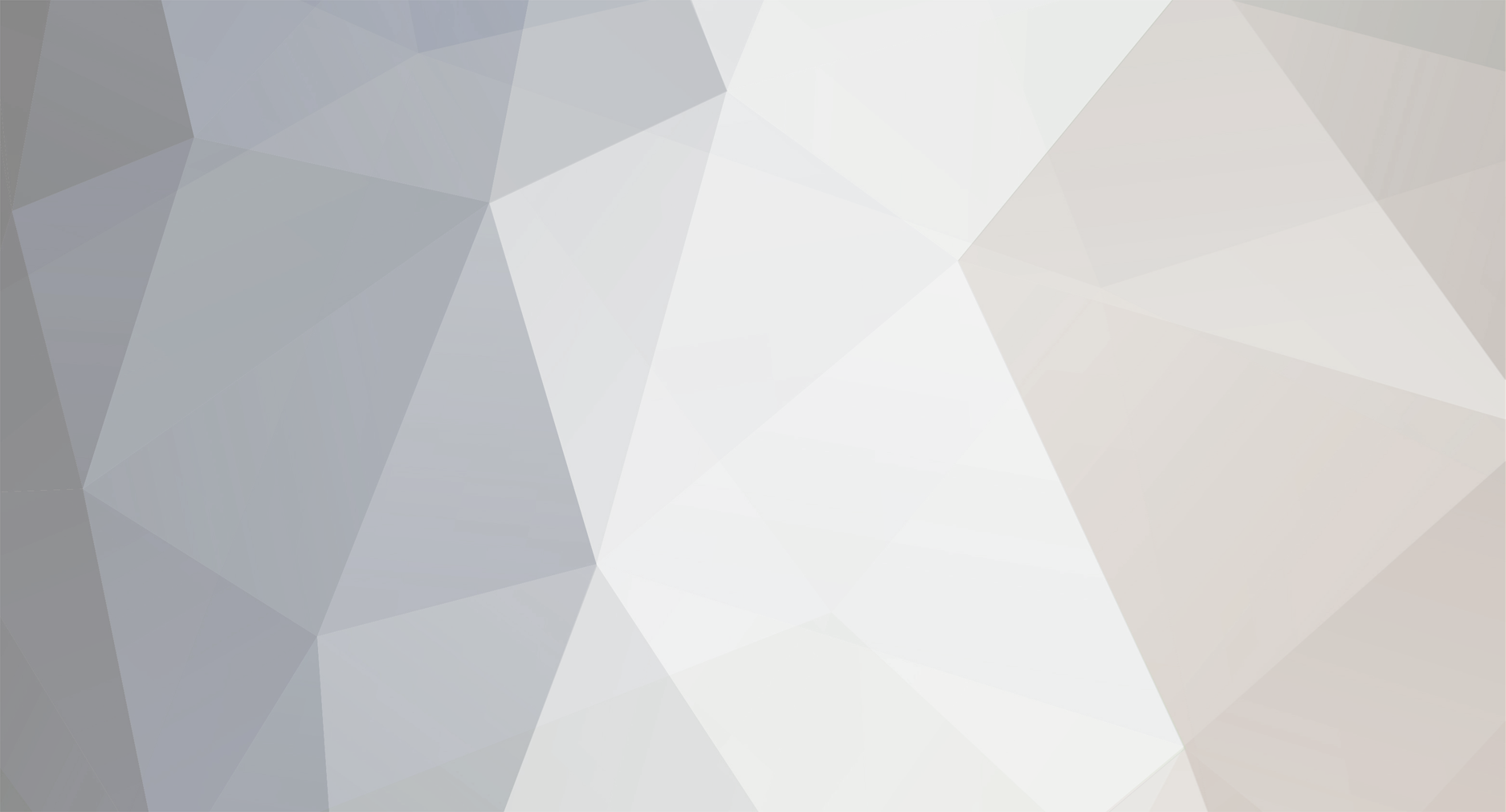
Danny P
Members-
Posts
299 -
Joined
-
Last visited
Content Type
Profiles
Forums
Gallery
Blogs
Events
Articles
Store
Downloads
Everything posted by Danny P
-
If you still need the information I will post some pictures this weekend. When I forget just let me know! Danny
-
Somebody who can recommend a steel constructor in King's Lynn, Norfolk? A friend is going to visit the UK and he will bring me some angle irons for my bedford mw 15 cwt body. I will need 1 1/2" x 1 1/2 " x 3/16" angle irons which are on the floor of the body if I'm right. Dutch angle irons are 40 mm versus british 38 mm angle irons. Yes, these issues are Dutch restorers dealing with! Thanks, Danny
-
restoration Bedford MWD restoration
Danny P replied to rampant rivet's topic in Blogs of MV restorations
That air filter looks really good but how about the air flow? Did you already test it by running your vehicle? -
Thank you both, Richard and Degsy! I've turned the adjusting wheels several times back and forward to get that feeling you were taking about and I think I have succeeded! Danny
-
Richard, Yes, we better talk about clicks rather than turns. But to my opinion the thickness of the shoes, from original ones bedded in or new ones, doesn't matter for the number of clicks turning back as the shoes are towards the drum as a starting point, or did I misunderstood you? Still not clear to me how many clicks turning back or free space at the foot brake pedal!
