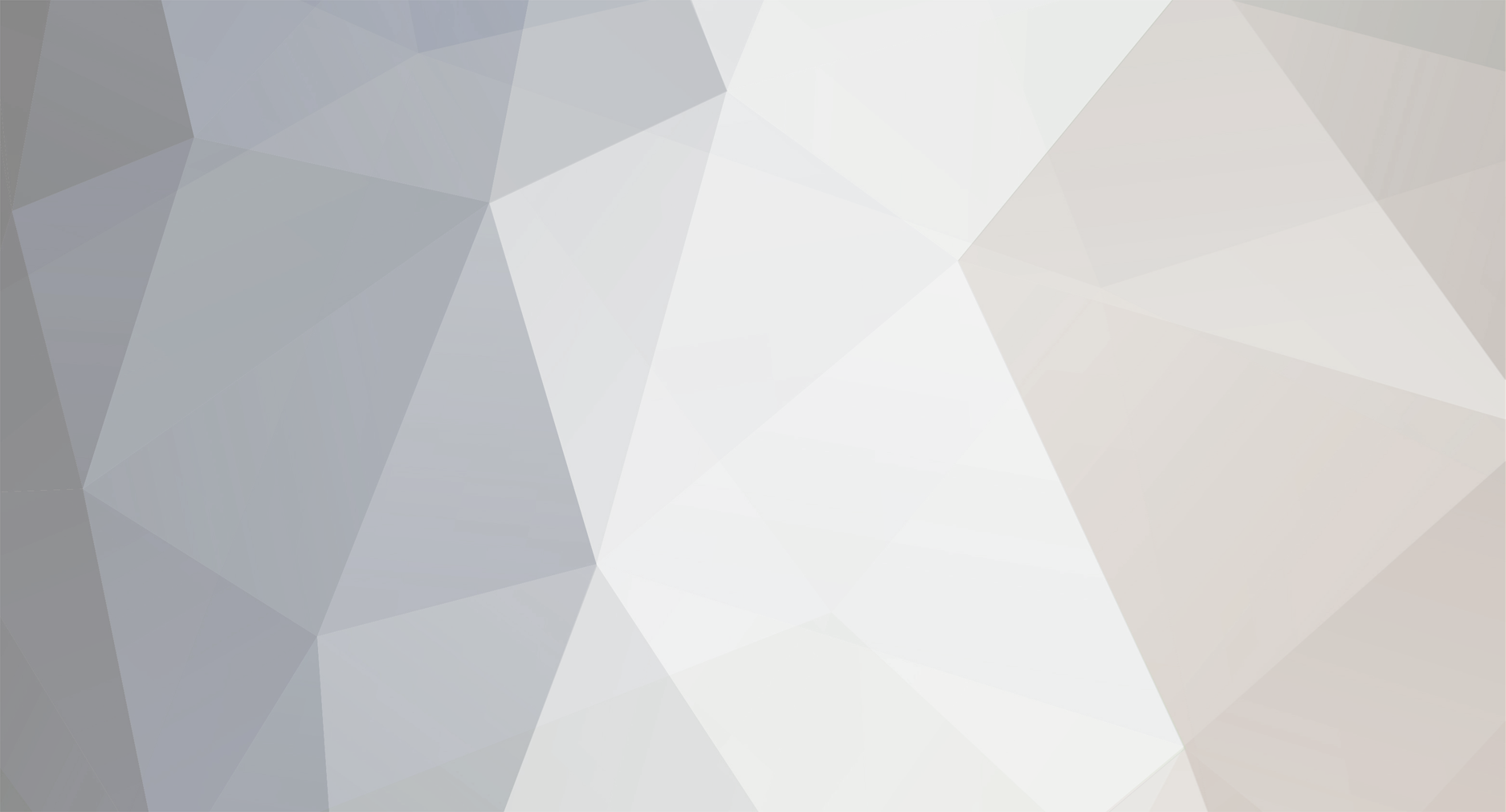
Tamber
Members-
Posts
236 -
Joined
-
Last visited
Content Type
Profiles
Forums
Gallery
Blogs
Events
Articles
Store
Downloads
Everything posted by Tamber
-
Found it. That certainly could've ended with an unintended bath.
