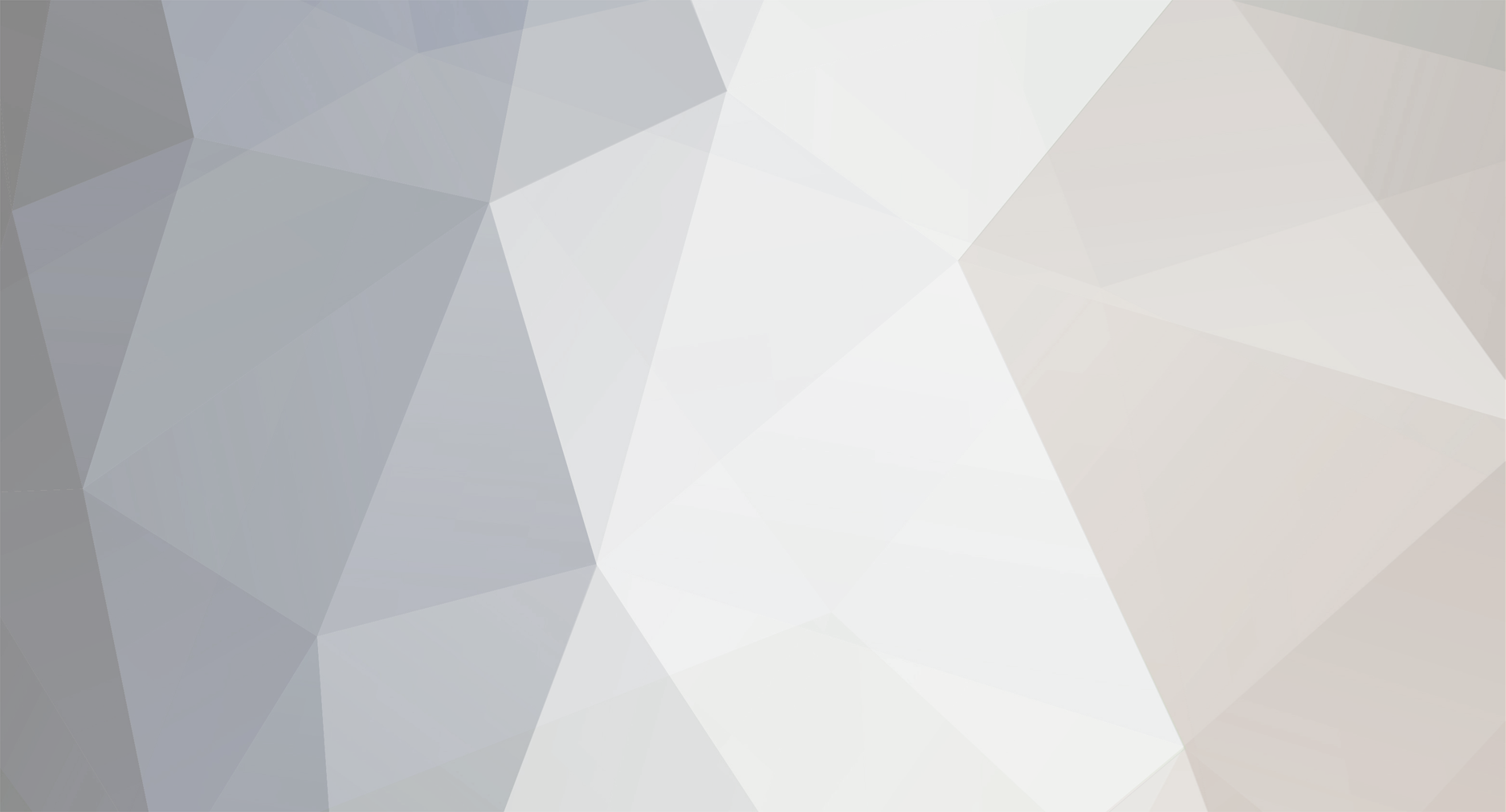
Tamber
Members-
Posts
236 -
Joined
-
Last visited
Content Type
Profiles
Forums
Gallery
Blogs
Events
Articles
Store
Downloads
Everything posted by Tamber
-
Righto, update time! Tore apart, and started rebuilding, a perfectly functional fusebox because I was sick of how rubbish it looked with the busbars on the front. (Why did I do it that way?) In the process, I found some much nicer relay holders, which really neaten the thing up. The 'Afterthought' micro relay holders -- for panel illumination and reverse lights -- went in later; and that leaves me with two spare relay holes. Thought I'd push the boat out a little and add just little a valve stem sealing, as a treat but not too much. Thought I'd give it a go, considering how much oil seemed to be coming down the valve stems. (It's possible that the head will have to go back to the machine shop in the future, for a set of new valve guides, hardened seats, etc. But that's in the future.) Plunk! 3 inlet runners welded up. Not the final length, I just wanted to make sure I had enough on 'em to do what i wanted. No, I'm still not entirely decided on what I want to do, just yet. Fuel injection bits continue: And even some paint! Spot the bit I missed... Oh, and why not some new core-plugs, too: Working my way closer and closer to having an assembled engine, though there's still some bits I need to track down. (Right now, the annoying little bits -- I suspect -- are going to be: A lash cap, and a cam follower. Though I could assemble the engine with the ones I currently have, and change them later. They''re both pitted: the lash cap from corrosion because I clearly didn't protect it well enough when I took it out to stop it coming adrift from the stuck valve; and the follower... I'm not quite sure.) More bits continue to be rust-treated: I'm using plain, boring old generic 45% phosphoric acid; rather than any brand name rust-killer. It's very dependent on temperature, but on a 20+ degree day you can watch it fizz and do its thing. The thermostat looks like it's going to be a pretty easy part to replace, thankfully. 82Β°C, 54mm diameter flange. Jelly-bean part. Couldn't figure out which bit of the block I missed while painting? πOkay, fair, it was difficult to see!
-
10 year steer tyre regulation,
Tamber replied to hotel magnum's topic in Legislation, Licenses & Registration
