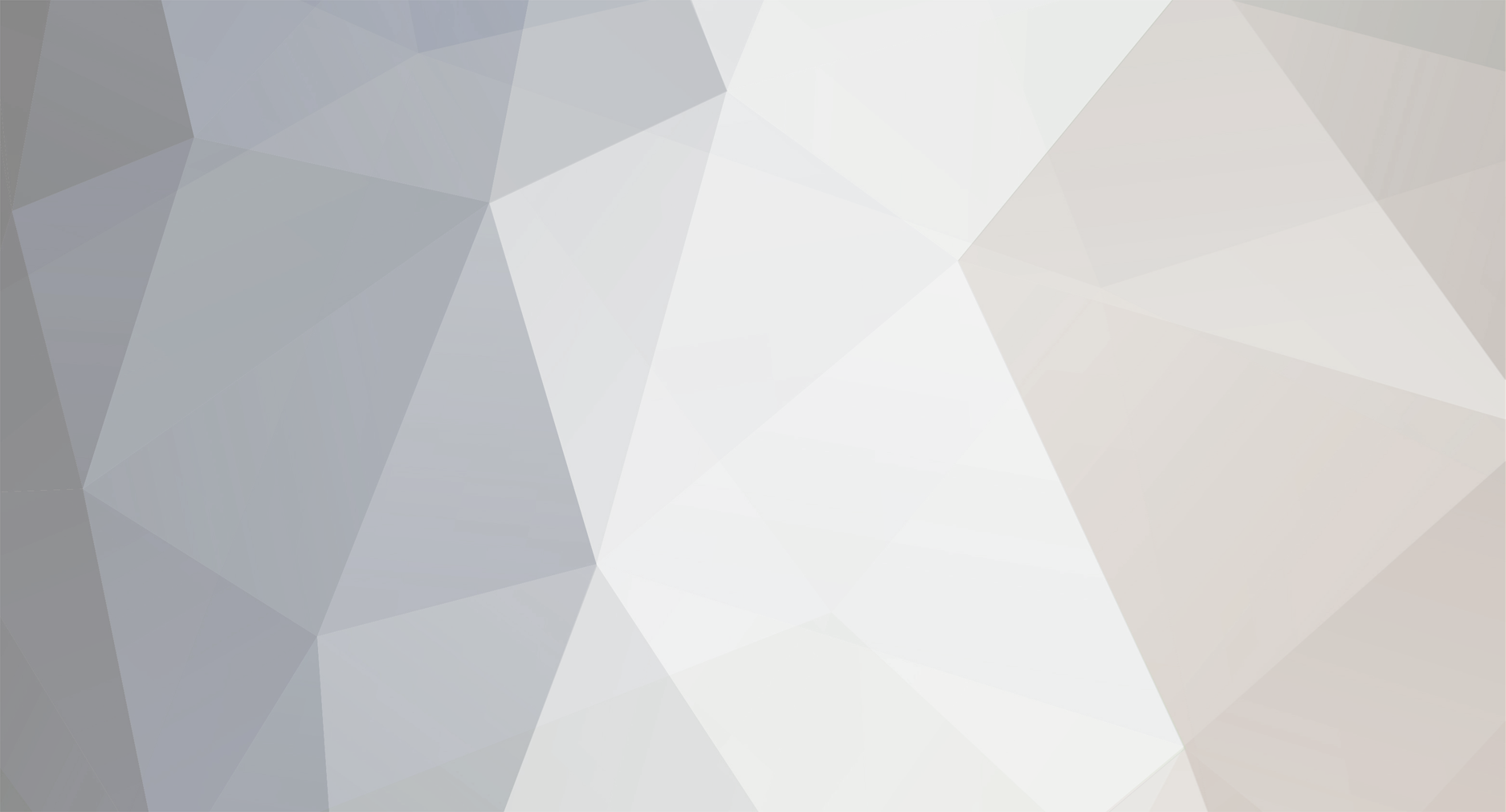
Chris_Collins
Members-
Posts
225 -
Joined
-
Last visited
-
Days Won
1
Content Type
Profiles
Forums
Gallery
Blogs
Events
Articles
Store
Downloads
Everything posted by Chris_Collins
-
restoration Morris Tilly late model
Chris_Collins replied to Chris_Collins's topic in Blogs of MV restorations
A bit more progress of the timber work. The side pieces are all now screwed and glued but not attached to the metal sides yet. The front main cross bearer is complete and joined up to the main pillar supports. The rear main cross bearer is cut to size and clamped in situ to hold the sides up. I am waiting on more timber for the rear tailgate hinge supports and rear floor step. I need that assembled to help get the whole body square before I put the floor boards in and make a tailgate. But before I can do that though I have to rebuild the inner wheel arches. -
restoration Morris Tilly late model
Chris_Collins replied to Chris_Collins's topic in Blogs of MV restorations
"Using the other set of rear panels allowed me to lay out the timber frame as I cut each piece. A very time consuming excercise with each piece lapped into two others. I also did two sets at once so glad to have that out of the way." -
restoration Morris Tilly late model
Chris_Collins replied to Chris_Collins's topic in Blogs of MV restorations
More inspired work from the House of Neville. "With one set of rear side panels in place with their timber support and the roof all bolted up and in the correct position, I bolted a brace across the two B pillars to keep it all in place and then made up another new timber bulkhead which bolts to the rear of the roof. " -
restoration Morris Tilly late model
Chris_Collins replied to Chris_Collins's topic in Blogs of MV restorations
wo sets done. The formers barely suffered at all. Now just need a lot of holes drilled in them. -
restoration Morris Tilly late model
Chris_Collins replied to Chris_Collins's topic in Blogs of MV restorations
First panel done. Came out quite well. -
restoration Morris Tilly late model
Chris_Collins replied to Chris_Collins's topic in Blogs of MV restorations
One of the plywood sheets was laid inside the metal blank and the shape traced out with appropriate allowance for the folds. That shape was then cut out of the metal blank x 4 and then the two plywood sheets were bolted together with the metal sheet sandwiched in between. A few clamps were added to secure the edges. I only need these formers to survive long enough to make four panels so they don't need to be too elaborate although I need 30 mm folded over for the wheel arch in a circular pattern which needs a lot of slow tapping and is a significant stretch.. -
restoration Morris Tilly late model
Chris_Collins replied to Chris_Collins's topic in Blogs of MV restorations
Time to finish the side panels. First they need trimming to shape and folding the edges. I bought a couple of sheets of heavy plywood to use as a former. Placing an original panel to trace the shape I then drill a few holes into the plywood which are shared by both metal sides. The two sheets of plywood were bolted together through those holes and the shape cut out. -
restoration Morris Tilly late model
Chris_Collins replied to Chris_Collins's topic in Blogs of MV restorations
some time ago I had pieces folded up to form the rear body sides. I had the front and top fold done and the rest I will hand form. Now the roof is on I can start on the rear body. I started by supporting an original side in place to use as a guide for the main timber support. This has been marked out, cut and holes drilled to line up with the cage nuts in the B pillar. This is then placed on the new panel so it can be scribed out and cut to shape. Attached Thumbnails -
restoration Morris Tilly late model
Chris_Collins replied to Chris_Collins's topic in Blogs of MV restorations