-
Congrats! ...so, when are you starting the rebuild on the next one? :-D
-
I'm not even moving it up the list, it can stay where it is until it gets it right. (Trying to keep the collection of loose parts down; so I really want to focus on getting the brakes back together, for now. Otherwise I'll have a heap of bits that I'll lose...) It's not a catastrophe, just a minor inconvenience along the way.
-
No sign of it yet, nope. I'll probably end up kneeling on it while working under the truck, or something...
-
restoration Civilian Mk1 Militant
Tamber replied to Zero-Five-Two's topic in Blogs of MV restorations
'tis always interesting seeing how these older trucks weigh up compared to modern stuff. I guess they just have a presence about them that makes them feel bigger, until you have them parked next to a new wagon. -
Well, it appears I didn't get as lucky as I'd hoped. (I should note, I've not run it since discovering that screw fell out.) I have one unhappy-looking exhaust valve. (Also, the oil was as diluted as expected. I got 20+ litres out, it stunk like petrol so badly that you could smell it six feet away.) Off comes the manifolds, starting with the two studs that hold the downpipe onto the manifold. Naturally, one nut came off as if it were still factory fresh, and the other just instantly sheared flush with the casting. Some more finagling and cussing got the carburettor off... (Note the studs holding the manifolds together have also been removed, I was hoping to remove just the one; but that's not how it works and, besides, the other would've just been in the way anyway.) And, thankfully, all the nuts came off the studs/bolts came sweetly out of the head to allow me to remove the manifold. Not as heavy as I'd expected, honestly. Unfortunately, it gets a bit worse from there. Some careful checking with a length of TIG rod around the diameter of the valve revealed no simple obstruction pinched between valve and seat, so either the valve is bent, or just seized in the valve-guide. I did get the valve to move slightly upwards via the very careful application of a little force, to nearly bring it close to its rest position, but it felt pretty horrible. There was a scraping/dragging sensation that comes from something being far too tight in a bore; I suspect that, at the very least, it's going to require a new valve and valve guide. *sighing a-plenty* An engine rebuild was already on the TODO list, but I was hoping to be able to carry on limping it across to the workshop under its own power so that I could do welding work. The engine is a project in and of itself, and I want to leave it until at least after the brakes are done before taking that on. And just to rub it in, I've been blocked in the compound by a heavily-vandalised & immobilised truck, so I can't even simply tow it across to the workshop to do any welding. I'll manage, somehow.
-
Looks very similar to the one I have, though perhaps it's a little skinnier. (Mine's got a 7mm diameter body) It can be a very useful tool, if you can just manage to get it to reach where you need and point in the right direction, which is easier said than done. I've not managed to get much done over the last we... fortnight or so. It's been a bit hectic with work, etc; and it's all just a bit of a blur. Doesn't help that my work week is out of sync with the calendar week, so I'm never really sure what day it is. Anyway! The screw that's missing from the carburettor is a little oddball, it appears to be M4x0.75; which is a non-standard (but formerly popular apparently in French stuff) metric screw that's apparently made of unobtanium. (Yes. Metric. I was highly surprised, too. I had to do the "check it four times, remove glasses and hold it up to the light and a bit closer just to make sure" dance. Started with the UNF/UNC thread pitch gauges; they fit the thread profile, but not the thread pitch. Whitform is the wrong angle, so it wasn't that. And the 0.75mm metric gauge dropped in perfectly. Go figure.) I've solved this problem the slightly rough way (Retapped the hole for a screw that I actually had: a standard M4x0.70. :red:) and applied a dab of thread-locker to all of them. Continuing on the theme of hackery, I've undone the rear cab mount and jacked the cab up very slightly to sit it on a length of 1-1/4" box section laid across the chassis rails; taking the weight off the rear mount and the hollow section it's attached to, so that I can cut out that rusted section and replace it with new metal without the cab falling off. Hopefully. I'll have the camera rolling when I make those cuts, so you'll have something good to laugh at afterwards, if it does go wrong.