It's a royal pain in the arse. I can only hope that tyres made after this came into force will start coming with manufacture dates on both sides. (Though with my luck, there'll be a batch of the bargain-basement ones made that they screw up and put a different date on each side. π ) I can't see anything in the linked regulations, but I will say it'd be a very good idea to, yes. Otherwise, sod's law will say you get a tug just after you've spent a frustrating time changing the wheel by the side of the road after a blowout, and get a PG9 for having a 20-year-old tyre on the steer axle, because you forgot the spare was that old. π€¦ββοΈ Date code is fine on the inside on a front, or on the inner of a rear pair. It's when they're on the faces in the middle of the pair that it's a pain. It's become a frequent occurrence for vehicles we've prepped to come back from test with an advisory for at least *one* of the twins, because of a date code that was between the tyres. As previously said, I can only hope they start getting date-codes put on both sides... Though, work's recently got a tyre machine, so I'm far less opposed to turning tyres on the rim to make them face the way I want them to, than when I had to swing a sledgehammer & levers for half an hour. π As far as ten year old tyres being unusual in commercial use... I beg to differ. Maybe they don't last that long on trucks that spend all day pounding up and down the motorway on trunking work; but they're a weekly occurrence on inspections at work (Last set I saw was yesterday! Early 2011 date codes on all 4 across the back axle.) And that's, of course, assuming that they've not been dragged out of the back of a warehouse somewhere, nearly a decade old without ever having seen the road. (You might laugh, but it does happen. Even worse for oddball sizes!) -
It slowed me down, but it's not stopped me yet. I have too many other things to be angry about, so it's good to have something to work it out on! π
-
On the note of the rear light wiring... Originally, I had the wiring to each rear light cluster pass down its respective side of the truck. That was fine, but if I were to do it now, it'd all pass down one side then split at the rear cross-member. But, no, I'm going to just have to put up with it doing a bit of a loop around both sides of the truck, to all come together at an adaptable box only to fan back out again. Cables all fed in... And wired up to the various relays and fuse-holders. (Aside from the switched ignition feed for triggering the relay, and a battery feed power wire out to the circuit-breaker. And a big length of battery cable to bring power down to the box from all the way up at the front! Oh, and a couple of ground leads, because my new rubber cab mounts do a fantastic job of isolating the cab from the chassis, electrically, it seems!) Looks a little over the top, but I don't think it is. π It's doing the same job as any other one of those "smart relay" jobbies, but also providing a place for me to connect all of the back lights, too.
