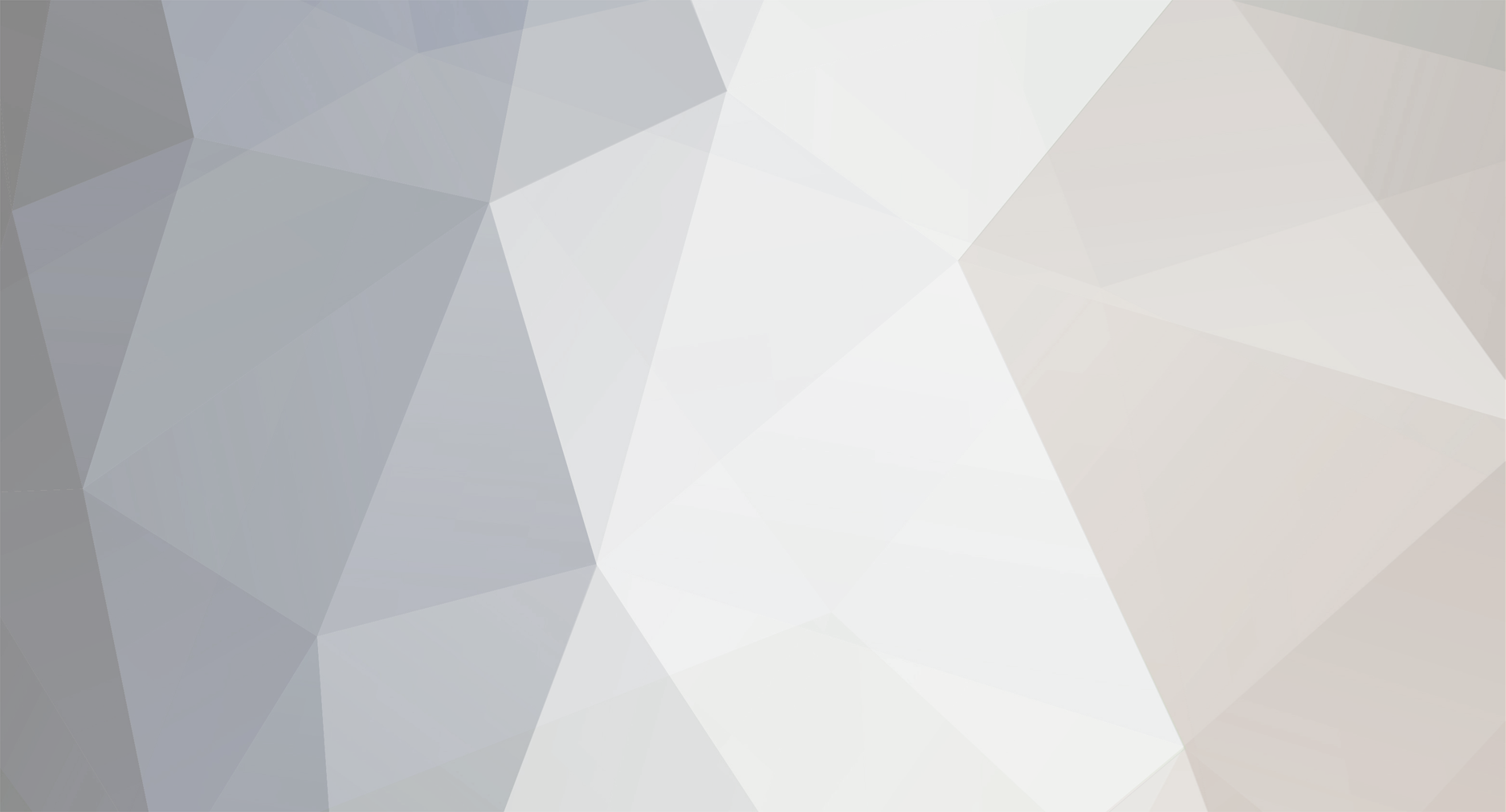
andypugh
-
Posts
796 -
Joined
-
Last visited
-
Days Won
10
Content Type
Profiles
Forums
Gallery
Blogs
Events
Articles
Store
Downloads
Posts posted by andypugh
-
-
49 minutes ago, radiomike7 said:
If going down the generator route bear in mind you may need a larger amp rating than the full load amps due to the starting current which you should be able to calculate from the motor characteristics.
