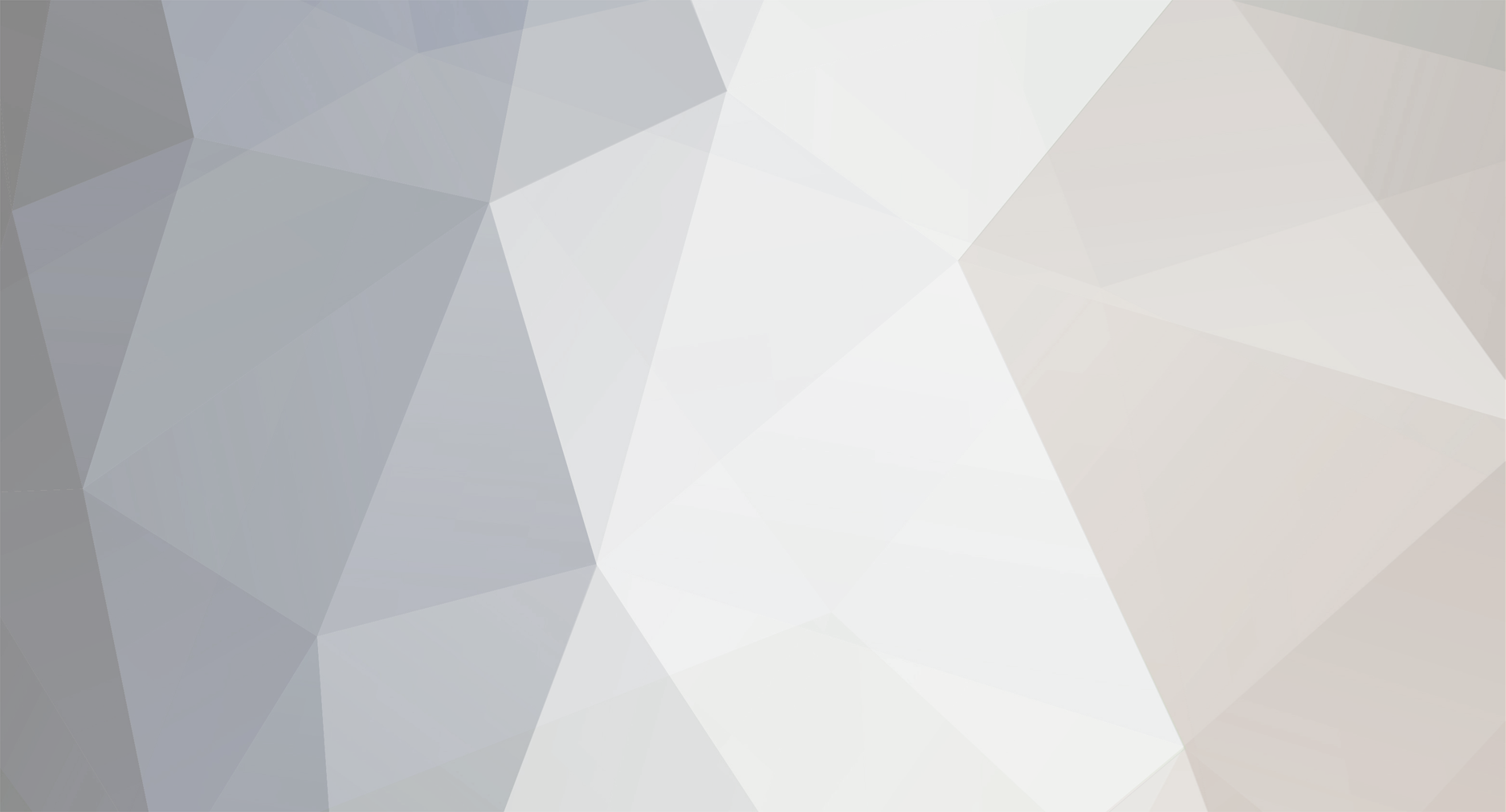
BenHawkins
Members-
Posts
861 -
Joined
-
Last visited
-
Days Won
3
Content Type
Profiles
Forums
Gallery
Blogs
Events
Articles
Store
Downloads
Everything posted by BenHawkins
-
My other job for this week was to machine the universal joint hub. It was kept off the table of the milling machine on two parallels and clamped in a machine vice, using a scrap of aluminium machined to the same length on the other side of the jaws. A centre finder was used to centre the spindle axis on the centre punch mark. Before drilling the first hole. The hole was enlarged with successive drills up to 25mm. These had to be blacksmith drills as my milling machine is relatively small. This did mean I had to peck at the holes once I was past the flutes as the swarf could not escape; but they were not long enough for me to accidentally drill the table.
