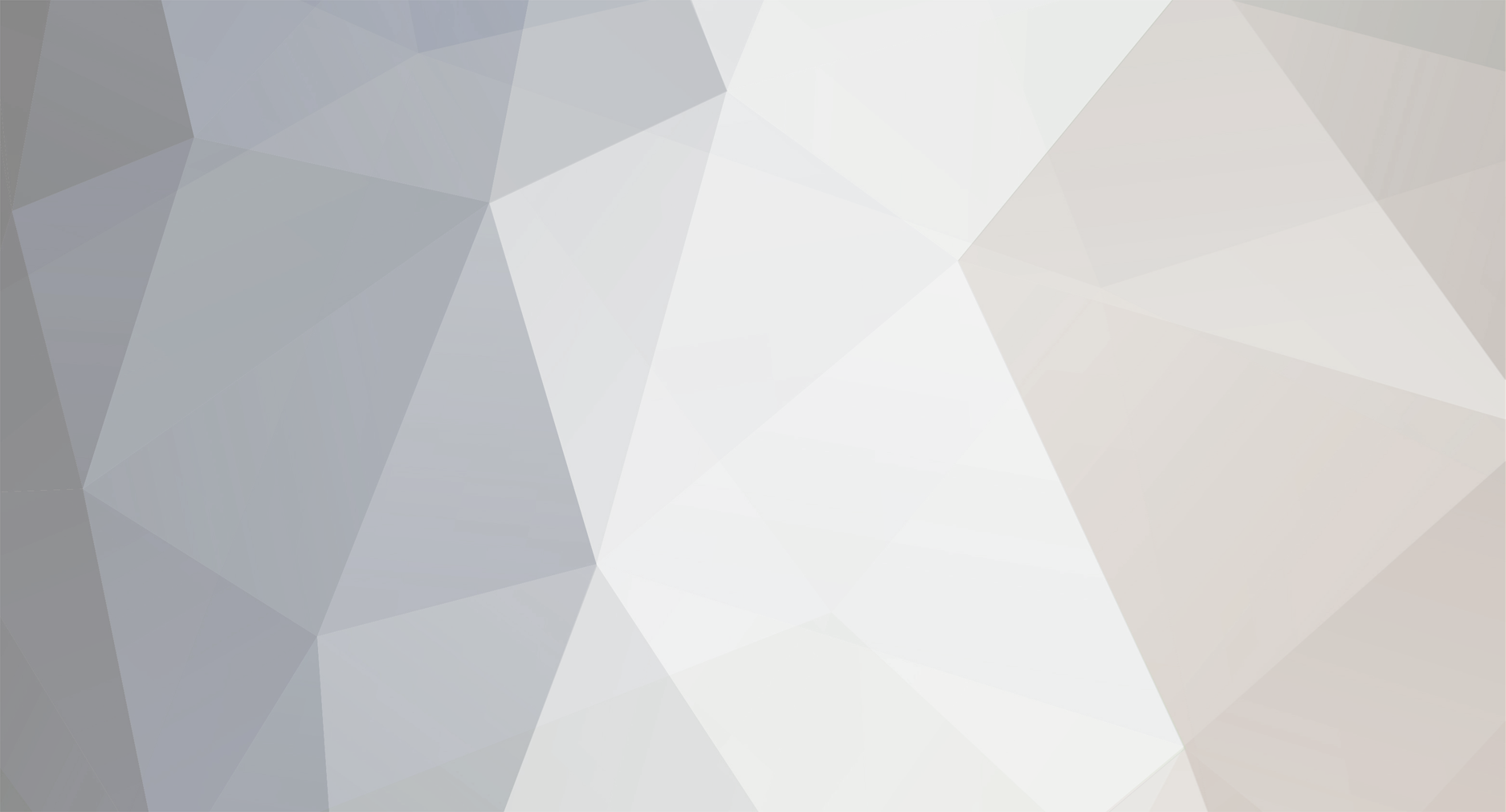
Chris_Collins
Members-
Posts
225 -
Joined
-
Last visited
-
Days Won
1
Content Type
Profiles
Forums
Gallery
Blogs
Events
Articles
Store
Downloads
Everything posted by Chris_Collins
-
restoration Morris Tilly late model
Chris_Collins replied to Chris_Collins's topic in Blogs of MV restorations
More pics of engine progress Attached Thumbnails -
restoration Morris Tilly late model
Chris_Collins replied to Chris_Collins's topic in Blogs of MV restorations
A belated update... Hello all, appologies for a lack of activity, There has been progress but its slowed somewhat. We had been waiting for a loom for some time, but eventually got it from a local supplier of Vintage looms. Engine and gearbox mounts were few and far between so we contacted Old Era services who fabricated new dies and refurbished our old mounts, and did an amazing job. Mean while our friend and Morris Register of Victoria Techo Rod Smith, assessed our engine collection, three Tilly engines and two Morris 10 engines, and began work. on our first tilly we will use the SU carby as used on the morris 10 as we only have one Tilly carburettor (SOLEX 30 HBFDO). i do wonder if the Solex will be a weakness, as the SU has such a good name for reliability. No matter thats what they had, and I'd like to get a second one day, but there will be plenty of time for that. sadly only one Original Tilly block was usable, so we've settled on using a car block modified to Tilly spec using bits ratted from the Tilly engines to build the second engine, sadly there aren't a lot of detailed photos other than a general impression of progress. See below. Attached Thumbnails -
restoration WW2 20cwt Water trailer/bowser restoration
Chris_Collins replied to Ian L's topic in Blogs of MV restorations
Great to see you back on the projects Ian, hope to see that standard tilly get some attention as well one day. Cheers Chris -
Hello everyone, once again daft question from a wally... so Our Morris Tilly is approaching time to start bringing major components back together, EG engine and gearboxback in, but the local supplies of NOS morris 10 engine and gearbox mounts seem to have dried up, I've approached a Chap in NSW who does rerubbering of engine mounts, but of cause hasn;t got a lot of call for Morris 10m so hasn't bothered with them yet. He's happy to have a go but we'll need a minimum run to make it worth his while. However, surely in The Old country, there would be someone who does this sort of thing? and probably has the Dies etc already, Australian Historic motoring is a drop in the ocean compared to what happens in your part of the world? I have had little luck with the Morris Register, there doesn't seem to be a lot of active restoration going on. Do you folk have contacts that re rubber engine/gearbox mounts/suspension Buffers etc? Has anyone had any luck casting new mounts using modern polyurethane rubber? My profession is chemistry, and I'd be surprised if you couldn't find a suitable PU rubber that can be readily cast and poured, and would do a pretty reasonable job at vibration dampening especially for a modest little moggie engine like the XPJM 1140cc... I'm sure as long as its not some garish colour, no one is really going to get their dander up, and if you make a mess of it it'd be pretty easy to remove and have another go. Any thoughts on this would be greatly appreciated.
-
What an amazing find, I'm extremely jealous! the information you can glean from this vehicle that other owners can only guess at based on bolt hole distances etc as everything had been stripped from it, just brilliant, a real time capsule piece.
-
Hello all, Tilly No 1 is streaking towards completion, starting to get our electrics together, Morris tens seemed to use a Lucas RF95? but the Tilly uses a CAV model 75 bt-19x. we have one original that is functional, others that look a little sad. How readily refurbish able is a NOS stock CAV regulator? Should I simply get a reproduction Lucas type regulator, or should i get a modern regulator and hide it inside the regulator box? are these beasties a source of mischief I would be best to avoid? Cheers! Chris
