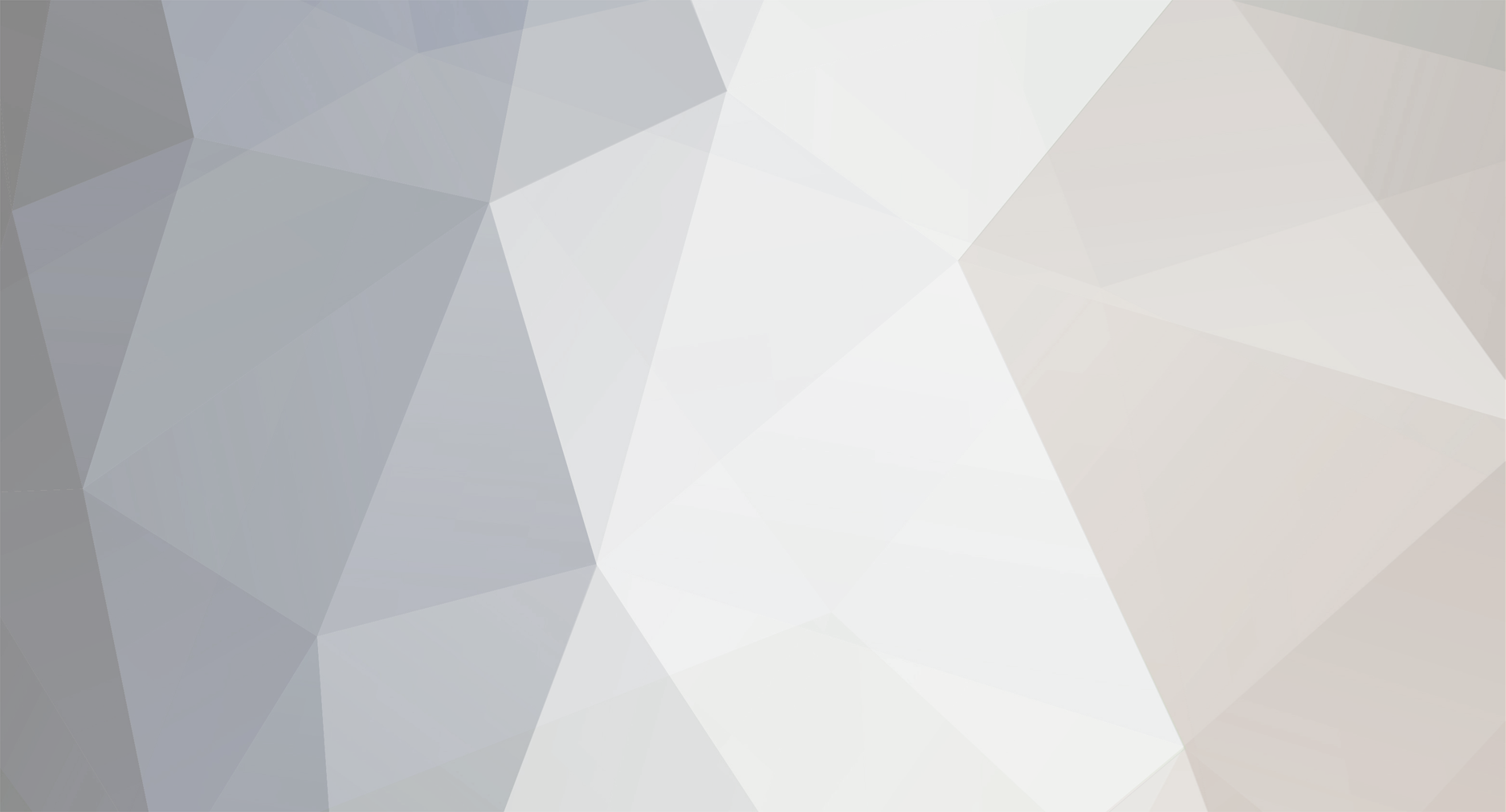
BenHawkins
Members-
Posts
861 -
Joined
-
Last visited
-
Days Won
3
Content Type
Profiles
Forums
Gallery
Blogs
Events
Articles
Store
Downloads
Everything posted by BenHawkins
-
I made the pins for the universal joint at the same time as those for the 1914 Dennis. I have now also made the four bushes; these will have to wait to get hardened. At the NEC car show this weekend John Dennis very kindly presented me with a copy of the test record for engine 4222. At 50 BHP and 0.75 pints per HP per hour I should be able to consume 37.5 pints per hour. I should not be able to consume more that 25 pounds worth of petrol in an hour (at current prices)! The test date of 8/2/1911 supports the engine originally being fitted to a Liverpool Salvage Corps tender. I am 50% sure it is this one:
-
I have reopened negotiations with an Indian supplier and added 50 off 5/8 Thackery washers. Can't promise anything though.
