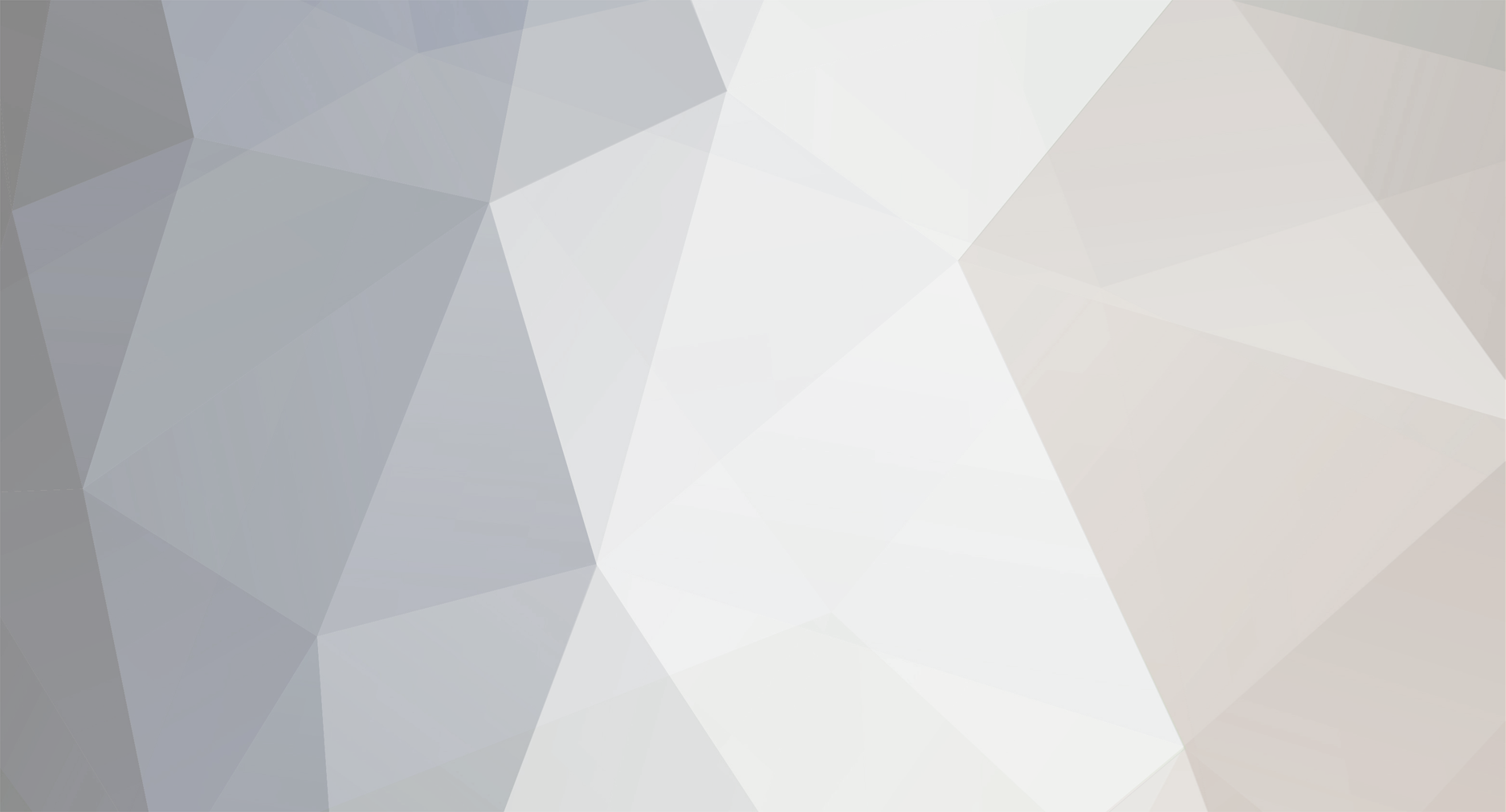
Andrew Rowe
Members-
Posts
309 -
Joined
-
Last visited
Content Type
Profiles
Forums
Gallery
Blogs
Events
Articles
Store
Downloads
Everything posted by Andrew Rowe
-
restoration of a valentine MK5 tank started
Andrew Rowe replied to monty2's topic in Tracked vehicles
Yes, it was an interesting Earthquake! Officially it was upgraded to a 7.9 and I think they have said there has been at least 1500 aftershocks since it happened, some ranging to 6.5. Things have settled down now. To put it in perspective they say that it was up to 50 times stronger than the Christchurch (NZ ) earthquake we had a couple of years ago that killed about 250 people, where as this one took two lives because it happened in a less populated area. Some costal land was raised out of the seabed by 1 to 2 mitres. The Tank factory still forges ahead! Today we have the steel work for the radiator header tank , which sits above the fan should. This piece is now installed and you can see the radiator header tank tucked up inside this housing, very snug fit, sits on little 1/2" thick felt pads. Also in behind the oil cooler you can see a 1/4"water tube from the main bottom water pipe up to the header tank .The third pic shows an extra steel plate that covers over across the width of the header tank. The rear transmission doors will partly close down on top of this when shut. The last couple of pics show the engine air box drain "catch can" and the position where this is located. This needs to be installed before the rads go in, as there is getting less and less working room in the backend. The air box on the engine, which is the cavity between the cylinder liners and the engine block wall has 2 x 3/8" pipes draining excess oil residue down these lines to the "catch can ". There is a check valve in each line that opens when idling and closes when pressures get above 1.5psi , as revs increase, other wise there would be a continuous drain of oily residue when engine is running all the time. I installed a handy tap which you can empty any fluid to the outside of the hull will little trouble. Cheers from The Tank Factory. -
restoration of a valentine MK5 tank started
Andrew Rowe replied to monty2's topic in Tracked vehicles
With the motor finally seated into position, the plumbing up and electrical connections can be connected now. The first couple of pics show the fan shrouds along with their protective guards ready for reinstallation and now installed. Then the next sequence is the fitting up of the fan blades. There is offside and nearside, nearside being the L/H side of the Tank. The blades counter rotate and suck the air from the turret area across the engine and out through the two radiators. Next, the oil cooler is installed, which is a solid neat fit across the width of the Tank. The final pipe work for the oil cooler and radiator bottom tank outlet is also installed now as well. There is also a 1/2" cooper tube that is fitted underneath the bevel box that goes to the gearbox as an oil level balance tube, it is important that when taking the engine out at anytime , that you remember to remove this pipe as it goes through the cross member that the steering clutches sit on and you will rip it in half , if you forget about it! Cheers from The Tank Factory. -