-
restoration Morris Tilly late model
Chris_Collins replied to Chris_Collins's topic in Blogs of MV restorations
Quick Update: I've been away in the old country for 5 weeks or so, had a grand time, met Rampant_rivet at Caldicott Castle and saw his brilliant Bedford MW, and amongst other things sent my steering wheel frames to Steering wheel Restorations in Kent. They were basket cases the resin castings completely gone, though thankfully the frames were sound. I striped off the old resin, careful use of a dremel patience and thoughtful application of a screwdriver and hammer! When cutting into the resin, I noticed they were an odd shade of "pea/Toy soldier Green" they weren't the Bakelite I thought they might have been. A suprisingly soft material despite its age, very good at clogging up dremel bits! We sandblasted and primed the frames, and that's where things stalled, it was a low priority at that stage and the shipping to the UK would be rather steep. My trip to the UK meant I could save a few dollars on postage so i boxed them up stuffed them into my suitcase, and when the opportunity arrived I sent them, and hoped for the best. after hearing nothing for a few days I rang them, fearing they were lost in the post, "yeah, we recieved them a few days ago, I've just pulled the first one out of the mould, and the second one should be done monday" Wow, I was expecting months. That was just before bank holiday weekend,. I recieved them Wednesday evening, and i couldn't be happier and at the first opportunity I took them down to Johns place and popped them on the Tilly! They even did a reasonable job matching the green! -
restoration Bedford MWD restoration
Chris_Collins replied to rampant rivet's topic in Blogs of MV restorations
Hello Jeremy, It was great to meet up today and have a chat and a few mug fulls of Char, your Bedford is an absolute gem and it was a real pleasure to met you, your mates and your lovely wife. Hope you have a great weekend and a safe trip back home. Cheers Chris -
restoration Morris Tilly late model
Chris_Collins replied to Chris_Collins's topic in Blogs of MV restorations
John Neville is a Wizard of metalwork! I'm extremely lucky to have such an inventive person to keep this project rolling along. -
restoration Morris Tilly late model
Chris_Collins replied to Chris_Collins's topic in Blogs of MV restorations
Sandblasting and painting will have to wait for the new year. Attached Thumbnails -
restoration Morris Tilly late model
Chris_Collins replied to Chris_Collins's topic in Blogs of MV restorations
I used welding rods to get the correct size round to make the small keepers for the seat cushion straps. small tabs were added to the seat back and holes drilled to attach. Apart from adding the handbook pocket to the rear of the drivers seat these seats are complete. Attached Thumbnails -
restoration Morris Tilly late model
Chris_Collins replied to Chris_Collins's topic in Blogs of MV restorations
They didn't come out too bad. Attached Thumbnails -
restoration Morris Tilly late model
Chris_Collins replied to Chris_Collins's topic in Blogs of MV restorations
I then scrapped up a simple die to form the small pressings. Attached Thumbnails -
restoration Morris Tilly late model
Chris_Collins replied to Chris_Collins's topic in Blogs of MV restorations
I cut a piece for the reinforcing and plug welded it in place Attached Thumbnails -
restoration Morris Tilly late model
Chris_Collins replied to Chris_Collins's topic in Blogs of MV restorations
I had some sheet metal folded and scribed the shape onto it. I cut a piece of 10mm bar the same shape to dress the edge and folded a new piece of 4mm wire into the edge using a pair of pliers. Attached Thumbnails -
