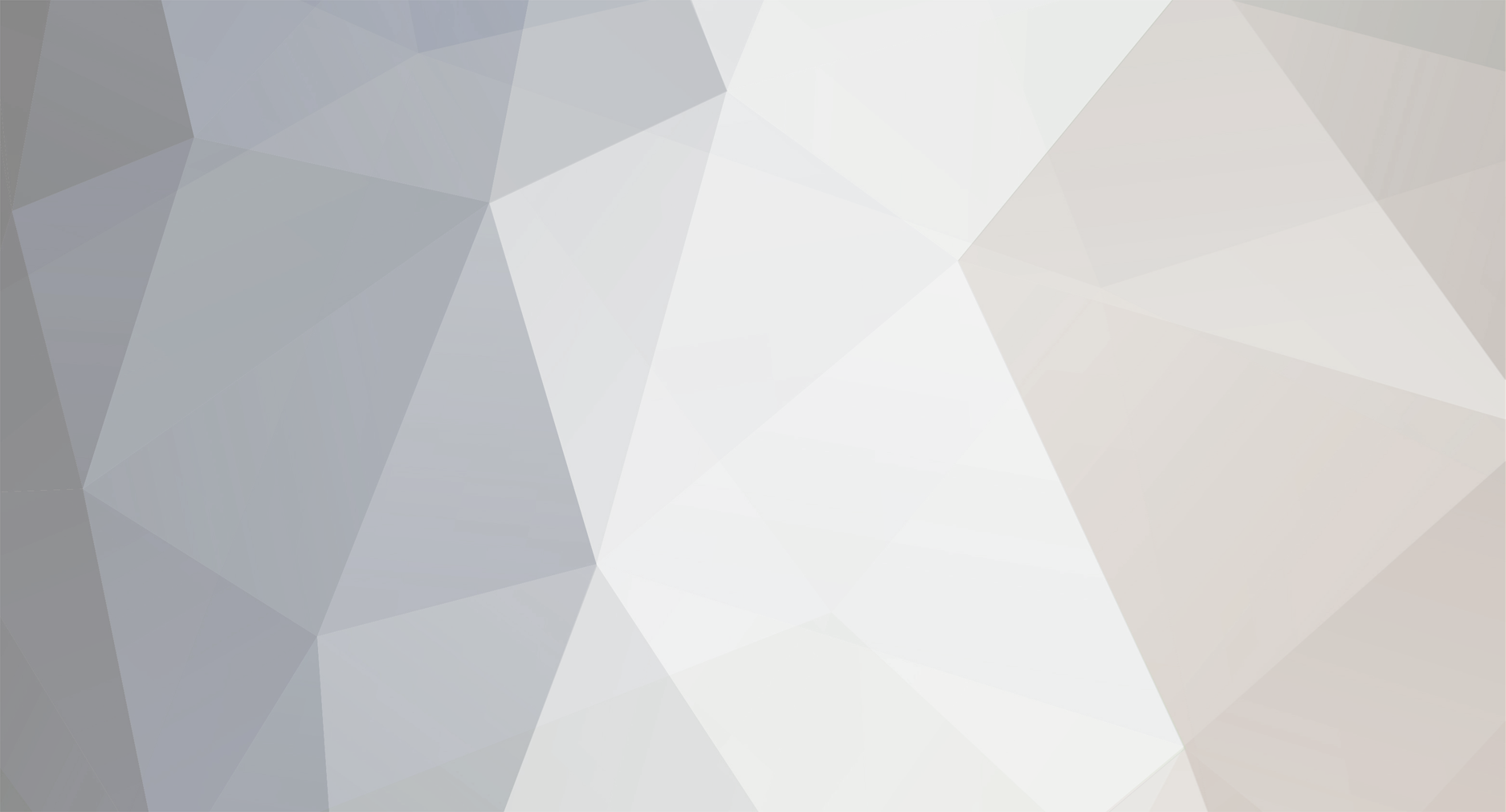
BenHawkins
Members-
Posts
861 -
Joined
-
Last visited
-
Days Won
3
Content Type
Profiles
Forums
Gallery
Blogs
Events
Articles
Store
Downloads
Everything posted by BenHawkins
-
I have drilled the bulkhead for the cab supports and filed them into the tear drop shape used by Dennis with modified coach bolts. Then modified some 3/8" BSW coach bolts to fit.
