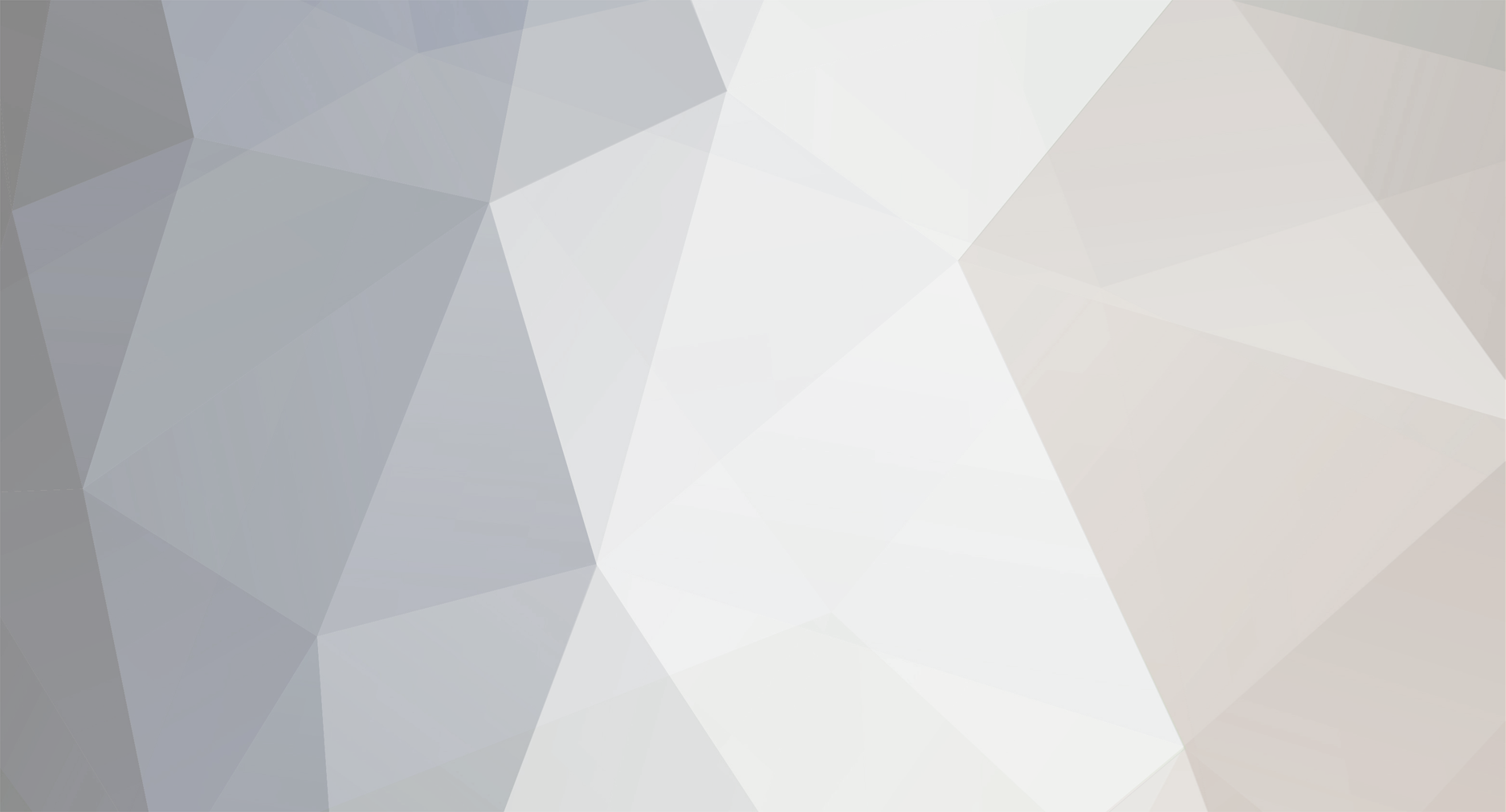
Chris_Collins
Members-
Posts
225 -
Joined
-
Last visited
-
Days Won
1
Content Type
Profiles
Forums
Gallery
Blogs
Events
Articles
Store
Downloads
Everything posted by Chris_Collins
-
restoration Morris Tilly late model
Chris_Collins replied to Chris_Collins's topic in Blogs of MV restorations
More Updates From John, The cab with the drivers door fitted and showing the difference between where the door wants to sit and where I want the door to sit. Attached Thumbnails -
restoration Morris Tilly late model
Chris_Collins replied to Chris_Collins's topic in Blogs of MV restorations
"A bit of heat to loosen the hinge bolts. There are two different size bolts for the top and bottom hinge. And the rotten bailey channel. " Attached Thumbnails -
restoration Morris Tilly late model
Chris_Collins replied to Chris_Collins's topic in Blogs of MV restorations
"The doors will all need new glass and bailey channel. the windows raise and lower through an interesting set up with four pulleys and thin wire cable running through a gear on the window winder operating on a short section of wire chain. " Attached Thumbnails -
restoration Morris Tilly late model
Chris_Collins replied to Chris_Collins's topic in Blogs of MV restorations
More news from John Neville. "I am at the stage where I want to install the B pillars and attach the rear chassis rails and floor. I clamped the B pillars onto the chassis and hung the drivers door on its hinges to make sure it lined up properly. It did almost but not quite. The B pillar hinges have no adjustment but there is about 6mm adjustment on the door hinge. The best way i think will be to position the door and adjust it to the opening as best I can lining up the gaps and catches before I weld the B pillar. To make it a bit easier I decided to strip the doors now and lighten the load. This drivers door is in very sound condition including very good interior timber trim. Under the dilapidated bailey channel is a very good sample of original paint color, although Chris is going with a mid war brown for these restos. " Attached Thumbnails -
restoration Morris Tilly late model
Chris_Collins replied to Chris_Collins's topic in Blogs of MV restorations
Despite the rear body side panels appearing straight(ish) in most photos, none of them are good enough to use. Either too dented, bent or rusted or containing too many additional holes we considered they would detract from the final appearance if the rest of the bodies come up as good as we expect. So new panels were decided on. The front and top folds were done at our local steel supplier and the rest of the forming will be done by hand. Chris gave them a coat of primer to protect them pending further work. Attached Thumbnails -
info for restoration water tank trailer
Chris_Collins replied to m.ciucchi's topic in Trailers, plant and equipment
Hans, If m.ciucchi doesn't want it I'd be happy to buy it and any other trailer parts you might be willing to offload, i fear shipping a whole trailer to australia is going to be prohibitively expensive so i may as well build a Replica and use hard to replicate parts as they appear on the market. of cause if someone knows of a 10cwt GS or arborne trailer in the Antipodes i'd be very interested. cheers chris -
restoration Morris Tilly late model
Chris_Collins replied to Chris_Collins's topic in Blogs of MV restorations
Next was the two panels that re-inforce the floor. I had previously removed these from the rusty Tilly as they are not part of a car chassis. Once again holes were drilled to plug weld. Then grind up the welds and touch up with primer. I need to get a worn down grinding disc to finish grinding up the welds in the ribs. Small enough to fit the radius at the end of the rib. Attached Thumbnails -
restoration Morris Tilly late model
Chris_Collins replied to Chris_Collins's topic in Blogs of MV restorations
"Next to attach the passenger seat re-inforcing panel and seat brackets I drilled some holes in the floor so I could plug weld from the top to the panel and brackets. To get the panel and brackets to sit tight I lowered the body onto a chisel and block of wood and moved it after each weld. To align the seat brackets I bolted up the top side of the seat mount and then removed it once I had then brackets in the correct position with the chisel. " Attached Thumbnails -