restoration Morris Tilly late model
Chris_Collins replied to Chris_Collins's topic in Blogs of MV restorations
That almost completes the bottom half. The seat back on the complete set of seats we have are not good enough to use so I will make two sets of those. There is a reinforced section on the bottom which has two small pressings which take the weight of the seat back against the legs. The first thing to do was unpick the wire edge and fold out the frame for a pattern. Attached Thumbnails -
restoration Morris Tilly late model
Chris_Collins replied to Chris_Collins's topic in Blogs of MV restorations
I drilled holes around the edge of the seat base to plug weld to the frame and turned down some half inch bolts to match the stepped bolts that hinge the to seat halves together. Attached Thumbnails -
restoration Morris Tilly late model
Chris_Collins replied to Chris_Collins's topic in Blogs of MV restorations
With the legs bent up and joined I added them to the base frame and also added the adjusting mechanism and the claws that locate the legs to the floor frame. Attached Thumbnails -
restoration Morris Tilly late model
Chris_Collins replied to Chris_Collins's topic in Blogs of MV restorations
Next is the legs of the seats. This is made from standard 3mm x 25mm angle iron but is trimmed down to 18mm on one side so first was to cut off the excess on one side. I will do these as eight bends on the lager radius of the template and then weld them in the centre where required to get the correct shape and size. Attached Thumbnails -
restoration Morris Tilly late model
Chris_Collins replied to Chris_Collins's topic in Blogs of MV restorations
It came out exactly how I wanted it. Attached Thumbnails -
restoration Morris Tilly late model
Chris_Collins replied to Chris_Collins's topic in Blogs of MV restorations
To prepare for the seat base frame I had a piece of 2mm strip folded to the correct dimension. I ground a round edge on the top of the template to accommodate the curve of the strip of now angle. I was able to use the cross cavity to anchor clamps and supports to secure the angle and with a bit of heat worked the angle around the template. It puckered in the corner as is went which I expected and it was just a case of heating the pucker up and hammering it down. Attached Thumbnails -
restoration Morris Tilly late model
Chris_Collins replied to Chris_Collins's topic in Blogs of MV restorations
It would seem a lot of effort just to press out two seat bases but I will get more out of the die. The seat base frame is light right angle fold in 2mm steel. I will use the top template to form that angle around. Also the seat legs have the same profile as the front of the seat base and are made of 3mm angle iron. I can use the same template to form them. I have since convinced Nick to give me lessons in CAD drawing. Attached Thumbnails -
restoration Morris Tilly late model
Chris_Collins replied to Chris_Collins's topic in Blogs of MV restorations
So I cut a piece of sheet to size and gave it a go. I allowed a few extra mm all round in case the pressing pulled in slightly. It didn't seem to move at all so once it was done it was a simple matter of scribing around the top template and cutting out with tinsnips. Attached Thumbnails -
restoration Morris Tilly late model
Chris_Collins replied to Chris_Collins's topic in Blogs of MV restorations
I have to say I was very satisfied with the result. The pressing was very uniform and the lines on the underside very defined and exact. Attached Thumbnails -
restoration Morris Tilly late model
Chris_Collins replied to Chris_Collins's topic in Blogs of MV restorations
So that was the female part complete. The male part I used 25mm steel bar. The ends were rounded of in the lathe and a cross piece welded in situ in the female template. Some 10mm flat bar added to reinforce the round bar and then it was ready for a test on a piece of scrap.