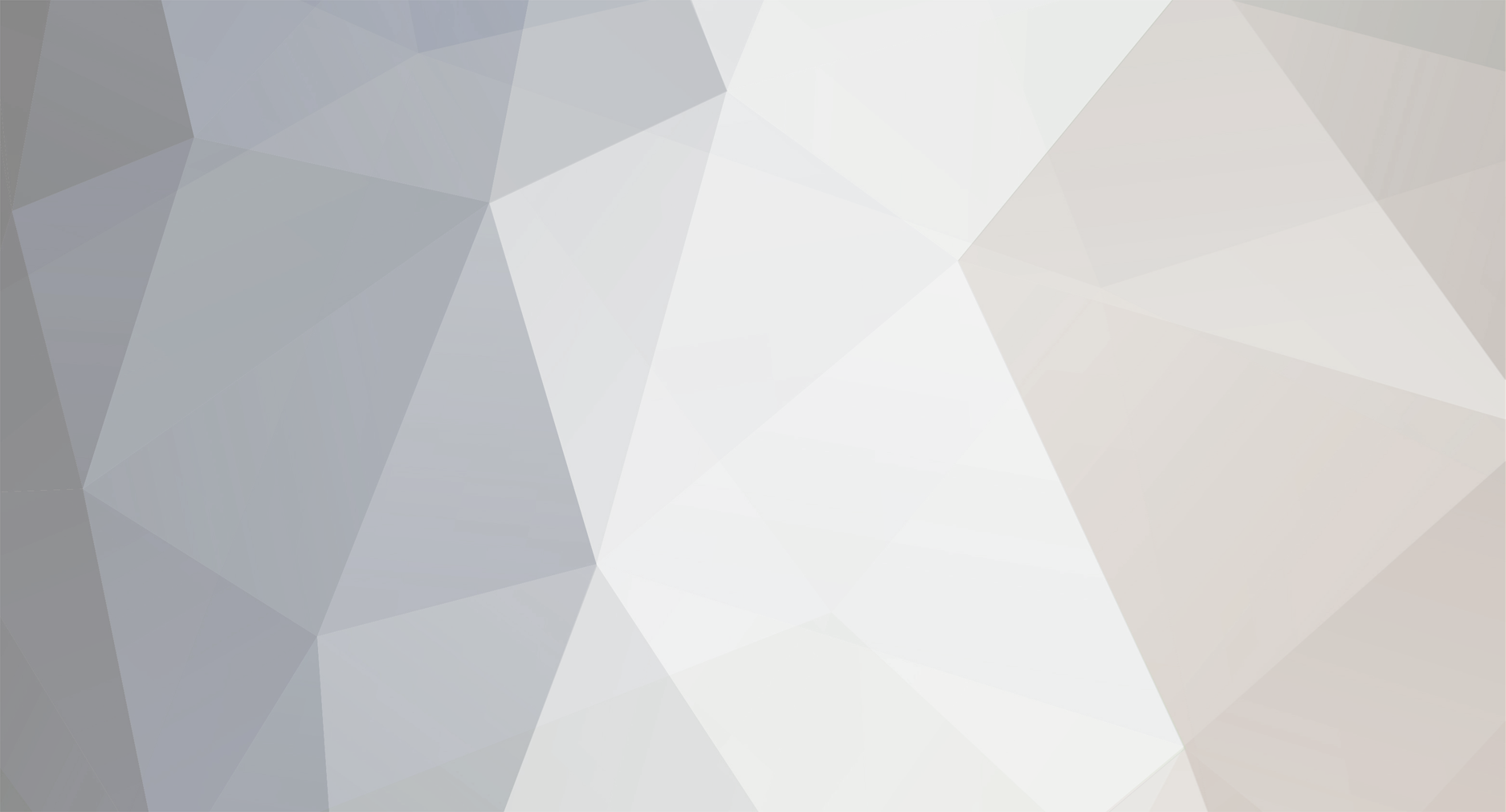
BenHawkins
Members-
Posts
861 -
Joined
-
Last visited
-
Days Won
3
Content Type
Profiles
Forums
Gallery
Blogs
Events
Articles
Store
Downloads
Everything posted by BenHawkins
-
When machining the ball I raised the table by about 0.010" each time, running the boring head at 200 RPM and each revolution took several minutes. I am not sure exactly how long it took but I would guess a minimum of 5 minutes per revolution (on the final pass, much quicker when roughing out) and therefore given it was a 3 inch diameter a feed of less than 0.009" at the centre and 0.0045 at the edges. The drawings do not ask for the ball or socket to be hardened, but the drive pin is again "UBAS Steel Case Harden". I have chosen to use EN24T and have it nitride hardened. This called for spherical ends so I have used the same method but required a way of holding it so I took a scrap of aluminium bar, bored it through at 1-1/8" and used a hacksaw to cut a slot so I could use a pinch bolt to secure the drive pin. Finally I put the drive pin in the lathe and polished up the ends. I need to make a few more parts for hardening so I can justify the minimum charge. Phosphor bronze blocks fit on the end of the drive pin and run in the slots in the socket. Having struggled to find a metal merchant to supply some at a reasonable price I ended up purchasing some from an online auction. It should keep me busy for a while when it arrives as there are a number of oil grooves to cut in the blocks. I cut the slot in the gear selector drop arm so I could clamp it to some 1" bar and machine the boss on with a ball nose slot drill using the rotary table on a milling machine. I then transferred the blank to the shaper to remove some of the excess material. This is usually a great machine as I can leave it running whilst working on other jobs. However the magic smoke escaped from the 20 year old variable frequency drive that I use to run this machine. I found it in a skip and it was only just rated for this motor so I have ordered a more appropriate one but at present no further work has been done on this component other than order some HSS to make a slotting tool to put the keyway in.