-
Fwoo, right, er... Yeah, it's been a while since I signed in here. 2020 kicked the daylights out of me, and 2021 is not doing my nerves any favours. So, since the last post with pictures, in some sort of rough order: I learned a thing about this engine Quoth the manual: Sez the reality: Doesn't look like there's a liner at all, huh? Funny, that. π Had to move unit again. And the landlord at the current one won't let me leave the truck outside, in the parking bay assigned to the unit. So the truck takes up most of the space in the building. And it got there via a weekend's worth of comedy, while I had one hell of a cold and my brain was pudding. I gave all the cylinders another honing, and they've cleaned up decently; No. 4 still has scoring in it, so it'd require the block being bored out in order to get rid of that. Plan remains to get the engine reassembled and running again; it's not ideal, but it should work just fine. Ring end-gap for all cylinders, with the new rings and pistons, is on the loose end of factory spec. Still going to run it. Tongue in cheek answer is: It's boost-ready. December 2020 "Anyone who said hell might freeze over before I get this truck done, may well be right." During that, I started making progress towards the engine going back together. As a side note, I had the head skimmed to ensure it's got a good surface to seal, and the machine-shop said they had to take 8 thou off it to get it flat. (The deck of the block seems to be flat as far as I've been able to measure it) I'll re-CC the chambers further on down the line and work out how that's changed the compression ratio; should be pretty lively, considering how much get up and go it had before, with all but 7 rings stuck, and down a hole! January 2021 Started off with the makings of the new inlet manifold (Because I'm going EFI, but don't want to hack up the nice original manifold to add injector bungs, etc.) Feb 2021 Rods & pistons in the block. Rear main seal seems to be settling in nicely with all the rotation, and it's not so uncomfortably stiff. Still fairly difficult to turn it over, with the drag of a full set of rings and all, but once I overcome the 'stiction', it rolls over nicely. Additionally, have some video of the dismantling process: Back onto reassembly, the timing cover/front pulley seal was a GACO 6350016, which cross-referenced to a Payen NA512 C939, as allegedly used on other Vauxhall products of the era. Timing cover cleaned, scrubbed down, primed. And as of today, painted: Colour seems a little dark compared to the remnants I have of what the engine was originally painted, but it's in the ballpark. Maybe it'll get closer as it dries? Back light wiring has been altered again, now all going to a junction box that also feeds the trailer sockets. Discovered some brake light wiring had rubbed through where a grommet had disintegrated, so I'll repair that too while I'm in the region. In short, things have happened, but not as much as I would've liked to have gotten done; but 2020 ran me flat pretty damn quick, and I'm still struggling to break even, energy-wise. The important thing is that I'm still moving forwards, and I'm still on this side of the grass. I've given myself a deadline to have the engine running by the end of 2021. Seems a long way away, but with as quick as 2020 went by (while simultaneously taking forever), I'm not sure if it's actually too optimistic! Quite a list to get to that point.
-
Definitely worth doing while the bits are still around! It's not so much of a problem where there are modern alternatives that can be made to work (like the hub seals), but for things like the tracta joint seals... that seems like it's going to be very much "When it's gone, it's gone". Good to hear! Should hopefully be an easy fix. Likewise the front hub seal! That sort of thing is still a problem on modern vehicles with modern seals. Oil just has a habit of getting everywhere... π Thanks! I'll admit, I've not made a great lot of progress of late. There has been a bunch of not terribly interesting cleaning, scraping, sanding, and painting going on; and the engine stuff is stalled for the time being. I really need to go ahead and order more steel for the continuing cab reconstruction, though...
