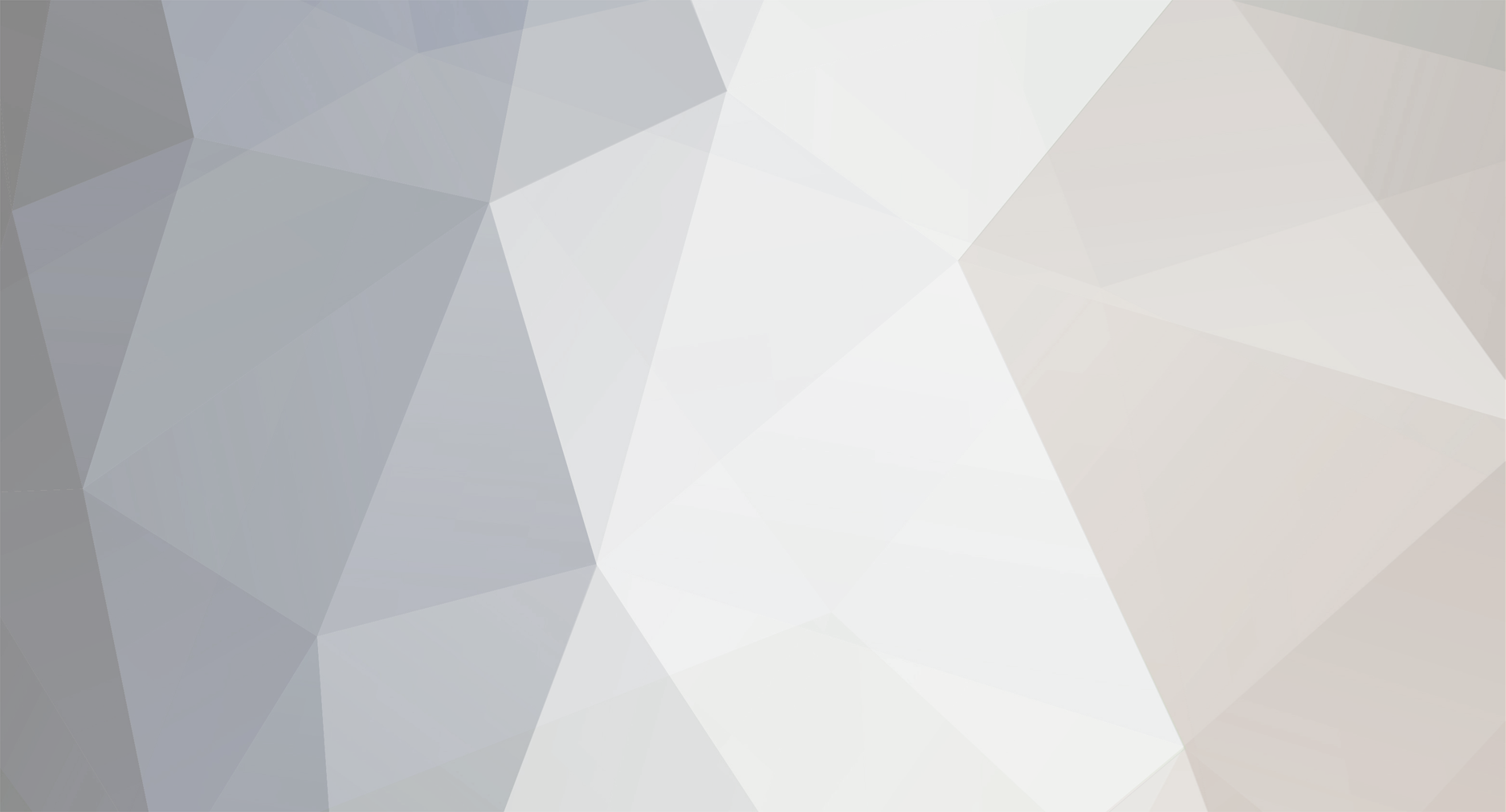
Aussie
Members-
Posts
172 -
Joined
-
Last visited
-
Days Won
1
Content Type
Profiles
Forums
Gallery
Blogs
Events
Articles
Store
Downloads
Everything posted by Aussie
-
I made one (see "Ozzie Saladin") but didn't entirely trust my welds. So I wound the adjuster down to expose about 23 threads, then put on the unloader to take up the tension (but without trying to wind it down any further). Then wound the adjuster up to the top again and it was well clear to remove. Having said that, it wasn't hard to make the unloader, and I suspect it will be needed when putting the wheel stations back on. James
-
I need to remove some old electric cables coming out of the hull exterior. These come out through metal bosses welded to the hull but I can't easily undo any of the nuts and don't know exactly what I should be doing. For example, the cables at the rear end appear as two cables on the outside but only one on the inside, and they seem too big to fit through the boss. I wonder if there is a connecting plug and if so I'll just pull them off. However the cables are pretty ratty and I don't want to be yanking them off if this isn't correct. Seems it's too easy a procedure to rate a mention in my manuals, so advice is appreciated! James
-
Someone told me that these brakes were used on Rolls some years (if not decades) earlier - not sure if that's true. They look very complicated but basically there are two pressure (disc) plates, inner and outer, with a central plate in between. The central plate moves with the wheel so when it's squashed it stops. The outer pressure plate can only move forward and back along the line of the axle, and the adjusting ring (with the serrated teeth) is used with the "special tool" to tighten the brake by screwing the outer plate in against the central plate. There are two hydraulic cylinders that push on the inner face of the inner pressure plate. There are also ball bearings involved in this process - the the inner plate can swivel to a limited extent and this pushes the BB out to help stabilise the pressure (they are opposite the cylinders). Can't imagine why they used boring-old drum brakes on the Saracens, etc! I like the look of those O rings in lieu of cork packings. Do you have the size/specifications?
-
Thanks Andy. You're a life saver! Another duhhhh moment. I had taken off the big drain plugs but after your post I stuck my finger up the hole and discovered another plug (the culprit). It is on the Parts pic (16) but I hadn't spotted it. Two pics: one with the plug where it should be (i.e. box flush with hull) and the second with it jammed. And the two plugs The boxes then came out without protest. I guess my two things to remember are 1. If it feels like you're pushing metal against metal you most likely are, and should have another look around 2. Must remember that the plug will need to go back in after the bevel boxes are back in position. And, of course, 3. If you can't figure something out, ask for help! Thanks again James
-