restoration Morris Tilly late model
Chris_Collins replied to Chris_Collins's topic in Blogs of MV restorations
More Progress from John, "I cut a bit further along this rusty section of sub frame as it had another pin holed area a few centimetres further down so rather than have two small patches I put in one bigger one. You can also see holes drilled in the ribs in the floor. The previous onwer had stored the car outside and to prevent water sitting in the ribs he drilled drain holes. Luckily he periodically smothered the whole vehicle in lanoline which had crept into everywhere and helped preserve it. All these holes need welding up as well as some extra holes in the floor where the cars had attaching pins to retain carpet and different seat mounting holes. " Attached Thumbnails -
restoration Morris Tilly late model
Chris_Collins replied to Chris_Collins's topic in Blogs of MV restorations
Body primed and upside down to repair a couple of rusty sections in the right side chassis rails. You can see where I started to cut out the rust with tin snips. Also shown is the reinforcing piece for under the passenger seat and the seat bracket mounts in position of where they need to be welded in. Attached Thumbnails -
restoration Morris Tilly late model
Chris_Collins replied to Chris_Collins's topic in Blogs of MV restorations
New bushes were installed in the suspension arms and links. One bush was pushed in one side and then the other side was cut down in the lathe and the two halves glued together. Attached Thumbnails -
restoration Morris Tilly late model
Chris_Collins replied to Chris_Collins's topic in Blogs of MV restorations
Another big job was stripping all two sets of suspension dampers. About ten dampers were stripped to get enough parts to complete eight. Four front and four rear. The arms were sandblasted and the housings treated in the electrolysis bath. Pistons and valves were cleaned in thinners. Apart from a couple which had rust inside, they mostly cleaned up well. I pressed out the arms and installed new oil seals and then reassembled them. I used a small punch in the press to cut enough gaskets for the rear seal in one go. Attached Thumbnails -
restoration Morris Tilly late model
Chris_Collins replied to Chris_Collins's topic in Blogs of MV restorations
The finish on a Tilly as mentioned earlier is rougher than a car. No lead wiping is included so to convert a car body to a Tilly requires melting all the lead out of joins around the door area, and front seams. Seems strange to 'de-finish' a vehicle. Attached Thumbnails -
restoration Morris Tilly late model
Chris_Collins replied to Chris_Collins's topic in Blogs of MV restorations
Sandblasted and ready to give a coat of primer to hold it from rusting as all the repairs and rebuilding take place. Attached Thumbnails -
restoration Morris Tilly late model
Chris_Collins replied to Chris_Collins's topic in Blogs of MV restorations
The side panels for the rear body whilst being intact and rust free are a bit too difficult to straighten perfenctly so we opted to make new panels. The inside tool boxes were removed by separating the spot welds. The boxes can be sandblasted and reused by rewleding to new side panels. Attached Thumbnails -
restoration Morris Tilly late model
Chris_Collins replied to Chris_Collins's topic in Blogs of MV restorations
There is still a fair bit of work to go on the body but at this stage it was ready to sandblast. I took it outside and Chris spent some time removing any remaining body deadener from the underneath so the blasting would be effective. Attached Thumbnails -
restoration Morris Tilly late model
Chris_Collins replied to Chris_Collins's topic in Blogs of MV restorations
Underneath the passenger floor, where I wleded in the large flat patch, this piece of reinforcing needs to be relocated along with the mounting brackets for the seat base. This was removed and the excess old floor metal removed. Attached Thumbnails -
restoration Morris Tilly late model
Chris_Collins replied to Chris_Collins's topic in Blogs of MV restorations