-
The hub seals (front and rear are the same as far as I can tell) were from a local bearings & seals supplier. They're a 3.68x5.12x0.5 inch double lip oil seal. Cost me a little over Β£9 apiece, and they seem to be working so far; but I haven't done any great amount of driving yet so all that really says is that they don't instantly disintegrate. The brake cylinders were an ebay find, I'm afraid. New old-stock stuff. I have still got the old ones, and a reseal kit that purports to be for those cylinders, but I haven't even investigated the ones I took off. (And the old fronts appear to be pretty much completely scrap, but again I haven't put too much time into investigating whether or not they're actually beyond repair, since I've not found a reseal kit for them, so I could be pleasantly surprised.) And you didn't ask, since you're only doing the rears, but... Tracta joint seals and the springs that go with them, for the fronts, I got from thexmod.com, recommended by Frankenhealey on RetroRides. The seals are https://www.thexmod.com/item_detail.asp?id=2854&t=Seal_Oil_Tracta_Housing_6350119 and you'll require two of them. The springs that go with them are https://www.thexmod.com/item_detail.asp?id=6196&t=Spring_Oil_Seal_7065773 and that listing is for one. You will need four. Don't do like I did and buy 2, thinking it was a pair. (...and then screw up again when going to get another pair, and end up with only one. ...honestly, if my head wasn't screwed on...) And as for the cab... the more I poke and pry, the more scared I am that I took it up to the heady speed of 30 mph... and I'm really glad that I didn't have that rear prop while I still had access to enough room to get up even more speed. π± Then again, with as many stuck rings as I had, I might not have had the power to get any faster in 2wd. π
-
Since the last post, I have: Finished up the tacho/hazard/indicator pod. It's not perfect, but perfectly functional and I can live with that for now. (Priority for the time being is to aim for roadworthy and sound.) I do need to make an adapter for the original air-gauge mount, to take it from the oddball size down to 52mm for that nice twin-circuit air gauge. Also I might need to add in a little warning lamp for the hazards somewhere but that shouldn't be too much of a problem. (The switch isn't illuminated, and the indicator switch doesn't -- and can't -- flash with the hazards.) Started some paint/rust stripping, and priming inside the cab I was going to just use the grey primer I have, but I had some of the etch primer already out and left over from giving the front wings another coat. The floors have since got a little red-oxide because, again, I had some of that out from painting other things. The grey primer would be more ideal, since I plan on the inside of the cab being a grey colour anyway, but hey. It's got paint on it, that should slow the rust a touch. Got the first piece of new floor in! ...okay, it's only the bit immediately behind the battery-box, but it counts. Made in two parts so that I could make a neat(ish) job of putting a hole in for the wiring to pass through. Welds on the side of the battery box still need dressing back; the picture makes them look worse than they are. And they don't look all that pretty anyway; having to do chain-of-tacks doesn't really give the flux-core time to warm up and do its job, so they look really really ugly before they get dressed back. Bracketry! Quite stout bracketry at that. This ties the outer edges of the cab frame to the rear crossmember quite rigidly. Once I'd done this, the passenger door stopped being quite so stubborn to open, as the cab would sag and bind things up once I started to open it before. I also did the other side, too. So that's progress. (And then I spent the rest of the evening laying under the truck, pondering.) Pondering! "Hmm... I wonder if I could put a hydraulic pump on that PTO instead? I'd have to run the winch with a hydraulic motor, though." And I reckon I could, too! I would have to build more brackets, though, and it's not like I'd really need the ability to run the winch in either direction at a moment's notice like that. Can't really say I have any real need for other hydraulic equipment either; but I might just work it out as a thought experiment anyway. Either way, the winch definitely needs some attention, though. Just about everywhere it's possible for it to leak oil, it is doing. (That'd be down the splines for the input flange, then. π) Oh, and some other bits fell out of the engine, too. Oh no. Anyway, here's Vandervell... *strums guitar* (Bradford Grinders has them in stock, and I was pleasantly surprised at the price.) Oh, and on the note of engine parts... One ... well, six more pieces of the puzzle. All but one of the bores have cleaned up with a honing; but they're right on the outer end of the spec, and β4 has scoring that still catches the thumbnail even after honing. If not for the scoring, I would probably build it up like that and run it anyway; but as it is, I'd rather not. Going to be at this forever, at this rate! In hindsight, I probably should've ordered the +.020 pistons and just accepted I was going to need to run the block to the machine-shop to have it bored out. Ah well.