restoration of a valentine MK5 tank started
Andrew Rowe replied to monty2's topic in Tracked vehicles
The engine is lowered in ( approx. 10 degree angle ) for the final time after several trial fits for clearances and pipework issues that have been sorted. The second pic shows the "quick coupling " connection with 8 x 1/2" BSF bolts to each of the steering clutches. The last pic shows the clearance for the generator to the fuel tank , that I had eluded to earlier. Either it was good luck or well designed piece of British engineering! Cheers from The Tank Factory. -
restoration of a valentine MK5 tank started
Andrew Rowe replied to monty2's topic in Tracked vehicles
A few little fittings for the engine bay; we have the control rod cover for the lower R/H side. This pretty much has to go in before R/H gearbox mount is fitted. Then we have the 3 x upper fuel tank straps for securing the tank to the wall. Next is the fuel tank fitted into the L/H side of the engine bay, a really snug fit, as you will see later on , the tolerances are only about 1/2" to spare. The last two pics show the Engine bay ready to take the engine for the final time. Cheers from The Tank Factory. -
restoration of a valentine MK5 tank started
Andrew Rowe replied to monty2's topic in Tracked vehicles
We must be the only two in the world that have started and run a Covenanter Tank engine , more unique than the common Tiger Tank ! Cheers Andrew. -
restoration of a valentine MK5 tank started
Andrew Rowe replied to monty2's topic in Tracked vehicles
I will start it before I turn 50 Adrian ! Cheers Andrew. -
restoration of a valentine MK5 tank started
Andrew Rowe replied to monty2's topic in Tracked vehicles
Ahh, yes the Covenanter, the "sports car" model of Tank. I am lining up a slot in the Tank Factory in the near future to start the restoration of said vehicle. Just picked up some brand new starter motors and generators for her the other day, Simms type, which are more uncommon than the usual CAV electricals. Back to the Valentine ; shown is the fan ducting to the radiators. I have had to fabricate these, as this sheet metal work usually gets the chop when the engines get pulled out from when the Tanks were disposed of. I have also had to fabricate the L/H gearbox mount as this was missing also. Cheers from The Tank Factory. -
Once you guys have dug it up , this is the proper motor that powers it; a Meadows Flat 12 of 300Hp petrol, and also a Meadows / Wilson gearbox, sounds like a Spitfire engine when you run it up with no mufflers ! Cheers Andrew.