-
Braver, or dafter, one of the two. That's always a possibility. I don't plan on starting it until I'm confident I don't have any chunky bits inside it. Even if that means I'm towing it around the industrial estate with a forklift for the next year or two. :-D (With my luck, now I've said that, someone will have had a tidy-up and thrown my tow-bar out... :rotfl:) I know I will need to tear that engine all apart at some point, since -- even without the screw that it has ingested -- it sat so long with the carburettor open to the elements that at least one bore is going to look a bit ugly; but, right now, I have enough on my plate -- and the looming threat of a workshop move potentially within a few months -- that I don't really want to add that as well. However, I am going to try my luck with a small, powerful magnet and see what I fish out of the plug-holes. If I don't get something from there; then I'll take the inlet manifold off and try my luck there. (But I don't plan on taking the head off, unless the engine's out of the truck and I'm going for "full rebuild/recondition".)
-
Camera poked down plug-holes has come up inconclusive. I don't have any horrible noises when I crank the engine over, though, so I'm not going to bump "engine tear-down" up the list of priorities just yet. For the time being, I'll plan on towing the truck to the workshop with the forklift when I need to work on it. Today also saw some more rot removal. The repair/reinforcement around the nearside end of the rear cab crossmember, which was full of rust-flakes. (A healthy, iron-rich way to start the day; best enjoyed as part of a balanced diet, etc.) Surprisingly, the battery-box didn't drop out of the truck when I removed that bit. Still a little overwhelming, but I'm building a picture in my head of how it's supposed to go back together, as I strip the layers back. One piece at a time...
-
Eesh, if it's not one thing, it's another. The other day, I went to double-check and re-set static timing, just in case I'd screwed something up; and as I barred the engine over, there was a thunk and it stopped dead. Pulled the spark-plugs, and it started to turn over again; wound it over on the starter, and fuel squirted out. Note, not fuel mist but liquid petrol. :wow: Some checks were made, and I spotted fuel dribbling down onto the throttle-plate. Did the usual wishful-thinking fix of tapping the float-bowl with a screwdriver; nothing improved. "Ah, fuel pressure's maybe a little high..." thinks Jim, in a full-on smoothbrain moment, completely forgetting that the electric pump was meant for carburettors and that sort of issue would've reared its head sooner anyway. So a pressure regulator was ordered, and fitted. And the problem persisted, even with the pressure set to 1psi. A co-worker suggested a stuck float, and the float-bowl was removed. Float wasn't sticking, but fuel did seem to be pouring out unless it was held at a certain angle. Let's have a wee game of Spot the Difference (Followed -- and this is foreshadowing -- by a game of Hide and Seek.): Venturi side of the emulsion block after the carb rebuild: Venturi side of the emulsion block this afternoon: Yes, that screw has gone where you think it's gone. :angry: I'm going to break out the inspection camera and go on a hunt for that stray screw. I'm not getting my hopes up too much, but I shan't despair yet. (In any case, does anyone know what size & thread that screw is, then I can order a replacement? :-D) I also need to get some more oil ordered, since the sump probably has more petrol in it than the tank does, at this point...
-
Another mini-update, as I've been in a little bit of a slump recently and haven't gotten much done. (I really need to tidy my workbench off, so I can get back to those brake expanders; that'd help. They're somewhere under the heap of cable-ends, bags that used to hold parts, and installation documentation from various kits.) Thanks to Ian (Ian43 on this fine board), I now have a working door-lock and locking fuel filler cap. (Before anyone mentions it; yes, that Record vice in the latter half of the video has seen some serious abuse, and keeps on kicking. Two lads were recently dismembering a hydraulic ram in it; and the handle is now shaped like a turkey twizzler because they were tightening the vice with a length of tube over the handle :shocked: And when that didn't work, they welded the job to the vice jaws... :wow: Let's see the powdered shop-floor-sweepings modern knock-offs stand up to that.)