-
I need the tool to fit the universal joint to the 1908, but as I don't strictly need to remove the 1914 one I will probably do more harm than good in attempting any more progress on that task!
-
The next job I wanted to do was the "End for Arbor Shaft, Part Number 1333/4". Another part where the original drawing has survived. This is a fairly complicated part as it has a spherical end drilled for a drive pin and has to be able to articulate in the socket I made previously. I decided this was best done in the milling machine but first required me to machine a back plate with an 8TPI thread to fit my dividing head. Once again when setting it up with the blank I had machined previously I was right on the size limits for my milling machine and the tail stock had to overhang the table. I had to machine a left hand boring bar from a piece of 1/2" HSS as my boring head screws onto an arbor and would therefore unscrew if I reversed the direction. For those of you who have not seen this process before it basically works on the theory that if you cut a sphere in any plane you will end up with a circular cross section to the cut. The next stage was the cross drilling, starting with a stub drill and working up to the biggest drill I could fit on the machine (a 20mm reduced shank drill fitted in a 1/2" collet). I then refitted the boring head and opened the hole up to 1.120". Once the end is brazed into the prop shaft I will then run a reamer through to open it up to 1.125". The final machining stage was to swap to a fly cutter and put two flats on, using the dividing head to make sure they were 180 degrees apart and symmetrical about the axis. Polishing with some 800 grade silicon carbide paper improved the surface finish and finally I checked for smooth operation inside the socket to make sure I had generated a good approximation to a spherical surface. I need to lay all the transmission out soon to see what parts I am missing.
-
This vehicle was originally purchased by Ernest Shentall of Chesterfield; the other day I was visited by the son of one of the last owners of the company. He left me with five potato sacks as would have originally been carried (although these are a little later). I also have a fruit crate but I will need to find some more. I dropped the pattern for the clutch off when I collected the casting for the transmission brake drum. I don't have the drop arm for connecting up the gear linkage so I drilled the holes in some square bar. There is a slightly longer original to show how much of this piece of bar I need to turn into swarf. [ATTACH=CONFIG]116780[/ATTACH] I wanted to remove the flange for the rear universal joint so I brazed some 1/4 silver steel rod into a laser cut blank. All I managed to do was bend the silver steel so I might leave the flange in place as there is nothing really wrong with it.
-
I have been putting a little more thought into the original model of engine fitted. Drawings have survived for a number of the parts, these include the timing gears so we know they were 3.25 module, 33 and 66 teeth. The major components I am missing (and have no drawings for) are the crankcase, sump and crankshaft. As I have three cylinder blocks I can be fairly sure of the centre distance of the valves and general arrangement drawings show the distance from the engine mountings to the crankshaft axis. As I have some connecting rods as well it means I can work out position of the camshaft, crankshaft, cylinder blocks and crankcase relative to one another. There need to be two other gears, another 33 tooth for the magneto and one for the water pump with a lower tooth count. I can't be quite so certain of the centre distance between cylinders or the dimensions of the tappets but hopefully I can measure one of the surviving models. There are photos of the crankcase from above and below in the inspection department at White and Poppe but unfortunately I do not have permission to reproduce them here. I will continue to draw up the components I have and hope more parts turn up before starting to manufacture any missing parts.