-
I run a Scorpion , and have fitted a fuel pressure regulator in line as a precaution to over fuelling in the carb, which I had experienced years ago on another Scorp. This one has a gauge and reads about 3psi when the fuel pump comes up to maximum pressure and that seems to be all it produces , so the fuel pump must have a built in pressure regulator? So if this self regulating pump fails it forces fuel past the needle valve and floods the engine, which as I said I have experienced. Also, I have noticed that the fuel pump will tick away quite fast if sucking air, I had to undo the fuel filter bowl and turn half a turn , retighten and it came back up to pressure ( 3psi ) and slowed down it's beating as it had reached it maximum, just my experience, Cheers Andrew.
-
restoration of a valentine MK5 tank started
Andrew Rowe replied to monty2's topic in Tracked vehicles
The radiators have been pulled from storage, so we can check condition , etc. The radiators on the Valentine consist of two mounted at the back over the gearbox area, on a slope of something like a 45 degree angle. They lay flat on this angle but can swivel where they are connected to at the top and bottom header tanks, so you can get limited access to the gearbox .We have stripped all the top and bottom tanks and these are getting all new laser cut gaskets, with all threads cleaned out and new bolts. We have some boxes of new graphite packings, which is really good, so all the new joints where the radiators swivel will get these . The radiators themselves appear pretty good so have opted to not disturbed the top and bottom tanks as the seals look very good on these.Cheers from The Tank Factory. -
restoration of a valentine MK5 tank started
Andrew Rowe replied to monty2's topic in Tracked vehicles
Work continues on laying all the wires through the conduits. At first we thought we could prefab some of the looms before install, but this was not to be the case, as in order to fit them in the Tank, sections have to be unscrewed and moved into position and then done up again. Sometimes it can be a painful process of putting conduit in and then doing everything up , only to find that you have to take them back out because there needs to be a few alterations , as the tubes interfere with more parts that get installed later on, so it is all about knowing the next parts and processes and what effects each other. Sounds confusing?:nut: We are using standard automotive wire of different gauges inside the conduits as very little is actually seen. All ends are soldered and heat shrink sleeves used to insulate the joints. Also the main battery cable feeder conduits we have done outside of the Tank before installation. The last pic shows the rear bulkhead terminal block wires to engine generator (24V ) and cold starting wiring loom.Cheers from The Tank Factory. -
restoration of a valentine MK5 tank started
Andrew Rowe replied to monty2's topic in Tracked vehicles
These Valentines were in used right up until 1960! and the odd part were still in Govt. stores in the late 70's early 80's. I have heard stories of things like steering clutches being specially ordered from the original manufactures in the 1950's to keep our ones going when the NZ Army decided to form Armoured Brigades for CMT ( Compulsory Military Training )Cheers Andrew. -
restoration of a valentine MK5 tank started
Andrew Rowe replied to monty2's topic in Tracked vehicles
Shown are a few more pictures of the remote gear change shaft , that runs the length of the Tank. There are 4 round steel housings that are held in bronze castings along it's length. Inside these steel cylinders are 2 x sets of bronze rings that hold 22 x 5/16th steel balls each ,that form a cage that the 1&1/4" shaft slides and rotates on to transmit the movements required for changing the gearbox to the selected gear. The last 2 pictures we are test fitting the engine. This requires about a 20 degree angle , the front being lower when it is lowered in and moved forward to rest on the front engine mount. Both steering levers have to be fully back to allow enough space for the steering clutches to be moved back against the heli-hub units to allow a gap of about 5mm each side for the bevel box to be lowered in as the engine is moving forward. It just clears the rear conduit by about 10mm as this happens. The bevel box mounts need to be in position on the bevel box as it is lowered, as once it passes down pass the clutch units you cannot get them in! We have found that we are 3mm too high on these mounts, so I will mill that off the bottom to bring the output flanges in line with the clutch units. Just happened to measure the centre of the fan hub from the inside wall of the Tank, and each side measures in exactly the same,@ 309mm! Cheers from The Tank Factory. -
restoration of a valentine MK5 tank started
Andrew Rowe replied to monty2's topic in Tracked vehicles
Showing today are the oil pipe lines and the oil tank. The engine runs a "dry sump " , so has this tank for it's fluid. The oil on a Mk5 also runs through a 5-row oil cooler that will run across the width of the Tank above the gear box. This part will go in after engine and fan bulkhead. The 3rd pic shows the engine water drain , that comes across the front of the engine, through the middle bulkhead and through a hole in the floor to drain. Along side and above it we have the commanders engine shutdown lever and knob. This is connected also to the drivers shut down lever, through clevis's that have long slots in them, so either can shut down without effecting each other. The last series of pictures we can see all steering controls together and their associated rods through to the rear engine compartment, and the "business" end. Cheers from The Tank Factory. -
Just a quick question, Is the hub seal, inner , (next to the brake disc ) anything special for the final drive. The seal is 100 x 80 x 10mm , ie is it high temp etc ? Cheers Andrew.