-
That didn't go wrong in the way I expected it to. I was expecting him to rip the back end out of whatever it was he was recovering, or something similar, not that! :wow:
-
Very very true, unfortunately. (Same with all those parts places that are wall to wall shelves with scruffy little cardboard boxes, and the old guy behind the counter who knows where everything is; even if you're looking for that 1958-only counter-clockwise turbo-retro-encabulator that's just a strange assembly with spinny bits and a collection of springs to everyone else. Then the Franks pass on, and you get left with the spotty young kid who's job is apparently just to tell you that the computer can't find the part you need because it doesn't recognise your chassis or registration number. :computerrage: ) But I digress... :angel: These are the bits I have: The plastic top cap, and part of the control valve. They go in here: (CTS circled it while they were taking pictures to send to their sources and whatnot.) After prodding, poking, mapping the ports out, and headscratching, I have a rough idea of how it might've worked, and possibly what bits I'm missing (I think I have a drawing somewhere on my desk. I know I made a drawing, it's just finding it. I organise geologically; think sedimentary.. :red: ); but that's not the same as knowing what was actually there and how it actually worked.
-
I'll get some pictures when I'm next at work. (Ideally, I'll have pictures tomorrow, unless I forget. :rolleyes: ) Even just knowing what shape the missing bits need to be would be a great help! I agree with that sentiment wholeheartedly; tricky to get some of that information into a form that can be written down, though. Continuing onward... I decided not to work, today, due to it being a bank holiday; and, instead, ...went in to work, and spent the day getting rained on while I tinkered with the truck. The rear lights. See what I mean about "a touch modern"? They'll do for now, at least. I was happy with them earlier, now I'm not so sure. (I wonder how long the Rubbolite 360s have been around, though... plenty of decade+ old stuff running around with them on, and still plenty of brand new stuff with them fitted from factory.) The ones that were on there when I got it were multi-functions made by Butler, that had been fitted on a bracket mounted to the supports for the wings. When I took those off the brackets, I discovered what had been on there previously... Looks like they were originally mountings for a pair of Lucas L594s. After that dubious bit of 'productivity', I changed tack again; and managed to get the dizzy out, with lots of careful mallet-work to get it unstuck from its home in the block. I don't seem to have any pictures of the exterior of it before I started cleaning & un-gumming, but the inside was less than spectacular: Model & part number, just in case anyone was wondering: Delco-Remy D204 7953576 It did clean up nice, and everything moves as it should. Including the vacuum advance, which was looking rather sorry for itself initially. (Once again, apologies for the lack of pictures, but my hands were utterly filthy from cleaning rust flakes and gunge out of it; so operating my phone was pretty low on my list of priorities.) I did put a new O-ring on (size 211) while I had it out, and applied some copper anti-seize paste to where it sticks into the block, so that I'd have a chance of being able to adjust it. Some persuasion was required to get it to seat back in the block, but it went in with no major hang-ups, and can be twisted freely now -- with the clamp loosened off -- so I can actually adjust the timing. (And, yes, I did get it to go back in with the rotor arm pointing in the same direction as when I took it off. )
-
Nothing major at the moment; just trickling along getting bits and pieces together, so this is mostly a "still here, haven't given up" post. I dropped the brake servo off at CTS a week or so ago to see if they could find the missing bits of the control valve for the servo cylinder; no luck there. (Side-note: Apparently, their go-to place for information on these bits has most of its knowledge-base residing in the head of a man named Frank, who's only in on Tuesdays. It scares me a little just how much information is contained solely within the Franks of this world.) The hunt continues to figure out what bits I'm missing, and where to get them from. Worst case, I'll have to come up with my own solution for controlling the assist cylinder. (I suspect it'll be along the lines of an external valve with an extended plunger reaching through where the original valve was.) On the lights front... or, well, rear: I've gotten some light units for the back end. They're perhaps a touch too modern, but we'll see how they look when they're on the truck. More wiring to follow.
-
For a brief moment, when I looked at that pic with the tow bar, I thought you were towing the matador with the little traction engine, and I was rather impressed. :embarrassed:
-
Turn of phrase. :embarrassed: They're tightened to spec as per the manual: tight as possible by hand, with the socket sans bar, and then back off a sixth of a turn. Not sure if I'll need 'em, at the moment. I've not driven it with drive going through that rear diff, yet. We'll see.