-
More transmission parts have been blasted, primed and painted. I dropped the transmission brake pattern off at the foundry so we are slowly ticking off the missing parts. I have also drawn up the mudguards and placed an order for them, hopefully I can pick them up towards the end of July. Taking measurements from the clutch showed that in addition to the corrosion it was quite warped as well. This meant the only real solution was to build it up into a pattern. I started by gluing strips of MDF on and building other areas up with filler. It is marginally too big to fit my lathe so I mounted the rotary table on the milling machine and tilted the head to the 12 degree angle required. The clutch would not have been possible to pull from the sand so I decided to build up the inner surface as well with filler. Originally this would have been done with a core but this seemed a bit excessive for one casting and I can always mill the casting back to standard dimensions. I tilted the head 2 degrees in the other direction to get the draft angle. I have given these surfaces a coat of primer but I still need to add some threaded bushes into two of the holes so the pattern can be lifted from the sand and build up the mating faces to give me some allowance for machining. Hopefully I can drop this off when I pick up the transmission brake casting.
-
A good friend of mine assured me he had a spare Dennis 2 ton clutch in his shed so we visited to have a look. After a couple of hours of shunting vehicles around and dropping the boiler out of a steam lorry we spent a few hours emptying a shed to find the clutch (and some parts for his projects!). The crack and broken rim was a bit of a concern and where the clutch stop acts it has worn down to less than 0.1" Removing the woven lining showed even more damage. I will have to decide if it is worth investing in an AC TIG welder to have a go at repairing it or just build it up into a pattern with ply and filler. I already have clutch stops and these have been blasted and primed. The friction linings need to be replaced.
-
All the service engineers have been away from work over the past couple of weeks so I have been standing in and travelling around the country. Last weekend was spent picking up parts and visiting an archive to try to find a registration card for when this chassis moved to Lincolnshire, we only got as far as registration cards for 1922 so we need to return to Lincoln at a later date. Milling of the UJ socket has continued. And once the rotary work was finished I bolted it to the table and roughly shaped the profile for the smaller front flange. Followed by a bit of final deburring and filing. And finally a clean and coat of primer.
-
Thanks for that, always nice to compare the different manufacturers methods. We went away to look at another unrelated project for some of the weekend but have still made a few bits of progress. I spent a few hours straightening the gills on the radiator tubes. Looks quite nice when pushed out in the sunshine. It was fun to let it roll down the slope and be able to steer it and stop it with the handbrake. I have removed most of the excess material from one side of the universal joint socket. I will swap to a long series cutter to finish it off then repeat the process on the other side. The foundry had problems with my MDF pattern for the rear brake drums delaminating when pulling it from the sand. As the transmission brake pattern is even deeper I have gone for a steeper taper (4 degree included angle) and turned some aluminium inserts. These are 12mm diameter on the other side, 9.5mm diameter through the bulk of the pattern and tapped M6 on this side so the bolts can be used to extract it from the sand. Hopefully this pattern will be less traumatic. Another rub down and coat of paint and it should be ready to drop off at the foundry.
-
Even with the Bridgeport milling machine it was not an ideal fit, I had to remove the handle from the rotary table as the arm did not clear it. I then operated the rotary table using a bolt through the spindle. I made the arm from EN3 so I had the option of welding if it all went wrong. However I did have visions of a welded on socket fatiguing through. The first attempt at bending the arm left it with about 3/4" of clearance between the arm and the spring retaining plate but there was not enough space left for suspension travel. I have now reduced this to about 1/8" to give maximum suspension travel. The drag link is at quite an angle but you can see this in the factory photos and it is unusual to this particular model. I did look at whether the ball joint could mount under the steering arm but then it would hit the leaf spring before full lock is achieved. Basically after many goes at making it work I think I must be within about 1/8" of where the ball joint was originally positioned.
-
Having decided where the ball joint needed to go on the steering arm I thought about how to make the tapered socket. I was able to find the angle on the original drawing; 10 degrees and 52minutes. Why they chose such a strange taper I don't think we will ever know but I decided I should be able to make the taper on a Bridgeport milling machine (my mill is too small). The angle equated to slightly over 0.095" per inch. After setting the ball joint axis concentric with the rotary table and positioning the head on the same axis I tilted the head until raising the table one inch gave a deflection of 0.095" on a dial indicator. Then fitted a 3/4" end mill to machine the socket. Then checked the depth against the ball joint. Trying it on the chassis again showed the drag link was slightly too long as full left lock could not quite be achieved so the drag link was shortened by 1/2" The outside of the socket was shaped with a combination of saw, angle grinder and files. And when retrying the parts it was possible to achieve full lock in both directions.