-
I could probably weigh them when I've gotten them all off, and see how much of a difference there is; unless it's vastly different, it's probably fine for what is -- at the end of the day -- not a high-performance screamer of an engine that lives on the edge, but having 6 matched pistons is more ideal. ...plus this way, I'm not reusing that battered No.4 piston again π
-
Yesterday! So, taking advantage of the last good day before the weather moves in... ... Several hours of sanding, scraping, and cursing in full sun *melts* Which gets me this: This wing appears to have been replaced in commercial life, having a black undercoat and then the yellow paint atop it. Very well adhered, as opposed to the prior wing... which was yellow paint over four layers of flaking DBG. Anyway, it came off eventually, exposing some slight pin-holes. Easily fixed, then primed. (I could've blended it in a bit more, and made it disappear completely; but I didn't.) Matched set! π One with factory spot-welds, the other with some gas-weld stitches. Presumably after someone had an oopsie. π (Not entirely sure if I added to any of those dents with the escape from that yard, but I don't think I did much beyond scraping some paint and bending the bumper that I straightened back out before painting.) Also, as of last night -- 2am ebay session. It's dangerous, I tells ya! -- I have some NOS Hepolite pistons on their way from Limmasol. So, all being well, that should sort me out nicely for pistons & rings.
-
April: Mostly paint... And a little roof-patching, so I can refit the wiper spindle: Will definitely need to get further into that inner portion to rust-treat and paint, but for now it will have to do. (...that is not how that linkage goes back together, I'm pretty sure; but I can't remember how it was before I took it out, and I don't appear to have any pictures.) Flush with success from that, I went to free up the other spindle to try have a matching pair. And twisted off the spindle shaft trying to turn it. Okay, I'll have to make a new shaft, just need to get the remains of the seized old one out... ...and then I managed to snap the cast outer, trying to drift the remains of the shaft out. Marvellous. It's not the end of the world to come up with a replacement, though; and I've got something drawn up that I can leave with a local engineering firm to make, at some point in the future. Might as well make a bit of a feature of it, I suppose. π Front bumper prettification mostly done: Not turned out perfectly, with a few tiny flakes here and there, and a couple of spots where primer bled under the masking. I'll just call it "retro-realism" or something. π Panel removal continued with the other wing: I'm impressed that it all undid, and I think I only snapped two bolts in total between the two wings. I now have a good bit more access for cleaning & painting the chassis, and repairing those front cab mounts when I get to that. Friday I must say, they did quite a good job hiding that dent. There's also other very visible signs of previous repair work, done with an eye towards function more than form. That aside, I'm very impressed with how solid the panel is. What previous repair work? Well, if I may highlight it a little: (Yes, I did only spot that bit that I missed on the inside of the headlight hole when I looked back at this photo. π) And with the good weather only forecast for another day, the next portion was to do the opposite side. (Which I'd already partially started, with cleaning & painting the back-side.)
-
That looks to be one of the proper Light Recovery variants; quite different equipment on them. They were built right from the get-go as a (pretty well-equipped, judging by the EMER) recovery vehicle; whereas 11CE32 was a cargo truck, with winch, that got a fixed jib installed upon entry to commercial life. Commercial life also seems to have granted 11CE32 something else I didn't expect; I've done some measuring and some maths, and it seems like the engine that's in there is higher compression than I expected. (Being what appears to be a later engine; my boss asked how many coolant ports there were in the back of the block, and reminisced about being able to tell whether it was an early or late block by the size of the bump on the back of the head. ) As best I can tell, it's somewhere in the region of 7.5:1, which will do me very nicely, I think. I've also had the main-caps off, and the main bearings look like exactly like the rod bearings: Pretty much brand new, which is another pleasant surprise. As far as the work I foresee for the engine, starting with the block: The bores have a little wear, but it's not excessive. I think a light hone, and some new rings, should see her out for a good few years. (But it might be a good idea for me to get a set of liners, further down the line, just to have in stock.) Replace the piston in β4, since it seems like it's seen some debris. (Possibly that screw that went walkies from the carb. π³) A bunch of cleaning (And some paint. The appropriate shade of Sky Blue, of course~) Track down the appropriate 4WD sump and oil pickup, to avoid any more unfortunate incidents of self-clearance occurring) For the head? Other than the known bent valve (and probably trashed valve-guide), I don't yet think it'll need much work either, just a light refresh. Still need to give it a proper double-check for flatness, but hopefully that doesn't turn up any horrible surprises.
