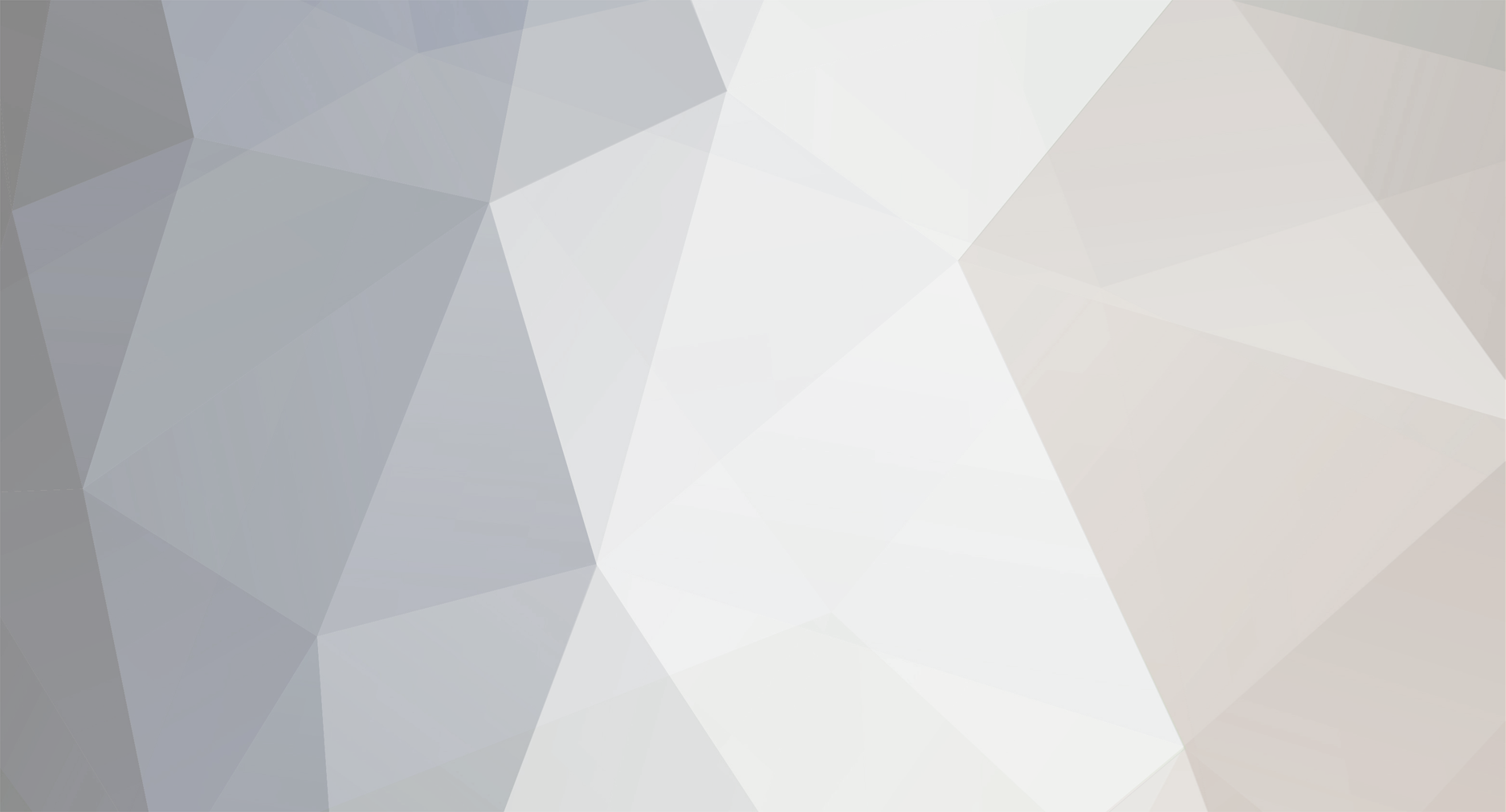
Aussie
Members-
Posts
172 -
Joined
-
Last visited
-
Days Won
1
Content Type
Profiles
Forums
Gallery
Blogs
Events
Articles
Store
Downloads
Everything posted by Aussie
-
Thanks Richard. Some pics that might help others (and apologies to everyone else!) Drained it - I guess ATF since it's red and actually lots of it. Perhaps the seal wasn't as bad as it looked. As per Richard's advice, undo the bolts then screw 3 into the extractor holes and gently screw them in to extract the bearing carrier with seal, seal plate and circlip. The seal is held in place by the circlip with the seal plate in between, however it isn't possible to get the seal out by just removing the circlip because the seal is firmly pressed in. The bearing carrier snugs up against the bearing and the seal can be seen in the centre: Getting the circlip out was a challenge - very heavy duty and my pliers are probably a bit light-weight. Decided to wear safety glasses and glad I did because when the circlip came free it flew 5 metres across the shed! So much for OHS! This shows the bearing housing, circlip, seal housing and "outside" of the seal. This shows the lip on the inside of the seal plate that fits into the groove on the seal. When it is fitted together it supports the lip of the seal, possibly to prevent it pushing out and failing under pressure. Others have suggested flipping the plate to fit non-standard seals that don't have the groove. If this is done the lip won't have the same support, so at this stage I'm not sure if it's a good idea. Will have a look at the SKF seal when it arrives next week and decide what to do. I'll have a few questions later. Mainly, the bearing housing bolts were covered in some sort of gunk and I'm not sure if that's just thread locker or some sort of sealant. Cheers James
-
I'd love to see a more complete list if there is one. The list is obviously missing a few things but I'm particularly interested in Centurion tank 01ZR10. James
-
Have the radiator, fuel pipes/tank and generator oil leak under control but on opening one of the FFW filler plugs there was no oil to be seen (supposed to reach bottom of filler plug hole with the hole at top dead centre). So now replacing the oil seal but don't have instructions and not entirely sure how to do it. I know it's been discussed before but still not entirely clear to me, so please humour me and I'll post pics and my research as