-
At over 14" diameter I can't machine the clutch on my straight bed 6.5" centre height Colchester Master. However I am able to use a gap bed Colchester Student so decided that was probably the route forward. The first job was to set the compound slide accurately to 12 degrees. As it is difficult to get the precision required for this job from the marking I used dial gauges to set it up. The next stage was to check what taper I was actually machining by using a trial cut on a bar end where I had machined a groove exactly 1" from the end so I could take accurate measurements of the taper per inch. As this was coming out correct I assumed the error over the 3.5" of lining would end up being no more than a few thou and would easily be corrected as the lining wears. It is probably a bit bigger than the lathe is meant to machine. As the outside was taking shape I checked nothing was going too wrong with an angle finder. The tool holder was reversed for facing the far side off. The front face was machined gently as I did not have the security of the centre pushing the casting onto the lathe jaws. I still need to machine the four holes for the hub securing bolts, the three holes for the springs and remove some of the excess material from the inside faces.
-
Nothing too exciting this week; mostly small jobs like cross drilling bolts for split pins and opening up the gearbox mounting holes in the new chassis rails. A little more roughing out of the gear selector drop arm. I need to mark it out in the opposite plane and repeat the process. Back on post 376 I collected the clutch casting. There is quite a bit of machining to do on this so I started with clocking it up to find a good approximation to the middle and skimmed the inside face before boring the centre out to 4" diameter to fit the central spigot. I want to get the clutch finished before committing to the flywheel casting as it will be big, heavy and also expensive to machine as I don't have the capacity to do it myself.
-
All the way back on page 2, I fitted new rails for the engine and gearbox as the originals had been removed (presumably as part of it being converted to a trailer). I had looked at lots of acetylene generators but they all seemed too expensive. This auction only had a couple of veteran parts in it and did not have online bidding so I thought it was worth attending the sale.
-
I have been lining up the Hooke's joint hub in the milling machine. I think there is just enough height, so I should be able to bore it out to size. I have been to an auction this week and purchased a more appropriate acetylene generator that does not appear to have been used for several decades. It was made in Powell and Hanmer of Birmingham (who also manufactured the side and tail lamps). It still had quite a lot of Calcium Hydroxide in it.
-
We marked up where the mounting holes for the gearbox should be drilled and clamped it in place to make sure everything lined up. Then drilled the pilot holes. As the selector drop arm also seemed to line up I put it back on the shaper to continue roughing it out.
-
I reverted to the three jaw chuck and machined the other side of the transmission brake drum. Followed by marking through the holes in the hub and drilling the mounting holes. A trial assembly with nuts, bolts and Grover washers. I still need to cross drill the holes for split pins.
-
My glamorous assistant has found it on page 36! Other than one poor batch of castings I have been very lucky! I have attempted to use up all the left over Dennis parts that might have been used as "in service" replacements on this project. This original gearbox and transmission brake arrangement would have been this one with a 9.75" transmission brake. The gearbox I have is the later one (appears to have been introduced in 1920) and allows for a power take off and a larger transmission brake with pivots mounted from the gearbox rather than the chassis rails. I have kept to the original 9.75" diameter (this also matches the brake shoes I have).