-
Okay, they should be showing now. We'll see how long for, before everything falls back over again. π
-
Argh. I'm pretty sure I know what's causing it. Everything wants to load them over SSL, and nothing likes the certificate on my server. That's gonna be a colossal pain in the backside to sort, but I'll see what I can do.
-
...where was I last? Ah, yes. Peering into the engine and making some wild-ass assumptions. Since then: Not insurmountable, but some portions might be a little tricky with restricted access. We shall see. Thankfully, the other side is much better: Anyway, following on from that, some other bits "fell off": Amazingly, it came off without much of a fight. However, the extra light and room afforded by removing the engine and this corner panel exposes some more joys to be dealt with in due course: I have a plan of attack for dealing with this, too. But that can come after I have dealt with the rear of the cab a bit more. I need to clean up some of my older welding -- from when I was stick-welding the brackets on in a muddy car-park -- where my priority was to stop the cab from falling off completely. More of the wiring was shifted around, run in different places, and generally modified. In retrospect it would've been better to make the wiring up after all the structural work was done but ho-hum, I've learnt things over the course of doing this that would make it easier if I had to do it again. Further on from then, the handbrake bracket came off (It just came off in my hand, honest!): It was at this point I thought to try the brake light pressure switch in that junction, that I couldn't do so easily when the engine was in the way. Turns out, it still works, which is nice; but I am missing one of the screws. It's a pretty common part, so easily replaceable even if I might hate myself when I have to bleed the brakes afterwards. Anyway, with that bracketry out of the way, I could continue my cross-member replacement programme: Access wasn't quite so good on the other side, due to some floor panel that stubbornly remains in the way but that I am loathe to remove in case it's holding things in place. There is precious little metal of any real structure remaining in the lower back of the cab. All tidied up with a bit of grinder action, and protected with lashings of red primer. Then, when that was done, I used my last cutting disc to neaten up the back of the cab, to make it easier to fit new metal down the line: Then the world went even more to pot, and that has somewhat stopped play for the time being. I did get the chance to get some bore measurements, to determine how worn the bores are and whether or not they're in a range that can clean up without too much trouble. (I've also been trying to order in parts, scratching my head over whether or not it's possible to increase compression just a smidge without spending ludicrous money on completely custom parts, trying to figure out what engine is actually in the truck (Because just when I think I've got it all figured out, I find another part of the manual that makes me start second-guessing it), and all sorts of other things because I'm not sure what I can attack next that doesn't need parts I don't have. π)
-
Those boxes are looking quite smart!
-
Makes sense that there'd be a pickup difference between the two. Might have to track those bits down, if I don't want it to end up dinging it again. Anyway, rod bearings look pretty much brand-new. Rod journals look great, too. Some unusual pistons. There are two types of piston in this engine, one type stamped 'B' in the crown, the other stamped 'Y' and looks pretty snazzy: (For some reason, I struggled to get a decent picture of the pistons at all; this one has a torch shining up under the piston skirt, to show the interesting cuts and whatnot. The 'B' type piston has fewer cuts/slots in the skirt, and (I think) a heavier skirt overall. I'll try and get better pictures after I've given them a proper cleaning. (Also, unsurprisingly, there were a few stuck rings.) Also, as for the bores, it's No.4 with the vertical scoring. Does seem like it should hone out okay, though it's a bit beyond a quick DIY hone. I'll give the place work uses a ring and see what they say.
-
Yup, that's the one that's accessed through the flap in the side-tin. The other one is much shorter, mounted lower and further to the rear of the engine (just behind the oil pump.) Flat steel blade type, stamped with 'MIN' and 'MAX'; MIN lines up with the top of the filter screen on the oil pump, MAX is an inch or two up from that. I'll definitely give it some closer investigation next time I'm up at the workshop.
-
Thanks! It certainly took some perseverance! I loosely followed the EMER for the cradle, but don't have a trolley jack quite up to that sort of job. And yeah, solid wheels certainly seem to be the way to go, along with a sheet to lay on the ground to at least give me a flat surface to work with. It does seem like it's the wrong sump, a centre well that's very close to the front diff. I already suspected this is a rebuilt engine, but possibly a bitsa using parts that were to hand, in its commercial life? Either way, I'm sure it could tell some stories... EDIT: ...would that perhaps explain why there are two dipsticks, then? There's one that's accessible through the usual flap in the engine tin, and a much shorter one that goes down into the central sump right next to the oil pump, that you can only really get at from underneath the cab.