penance and to hopefully help someone else. The fluid is ISO 10 or 15 (warmer climate) hydraulic fluid. Automatic transmission fluid is apparently also OK so long as it's ISO 10 (someone suggested it is ISO 30 but I think that's wrong). Need 5.54 litres, so it figures that it comes in either 5 or 20 litres! The seal needs to be a high temperature (or pressure? can't recall which) seal. ID 44.45mm, 1.75 inches; OD 63.652mm, 2.5 inches, Thickness 3/8inch, 9.5mm. Bought a seal from a local shop but am advised not to use it, as it is black and therefore not high-temperature enough. John Deere AT52447 is suggested as a replacement. The other option (that I'm going with) is SKF Bearings Viton seal 17395; that was suggested to a friend by Tim Vibert, who has more experience than most. The seal is apparently fitted to a plate with a lip that pushes into a groove on the back of the seal, so neither of these seals fit as is. Some suggest flipping the plate so the groove is on the outside but my friend warned that the seal might "turn itself inside out" with enough pressure. Not so sure about that but will machine a plate to fit just to be on the safe side. A "genuine" seal is also an option of course but apparently they're a bit hard to source. Anyway... 1. First job is to separate the gearbox, supporting it (engine lifter and straps) while withdrawing it. So far so good! 2. The seal is obviously knackered so I'm glad I decided to do it before putting the engine back in. (The bolt in the filler plug was to guard against dropping the plug into the housing. Tied a bit of wire to the end but think there's a "proper" wrench available for the job. Came with a resident spider that obviously doesn't (didn't) like my chances of getting it mobile again! So where to from here? Do I undo the nuts or remove the circlip (or both)? Not sure what the circlip is doing, and the drawing I have shows a bearing housing so don't really want to turn this into a disaster! Thanks for any advice James
-
Sorry Paul Those are photos of plates but not sure what manual they're from, and the info relating to numbers wasn't included - so limited benefit! Perhaps someone else will be able to help. The only other bit I found was a circuit diagram which might be useful. Sorry I can't be more helpful. James
-
Not so sure that this is what you're after but it might help a bit. The wires in the terminal banks have a stamped number which helps match them up.