-
Regarding the video I mentioned earlier… It's nearly an hour of your life you can't get back; no refunds. :-D Anyway! The OSR expander and brake cylinder are out, sitting on the workbench awaiting attention. Gave myself a hard time removing them by forgetting to remove the stop-pin, so the brake cylinder didn't unscrew from the expander... the pull-rod unscrewed from the brake cylinder. Ah well. Sunday, I set in to be productive! Can't say I was really all that productive, and some pointless cosmetics happened. It all starts with the hub, which I slung on Saturday night; hub nuts in, torqued, etc. The obvious next step after that, was to go pressure wash the hub... plate... ...thing, like I commented about in the video; because it was pretty manky. Well, something funny happened when I did that... Well, it saves me wire-wheeling it to get the paint off, I guess. :shocked: No kidding, just the pressure washer with the heater turned on, and the paint just peeled off. So then I had to go get out the paint and make that all nice and shiny again. And while that was drying, the good idea fairy struck again... Clearly, I needed to inspect the inside of the axle housing for anything that looked suspicious; and this wasn't merely a case of me forgetting that the bottom two bolts are the drains, and zapping the bolts out starting from the top. :n00b: Mmmm, shiny. :-D Looks like the cover has seen its fair share of chaos, though. Especially at this bottom corner! :wow: (And, from the outside) Overall, though, it's looking a bit shabby... ...and I already had the paint out, so after a bit of faffing with a wire wheel to strip the surface rust... then running out of battery on the grinder, off to the pressure washer I went! Well, that's interesting. Once again, the paint just peeled back in layers; like an onion, but with less crying. Anyone recognise their handwriting, several decades later? :-D This was under a layer of black, then four or so layers of green. There's also a layer of white under there, too. Anyway, I cleaned it up, dried it off and gave it a couple of coats of paint; with a little twist. I think I'll give that little patch a coat of clear, because I found it interesting enough to keep. That was where I left it on Sunday, while I waited for the sealant to set. This afternoon, I got around to putting the oil in it; which was a slow, exhausting process... pumping 90-weight oil in until it started to ooze out of the level plug. Hopefully, I can now return my focus to the brakes; I'd like to have at least the rear brakes working by the end of the year. We'll see how that goes, but it's good to have goals, right?
-
Phew, these past couple of weeks have been a bit of a blur, again. I keep looking at the date-stamps on the photos and going :wow: Tuesday before last, after work, I refitted the NSR hub; put the wheels back on, discovered I'd forgotten to put the tapered washers back on, threw my hands up in the air, and went home. Wednesday, I pulled the wheels back off, put the tapered washers on, put the wheels back on again; and moved over to attacking the other side. Now, the OSR is the one I made an attempt at attacking last year, and couldn't get the drum off. Still didn't get the drum off on Wednesday, either. Took the whole hub off with the drum attached; which made it about as heavy and cumbersome to deal with as you might expect. For giggles, I took my camera with me and recorded most of the four-ish hours I was there; though, with the dead space and "sit here hammering on something for half an hour" clipped or sped-up, it's trimmed down to a little under an hour. (For those who can stomach nearly an hour of inane mumblemouth rambling, cursing, and the sounds of forklifts/angle grinders/things being hit with a hammer; the video is processing and shall be uploaded in due course. I promise I've removed most of my standing around thinking and scratching my head. :-D) Nearly a week after that (Which was a surprise to me, it felt like a mere couple of days!), I got the drum separated from the hub; and oh boy did that take some effort. With the whole assembly sat on its back -- drum flat on the floor and the hub 'hanging' from the shoulders on the wheel studs -- I pounded on the end of the wheel studs with the 40oz "Persuader" until the thumping changed tone, and the hub dropped free not too long afterwards. I got complaints from everyone in the canteen on the other side of the building, because I'd filled their afternoon break with heavy thumping sounds. :rofl: I then celebrated by wiring up the other sidelight; because why not! The hub has been cleaned up... ...primed... (Yes, I used spray primer, rather than the nicer brush-on stuff. :-X I wanted to get some primer on it sharp-ish, rather than leave the bare metal alone in the damp air of the workshop for too long.) ...and painted. (First coat, it looks much better after its second.) It's also gotten a new axle seal; even though it hadn't been leaking, I was already in that far and had the seal... it'd be silly not to! (Of course, now it'll bloody leak! ) Out with the old seal, and admiring the bearing. Then gently, but firmly, seat the new one; as seen behind my fancy new hand-made artisanal wooden mallet. I've also now removed the brake shoes on the OSR, and am to attack the brake cylinder & expander next. Progress is a thing, it seems.