-
Also, I've yet to pull the pistons & rods out (I was meant to do that today, but I've spent the entire day in a sleepy haze so I didn't head up to the workshop. 's been a couple of days this week where I've not really woken up until it's just about going dark, and I'm not sure why.) but a quick inspection of the bores while barring the engine over has shown a couple of cylinders with marks to the wall. One of which (I want to say it's No.4) looks to be corrosion from moisture, the other is vertical scratches. Knocking the pistons out will really let me find out; it would not surprise me if there's broken rings or other damage in there. The marks don't seem to be very deep, but they're enough to catch a fingernail.
-
All that later resulted in this: Apparently my "decent-ish" trolley tyres weren't all that decent. They were all pretty much flat by the time I got it out. And then my hasty upside-down welds broke at the door to the workshop, after I'd spent quite a considerable amount of time trying to wheel the engine up the yard. But it got there, eventually. Just to cheer you up/make you cringe in horror, there is -- of course -- video of the shenanigans I went through to reach this point. π Anyway, with it in the workshop, and an engine stand on the way, first order of business was to remove clutch, flywheel, and clutch housing. Clutch wasn't the prettiest, but I've seen much worse drive into the workshop. One (presumably asbestos-laden) cookie: Flywheel looking similarly grim: With the back end undressed... ...time came to get her stood on the engine stand. Now, I wasn't expecting great things of said engine stand because of how cheap it was, but it *was* listed as rated to 560kg. Presumably, that's 560kg in either a very short engine, or one where you mount the stand to the side of the block, because... ...I put the shop-built cradle back under the front of it, so I could carry on working. Some further tear-down discovered other concerning items: I've still yet to take the camshaft out, but looking down at it through the lifter hole and barring the engine over it doesn't seem like the cam lobe has any visible damage or wear. Further investigation warranted. Executioner time! Off with her head! Number 4 appears to have seen some excitement. But the head doesn't appear to have seen the same battering, only what appears to be corrosion damage from -- presumably -- it being sat there with that inlet valve open for so long. 20mm deep combustion chambers! Nice! π Trying to clear my workbench a bit, I thought I'd crack on with putting that compressor back together a bit more. So, out comes that NOS piston and sit it next to the original one. Spot the difference! Also, spot the problem that I hadn't yet. Okay, bit of surface rust on those rings, that'll clean off okay with some wire wool. So, extract the rings, pick up the original piston... and it just happened to catch the light just right. Oh dear. So, cleaned up that aluminium piston good n proper, cleaned up the rings, checked & set the ring gap, made sure it all went together. Good-o. And then my steel arrived for reinforcing the engine stand! So I did that, and then braced meself. Took a few deep breaths, braced myself a bit more, and... eventually... the engine's ready for belly-rubs. Oily bits exposed! And only a 1/4" of sludge in the bottom of the sump, too, which I'm quite impressed by. Spent the rest of the evening cleaning out the inside of the sump back to nearly spotless, and hammering out the dents, since the sump appears to have met the front diff at some point. (Now picturing someone taking an RL off a Dukes of Hazzard style jump, and wincing profusely.)