-
Thanks Richard, I agreed with them to bond it as I can add the rivets myself but having provided a drawing for the lining I was surprised they made it differently. However, if I didn't post it here no body would ever know once it is fitted. Ben
-
I tried fitting the flywheel but it will not go all the way back onto the flange. I marked these holes on the drawing as 7/16" for the 7/16BSW bolts so will ream them out by a few thou to resolve the issue. Trying the clutch in place. Then trying the front propshaft in place. This came off the engine from the Gosling pumping set so unsurprisingly is not the correct length to reach. I need to remove the joints from the splined shaft and make a new (longer) shaft
-
The friction lining company managed a 72 hour turnaround on the clutch. They would not rivet it, and have just bonded the lining on so I guess I will add rivets at some point. They also ignored my drawing and put an angled joint more common on modern equipment. They bonded lining material onto the clutch stops as well.
-
Between all the other jobs I have been painting the boards for the back of the cab; the first two were ready to fit but the cab frame had to be jacked up to be able to screw them in place. Unfortunately we did not have enough hands to get a photo of it up in the air as the glamorous assistant was acting as ballast to steady the cab. The boards are secured by screws through a strip of steel and into the uprights of the frame. And a trial fitting of all the parts.
-
I used a plane to chamfer the top of the board to follow the roof curvature. I planed a similar chamfer on the front arch. After scribing the thickness of the tongue and groove roof boards on the front panel and lining up the front arch I realised the corners would protrude slightly so these were then planed back.
-
The front of the cab roof is supported on two steel props that bolt to the bulkhead. I have welded the bracket to the bottom end of these so I could check the alignment with the ash frame. So I could then cut the side boards to length and mark the arc of the roof. Then used a jigsaw to cut the arc and sand paper to tidy it up.
-
I went to see the machine shop and the flywheel is finally finished. I still need to make the phosphor bronze centre bush. I gave it a quick coat of paint and checked the sizing for a 1/4" thick Ferrodo lining by using three 1/4" drill bits. The clutch sits just proud which I believe is correct. I now need to book it in for lining and will probably have both parts balanced before fitting.
-
I then used a router to copy the profile more accurately And did the same for the roof support. The two parts side by side. The final job for this week was to thin the lugs down on the control levers (fitted to the steering column) and drill them for to fit the clevises.
-
I used my laser cut template to scribe the outline onto a mahogany board. Then used a jigsaw to roughly cut the shape. Then clamped the template to the timber profile.
-
Thanks for the comments about chuck accuracy. In this case I don't think it matters as the dial indicator is still rotating around the spindle axis even if they do not share an axis. The same goes of the boring head; the tool tip should still be transcribing a circle even if the boring arbour and the spindle are not coaxial. I decided taking multiple nibbles at the bore would be a bit tedious so bought a second hand 1-5/16" drill bit from an online auction site before I went to India for a week. It had arrived on my return so I was able to open the hole out a bit to start with. For the first couple of cuts I had to retract the tool a few times to clear the swarf but the final cut could be taken as a continuous pass as there was a bit more space for the swarf to go. I ground another piece of high speed steel to chamfer the hole. And tried the universal joint I had made previously Still the other end to do.
-
I previously machined an M14 thread on the end of a piece of 30mm diameter steel bar so I could screw a small boring head on the end. The first attempt at a small cut was successful until the slide way adjusting screw that protrude from the outside diameter of the boring head crashed into the propshaft tube. Which means the first cut has to be deeper than I would ideally like to clear these screws. I can see the swarf getting in the way as I make the hole over 5 inches deep but we will have to see how it goes.
-
I have mentioned before that my lathe is a bit too short to bore out the propshaft tube in the conventional fashion. I think I might have a way around this and have machined a bar end of steel to fit the tool holder and tapped it for some clamping bolts. This allows me to mount the propshaft tube from the tool post and support the other end of the tube in a fixed steady. Using a centre indicator to make the tube coaxial with the lathe spindle (using the tool height adjustment and cross slide adjustment to centre the tube)
-
Everything was then clamped back together and the diagonal dimensions measured to make sure it was all square before drilling and fitting screws. The side planks still need to be finished off when the supports from the bulkhead are put in place and the roof line marked out.