I'm stuck! Well the FR and FL bevel boxes are, and I'd really appreciate help from folks who have got these out, bearing in mind that I think the problem is rust but might be missing something obvious. I've removed pinions, cables and inner housings, so can't see anywhere that should be catching. However when I tried the extractor bolts the boxes moved out easily enough to be flush with the ends of their mounting studs, but then no further, and really solidly stuck - no give at all. Not to be deterred, I put my trusty 3/4" bar breaker on, and managed to snap off one of the extractor bolts (High tensile). Knew it would happen but .. should have known better. Plan C was to put a jack between the boxes but that didn't work - no movement at all. Felt as if I was just trying to jack the sides of the hull apart - very solid! Plan D was a heavy hammer with the above - no help Plan E was to squirt Penetrene on the outer bit showing, then tap the box back in, then Penetrene to the inner aspect, then extract. Repeated this several times but still sticks at exactly the same spot. Plan F will probably be to heat the hull housings and try A to E again, but while 99% is rust there's now a fair bit of Penetrene around so not sure that this is completely safe/sensible. So I'm out of easy solutions for this and really do need some inspiration. James
-
Hi Terry Tim Vibert had some a few months ago - don't know if he still does. They are/were the correct pattern. You could also look at http://www.modsurplus.co.uk/index.php?option=com_joodb&view=article&joobase=10&id=32886&Itemid=129. They are straight bar treads and not RF so not the same tread as the Trak grips. James
-
Thanks James. Very interesting and helpful. Regarding the pressure relief valves on the bevel boxes, I wonder if anyone has tried adjusting these to reduce the pressure that they open at? The base seems to be fixed to a hollow pin that is flanged, so to take them apart would involve grinding the flange off. Then the spring could be replaced with a weaker one, and the base fixed back on by splaying out the end of the rod again. [ATTACH=CONFIG]87861[/ATTACH] Then again, if the rod is lifted slightly the pressure is zero So.. i wonder if you could just put a circlip or equivalent where the scissors are in the pic. That would relieve the pressure and I don't expect that too much oil would leak out (?). The rod could move further out if there was more pressure, and if you wanted to go swimming the circlips could be removed. Seems too easy, so is it a silly idea? James
-
Wow - that looks so nice and clean and shiny! Please let me know about the seals - I'd probably prefer new, if anyone makes them. Also, could you expand on the non pressure breathers you put in? And the O rings instead of cork sounds like an interesting idea too. Have removed 5 of the hull suspension brackets - nothing terribly exciting but time consuming and fiddly. To remove LF I need to remove the steering jack to get at bolts but the jack needs to come out anyway - needs a new dust boot, at least. A couple of things.. The "special" bevel box bolts have a smaller head and thick washer so you can get at them. However one was so rusted I couldn't get anything on it, so had to drill it out. Think I'll get a turned-down stainless bolt to replace it, although hopefully the beast won't be so badly abused from now on. The suspension bolts are different lengths. Logical enough but seems simplest to put them back where they came from, before storage. Housekeeping.. Got a drum of degreaser that I really don't use that much for parts (not much grease to remove!). However it's fantastic for cleaning the floor - wipe a bit on and mop off with water. Be careful with ventilation, etc, etc, etc, of course.