Thinking about it, running an engine to drive a generator to drive a motor is silly. It makes far more sense to convert the lathe to run from line-shafting driven directly by the engine. And, to be green, the engine should be multi-fuel, maybe external-combustion. 🙂
Yes, a steam engine and big whippy flat-belts is definitely the right approach here.
-
7 hours ago, mammoth said:
I will opt to purchase a generator.
A VFD might be more convenient, and quieter. Though could be tricky if the motor is pole-switching or Dahlander and not re-wirable for 240V operation.
-
Quote
The hubs came off the axle as described, the nut being quite loose (should it be tight or not?)
No, the nut should be set to give bearing clearance between the hub and a thrust-washer on the axle and then locked in place with a split-pin.
You might not still have the thrust washer, or it might be friction-welded to the hub or the axle by now. I have once had to grind one off (On an N-type in Tunbridge Wells, I think, or it might have been the one in Thaxted)
Quoteand showing the bearing sleave with no wear - a nice find. No linings on the brake shoes
The brakes were originally iron-on-iron, any linings are retrofitted. Some owners are still using iron-on-iron and report that the brakes work at least as poorly as the lined ones.
-
39 minutes ago, PITT24423 said:
Looking for a magneto drive coupling which to date I haven’t been able to source as the original is just about torn out
That style of coupling is pretty standard, but maybe not in the exact size you need. Do you know the tooth count and the diameters?
It's possible that one of these might fit: https://www.bearingsrus.co.uk/transmisson-products/coupling/bowex-gear-coupling
Otherwise I would be looking at 3D printing. Given some basic diameters I can model and print you one.
-
A less traditional approach might be to leave the ring unjointed, weld brackets to the join. Pull it up very tight, MIG weld the join and grind off the brackets. This probably won’t pull up as tight as a well-executed shrink fit, but might be more relaxing than a badly executed one.
-
14 minutes ago, Asciidv said:
Andy the profile of the spokes is actually quite complex.
That's why I am suggesting the copying machine.
If you do make your own spokes, then my watching of Engelscoachshop would lead me to suggest not cutting the tenons, or leaving them very short. That seems to be their main adjustment.
-
It also appears that the brake drum mounting ones have a definite bulge, rather than just a lesser degree of radiusing where the bolts go through?
Possibly made with a form tool originally?
Anyway, the answer is probably to make a copy machine, like this one:-
1
-
-
5 minutes ago, andypugh said:
Try eBay for long-series cutters. https://www.ebay.co.uk/itm/193879967564 for example.
Thinking further: https://www.ebay.co.uk/itm/174707121469 in a CNC horizontal mill might work. How tight is that internal radius?
I do have a long 25mm cutter going spare: https://photos.app.goo.gl/U8TiSe9iKoyeYzow8Throwing money at a wheelwright might be the more expedient solution.
If you do want to make your own wheels (and it is something that I have always fancied a go at myself) then watching "Engel's Coach Shop" on that YouTube might be rather informative.
-
Try eBay for long-series cutters. https://www.ebay.co.uk/itm/193879967564 for example.
-
1 hour ago, mammoth said:
I think you are right Andy, however separating the hub from the axle beam will need to be achieved first. (Barry, can you advise?)
Having taken the wheels off of N-types more often than most myself....
You should be able to just undo the nut.
The half-shaft is anchored inside the differential.
The hub runs on a bearing on the outside of the axle tube.
The "spider" is keyed to the half-shaft and held on by the nut.
The nut clamps the hub between the spider and the thrust bearing ring.
The spider transfers the torque from the half-shaft to the hub.
-
1 hour ago, Scrunt & Farthing said:
What gauge is that, Andy?
Around .25mm / 0.010" or something like 33 SWG.
-
1
-
-
You need some sort of embiggening chamber.