Second tank completed. The ends and baffles on the second were not as good so I put them in the electrolysis bath for a few days. The ends have some fine pin holes in them. I then had them re-zinced at a local electroplaters. Before reassembly I ran some solder over the holes on the inside of the ends and then put it all together. They now only need pressure testing and painting. Chris had painted both rooves and all the timber inserts. These have been reassembled and the first one installed. Timbers for the spare wheel carrier have been cut and fitted. The timber doesn't bolt down satisfactorily to the roof contour and i am thinking of steaming it to get it to hold its shape. My plan is to crank up my Wiles Cooker to provide the steam and pump it into a piece of pvc pipe. A job for later. Attached Thumbnails -
restoration Morris Tilly late model
Chris_Collins replied to Chris_Collins's topic in Blogs of MV restorations
I popped the ends off the body of the tank and firstly riveted and soldered the bottom drain plug flange. Next the fuel line filter and pickup. This has a nut on the inside to tighten up the brass fitting and then soldered on the outside. The baffles were then soldered in and then the fuel filler inlet flange and fuel gauge flange were riveted on and soldered. Lastly the ends were pressed back on and crimped tight and all the seams soldered. Not the neatest of soldering but I am very happy with the end product. Pity it will be slung underneath never to be seen. Attached Thumbnails -
restoration Morris Tilly late model
Chris_Collins replied to Chris_Collins's topic in Blogs of MV restorations
I removed this tank and found it had been modified by blanking off the original filler neck and then fitting an original Tilly neck. Once removed I have a complete set of correct bits for each tank. Attached Thumbnails -
restoration Morris Tilly late model
Chris_Collins replied to Chris_Collins's topic in Blogs of MV restorations
I got the end flanges, baffles and most fittings off the car tank but I only had one filler inlet flange and that being on the complete Tilly tank. The car being different. This Tilly I knew had a foreign tank fitted. Attached Thumbnails -
restoration Morris Tilly late model
Chris_Collins replied to Chris_Collins's topic in Blogs of MV restorations
Once this seam was finished I lowered my press to its bottom and placed a plate at each end of the tank. It pressed in perfectly. I need to now attach all the external flanges and baffles before permanently attaching the end flanges. Attached Thumbnails -
restoration Morris Tilly late model
Chris_Collins replied to Chris_Collins's topic in Blogs of MV restorations
My late father was a plumber and used to make a lot of galvanized iron tanks when I was young. I remember being about six years old when I began helping him by holding the rivet dolly on the inside while he hammered the tin rivets from the outside. As the tanks got higher I had to work off a ladder with each hit almost knocking me off the ladder. Anyway, I still have his old tools which haven't seen any use for many years. Who'd a thought. I supported a piece of railway line in my vice as the anvil for swedging the lap joint. Attached Thumbnails -
restoration Morris Tilly late model
Chris_Collins replied to Chris_Collins's topic in Blogs of MV restorations
I checked each fold in the end flange as I went. It was a little bit of guesswork as to exactly where the next fold was to be positioned but I managed to get it pretty close. Once the four folds were done the lap joint was closed up. To keep the joint nice and tight I forced a couple of pieces of timber inside. Attached Thumbnails -
restoration Morris Tilly late model
Chris_Collins replied to Chris_Collins's topic in Blogs of MV restorations
The first fold with that pipe came out a little too tight so I opened it up a little and pressed it again with a larger pipe. Instead of altering the press I slid the larger pipe over the thinner one. This came out exactly as I needed. Attached Thumbnails -
restoration Morris Tilly late model
Chris_Collins replied to Chris_Collins's topic in Blogs of MV restorations
The tanks are 865mm long and I had to work out a way of folding the curves in to follow the seams in the end flanges. A bit of scrap steel and pipe and the old G clamps into action again. I used a piece of 100 mm heavy steel channel and a piece of 50mm pipe and welded some scrap in the inside of the channel to centre the pipe. The four locking pliers help centre the sheet where I want it to be without moving until there is some load on the sheet. Attached Thumbnails -