-
I was embarrassed into fitting that the day after your visit but did not take a photo so it did not get posted on here. We spent yesterday at the Regents Street motor show looking at ridicules contraptions that I can't afford! It has been another slow week for truck work but I have picked up the parts from nitriding. I still need to fit the gearbox in order to work out how long the prop shaft needs to be and the "jaw and star piece" have not been cast yet for the Hooke's coupling. And some more parts have had their first coat of gloss.
-
Then it was just a case of fitting taper pins and giving the whole jaw another coat of primer. I have also cut twelve brackets from the 2" angle. The secure either end of the three rails over the bed. I gave them a quick blast and a coat of primer. My glamorous assistant machined the numbers off a set of bolts so they had a coat of primer at the same time.
-
A trial fitting of the jaw to make sure the neutral notches fall in line. The jaw is fitted to the end of the selector rod with two taper pins. The precision of the alignment of the notches to the jaw is fairly important. The jaw was clamped on a parallel to keep it level, the rod was clamped in the vice using a piece of aluminium rod in one of the notches. Just to complete the setup an engineers level was used to check the rod was parallel with the table of the milling machine. Then the rod could be drilled through (in the location of the existing holes in the jaw). A taper pin reamer was used to open the holes up until the I could see clean metal in both sides of the jaw.
-
A bit more sanding and painting this week. However I remembered the selector rod needed completing. I started by marking out the detent notches from the old broken rod and then tilting the head on the milling machine. Followed by milling a slight flat between them. And filing the slot in the bottom of each notch.
-
The tail boards have had another rub down and undercoat. Still not quite as smooth as I would like but hopefully it will not be too long before they can be fitted. I have spent several hours making swarf from a piece of 1.5" EN24T on the lathe. The result is four bushes for the Hooke's type universal joint. Here are two of the bushes being tried for size in the transmission brake hub. I need to book half a day off work now so I can drop a box full of parts off for a 45 hour nitride cycle. This will involve heating the parts to around 500 degrees Celsius in an atmosphere of ammonia gas and should harden a layer about 0.020" deep and give a hardness of around 530 Vickers.
-
The brass countertop hinges are visible in various Dennis plans and are still available to buy new. I think they would probably have been left as plain brass but not polished. I could not find a new catch but the one I used is off an old piece of furniture. I milled the catch plate from a piece of brass angle. It all seems to look OK now the paint is on and the boards are fitted. The countertop hinges mean the whole door will fold flat making access easy. I managed to get the side rails smooth enough for their first coat of gloss.
-
Despite quite a few hours being spent on sanding and painting I don't have many photos to show this week. However, there is this one showing the hinges and catch fitted to the hatch in the floor boards.
-
Thanks, that is where most of the information has come from. In one of the catalogues of photos there is a picture of this exact vehicle but unfortunately prior to the registration number being painted on.
-
We did manage to get in touch with a descendant of Sir Ernest Shentall this week but unfortunately there appear to be no family photos showing the vehicle. It has been a fairly quiet week for mechanical work as it has mostly been painting; but this did mean four of the floor boards were ready to fit. The pre-delivery photo shows a pair of tie rods between the side rails and the tail boards. After measuring the dimensions I cut a length of 3/4" diameter EN3 steel and welded the mounting to one end. The next stage was to put the bend in at that end before aligning the mount on the other end. They still need a bend adding at the unpainted end. I have filed the oil groove in the shoulder screw so once I have turned up the bushes I can take a batch of parts for nitride hardening.
-
These lamps turned up this week. They are of the type fitted to the Leyland lorries owned by CP&Co and are stirrup mount.
-
The coping irons are now fitted but most of the week has been taken up with painting. Whilst waiting for the various coats to dry we have been trying to track down the original registration number, this time going through old newspapers. We found three accidents. 26th July 1919: Ernest Shentall's lorry drives into a clothiers sunshade and smashes their window. 22nd October 1920: Ernest Shentalls lorry was travelling down the High Street in fog, a Ford car heading up hill swerved to avoid collision and crashed into the house of Fred Staniforth. 22nd August 1925: FATAL HESITATION"Somebody sitting on a fence shouted "Eh Up". I looked round and saw the motor lorry only 10 yards away from the boy, who hesitated, turned partly around, and then struck off again. The front of the motor caught him, knocking him 10 or 12 yards, and both wheels passed over his body, killing him instantly." Thus an eye witness graphically told the Coroners jury at Chestefield last night, how Harry Kingswood (13), 138 Lancing Road, Sheffield, was fatally injured by a four-ton motor lorry belonging to Sir Ernest Shentall, Chesterfield, on Thursday. Martin L Caiter, 125 Cresswell Road, Clown said he and his brother in law sat on the front with the driver. They had got nearly to the bottom of Tinkersic Hill on the Brimington Road when they saw a steam roller on the left side of the road, and a ford van on the other side. Both were stationary, practically opposite each other and facing Chesterfield. There was plenty of room for their lorry to pass. Owing to the road being under repair and the fact that they had had to stop to allow another vehicle to pass, they were proceeding so slowly that the youth could have run at the back of the lorry. When they were practically level with the steam roller, the deceased ran in front of them, although the driver had sounded his hooter several times. Witness felt a bump, and the driver pulled up in 10 yards. In his opinion it was a pure accident, and nothing more could have been done than Sims the driver, did. We contacted the Derbyshire archive and Coroners office but unfortunately no other records seem to have survived. As Shentall is an unusual name I think the next step may be to send a letter to everyone with that name in the phone book. Back to mechanicals: I needed to add the oil grooves to the universal joint driving pins. The first stage of the process was to put masking tape around to mark the required helix, followed by starting the groove with a 3mm angle grinder disc and finishing off with a 1/8" needle file. I have finished machining the diameters and head on the corresponding shoulder screw, this still awaits similar oil grooves. The final related job this week was to fit a winch so we can get the truck back in the garage after pushing it out, either I am getting weaker or the truck is getting heavier with all the bits we are adding.