-
Time for an update. Basically working on bits and pieces rather haphazardly but now think I have a better plan (basically what everyone else did from the start). So.. Made a spanner to undo the spherical housing, but have some NOS wheel stations so rather than fiddle I think i'll use the NOS wherever possible and keep the others for spares. Seals for the spherical housings seem to be hard to get, so if anyone has any ideas I'd be grateful. Also made a tool to unload the torsion bar adjusters but don't entirely trust my welds, so rather than follow the EMER (slacken the adjusters fully then use the tool to pull the adjuster lever down) I tighten the adjuster nut down to expose about 22 threads, then put on the tool but use it just to hold the adjuster bar down. Then slacken off the adjuster nut and the adjuster can be removed. I'm now pretty good at removing wheel stations, having finally removed the lot! Lessons? Well, the RF was a chore. Firstly the steering arm wouldn't come out - was looking at the angle grinder but fortunately found a spanner first, and unscrewed the arm. Then tried to remove the wheel housing. Bit of a long story but when I finally jacked it off with a Portapower I discovered that the shaft wasn't connected. So the outer bit came off, leaving the spherical housing and a bit of shaft bit no tracta shaft inside. Seems someone broke the tracta shaft (probably wound it up too much) and then just removed the broken shaft, leaving RF to free wheel (until the wheel bearing seized). Didn't bolt the intermediate shaft back on, and forgot to put a bit of oil back in. So, I put the portapower between the hull and the end of the shaft, and jacked - and jacked - then there was a loud bang as it exploded out of the bevel box, landing a few feet away (but missing my head). SWMBO promptly threatened to have it all carted away but I promised to be more careful. The bevel box is seized/rusty so needs to come out. Scraping muck of the outer face revealed the two threaded extractor holes (top right, bottom left). Bolts screwed into this should push the bevel box out. Off course, to get the bevel box out you need to remove the pinion housing. The bottom inside bolt has a smaller head and thicker washer to allow you to get at it. When you take the housing off, remember to keep the shims that go with it. The other wheel stations were reasonable except for the top link pin LC which was impossible to remove with bashing, heat, cold, Penetrene. Finally decided to cut it. Succeeded but swore I'd never do it again. Total shocker to cut - don't do it! A couple of stations wouldn't "pop out" so for these I jacked the bottom out to push the housing clear. (Tried jacking the Station up but actually started to lift the whole vehicle off its jacks, which was a bit unsettling). Flushed with success i headed of to the RR torsion bar. Did get it out but the cover plate set screws against the hull are a pain to get at, and I don't know what spanner you're supposed to use. They are a weird size and I ended up filing an 8mm spanner to remove less then half a mm so it would fit. 15/32 was a loose fit. My "extractor" was made up on the spot - ended up lightly jacking it out but wasn't tight. More grease than I've seen anywhere else on the beast! The next challenge is to get the torsion tube and upper and lower links off (I think the NOS wheel stations don't have the hull bracket - haven't seen them yet). However after fiddling with more cover plate screws I bit the bullet and did what I should have done in the first place - was trying not to remove the hull brackets because to remove a couple of the bolts you have to remove the bevel box pinion housing. But in the long run I reckon it's the way to go. That way I can clean and paint the lower hull properly, and leave the brackets, etc, for (yet) another day.