-
Many hours have been spent on the transmission brake casting this week. The first job was to mount the large four jaw chuck to the lathe and centre the casting with the aid of a dial test indicator. This is often quite a challenge with castings. My pattern had left a reasonable amount of machining allowance so I was fairly confident all the important surfaces would turn out OK. I started with the boring and facing. Then machined the outside diameter. I had to skim the bore out slightly around the mounting lugs as I had made the pattern slightly too small in this area. I fixed a stop to the bed to make sure I did not end up machining the chuck jaws. And then chamfered the edges. The next job will be to turn it around and machine the other side.
-
A trial fitting of the transmission brake components showed I did not have a full set of compatible parts. The shoes do not line up with the shaft axis so that is something that needs to be resolved. I continued to repair the gearbox casing and finally gave it a coat of paint. Still a bit of work to do on the contents but the box looks reasonably tidy.
-
-
I am still unsure about casting new bits onto my fragile old castings so I have continued with my glue and screw repairs. One of the bolt holes on the lower half of the gearbox was broken off. I filed it back to a flat surface and milled a new lump of aluminium to fill in the gap; this piece only really needs to stop the bolt sliding out of the hole. It was then glued in place. Holes were drilled and tapped through both parts (but not far enough to break through)
-
Agreed, but I am not too sure where that clearance was designed in. I thought that I would turn a piece of bar to the bore size of the timing case and stepped down to the dedendum circle and then trial fit it to make sure there is clearance before drawing the gear.
-
I wonder how close it was to "modern" flux for aluminium welding; this appears to be a combination of metal chlorides and flourides.
-
The starting handle was a bit twisted so it was warmed up to straighten it out, then blasted and painted. I removed the cover from the timing gears. The drawing for one of them has survived and states 3.25 module but does not explicitly state the pressure angle so I had this gauge cut (in the form of a 20PA rack) in the last batch of laser cutting and it appears to mesh properly. The cam shaft gears have 60 teeth (obviously that means the crankshaft gear has 30 teeth). The missing water pump drive gear should mesh with the exhaust cam gear but I do not have any drawings for this. Luckily the distance between the two shafts should be fairly easy to measure accurately and it appears the gear should be a fairly close fit in the hole it has to pass through in the casting. Just using a steel rule the centre distance looks to be around 122mm and the diameter it has to fit through is 56.5mm. The Pitch Circle Diameter for the 60t gear should be 60*3.25 (number of teeth * module) so 195mm and that appears to be the case when measured with a steel rule. The PCD of the water pump gear should then be about 122*2-195 = 49mm (twice the centre distance - PCD of the cam gear). Then to work out the number of teeth the PCD is divided by the module 49/3.25 = 15.077 teeth; as I can't easily have a gear with that number of teeth I guess my measurement is slightly out and it should really be 15 teeth giving a PCD of 48.75 (actual centre distance should be closer to 121.875mm). The overall diameter of the gear would then be (teeth+2)*module or 17*3.25 = 55.25 so it would fit through the hole in the casting. Of course as a 15 tooth gear the pump will be rotating at twice the crankshaft RPM.
-
Thanks, I did try this once but missed out preheating the existing casting and the special powder It is 20 years since I gave up French at school but I think it says this 1. Clean, and file back 2. Make mould 3. Heat existing casting with torch 4. Heat aluminium wire and use it to apply special powder to casting 5. Melt the edges and sufficient filler metal to fill the mould 6. Cool slowly 7. Free the mould from the legs It certainly looks like it would be a useful technique; I wonder what the special powder was. I had to work in Germany for most of this week so I have not made any progress this project.
-
In order to make the bore round again where is had been deformed during TIG welding the stuffing box was clamped to the table of the milling machine and a centre indicator used to make sure the spindle was correctly aligned with the bore. Then a boring head used to machine the bore until it was once again circular. A coat of paint was applied to tidy up the appearance and offer some corrosion protection. And now it is ready for fitting. It would probably have been as easy to make another one but it is nice to rescue as many original parts as possible.