-
Need your help adjusting the rear brakes on my bedford MW! I have turned the rear brake shoe adjusting wheels anti-clockwise (viewed from above) as far as they will go (shoes towards the drums). Subsequently applied pressure to the footbrake pedal to centralise the shoes in the drums, and again turned the adjusting wheels as far as possible. Next I have to turn back the adjusting wheels until the road wheels rotate freely but I wonder how far should I turn them back? Are there a prescribed number of turns? I have tried a few turns and experienced that this will set the free space of the footbrake until pressure. How far should the free space of the footbrake pedal be (lost that feeling)? And how much is it allowed rubbing the shoes against the drums or what is meant by rotate freely? Thanks, Danny
-
A new truck coming my way, a 1943 Morris Commercial C8 GS,
Danny P replied to svdwal's topic in MV Chatter
Sjoerd, Congratulations becoming a father and congratulations on your new British baby! Building a truck and building a family, a tough job. I wish you a good future for your family and good luck with the truck. Danny -
Hello John, Could you please check the width of the hatch for me; you mentioned 15" or 19"? Thanks mate!
-
Thank you John, no worries! I think I will have to go back to him once again unless someone else will respond to my question this evening!
-
Hi John, Tomorrow evening I'm going to someone who is going to cut some iron plates for me. Going through my list I realize that I have no measurements at all of the tailboard step plates as shown on your picture below. Would it be possible to send me the measurements TONIGHT????:blush: I would be very grateful but I understand if it does not succeed!
-
restoration Bedford MW restoration project 2012/2013
Danny P replied to Danny P's topic in Blogs of MV restorations
Hi Louis, Here is a drawing of the towing yoke spring plate: It is not a rectangular plate as you can see from the measurements. The bending starts from the yoke at about 1.5 inches. Sizes may differ a little at your truck but most important is that the pin will fit at the end. Hope the drawing is clear to you! Regards, Danny -
restoration Bedford MW restoration project 2012/2013
Danny P replied to Danny P's topic in Blogs of MV restorations
Thanks, Ginours! When I started the restoration in 2011 my goal was Normandy 2014. Unfortunately it looks more and more that I have to skip that and focus on 2019:cry:. My full time job:undecided:, my wife :wow:, two young children :kissoncheek:and rebuilding the house :-(are taking (too) much time. I am now planning to use the night hours instead of sleeping:yawn:. Damned, why has a day only 24 hours? :argh::argh::argh: -
restoration Bedford MW restoration project 2012/2013
Danny P replied to Danny P's topic in Blogs of MV restorations
After a long time once again an update of my bedford MW restoration project! Drive shaft mounted and sprayed Some details of the Frame work finished Towing cross tube sand blasted and primed, new spring and pin fitted. Made a copy of the petrol tank chains securing the tow pin. Ties mounted and everything finished in olive drab. Now I'm preparing for the body; seems like a fun job for the winter period -
Is this the one Maurice has bought?
-
Thanks a lot John, appreciate your help!
-
How interesting, I learn more and more! I wonder, that steel cable in the WOT2 mudflap in my first picture, is that your 1/8" bar John? In other words, is it left behind in the mudflap because of the folding production? I suppose this steel cable or, as you wish, this 1/8 bar would then also be present in the Bedford mudflap or is it empty inside? It is my last question John!
-
Thanks to you all for the information! Woa2 you must be right, they must be from a WOT2 looking at some pictures on the internet. Here's one: You can see that the end of the Y-shape iron is closer to the edge of the flap compared to a bedford MW. Also the roundings are larger (I measured about 2 3/4" radius at mine) Here's one of a bedford MW: You can see the smaller radius John is referring to (1 1/2") and the end of the Y-shape iron. There remain two questions: • In the above picture it looks to me that the width of the bent edge is more than 1/8" John was mentioning. I measured about 3/8" on the WOT2 flap which, to me, looks simular on the bedford picture above • how about the other side of the bedford MW mud guard? Is it completely flat or is there a thickening visible from the bent edge like the WOT2 flap as shown below?