-
question Rc of Steel, british armor, Saracen, ferret etc.
Aussie replied to Cold_War_Collection's question in I may be stupid, but......
That's really helpful. I have broken studs and thought I'd have to drill out the old shanks, then put new ones in the holes and weld. Grinding the old ones flat and then welding new ones onto the surface should be much simpler! -
Pics of the offending RF Bevel box. First shows box partly jacked out (then the shaft exploded off so I lost my anchor point for the jack) Second shows the outer face of the box Third, after scraping mud etc off, shows two threaded holes top right and bottom left. Bolts screwed into these will push the box out (more safely then jacking it!) Now off to buy some bolts..
-
Thanks guys. Solved the problem by scraping the muck off the outer face. Found two threaded holes at 1 and 7 o'clock, after digging grunge out of them. Will thread bolts into those and they should wind the case away from the hull. Safer than what I was trying. The shaft was stuck in the bevel box so I put an hydraulic ram between the shaft coupling and the hull, and jacked - and jacked - - the bevel box moved out to the end of the bolts then suddenly the shaft exploded out of the box and landed 5 feet away. Fortunately my head wasn't in the way but SWMBO has threatened to get it all towed away before I do myself more serious damage. Promised to be more careful. Also solved a puzzle as to why that wheel free-wheeled (until the wheel bearings seized) - someone obviously broke the tracta shaft (presumably wound up the transmission too much) and just removed it! Simple really! Pity they didn't put a bit of oil back in. Left camera at work but will post a pic later, either here or on MV resto "Ozzie Saladin" James
-
The gift that keeps on giving. Front bevel boxes are seized (full of water instead of oil) so they need to come out. Have undone all the nuts on outer flange and removed pinion housing. But it won't come out (no surprise, really). EMER says use two 7/16UNF extractor bolts but don't show a picture of what these look like or where they fit. Can anyone help? The other option is to jack them out from the inside of the hull but seems a trifle brutal. Thanks, James.
-
Not feeling quite so stupid so back on this post! The front wheels are locked, although they did turn a while back (in fact RF "free wheeled". Anyway, I disconnected the brake plate and drum (thumb) and the pressure plate (forefinger) spins freely, so I assume that exonerates the brake. I removed the outer ring of nuts to remove the housing, but was unable to remove the two slotted plugs to insert extractor bolts. Spent a while making a fancy attachment, thinking I could tighten down the hub nuts and press on the shaft to extract it: Waste of time! The flat bit of angle iron just bent. I can see how this could be made to work, but in the end decided to just bolt the hub cap back on and hit it This would work quite well if everything wasn't seized! So the hammer got heavier and temper shorter, but eventually got it moving. Used pine wood wedges while hitting it out, to give more leverage You can see where it separates - near the end of the wheel studs (not up against the brake drum, as I'd assumed). As it came out i got another trickle of water (yes, water!) So, out it came, in all it's rusty glory. However the gears themselves look ok, with no broken teeth. There are shims against the sun gear (I've left it on the shaft for the moment) and they need to go back the same. To remove the planet gear housing you undo the 5 housing nuts on the outer face, after removing split pins. This was a tight squeeze for my socket but was able to tap it on gently with a hammer. Then you put the housing with the inside facing down and gently tap the planet pins - these are actually also the hub cap bolts And with pins/bolts tapped in And you end up with the housing - there are big washers between it and the planet housing visible at the bottom) and they need to go back on reassembly. Tap out the tracta ball bearing - mine is seized, so part of the problem. And the 5 planet gears. Two spun easily and three were seized. So - I lifted one of them off its shaft. It came out quite easily and I was left with a handful of needle roller bearings! These a pretty grungy but should clean up if I can't buy new ones. Putting them back in will be quite a challenge, I suspect, so if your planet gears move freely, leave them in peace! The gears are tarnished but i think they will clean up with wet and dry paper. Each gear has one tooth marked with a centre punch (at the top in pic). These marks need to be lined up (on an imaginary line between the planet gear shaft and the central tracta shaft) on reassembly and as far as I can see, this is all that's involved with "timing" them. So now I'll spend some quality time cleaning this mess up and getting the roller bearings back together, as well as getting a new tracta bearing. And the good news (a gift that keeps on giving!) is that the wheel is still seized, so there's more trouble upstream. I'm guessing the other bearing but time will tell. Cheers James
-
Yes it looks a bit different. I'll remove the locking tab and unscrew the inner threaded nut (on the right in the pic before) then drift out the two dowels and it will come apart. The shaft comes apart in the centre, that's not a problem, so the inner part of the housing, with the oil seal, will then slip off over the shaft. Will post pics when I get to it (need to get the seals first!). BTW I'm now looking at my seized front wheels. Posted on the "I'm stupid" forum but any advice appreciated. I'm planning to pull the hub housing off by pressing the hub bolts out against the end of the shaft, and hope that's not a silly thing to do.. Will post pics on here when I know a bit more about what's going on (suspect it's because hubs are full of water not oil). Cheers James
-
Thanks guys. Understand what to do now. Will post pics when I get the seals and make the tool to unscrew the nut.