-
After turning the diameters of the transmission brake pattern I gave it a coat of primer. After sanding and a further coat of primer it looks like this. We went to Beaulieu auto jumble yesterday. Although this is not a Dennis pump I should be able to fit it in the available space. I have primed the pedal levers and drilled the treads. I drilled a number plate and fitted it to the brackets.
-
I was fairly distracted by the Keeley auction this week but came back with nothing. There was a little bit of progress on the pedal levers as I finished welded them together. Followed by blasting and priming the throttle one and turning pieces of bar to link them to the treads. Cutting out some MDF rings and gluing them together has given me the blank for the transmission brake pattern. I will need to mount it up on the lathe to machine a taper on the diameters.
-
It is true three phase supplied via cables from the national grid, one of the advantages of converting a building from industrial to domestic use. I have mainly been doing building work and tidying the other garage but managed to fit in a few tasks such as fitting the brake lever. Then adjusted the radiator alignment so we could fit the other bonnet side. We placed this petrol tank in place so we can get a better idea of pedal/floorboard positions. And finally checking how the gearbox support frames will look.
-
This weekend we took the Chivers (or Shivers) Jam Van to Brighton again so no time to work on the Dennis. However during the week I milled a flat on the brake lever followed by drilling and tapping 1/2"BSW, turned and threaded boss and silver soldered it. After fitting the pivot shaft I cross drilled and used a taper pin reamer so it could be held in place with a taper pin.
-
Thanks for sharing the photos, it looks like it is in good mechanical shape whatever you decide to do with the chassis. Despite the Dennis records being fairly complete the subsidy lorry index is missing so it is difficult to be very accurate in dates. The nearest data point I have for that chassis number is 11783 was sold via Atkeys (an agent for Dennis based in Nottingham) on 25/10/1918. However I don't know if this chassis was new at that stage. So I think we can at least be fairly confident that your chassis is 1918 or earlier. Great to see another survivor!
-
Sometimes I even surprise myself with what can be achieved with a pile of rust and thousands of hours!
-
I think I finally have the steering arm bent correctly so I should be able to get full travel. The parts book lists felt as fitted to the bonnet brackets so I have riveted some on. Then with a bit of fettling was able to fit a bonnet side and hinge pin.
-
With quite a large discount the internal profile cost 200 pounds to wire erode because the socket is so deep, the outside would have cost a further 400 pounds. So deciding to use the shaper was purely a matter of economics. The internal tool for the shaper was not long enough and although I could have made a longer one I was not convinced I would be able to get sufficient accuracy with my limited experience on the shaper. It was also an opportunity to play with the shaper. It is time to move the socket to the milling machine so I have machined a plug to support one end. Having finished machining the flats on the eye bolt for the brakes I drilled the hole. It just needs rounding off now. I warmed up two of the wing brackets to put the bend in them.
-
Whilst the shaper was working away I was able to rough out a blank for the final rod to link up the hand brake. I cut two lengths of 3/8" EN8 steel to length and we started to assemble the bonnet. A trial fitting of the drag link. It looks like I need to shorten it by 1/2" and the steering arm needs one of the bends adjusting slightly (again).
-
We clamped the gearbox in again with the straightened selector rods. Now that there are a few more parts in place it is good to see it does not hit any of them. The shaper has been working away for several hours to rough out the profile. Before turning the universal joint around and starting again. A couple more hours to go before transferring it to the milling machine.
-
I have carried on roughing out the universal joint outside profile. Whilst the shaper was traversing I straightened the gearbox selector rods in the press. They have turned out well. The pitting will not reach the gland packing so I don't think it will be a problem. I still need to make a replacement for the (broken) 3rd/4th gear selector rod.
-
I spent the weekend in London at a centenary event for the fire engine that got me involved in this rather silly hobby. However on the way to the event I picked the magneto up from servicing. The magneto coupling is not one I have seen on anything else. The middle section of the coupling was missing (looking at the wear marks it looks like it might have been quite worn) and a piece of rubber tube was secured on the outside with a jubilee clips. I think I will replace the worn pins and make the missing part from black acetal or tufnol.
-
Thanks for posting those. Quite a similar arrangement to the way this Dennis universal joint.
-
That is my 1908 Dennis (on another thread). There are three major components I am still missing; engine, gearbox and radiator. The hangers were one of the things I found most appealing when I went to see the chassis for the first time and looked under the floor. The rear most hanger in the photo is an original one; the front one is a replacement (fabrication from layers of strip) as the originals had been removed as part of the trailer conversion. This week has mainly been rather busy on a number of other tasks but I have managed to do a little more machining for the rear universal joint.