As for the welded-on parts, I think that I would be looking to plasma-cut off the modern wheel and then machine off the weld (and remaining bits of wheel) on a lathe.
Though the "modern" wheel looks plenty old, too.
-
4 hours ago, Scrunt & Farthing said:
I am in similar straits myself, and surprised by the size of the number needed to have a new one made. In particular the number of zeroes in the number made me think I might need to save up for rather a long time.
-
1
-
-
I wonder if screen-printing resist would work?
https://www.amazon.co.uk/Hunt-Moon-Screen-Printing-Emulsion/dp/B07PFWC1ZD
I used some for screen-printing and it gave excellent results just exposed in sunlight.
(https://photos.app.goo.gl/gNhHZ6pHHJCv9ZLEA was the final result)
-
Interesting to see that even when new there had to be plenty of drip trays under them.
-
37 minutes ago, alsfarms said:
Hello Dave, I tired several ways to see what you are selling on US EBAY and also UK EBAY.
It's item 284246864651 - http://www.ebay.co.uk/itm/284246864651
But utterly irrelevant to this thread.
-
1
-
-
9 hours ago, radiomike7 said:
I don't remember how they managed reverse without reverting to spur gears but I am confident some one on here will know....
You just cross the chain, obviously 🙂
(My grandfather used to say that he once tried that, when they simply could not get a motor on some equipment to reverse. I have never been sure whether he was serious, and it is now several decades too late to ask)
-
2 hours ago, Doc said:
Nails and screws were all sunk below the surface of the boards and hidden with linseed putty.
I recently watched a YouTube video of a chap making a new front door for his Victorian house and painting it in the Victorian manner. An interesting take-away was that you can fill with linseed oil putty then paint straight over. Both the paint and the putty are a mixture of linseed oil and whiting, so it shouldn't really be a surprise.
-
1
-
-
9 hours ago, Scrunt & Farthing said:
Does a worm drive prevent you from "bump starting", due to the irreversibility (or inability to back drive) of a worm drive?
They are typically low enough ratio to be reversible.
We have an old worm-drive chain hoist. That is irreversible, but only because it has a friction brake on the end of the worm shaft. With good bearings and adequate lubrication worm drives are fully reversible up to fairly high ratios.
-
1 hour ago, racer said:
do you get any feeling of "braking" when lifting off the throttle due to it's design ?
They feel exactly like any other differential.
-
36 minutes ago, Asciidv said:
Andy, do you have any facility to grind the balls after they have been turned? I noticed that your lathe has variable speed but the sound from it did not seem to be synchronised with ball diameter only to the start and end of each cutting cycle?
I have a tool and cutter grinder which is, in theory, capable of grinding spheres. On my particular one (early Alexander) there is no easy way to disable the 90 degree stop.
The lathe speed is synchronised to the current working diameter, but the VFD control is slightly laggy so might get left behind on small diameters / short passes.
The speed changes are more obvious at the start and end of each pass, but it should be running at constant surface speed.
The VFD is controlled by Modbus through a USB interface. I would like to bring that into the realtime layer, but that needs new drivers for the Mesa interface cards. This is not an unsurmountable problem, as I am the guy who writes the LinuxCNC drivers for the Mesa cards.
-
1 hour ago, BenHawkins said:
Thanks Andy, I will dig out the original factory drawing and annotate it for the new diameter, or is a new fangled step file better?
Step should work, but a traditional drawing is probably about as easy.
-
Seen on that YouTube:
Possibly some interesting materials and techniques there.
-
3
-
-
2 hours ago, Doc said:
First machine to see action is my Dean Smith and Grace lathe.
A Yorkshire lathe for a Yorkshire truck.
Though, at the time, most of them were.
Daimler CB22
in Pre WW2 vehicles
Posted
Our 1916 Dennis has a bronze wheel like this. It has been running on generic "steam oil"[1] with the club since 1955 doing around 1000 miles a year (which isn't a lot. but probably more than most solid-tyred vehicles). Last time I saw the wheel it looked great.
[1] As far as I know, Valvata 1000. Ben might know if that is still what they use.