-
Front wheels are both seized, although they did turn a while ago. Anyway, I disconnected the brake plate and drum (thumb), and the pressure plate (forefinger) rotates freely, so I think that rules out the brake as the culprit(?). Then removed the hub cap and, joy of joys, got just a few ml of water dripping into the bucket. (Can't get the drain plug to bottom centre to drain the rest, due to the wheel being seized) So, my opening question as I come to terms with what is wrong: I've removed the outer housing nuts but see no chance of removing the two slotted plugs to insert "extraction bolts" (whatever that is) other than by drilling them out. Also can't see any way to remove the bearing without removing the housing. Would it be ok to bolt a bracket onto the hub plate bolts and then push that out with a bolt screwed against the end of the shaft? I also considered putting the hub plate back on and hitting it with a hammer, but that seems a bit brutal. Thanks James
-
Pic from "the outside looking in" probably not all that helpful because it's "3D", with a tubular housing and with the bevel box shaft sticking out from the base. Still I find pics less confusing than drawings so here's a couple. The tracta shaft slides into the tubular housing and the cork gasket can be seen near the outer edge. EMERs warn not to damage this, and I didn't but confess I had no idea where or what it was beforehand! The oil seal fits between the spherical end of the shaft and the inner aspect of the cylindrical bit in the last pic. It's quite a thick rubber ring. On swivelling the housing (only rotates up and down, of course) the oil seal wiped off the gunk on the sphere, so a gentle clean should fix that. (On first looking at it I thought I might need to use wet and dry paper). There are small gaps visible between the seal and the housing, and between the seal and the sphere, but this might be the way it fits, with deeper portion doing the sealing. Now my question, and please be gentle! I have no mechanical know-how other than what I'm gradually learning. I'm yet to get the seals, however do I just lever the old one out and push in the new - i.e. will it "click" into place and stay there? I assume that's the case but will I need to fix it in with a sealant/glue of some sort? Next adventure will be to see why the front wheels are seized - it isn't the brakes so...
-
Not sure. Out of 15 released all had their turrets removed to beef up M113s, then 6 M113s were sold to New Zealand minus their turrets. So 6 turrets found their way back to Saladins (I guess), leaving 9 "headless" ones. There's one at Puckapunyal Army Museum, one that I know is being restored at present, and I think another (but might be the same one) that was on utube a while back. I've seen an M113 with Saladin turret - they do look pretty cool - and a chopped one (no turret or armour above hull line) in a paddock that will probably end up being restored. An HMVF member is restoring a turret in UK for me so I'll end up with a complete vehicle (10 year plan!). Interestingly, I have a photo of a photo of my vehicle around 1965 in the Aus army, but can't post it without permission from the owner of the pic (Prince of Wales light Horse Museum).