-
Guy, thank you for the offer! I will first need to know some other dimensions, hopefully from John. I will send you a PM as soon as I have all the dimensions. John, would it be possible to do a measurement at your mud guards? I didn't at Maurices last week as I wasn't aware of the incorrect mud guards on mine. I would like to know the following dimensions (1-4) demonstrating in the sketch below. The intention of number three is the beginning of the rounding. And the thickness of the plate of coarse! How does the edge look like? Is it bent to both sides of the flap? The incorrect mud flap I have is bent to both sides of the flap? It is a rounding which can be seen on both sides. Is the bent edge on the MW the same as the QL?
-
Now things are becomming clear to me! I have posted many questions about the construction of the frame work and wheel arch thinking they were not right but now I see it is because of the mud flaps. If somebody would like to have my mud flaps for the right vehicle then I would like to exchange them for the wider bedford MWD mud flaps! An other option could be that someone could offer me four bedford MWD mud flaps. Thanks John
-
The mud flaps on my bedford MWD seem to have strange dimensions. They are approximately 12 inch wide (30.5 cm) and 15 3/4 inch long (40 cm). They look original to me because of the folded edge and steel cable in it. Shouldn't they be wider and what should then be the width? Or were different sizes used on the bedford MWD? Could it be from another vehicle? Detail of the cable into the folded edge (damaged corner)
-
John, Can't open your attached pictures of the bedford at Normandy. Would like to see them! Could you attach again? Good to know that the wooden slats on the inside of the wheel arch are original. I can't tell if the slats on my truck are original. The body has many original parts but I think it also had a rebuild. If I remember correctly the slats on maurices truck are the same except for the ones in the corners which are smaller at my truck. The reason why these are smaller is because of the heavy slotted screws which are going through the top and sides of the wheel arch. I would be happy when maurice would come up with his comments/thoughts about the wheel arch construction accompanied with some pictures of his. I might even call him to have a look because I live close to him.
-
The wheel arch consists of three separate plates; • one covering the top and inner side of the wheel arch which is a 90 degrees angled plate • two smaller plates covering the front and back of the arch. these have a folded edge and are overlapping the angled plate. Rippo's truck differs from mine: • the two smaller plates on my truck are only rectangular plates and do not have the folded edge at the mudguard location • the folded edges of the smaller plates are overlapping the angled plate on the outside of the wheel arch or as you wish the inside of the body/truck • the wood on the iron arch is fixed with wooden slats and screws at the inside of the wheel arch See my picture below (as you can see the wheel arch is up side down on a table I once have spoken with Maurice Donckers about this and he has told me that there should be no folded edge on the smaller plates at the mudguard location. The mudguard itself will cover the beam and they also have a folded edge which will go under the side plates of the wheel arch. He also told me that the smaller side plates sometimes were spot welded with the angled plate. I have also seen the slats on the inside of the arch on Maurice's truck. Maurice, if you read this post, please correct me if I'm wrong! Maybe you can explain to us? John, I wonder how your wheelarch is constructed, having no slats on the inside of the wheel arch?
-
It was about this picture but going through the whole thread I think I can leave them sq nuts, right?:blush:
-
Hi John, Below some pictures from the tailboard. The coach bolts are supported by three plates. Two outer plates are having one little whole each at the inside top and the plate in the centre has two little wholes at the top. What are they for? You can also see the tailboard side cappings which I believe is fitted with the later bodies (year???) Subsequently the sq nuts would be correct on the tailboard because of these side cappings? The step plates are fitted with sq nuts. The plates next to the steps, are they correct? Tailboard Next the insides of the side boards and floor board I now see there are some modern hex nuts on the floor angles. I have plenty of sq nuts in stock, should I replace them with the sq nuts or should they all be hex inside the body??? How exactly did you copy the hex nuts? The eye plate for the chain is fitted with coach bolts which do not fit. The heads protrudes from the eye plate. The other bolts below are countersunk which you were mentioning and are correct then. John, many questions you can read. I would really appreciate if you can answer them now we are on the subject? Please also remember my first question in the thread accompanied with that first picture! Regards, Danny
-
John, That's a very interesting story! I think we always like to follow a logical reasoning but often encounter the opposite. I have a mix of hex and sq nuts all over the outside of the truck but I believe some wood has ever been replaced. On the sides there are more hex nuts on the upper (drop down) part of the hinges rather then on the bottom fixed part. All of the hex nuts on my truck are the big ones you mentioned. The tail board has more sq nuts rather then hex and there are some bolts oversized. If I'm right, the tail board of Maurice truck has all sq nuts. I think I will try to follow your scheme when rebuilding the body, if I have at least enough hex. nuts :undecided: and maybe I will use all sq nuts on the tail board when I have a shortage of hex nuts or like to follow Maurice truck. Summarized in a way a mix would be permitted for my late war dated truck, if I have understood correctly. Just one question John, how about your front iron angles and front angle reinforcement on the front board inside of the body, not inside the cab? Just like my first picture in this thread?