-
restoration of a valentine MK5 tank started
Andrew Rowe replied to monty2's topic in Tracked vehicles
Here we show the driver's steering lever main supports. The next pic shows the installation of these controls going into the front drivers compartment. The last pic we are trail fitting the fuel tank and conduit to make sure nothing interferes with each other, which is critical, because when the engine goes in, it is a perfect fit and nothing wants to be out of place, so do it once , do it right , not sure where the vacuum cleaner bolts to though? Cheers from The Tank Factory. -
restoration of a valentine MK5 tank started
Andrew Rowe replied to monty2's topic in Tracked vehicles
For the Drivers controls we have the acc. pedal / clutch and brake pedals. The last couple of pics show the rear brake connections for the steering clutches and brake control rods, and then the last pic shows the aux. foot brake flexi-able cables that run from the middle bulkhead forward to the drivers controls. So , there are basically 3 lots of rods either side of the driver that run to the back of the Tank for controlling movement. There are also 3 more combinations of rods for ; main engine clutch / acc. and engine stop also. Emergency engine shut down is located at middle bulkhead, left hand side. Cheers from The Tank Factory. -
restoration of a valentine MK5 tank started
Andrew Rowe replied to monty2's topic in Tracked vehicles
A few more parts to the puzzle, we have the electrical diagram/ with Aux. fuel tank release lever. Next is the rear battery tray, that will be installed but not used for batteries, as we will run 2 x 12volts up front. Originally they used 4 x 6 volt batteries wired up to give 12 and 24volt. The last couple of pics show the machete brackets that go under the sloping drivers plate for stowage and also the front diver's floor drain valve. Cheers from The Tank Factory. -
restoration of a valentine MK5 tank started
Andrew Rowe replied to monty2's topic in Tracked vehicles
Hi "Top roller" , we have learnt what we know through pulling down and rebuilding several of these spicer boxes. The parts manual also indicates what parts are required and quantities needed, have not got any rebuild manual as such , just plenty of experience, Cheers Andrew. -
restoration of a valentine MK5 tank started
Andrew Rowe replied to monty2's topic in Tracked vehicles
Running along side the Tank rebuild, the electrical/ signals department has reported back with updated progress on the restoration of the 19 set that will fit inside the Turret. Just to give you a "Brief " background to the type of radio we are using. The WS No. 19 was developed from a British military specification issued in 1937. This called for a radio with a short- wave transmitter and receiver ( for regimental and squadron communications ) , plus a VHF transmitter and receiver for short-range inter Tank communications. In addition it was required to have an intercom for the crew communication within the Tank. The British PYE company was awarded a contract and began production of the No.19 set early in 1941. An improved MK2 version was produced from March the same year and during WW2 No.19 sets were manufactured in Australia, Canada and the United States. So , this set being 70 years old needed an overhaul to make it operational again. The radio consists of two modules, a power supply unit and a radio transceiver/ intercom module. Power Supply: This unit contains a 12-volt dynamotor ( also known as a "rotary transformer" ), which produces high- tension D.C. voltages of 275v and 500v , to operate the radio and intercom. It also houses fuses and filter capacitors. The commutators and brushes of the dynamotor required cleaning and the rotor bearings needed to be repacked with grease. All the old capacitors no longer met specs and were replaced with more efficient and reliable modern capacitors. In particular the high -tension electrolytic capacitors were replaced with modern non-electrolytic motor-start capacitors..............you still with me! These use a polypropylene dielectric , which provides almost infinite insulation resistance and much improved efficiency and reliability. During WW2 , the failure of electrolytic capacitors in 19 set power supplies was a major problem and there are reports that on one occasion a large consignment of higher quality replacement capacitors were flown from the USA to North Africa to repair all Tank radios in the western Desert. Transceiver Module: In overhauling the 19 set transceiver module, all capacitors also needed replacing -a total of 25 capacitors. Some of these were low voltage types where modern mylar-dielectric capacitors could be used as replacements. Higher voltage types were replaced with polyester , polystyrene , or ceramic capacitors. Unlike 70 years ago there are many capacitor options available today and so capacitor types most appropriate to the particular circuit function can be selected.........and you thought we were dummies! Other components that needed replacing, were