-
Trial fitting of the coping irons and rear hoop. It all looks like it will work. Removing all the ironwork again so I could give all the timber a coat of undercoat.
-
Underpants are the minimum "Personal Protective Equipment" required, other PPE is available! I do own a circular saw but I can follow my line more closely with a hand saw. The first job this week was to cut the thread on the universal joint pin and add the split pin hole. Much of this week has been taken up by priming the floor boards, first with a thinned coat followed by an un-thinned coat. I don't have enough space to do them all at the same time. I had made a mistake with the angle hoop so had to splice an extra piece in the middle but now all the welds are flushed off and it has a coat of primer it looks like the one in the delivery photo. I cut some lengths of 40x12 convex steel bar, drilled and countersunk them before welding them to make up the coping irons (thanks to "Motor Body Work for Commercial Cars" I now know what they are called).
-
I made a drilling jig and lined up the planks for the back board with some scribed lines for fitting dowels Checking the boards fit together. Using the 3, 4, 5 triangle rule I drew on a line at one end and trimmed it square, followed by marking off the line and cutting to length.
-
One day to shape the bearers but I did think my arm would fall off at the end of it! I have been looking through early photos and magazines but the bed is rarely on show. Gloss paint or varnish did not seem right as the finish would be scratched by the crates and would need to be easily maintained. My good friend Mick who provided the chassis in the first place lent me "Motor Body Work for Commercial Cars" (1916) and this seems to have the answer: Suggesting the floor should be dark grey or black. Back to manufacturing: Cutting and welding the rear angle iron hoop. The universal joint on the back of the gearbox has the first pin slotted so it can be retained by the second pin (a shoulder screw) with a slotted nut. I have only roughed out the shoulder screw so it needs to be finished and oil grooves added to both pins before they are nitride case hardened.
-
I do hope the Napier engine can turn up as well. Lets all keep looking. By messing up my steel order it did mean we had this afternoon free to check the engine fits correctly in the chassis. It was extremely rewarding to simply slot the 1/2" BSW bolts through the existing holes as if the engine has always been there!
-
Douglas fir tongue and groove boards cut to cover the bed area leaving an opening for the access panel for the back axle. With the access panel in place. The factory photo does not show the finish of the floor boards, seeing the boards here I am tempted to just varnish them. Unfortunately I messed up the cutting list for the steel capping rails so I need to order some more. I would like to thank my friends for their help this weekend.
-
I had invited some friends around for the weekend. The weather was a bit wet on Saturday so we had to stay inside where the space is a little limited. After bolting the bearers to the chassis we were able to lay out the timbers for the perimeter rail to allow the lengths to be scribed. We made a drilling jig from a reject casting to keep the drill square to the timbers, then counter-bored for the nuts and washers. The perimeter rail will later be covered by a steel capping piece. More of the timbers were primed and allowed to dry over night before reassembling and adding the corner braces I had made previously.
-
-
-
The rear universal joint socket had been getting in the way so I decided to bolt it in place. I still need to sort out some Grover washers for it and to fit the split pins. I had a day off work this week to make some progress towards manufacturing the bed. After marking out the ash bearers I cut the radius with a hole saw and the straight lines by hand. Then to get the clearance to fit the saw in the central section I cut a number of slots with the circular saw. Followed by chopping the wood out with a chisel.
-
A bit less progress this week as Beaulieu autojumble, auction and also collecting the engine for the 1908 used up around three days. After countersinking some of the laser cut profiles I bent them in the press. To give corner brackets for the bed. The timber for the bed has arrived as well and will hopefully take shape soon.
-
Cam followers, valves and springs. Unfortunately not a full set but relatively easy to copy. Four (yes a full set) of cylinder blocks. 120mm bore so the 35HP engine, this is exactly the same external size as the 110mm (original) engine but an extra 7 RAC horse power. White and Poppe guaranteed 51BHP at normal speed. Some scrubbing revealed the engine number, pretty clear as 4222. However when I looked at my records it appears to have started life in a Liverpool Salvage Corps tender rather than the portable pumping set frame shown in the photos from the 70s. Something else to research! When loosely assembled it really does look promising!