-
One of mine was cut off so making a plate to weld on the top bit, which was fortunately left on the engine. Anyway, here's some pics and a tracing on a sheet of A4 paper which allows a good estimate of dimensions. Good luck! James
-
Thanks Richard et al. A quick update on my trial of ultrasonic cleaner - it does work but I'm not all that impressed with the result, even after running it for around 24 hours, so it's not the "holy grail"
-
Pulled the engine and transmission out with fork lift and chains. Main pain was removing the stuff in the fighting compartment to get at the bits needing uncoupling but really not too bad. Hull was pretty grotty, of course, but cleaned and painted and now looking nice again! Having the engine out it then became clear after a steam clean that the only oil leak was from the generator. First thought the lower oil pipe junction but oil was running down from higher, i.e. the central seal. Filled it with oil but couldn't make the bloody thing leak, however I'm pretty sure that is the culprit and expect it would leak if the engine was running and oil pumping through it, so replaced the seal. No signs of leaks anywhere else... Discovered the left steady plate had been cut off, leaving the upper bit with the bushes, so now cutting another bit to weld to that. Will take some pics tomorrow as another poster was after the dimensions Still have the problem of no mounting plates for the petrol tank, and think I'll put in an electric fuel pump while I'm at it, so still a bit to do. All good fun! James
-
I reckon this Ferret is trying to tell me something, or drive me mad! It's also distracting me from the Saladin. Recored the radiator to fix the water leak, and cleaned petrol tank and pipes to fix the fuel blockage - all good... But now noticed oil under the left rear wheel. This is an old problem that I thought was a bevel box seal, but on closer inspection the oil is coming out through the hull, not the wheel station, and just running along the floor. I can't see where the oil is coming from. Might be an oil tank connection so I plan to take that out and see if it's the culprit. However, knowing my luck it will be the sump, etc, in which case the engine will have to come out. Assuming that's the case, what's the best way to remove it? EMER's say take out engine and gearbox together but others have suggested unbolting the engine from the gearbox and just taking the engine out. If this is the case, I presume the gearbox should be disconnected leaving the fly wheel attached to the engine? There is a lifting bracket at the rear but can't see one at the front - perhaps the slots at the sides of the flywheel housing (picture above)? Any guidance will be appreciated! Thanks James
-
An idle thought (no pun intended) - Ferret #2 stopped after idling for a (long) while. while trying to jump start Ferret#1, which is trying very hard to do my head in. No spark from plugs but new ones were fine, so replaced and started on the button. Won't idle it for so long in future! The old plugs are should be serviceable but not sure of the best way to clean them - the side wire looks very fragile/flimsy. I wonder if an ultrasonic cleaner would work but there is a layer of insulation inside the hollow bit of the plug which the ultrasonics might vibrate off. I plan to experiment with one anyway - will just dip the dirty tip in, rather than the whole plug. Anyway, I'd be grateful for advice on how to do it properly. Do I just very carefully rub with wet and dry paper, or is there something I can dunk them in to clean them more thoroughly? Thanks James
-
Oh dear. Sent the fuel tank off for cleaning and they've broken 3 of the 4 mounting brackets. These consist of two metal plates separated by a rubber bush that is glued on, and those have become unstuck. Does anyone know if the rubber bush can somehow be glued back on, and if so, with what (or by whom)? I might be able to source some if all else fails, but not sure if they're the correct hands. Or any other suggestions for alternative way to mount the tank - I must say I'm not entirely sure that resilient rubber mountings are really necessary, given the small amount of driving done. Thought of putting a bolt through to hold the pieces together and maybe that would work? Thanks James
-
A mod of the mod! Couldn't find brass tube so bought a couple of joiners: Very light run with the lathe to trim the threads down enough for a tight fit, then hit them in with a hammer. Didn't solder or braze because they're so firmly in that I don't reckon they'll ever budge. Et voila! Edited: Not so smart after all! The hole in the tank steps in, so you need a straight tube to fit it in. Trimmed the fitting on the lathe. Think I'll put a thin bead of JB Weld but they're hammered in a tight so probably don't need it.
-
Thanks Vince Lots of useful info on that page, as well as the banjo bolt mod! Cheers James
-
Know what you mean about the stink! Took off a banjo bolt - completely blocked of course. Re the mod to increase the height of the petrol pickup, do I just jam a bit of metal pipe in the opening or should it be fixed somehow (solder, etc?). I'm thinking it might vibrate out if it isn't stuck securely. Interestingly (surprise surprise) the fuel gauge sender is stuck on "half full". Plan to soak it +/- dismantle to try to free it up, but is it more likely to be knackered?
-
A few queries along these lines, if I may. 1. I've taken the (ferret) tank out to clean it. Not sure if the pump is 100% so I plan to connect the input hose to a can of fuel, disconnect the hose to the carbie and run that into a can, then crank the engine. Is there a measure of ml/min or PSI to see if it's working, or just be happy if fuel squirts out? 2. I've purchased a hand priming pump (the rubber bulbs that you get at marine shops) to put between the LHS tank outlet and the filter, with another filter on the suction side. This needs to be low down in the fighting compartment (i.e. near the bottom of the tank) so will need to get a short length of metal pipe with the swelling on the end, to save chopping up the existing pipe, to connect flexible hose. Imagine pipe is readily available (but haven't checked yet). 3. The other option is an electric pump in the same position as (2) - I guess a 12V pump is suitable, rather than 24V? However on Googling the warning is to wire it so that it stops pumping if the engine stalls. The tachometer circuit is one suggestion and it certainly seems sensible to not keep pumping fuel if the engine stops for whatever reason, but this is getting a bit complicated for me. You'd hope that the carbie would stop fuel flooding everywhere but I'm not sure. 4. Plan to modify the banjo connection as suggested by "Grasshopper" to increase the hight of the fuel pickup a bit. Haven't looked at it yet but assume a bit of flexible fuel pipe would be OK for this? 5. Agree absolutely with the problem of air leakage. The fuel pump needs to pull fuel from the bottom of the tank to the filter near the top of the tank before it starts flowing down to the pump. Any air leakage makes this difficult or impossible. I've found one culprit connection, which was part of my problems and is why I'm planning option 2.
