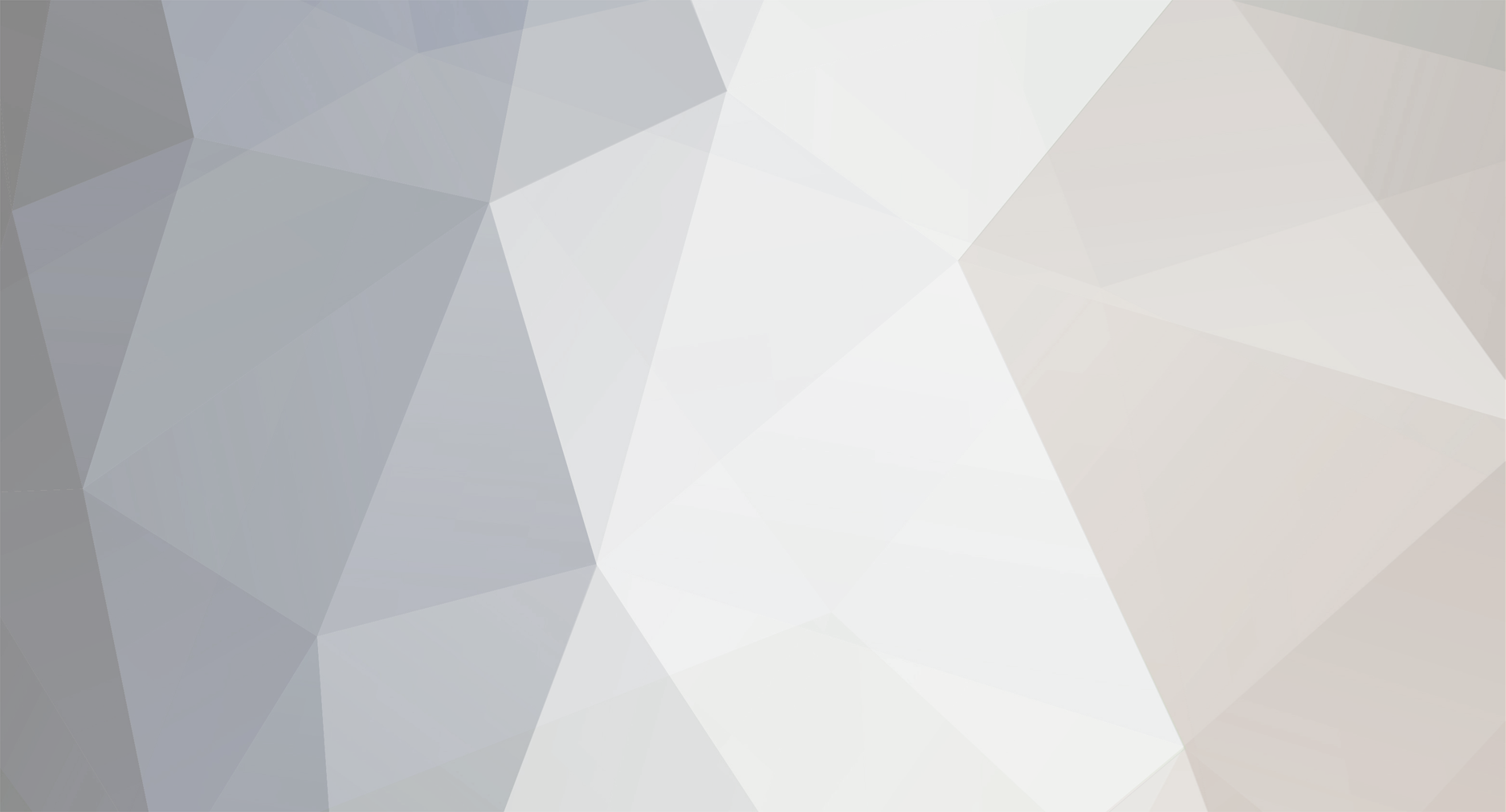
andypugh
-
Posts
797 -
Joined
-
Last visited
-
Days Won
10
Content Type
Profiles
Forums
Gallery
Blogs
Events
Articles
Store
Downloads
Posts posted by andypugh
-
-
16 minutes ago, Doc said:
breaking sharp edges. We'll not say too much about that...
I think it's legitimate enough, there are even special files for the job:
https://www.amazon.co.uk/Bahco-1-104-14-3-0-Lathe-File/dp/B0002YQ5PI
-
1 minute ago, andypugh said:
Very readily available, too:
Next day from Amazon, even. Though probably not in Imperial Sizes.
-
15 minutes ago, Great War truck said:
The Spring is of a square section wire and is there a significance in that?
Die Springs are often square section. A square section spring is slightly stiffer for the same outline dimensions.
Very readily available, too:
-
1 hour ago, Tomo.T said:
After some further file and sanding work the job is now ready for the grips to be applied (with solder)
I think that I would seriously consider epoxy.
1 hour ago, Tomo.T said:Thanks due to to Mike, Stan and Pipecraft Innovations Ltd. of Lancing, W. Sussex. who did a nice accurate job of the tube ring.
In fact the ring is so good that I am going to suggest a way to show off 🙂
Get them to make a bigger complete ring. Cut it in half horizontally, then press divots in the bottom half with a specially-made press-tool. Cut slots for the spokes and then cast bakelite round the wheel.
I don't think an authentic reproduction is out-of-reach. But I also don't think it is worth the effort.
-
1
-
-
51 minutes ago, Old Bill said:
Then there was the next challenge. How to compress the return springs to fit them!
Big cable ties? Worth a try.