The Tilly has a stronger handbrake than the car. It has four mounting bolts whereas the car has two. The Tilly also has a reinforcing patch of metal welded around the position of the handbrake to strengthen the floor. this was removed fro the old Tilly and excess metal removed and cleaned up ready to weld over the prop shaft tunnel. Two extra mounting nuts were welded in place. Attached Thumbnails -
restoration Morris Tilly late model
Chris_Collins replied to Chris_Collins's topic in Blogs of MV restorations
The bottom of the windscreen A pillar is finished off. Small metal sections were required for reinforcing the pillar on the outside and inside where it bolts together. Attached Thumbnails -
restoration Morris Tilly late model
Chris_Collins replied to Chris_Collins's topic in Blogs of MV restorations
John Posted more work in the last week "The pieces with the holes were removed from the footwells on bothe sides. I will weld these tilly pieces in after it is sandblasted. I will leave them out for now just so the body is opened up better for blasting. " Attached Thumbnails -
http://hmvf.co.uk/forumvb/showthread.php?54829-Small-British-ww2-MV Milweb is always worth looking at, theres a couple on there you might like, the austin Tilly is very nice looking cheers Chris
-
restoration Standard UV Tilly 12hp Light Utility 4x2
Chris_Collins replied to Ian L's topic in Blogs of MV restorations
Oh:mad: that is gutwrenching, heres hoping you can salvage them Chris Collins -
restoration Morris Tilly late model
Chris_Collins replied to Chris_Collins's topic in Blogs of MV restorations
http://www.wattyl.com.au/en/find-the-right-product/exterior/Metal/Prepare/WattylKillrustFishoilene.html strange, fish oil must be an aus thing, its a rust preventative that seeps into joins and coats areas hard to reach, seems be fish derived, sets like linseed oil does, eg slowly. strangely the stuff I use is odourless, certainly not fishy. I find it can be painted over but takes an age to set. -
restoration Morris Tilly late model
Chris_Collins replied to Chris_Collins's topic in Blogs of MV restorations
I'm the minion/monkey, John is the organ grinder, he might chime in, but i think it is basically this method http://www.homercidal.com/molasses/electrolysis.htm I think the advantages are its quick and effective, and john is more familiar with it. i'm going to experiment with the Molassess method in cleaning up stuff we're not in a great hurry to use, (footman loops etc) as i had some sucess cleaning up a despatch rider helmet with it, but it is rather slow and apparently turns cast iron into swiss cheese, and it has a reputation for being pongy (overratted in my limited experience) and John isn't as familiar with it. My experience is molassess treated stuff seems to start rusting before your eyes after taking it out of the bath, so i'm thinking i'll hit it with phosphoric acid immediately afterwards, should nicely convert any reactive iron into iron phosphate. That helmet came out looking like it had been sandblasted, even stripped the small remaining ammount of paint off. Cheers Chris -
restoration Standard UV Tilly 12hp Light Utility 4x2
Chris_Collins replied to Ian L's topic in Blogs of MV restorations
I've been inspired by your post! Particularly with my own tilly prject ticking along, a bit envious of the lack of unity chassis worries you would have. theres a couple about down in the antipodes and they might be a nice future project. I'm suprised you're having trouble finding brake shoes I'd have thought they were an item adopted from an existing source, but tillies seem to be full of odd little inconsistancies, in comparison to their car equivalent. did you need to get your rims re-rolled, or where they reasonably straight? We've managed to "just" scrape together enough tilly wheels for both cars, but have to cannibalise a few to get a good wheel. Iteresting choice to get your wheels powder coated, i can see the advantages. we went with a regime of sandblasting, prime, fish oil and Butyl mastic the seams and clean up with thinners, re prime and paint. there is a little pitting but overall they're not too bad. good luck and keep posting, I'm more than a little interested! Chris Collins