-
Worked it out. Just 2 bolts at each front corner. Fair bit of mucking about to get stuff out of the way but have it in the fighting compartment. Now waiting for some young muscles to help lift it out and then I'll give it the POR 15 treatment. Certainly looks (and smells) pretty evil at present, so I'm glad that I "bit the bullet"!
-
Lovely pictures! So I think I should try taking the tank out and doing the job properly. But... don't have EMERs that show how to do it, so any help is appreciated. I understand how it needs to come forward through the fighting compartment - no problem since it's a Mk1. I'm not sure how many fixing bolts I should be looking for. Can see one on both front corners but suspect there might be more?
-
Thanks for the advice. Seems a good idea to increase the hight of the pickups. Also sounds as if the tank could be removed without too much drama so I'll have another think about that too. Thanks again. James
-
Ferrets seem to be topical at the moment so thought I'd run this past you. One of the Ferrets became incontinent - leaking radiator so re-cored that. Now can't get fuel from the tank. Both fuel lines blocked and only able to clear one of them with the compressor, so now emptying the tank to get both lines off and unblock'em. My question - and I'm not expecting any easy solution but you never know - is how to get whatever crud is in the bottom of the tank out without removing the tank (and doing the job properly, I hear you say!). Is there something I can put in the tank for a while and then drain it out? I thought off putting a compressor hose into the tank to blow stuff around and hopefully loosen most of the dross but even that would work better if there was some sort of solution in the tank to swill around. I vaguely remember a petrol tank reconditioning item - might have been POR8 but really can't recall - that included something to clean the tank first.....? Cheers James
-
A bit of light relief! Checked the voltage of the tachometer terminals (bottom 2)at the drivers panel: nothing. Hit my head crawling around in the fighting compartment but found the junction box on the hull side beside the Commanders seat pedestal Lid off and checked voltage at the Tachometer Generator terminals (2nd and 3rd bottom from left): nothing So rotated the gun to the left to get at the bulkhead panel (the panel above it is the aux gen control) Off with the panel and... If you have a keen eye you'll spot the loose cable hanging down on the left Voila! Cheers James
-
Thanks Adrian, that's great. Trawled through the manuals again last night and found a reference to a junction box in the turret, so I'll try testing at that point first, when i get back to the shed. Should show which end of the system is playing up (or maybe hopefully just a bad connection at the junction box). James
-
Thanks Caddy. Still not sure how to get at it but will see if I can remove a bulkhead plate to spot it. James
-
The tachometer on the cent isn't working. It's apparently just a simple voltmeter that runs off a tachometer generator on the front of the B (right) bank of the Meteor. I've read the manuals and know where it's supposed to be but haven't spotted it yet - will see if I can remove a bulk head plate to find it so I can test it. I suspect it's just a loose connection and the tachometer is a lot easier to get at, so plan to start at that end and make sure the tachometer is working. So my question is, how do I test it? I guess connecting the terminal to a battery would do the job but not sure what voltage would be OK without damaging it. A car battery seems a bit over engineered and not sure if that would be safe. Cheers James
-
Not a bad day today so started the Cent without any problem but noticed the tachometer isn't working. I've read all the stuff I can find and it seems that it's just a simple voltmeter connected to a tachometer generator on the front of B (right) bank of the Meteor. Everything else is working. I'm guessing it's just a loose connection but can't spot the tachometer generator from the top of the engine bay and not too sure which wires to fiddle with on the driver's panel (although if push comes to shove I'll pull that apart) so I'm a bit lost! Anyone know how to find/check the tachometer generator end of things, and how to check the tachometer itself? (Bearing in mind that my knowledge of the black art of electrics is pretty basic). Cheers James
-
I agree - absolutely fantastic work! I've got plenty of work for you in my shed when you're ready! James