-
Thanks for the comments. I have limited carpentry tools so try to get away with what I have. Might put the shoulder plane on my Christmas list as I think there will be applications for it in the next lorry body build. I have continued to cut the joints in the same way and much of the ash frame has been painted. I put the top planks back in place so I could mark the arc of the roof. This allowed me to scribe a line along the side planks. And plane back to that line to give an approximation of the roof radius.
-
The other arch for the roof was cut from the offcut. Both arches were tidied up with a plane and sanding block The half-lap joints were cut in the same way and it was all tried in place for correct fit and so that the cut-outs could be scribed onto the uprights. It was then all dismantled again so the other half of the joints could be cut in the uprights and some of the parts could start getting their coats of paint. That should keep me busy for the next week!
-
Trying the sides in place. The arched piece for the back of the cab was marked out with a template I had laser cut. And cut out with a jigsaw.
-
I scribed lines on for the cut outs in the upper boards that finish the sides of the ash frame. After cutting to depth in a few places with a saw I removed most of the material with the chisel. And did further tidying with a chisel and sand paper.
-
-
For the last pieces of timber to finish the seat box I decided these would go in from the top so that it should be possible to remove the petrol tank without completely dismantling the cab. After scribing the lines I cut as deep as I could with a saw. And chiselled out the material to those lines.
-
I put some offcuts from the ash bearers on the bed through a planer then trimmed them to fit between the cab bearers. At this point I realised I did not really have any appropriate screws for holding the ash framing together (poor planning on my part!) This has given a chance to move some of the timber to the undercoat stage.
-
I repeated the procedure of cutting half-lap joints for the ash frame at the front of the seat and checked the fuel tank would still fit with the help of the glamorous assistant At this point I decided it would be a good chance to check the fuel tank did not leak and filled it with water for a couple of hours with no drips. All the joints cut in the ash frame were given a coat of primer.
-
The large water jacket over the top of the cylinder and the manifolds exiting at 45 degrees are unusual for a T heat engine. Looking through various early literature I found this from early 1904: They appear to have made them with a variety of bore sizes and number of cylinders, including 85mm which would be a good fit for the cylinder block I brought back from Beaulieu. One a few hundred more parts required for this veteran car project. I have scraped the green paint off the metal parts of the centre from the distributor on the W&P engine. Checking with a multi-meter the top (steel) commutator is connected to the spindle and the lower (brass) commutator is insulated from the spindle. The brass commutator only has one vertical segment and has some wear evident from a brush of some description. This appears to be designed to work with a single trembler coil, the top commutator switching the low voltage circuit and the lower commutator directing the high voltage to the correct spark plug. The insulators seem to be made from vulcanised fibre. The picture below appears to be the standard White and Poppe manufactured contact breaker and would have been used with four trembler coils. But Dennis appear to have fitted this distributor, which appears to have terminals to match the centre above. I don't know if it was their own design or bought from another manufacturer.
-
Thanks for the information, this is a similar chassis to my 1914 lorry.It is nice that somebody considers me a Dennis expert! It is a couple of years since I went to see this chassis; I did quite a reasonable amount of work to try to identify it. Although I was unable to read the chassis number when inspecting, the back axle did have the manufacturing date (June 1913).The measurements tie in exactly with the charabanc drawings and catalogue, but unusually it carries brackets for rear mudguards and had a foot step fitted at some point. The engine mounts are for the White and Poppe engine with separate cylinder blocks like in my 1908 Dennis.The Dennis order book for June 1913 shows a few charabancs but only one supplied without a body (Dennis bodies generally covered the wheels so no rear mudguards were supplied). This bare chassis was supplied to Chapman (of Eastbourne), who operated in the area where the chassis was found. I even have a photo of one of these chassis (they bought two) in front of the Chapman offices and it shows that the body was transferred from another vehicle as it is not quite a perfect fit. It is too expensive for me and from experience I think it could take several decades to find and make the parts to do it justice.
-
After chiselling out the excess timber. And again checking things go together properly. I have started flatting back the double boards and applying undercoat. The first board is hidden by the seat box so will not be seen.