-
Glyptal was originally, AIUI, intended for motor windings or some similar purpose; but has been used fairly often on the inside of engines and the like because it seals up the castings, helps oil drain back quicker, yadda yadda. Preparation of the surfaces being treated is key, though, if you don't want to risk it flaking off and potentially blocking oil passageways. (It also needs time to 'set', if it's not being baked on, IIRC.) There's a bloke on YouTube who went through the whole thing, though in something significantly newer than being discussed here. :-D (Application video here, but there's ones before that covering the extensive prep work: )
-
Hmm. Fair enough. I'll keep looking, then.
-
Refitted the hub the other da... last week, apparently. How time flies! :wow: The new seal seems to fit a treat, anyway. I also checked that the brake cylinder screwed onto the bisector, which -- thankfully -- it did; and made myself that hub nut spanner I needed. Which fits really quite nicely... (It should; I took great care with my final filing to dimension, for the bits that really counted. As far as I'm concerned, a grinder might be faster at hogging material away, but you just cannot beat a good file.) And then work consumed the time since then in a bit of a blur; and so I found myself finally getting around to using that hub nut spanner and tightening the nut in accordance with the WSM. Then, slung (Ahahahaha. Wrestled, wiggled, jiggled, twisted, squashed my finger.) the halfshaft back in, the ... plate... bit... back on, and tightened everything down. Then, full of enthusiasm, I went and tried the shovel method of putting the wheels back on; and I have to say, it works a treat! But it does help if you put the conical washers back on before putting the wheels on; or you end up staring at them in your hand, then up at the wheel, then back at the conical washers and muttering "you stupid b*****d!" at yourself... Ah well. I figure I need the exercise anyway... And I really should paint the end of the halfshaft, and that disc, too; they're letting the rest of the hub down. (It'll all have to come back off again when I go to re-fit the brake hardware, so I'll do it then.) On the note of the brake hardware, it's been suggested to me to lubricate the expander with copper anti-seize paste, as it's often used on brake hardware elsewhere. Would there be any massive objection to doing so?
-
Tada! I'm surprised at how fresh the rubber seems. A far cry from the rusty, grunge-encrusted old one I took off!
-
Typical! Something like that always rears its head after I get excited and order bits. :rofl:(Will I ever learn? Probably not! Guess I'm just determined to do everything the hard way!) We shall see whether or not it's the right size when they turn up (...from Germany, no less!), but from -- my admittedly patchy -- memory the pull rod seemed closer to 5/16" than 3/8". If not, then I can trade around to get the right combination of bits. EDIT: Measured the pull rod when I got into work today. 5/16". Phew. EDIT END. Anything likely to catch me out with the repair kit? That seems reasonable enough; there's not a whole lot of parts in there, and it seems to be a pretty robust mechanism.
-
I'll keep muddling along, then! Seems reasonable enough; I'll have a look around, because I certainly don't expect these ones to be up to much. (I mean, it moves when I pull on the rod, just about.) (A brief search on Ebay while I was writing this seems to have turned up some NOS units that appear to be just the thing. Lockheed L4255-099.) Seems reasonable enough! I'll bear that in mind while I'm looking for something proper to grease them with. (And I can't seem to find a cross-reference for 4613-M either, with a brief search. I'd be terribly surprised if there's not something suitable floating about somewhere, though.) On the note of muddling right along; I pulled the bisector apart and gave it a good cleaning. Unfortunately, I got so into the swing of things that I didn't take many pictures. :-X Crusty old grease! This, and a light coating of surface rust in the bores, made it surprisingly difficult to get things to budge at first; a liberal hosing down with our favourite close-to-hand "maintenance spray" and a bit of firm tapping and pushing got the various bits to slip free, whereupon the good ol' fingerprint-remover was put to use. I also gently applied a strip of fine emery cloth on a spindle in the drill to the inner bores just to clear off the surface rust; and give everything a quick spritz with light oil to stop it corroding in the workshop. Went back together quite nicely, and all moves nice and freely; should only need greasing, and a new gasket for the cover-plate.