Maybe one day!
-
I always look at this not as "cutting up a new part" but as buying a conveniently pre-assembled kit of parts to save a bit of time.
-
Yep! Fire-watch is essential, and -- hopefully -- tedious. It's amazing how things can seemingly move around of their own accord and decide to settle down somewhere before smouldering.