-
-
https://www.the-saleroom.com/en-gb/auction-catalogues/gilbert-baitson
Mainly _very_ Pre WW2. But there might be some stuff there.
-
How bad is the switch? If the metal is intact then I would imagine that the rest can be re-made?
You can get suitable Tufnol / Bakelite from eBay (amongst other places). I used some to make some replica Ner-a-Car light switches. (Now _there_ is a hens-teeth item: https://bodgesoc.blogspot.com/2014/11/the-last-bits-and-pieces.html ) -
27 minutes ago, mammoth said:
Well bought. Maybe it is too good to use as a donor??
Well there are complete trucks trundling around that started with a lot less.
-
it would look a lot better on solid tyres, in my opinion. But would also be less practical.
-
Or, I suppose, just pay the £20 for this die: https://www.ebay.co.uk/itm/1-3-16-x-12-die/283383706282
-
Another option would be a Coventry Die Head. I know where there is one (South Kensington) but it's all covidded shut. And is likely to be too small.
Though that does suggest another option. I know that you discounted making a die, but it might not be so hard to improvise a die using: https://www.ebay.co.uk/itm/391436755923
Maybe just a guide hole with a single die-head cutter running in a slot advanced by a bolt? Wood would probably work, or 3D-print.
-
36 minutes ago, Old Bill said:
However, the threads do need cleaning up. They are 1 3/16" x 12tpi which is an odd size again so now I am on a hunt for a suitable tap and die to borrow or buy. I don't want to start making those as well!
If you can get access to a lathe which has a big enough through-bore then I would suggest hand-chasing the thread.
(improvise a woodturning-style rest and let the chasing tool feed itself along. It actually goes a lot better than you might expect)
There are some on eBay at the moment, one is £5 BIN, but this one claims to be "USS": https://www.ebay.co.uk/itm/122563590343
-
I think that the springs must have had the square end formed after winding. Going (only) by the pictures I don't think that the mandrel would come out otherwise.
-
1 hour ago, Tomo.T said:
Next problem is how to re create and attach the small finger grips that surround the underside of the wheel, originally these would have been formed with the celulose coating, any suggestions please chip in.
Do you have a plan for covering the rim?
If all you need are some bumps to go under the coating, then I think I would 3D print them. Though the probable shape will make that a bit tricky as there will be no flat surfaces to sit against the print bed.
If you made a pattern from epoxy putty or similar then you could make a silicone mould and cast them in epoxy. But that would be one-by-one and pretty tedious too.
Combining the two ideas, perhaps a 3D-printed mould to form some epoxy putty into a consistent shape, then apply those to the rim. I think cling-film might be the answer to releasing the putty from the mould.
-
1
-
-
1 hour ago, BenHawkins said:
I have a feeling there should also be brass cups in the generators to hold the calcium carbide. Without brass cups I think the alkali solution of calcium hydroxide would eat through the aluminium quite quickly.
I have an aluminium acetylene generator for caving somewhere. Probably 30 years old.
But maybe ask a chemist?
-
On 6/29/2020 at 6:57 PM, TonyB said:
I believe their real value is transmitting power with heavy power loads, mills, pumps, and the steering gear on the Titanic I read.
If you google about you will see that the Titanic steering gear used the even more stupid triple-helix design.
(with a double helix the two sides can balance the load by floating the pinion laterally. Not so with a triple. And you can't cut the gears with a sunderland planer either.
-
1 hour ago, Tomo.T said:
It will pass muster at a distance and will doofa now.
It would be fairly easy to re-shape the body with a spot of hand-turning.
ie, with a rest and a hand-held bit of tool steel. (least-favourite wood chisel reground?)
-
1
-
-
3 hours ago, Scrunt & Farthing said:
What was the reason for splitting the brake drum do you think?
One possibility is to prevent cracking at the hub or spokes due to the outside getting very hot with the inside cold. (in that it is pre-cracked in a controlled way)
-
2
-
-
Mag drills are available used on eBay for reasonable money. Reasonable enough that I have one.
Though I do feel that the format of the Rotabroach Adder looks like it might be better in tight spots like old vehicle chassis. (I see some new ones for £450 on eBay today, which is a lot cheaper than normal, but still not cheap)
-
40 minutes ago, mattinker said:
I very much doubt that it was to prevent cracking, boiling water will still crack an engine!
It was 19-umpteen. A lot of engineering was based on rules of thumb and common beliefs. The baffle might have been intended to address a problem that did not exist, to address a problem that did exist, but ineffectively, or to address a real problem effectively. It is very unlikely that anyone then would have bothered to _test_ which of those it was.
Even now, where a car company might have more test vehicles than a total pre-war production run, a lot of stuff gets put in on the basis of "it probably does no harm" or a quick back-of-the-envelope FE analysis.
-
2
-
-
16 minutes ago, 79x100 said:
Thanks, I will have a look next time I pass that way. I have a bit of an interest in Karrier as my dad worked for David Browns for 50 years and I think that they made their gearboxes.
Talking of gears, if you need any then it might be worth talking to the company across the road, in case they know about Karrier and where they were made.
-
Well, I found a casino and a church in the same frame:
https://goo.gl/maps/HRkGCDo3SWyFUX637
But following the road I only found Brook Crompton motors. (important in their own right)
-
5 hours ago, Bob Grundy said:
A photograph I took of the factory at Huddersfield about 3 years ago, note the date in the stonework.
Where is that? (I was brought up in and around Huddersfield, so I think that I know roughly where that is by the style of the buildings. I would guess somewhere in the wierd maze-like one-way system south of the University)
1908 Dennis Truck
in Pre WW2 vehicles
Posted
How does the top tank attach to the radiator core?