-
The flange was also secured with four countersunk screws. Threadlock adhesive was applied to make sure they do not work loose. Marine metal was applied to hopefully prevent oil leaking from the crack and to generally tidy up the appearance.
-
The next step was to machine 1/4" off the back of the stuffing box to remove what was left of the original mounting flange. This left enough of the existing casting that the new flange will not be taking any of the force compressing the gland stuffing. The bit of aluminium in the left hand hole is where we melted it with the TIG welder. Then I machined a slot in the new flange that was laser cut previously. I cut three bungs of acetal to align the two parts where the selector rods fit Before gluing the two parts together.
-
For a while I have been thinking a modern AC/DC TIG set would be the magic wand needed for the repair of aluminium parts. I booked a demonstration of a reputable make of 200A capacity; it was a joy to use on nice clean aluminium and I could imagine fabricating all kinds of parts with one. I took with me the stuffing box for the gearbox selector rods; previously I had warmed it up with a propane torch until the oil stopped sweating out of it and given it a fairly thorough cleaning. Using a 2.4mm tungsten all we could get was smoke (both white and black) and fireworks. We eventually tried a 1/8" tungsten, gas lens and the balance to maximise cleaning but only managed to melt some of the aluminium and managed to blow the gas shroud apart. So I came away without a TIG welder. When I got home I decided to go down a different route with the repair. Starting by opening up the crack. Then using an aluminium stick welding rod to put a little bit of strength back into the casting. I did not dare try to weld the thinner parts. These rods have to be used "electrode positive" to give the maximum cleaning effect (destabilising the aluminium oxide). They are nothing like regular arc-welding to use; the flux is incredibly aggressive and leaves a really hard (almost glass like) slag over the weld. I also find I have to snip the flux off the end of the rod to be able to get it to strike. Finally as 2/3 of the arc energy is at the positive electrode it is consumed really quickly. It is not elegant but it does impart some strength. You have to scrub all the slag off or it will corrode the aluminium away when it gets damp.
-
The next part to clean up was the clutch release bearing; this has been put in place to keep it safe. There was a thick layer of green paint on the oil tank. Before stripping the paint I emptied some nice clean oil from the tank but there was also a thick layer of sediment so I put some paraffin in along with three ball bearings and gave it a gentle shake to remove the worst of it. The fixing straps seem to line up quite nicely with the original holes in the chassis. The bottom has fallen out of the filter (shown on the chassis rail) so this requires soldering back into place. It looks like unsoldering the end plate will be required to remove the dents from the top of the tank. The fan mounting bracket has also been blasted and primed. The inlet manifold looks much better without the green paint. My assumption is that the small pipe was used with a shutter to allow air into the manifold.
-
The shaper has been used to tidy up the ends of the universal joint hub casting. I need to carefully mark it out to define exactly where the holes need to be. This piece of angle fits to the back of the cab and follows the roof radius. It was made by cutting slots and welding them back together. It has had a coat of primer and will now be stored until needed.
-
This week has mainly been taken up by preparation and painting. The front wings have had another coat. Although not originally fitted I have cleaned up and painted a pair of mirrors. These clevises and levers will be used to connect up the ignition timing and throttle. None of them came with this vehicle but most are Dennis parts and it will certainly need a few more parts to make it all work properly.
-
For the second attempt I reduced the diameter by nearly 1/4" so there was not so much excess material to be left as frills and that was much more satisfactory. After pressing I soldered a 3/16BSW screw in the centre. I rubbed the cap on a file to level off the rim and then cleaned up any imperfections with some emery cloth. Before giving it a quick polish. There has been a bit of blasting, priming and flatting back as well but those photos are a bit dull!
-
The gearbox breather was missing the brass hemispherical umbrella when I received it. I thought the easy way to make this would be to press some brass sheet through a hole with a ball bearing. My disc was of diameter=pi*ball diameter/2 My first attempt ended up a bit too frilly.