restoration Morris Tilly late model
Chris_Collins replied to Chris_Collins's topic in Blogs of MV restorations
I got some galvanized iron cut to the exact size required and dressed both ends to form a lap joint for the main body of the tank. Another job for my hi-tech folding equipment. Attached Thumbnails -
restoration Morris Tilly late model
Chris_Collins replied to Chris_Collins's topic in Blogs of MV restorations
Both ends and baffles have been removed and they will clean up quite well. There is no rust to worry about so I melted off all the solder and removed the drain plug fitting, and the fuel line pick up and fuel gauge float. The flanges for them were sweated off and cleaned up. I will get a piece of galvanized iron and shape up for the replacement body and solder it back together. If needed maybe some POR 15 fuel tank sealer to cover the ends. Attached Thumbnails -
restoration Morris Tilly late model
Chris_Collins replied to Chris_Collins's topic in Blogs of MV restorations
The Tilly tank has a big hole in the bottom and I suspect a very untidy interior. They share the same stamped end and flanges for filler necks and guages. So I opened up the car tank and removed one end and baffle. Looking at the end I am contemplating getting some steel plates lazar cut and pressing some new end pieces in the same pattern. However before I try that I sweated that one end apart. It looks solid and might be able to be cleaned up and re-zinced. If I can recover all four ends and the baffles and recondition them I will just have to fold up the body of the tank and solder all the parts back together. Attached Thumbnails -
restoration Morris Tilly late model
Chris_Collins replied to Chris_Collins's topic in Blogs of MV restorations
I've digressed a bit to have a look at the fuel tanks I have to work with. This is a Tilly tank. Filler on top and about 150 mm longer than a car tank. Attached Thumbnails -
restoration Morris Tilly late model
Chris_Collins replied to Chris_Collins's topic in Blogs of MV restorations
Heres some more news from the House of Neville skunkworks! PS if anyone has leads on getting a Solex 30 HBFDO Carbie, I'd be very interested "Chris has got the roofs painted while I repaired a second set of seat bases. We had one complete set and the other only had the bottom parts. They are only made from 1" angle iron so it was pretty straight forward to cut and drill and rivet the top section. Attached Thumbnails " -
restoration Morris Tilly late model
Chris_Collins replied to Chris_Collins's topic in Blogs of MV restorations
Now that the body is painted the previously rebuilt axles, springs, dampers and steering gear can go straight on. The front torsion bar was really hard to align and required the use of a porta power to push the axle mount forward and the chainblock to pull the axle up. To stop the whole front end lifting I had to put a piece of timber under my gantry cross beam to work against the chainblock. My gantry spans the width of my shed and travels on rollers the full length of the shed. It is made from railway line and other scrap. It enables me to pick up anything and move it to anywhere in the shed. The railway line is supported on steel posts which also double as the support posts of the shelving when I built the shed. Makes life very easy. Attached Thumbnails -
restoration Morris Tilly late model
Chris_Collins replied to Chris_Collins's topic in Blogs of MV restorations
The firewall panel and dash panel and pedals have gone for sand blasting. The pedal pivot bolts and bushes are all flogged out so I got some bushes from a bearing supplier that will fit and bought some bolts which I turned down on the lathe to suit. Attached Thumbnails -
restoration Morris Tilly late model
Chris_Collins replied to Chris_Collins's topic in Blogs of MV restorations
I bolted a piece of scrap to the bumper brackets and to where the tow bar attaches, (which has also been fitted). By hoisting it on a chain at the back and using the block and tackle at the front I fashion a temporary rotiserie for painting. Attached Thumbnails