resistors. The original resistors were carbon - composition types. These were made of carbon powder mixed with an electrically inert material such as talcum powder , and sealed with resin. Even when new , these resistors had a resistance tolerance of + or - 20%. After 70+ years their accuracy is now sometimes greater than 100% off. Composition resistors are no longer available , so new carbon- film or metal film resistors were used as replacements. These have an accuracy of 5% and 1 % respectively. A total of 35 resistors were replaced in the radio. Wiring: much of the internal wiring of the radio had used natural rubber insulation, which had deteriorated over time. Wire with cracked and crumbling insulation was replaced with modern Teflon - coated wire. other wiring in the radio was treated with an epoxy sealer. After restoration, the radio's functions were tested and the receiver was realigned. The parameters tested were transmitter output power, receiver audio output, and sensitivity and signal / noise ratio. The intercom gain was measured and the power supplies voltages and ripple waveform checked. Now after a total overhaul of the No.19 MKII Wireless set, we have a communication system better than it was in WWII. Testament to this is the fact it now puts out 10 watts of RF power on CW instead of the 7 watts it put out when it was new! So, I think it should still be going in another 70 years:-) Attached are pics of the set and the original components taken out and new replacement components and the testing of the set. We still have to add front protective grills and the mounting for inside the Turret Busslle. Cheers from the Tank Factory. -
restoration of a valentine MK5 tank started
Andrew Rowe replied to monty2's topic in Tracked vehicles
Looking at the gearbox shifter gate the other day, something did not look right , so it looked like we had rebuilt a MK3 one, which is still 5 speed plus reverse, but with a slightly different layout, a trap for young players! The first two pictures show what I am talking about. MK3 uses a Meadows type 22 "crash "gearbox and the MK5 uses the American Spicer synchromesh box. The next 3 pics show the steering controls being assembled with their new bearings, etc. There will be 1/2" BS chain that will wrap around the "pulleys" at the end of the actuating shafts. These will transmit drive backwards and forwards to the rear of the Tank when the steering levers are being used, it will become clearer as the whole assemble comes together. The last pic show the steering rod support pads that go underneath the fuel tank and battery tray either side of the Tank in the rear engine compartment. These had to be made new, as are always rotted away. Cheers from The Tank Factory. -
restoration of a valentine MK5 tank started
Andrew Rowe replied to monty2's topic in Tracked vehicles
Next in line is the gear change shifter. This consists of 4 major sections. The front unit is the gear shifter housing that contains the gate for the gears, 5 forward and one reverse. Then there is a long shaft ( 1 &1/4 " dia. )that runs to the middle bulkhead through some bearing housing supports, then another universal joint, there being 3 of these in total along the shifting tube. Down the back, at the business end there are a couple of supports for the gate that connects to the Spicer gearbox. There are provisions for adjusting the gate to the gearbox for alignment and to make the gearbox gears mesh and perform correctly. Cheers from The Tank Factory. -
restoration of a valentine MK5 tank started
Andrew Rowe replied to monty2's topic in Tracked vehicles
We are still sorting control rods and brackets at the moment , although most have now all been blasted and painted. The first four pictures show the steering clutch and brake control rods now properly sorted, and ready for install. The next couple of pictures show the air cleaners we have been working on. These are original housings, oil bath type , but we are going to run dry type air cleaners for better efficiency and performance for the engine. The modification is done in such a way that they can be easily converted back to the original elements, if that needed to be done. The last 3 pictures show the fuel cap setup that I have been playing with. I had to get some new fuel caps cast up in bronze and I have machined the rough cast back and cut the new thread ( 16tpi ). The fuel caps are always missing when I have found old fuel tanks, so I have managed to borrow an original for the casting of my new ones. Cheers from The Tank Factory. -
restoration of a valentine MK5 tank started
Andrew Rowe replied to monty2's topic in Tracked vehicles
Sorting through more original control rods and end clevises. Mainly 3/8" BSF with some L/H and R/H turnbuckles for making the adjustments.Luckily I have a set of 1/4" up 1/2 " BSF Left hand taps and dies, which does make life easier. I think I added up the other day nearly 42m of rod of this type in the floor . Cheers from The Tank Factory. Happy birthday Adrian B , 50 !:-).