-
Okay, a bit of a catch-up! That oil control ring that turned up? Quarter of a millimetre too thick for the groove in the piston. Someone on RetroRides managed to find a NOS piston for the same type of compressor off a Bedford VAL, so I thought that'd do for at least pinching the rings & retaining clips from. (Spoiler: It... did, but something else screwed me over.) Screws for the oil pressure relief valve in the compressor: They're a No.3-48 UNC, in case anyone ever needs to know. I have also got some springs that should work. More testing to come. Also, some money was spent, and that kinked rear prop has been rebuilt. (New tube, and new UJs while they were there.) Looks a lot more like it's the correct length than it was before, now. Unfortunately, I don't really have the room to really fly around -- like I did on the old industrial estate -- and try it out. Still, she does move about on it, and there were no horrible noises when I did so. I'm taking that as a success. Further pottering about saw the front tow bar... ...thing removed, along with the radiator and a bit of front panel. The beam the towing hitch is mounted on is quite twisted, and I'm not terribly impressed with how it was mounted. It's done the job, I'll admit, but some wonky brackets with 3 bolts (total) and welded only on the top edge where it touched? I think I can do a bit better. I'd certainly not like to have to rely on it, at some point, and have it break off! Then, a little bit of this happened: And a bit of that: I also re-hung the (unfinished) driver's door back on, so it stops getting more and more squashed. I'll need to continue on with that, at some point. Weather permitting, I'd like to take advantage of there being a big hole where the engine used to be, to continue repairs to the back of the cab. Continuing onwards! Some steel turned up, and I found an engine cradle in it. Removal didn't go entirely to plan, and play stopped for the day at about this point: I wasn't intending to stick wheels on the cradle, but the little jack I was using didn't want to roll over that ground, so I had to stick the wheels on there while the engine was on the cradle, and all that. It wasn't altogether pleasant. I'll do some rebuilding to that cradle before I have to refit the engine, and do a better job of preparations...
-
August 2019 An escape, just in the nick of time, as the final objections to the demolition of the remaining Loco Works are withdrawn. Didn't make it up to the unit. Instead, she had to sit in work's yard for a bit, next to a pair of scrap DAFs, probably having the vehicular equivalent of flashbacks to the breaker's yard. This weekend, I broke out the welder at work, stripped the bumper off, and got the broken bumper mount welded back together. How'd it get broken? Weeeell... there were some escapades on the rescue mission, extracting it from the Loco Works, resulting in the RL ramming the crane on the back of the slide-bed. Anyway, once I got that stuck back together, we loaded up, and I drove the whole mess on up to the unit. (First time I've loaded a slide-bed by myself, and it didn't fall off again, so I count that as a success! I also managed the whole drive up there without breaking anything! Bonus!) Straightened the bumper a little, but didn't want to try push it any further, because the existing cracks at the bend points were already spreading; and it's easier to fix it if it doesn't snap completely. It should straighten better with some heat on it, and then I'll weld and reinforce it. Slowly but surely, things are coming together again. I've started reassembly of the compressor; one piston & rod is back in, I have a replacement oil control ring for the other one. (It yet remains to be seen whether or not this replacement actually fits. I hope so!) Still going to be held up by not having the right screws for the oil pump pressure relief. (The ones I got are very close to fitting, but are too big. I've ordered some of a slightly smaller size, but we shall see.) I also need to get another spring to replace the one that disintegrated upon removal. I will, of course, document dimensions/thread counts/etc when I find things to be satisfactory. In short, it's a herd of small pieces that are getting in my way at the moment. But I'm hoping it shouldn't take too long to have the compressor back up and running again. We shall see.
-
Scammell Pioneer Gallery
Tamber replied to AndyFowler's topic in Transporters & Wreckers (All Nations)
Where: M1 is the torque setting of the wrench M2 is the actual torque applied to the nut L1 is the normal length of the wrench L2 is the extended length of the wrench M1 = M2 x L1 / L2 This works where the extension is inline with the torque wrench. There's also a set of calculators at: http://www.fordservicecontent.com/renderers/torquewrench/wrench_formula_main_en.asp , for the more awkward setups. -
Thanks! Things seem to be working out well enough at the moment. π Progress is progress, and all that. In exciting news, the RL does seem to be able to fit on the back of work's big slide-bed; the only potential concern is height. (And that's mostly me being a worry-wart, I think.) So far, I've managed to free up, re-lubricate, and straighten the linkage of one of the wiper spindles; and elsenet, someone turned up some useful parts that may come in handy. Though it's always good to know more places that might have other parts, if needed! π Apparently, Series LRs have a little adapter drum that attaches to the 1/4"ΓΈ shaft with a grub-screw, and converts it to a 1/2"ΓΈ push-on spline; and nice short wiper arms that then fit onto said 1/2" spline. Bonus, they're inexpensive parts. https://www.paddockspares.com/stc987-wiper-splined-adaptor-drum.html and, for example, https://www.paddockspares.com/prc4276-front-wiper-arm-right-hand-drive-vehicles.html I'll see where that leads me. If it goes nowhere, then at least I'm not out of pocket very much. π