-
Think I ran out of time to get pics inserted, so will try again and ignore previous post (maybe an administrator could remove it?). This is an outline of how I removed the right centre wheel station, and hopefully will help someone tackling this. 1. The hand brake attachment to the brake drum had me perplexed but it's just held on by a cir clip (or e clip) so lever it off and the cable comes out the slot at the back of the housing. 2. Unscrewing the hydraulic line from the brake plate just "wound it up". Unscrewed easily from the hull end, where there is a sleeve that allows the nut to turn. 3. Undo the drain plug and drain the wheel station (I got about 300ml!) 4. Instructions were to remove the cable housing from the back of the brake plate but couldn't see the point. However my beast is pretty much disassembled so might need to do this if the hydraulics etc are all connected. 5. Remove the steering link. Couldn't get mine off from the brake end (wouldn't fit past housing on back of the brake plate) and had to drill out the nut on the ball joint on the hull end because it was just all spinning around. 6. Wedges for holding the top suspension bracket horizontal - angle grinder and a bit of welding for the handles. 7. Remove tension on the torsion bar by winding adjuster up as high as it will go. BUT first count the exposed threads so you can get it back in the same position. Mine had 12 threads - wrote it on the hull and must remember to not wire brush it off before writing it somewhere else! 8. Then lift up wheel station so top link is horizontal, and slip wedges between the bottom of the top link and the stops attached to hull. Then remove hoist and the wheel station is fully supported by the top link. 9. Now remove the bottom suspension link shaft and let it hang down. There are locking taper pins for both upper shaft (to rear) and bottom shaft (underneath the front end) to remove first. Then drive out the lower shaft FORWARD, i.e. hitting the end with the single hole in it. This the opposite end to where the locking pin was. Edited Nov '14. This isn't correct for the newer shafts! Mine were early ones and completely straight. On fiddling with a NOS wheel station I discovered that the newer shafts have a swelling at the end with single hole in it. So it didn't actually matter which way I bashed my straight shafts but for the newer ones (and logically for all) the shaft needs to come out with the single hole first. In other words, if you are hitting one end it needs to be the OPPOSITE end, NOT the one with the single hole. First pic shows old (straight) shaft on left and newer one on right. Second pic shows the direction the shaft actually needs to come out. You can't remove the newer ones in the opposite direction, due to the swelling on the end with the single hole. (Put a jack under the bottom link so it doesn't drop when the shaft comes out). Note you don't need the hoist for this step - everything is supported on the top suspension link. The bottom shaft was very dry, and while the taper locking pin for the top shaft was ok, the bottom one (on the right) was broken and therefore useless as a locking pin. 10. Remove the drain plug under the bevel box and drain (I got about 30ml!). Then remove the strap holding the bevel box end of the rubber boot and peel back. (Not sure that you really need to peel it back, and have a horrible feeling that my spherical housing might have a few dings in it). 11. Almost there! Attach your chain/pulley (I used and old bit off a 3 phase winch) or make up a jacking bracket (seemed too complicated for me) and take the weight of the wheel station. The knock out the top suspension link shaft - so the end with the single hole comes out first 12. Now just pull back gently and it all slides out, beautifully balanced on the chain! What didn't I do? I removed the whole unit rather than trying to disconnect the intermediate shaft pin, because I figure this will be easier with it all out, and I want to get at the oil seal at the bevel box end anyway. Now for more research to see where to go next! Cheers James
-
Removing Saladin brake cable and wheel stations
Aussie replied to Aussie's question in I may be stupid, but......
Eureka! I hadn't considered a circlip but makes a lot of sense. Will have at it tomorrow! Thanks a heap. -
Removing Saladin brake cable and wheel stations
Aussie replied to Aussie's question in I may be stupid, but......
Point taken. It's actually supported on 4 ton axle stands. The pavers (and jacks) are optional extras. Cheers. -
Removing Saladin brake cable and wheel stations
Aussie posted a question in I may be stupid, but......
I'm having trouble figuring out how to get my wheel stations off. The main aim is to replace the oil seals on the shaft coming out of the bevel box. So I'd be grateful for help with beginner questions. 1. Removing the brake cable from the back of the brake plate. The cable goes through a fitting that has a washer on it to hold it in the housing, but I can't see whether I should just lever that washer off or if the end screws off? 2. If I want to replace the oil seals, should I remove the whole hub assembly and tracta shafts - i.e. remove the end in the bevel box as well? Or should I knock out the pin in the second shaft so to leave the top shaft attached to bevel box? 3. I think I'm supposed to jack up the hub so the bottom link is level but this will have the hub an awful long way off the ground. Is this necessary/advisable? 4. What's the best way to support the wheel station to remove it? My Saracen EMER shows a lifting bracket that is fixed to 2 wheel studs. Another way seems to be to put a chain on an engine lifter and pulley, and run that in the groove behind the front brake plate - I guess that would allow more rocking/swivelling to get the shafts off? Thanks so much for any help. This is frustrating! Aslo if anyone has EMERs for the wheel stations, brakes and engine ..?? Cheers James -
Thanks for that Terry. Then it's a Mk 3 as I'd originally thought.