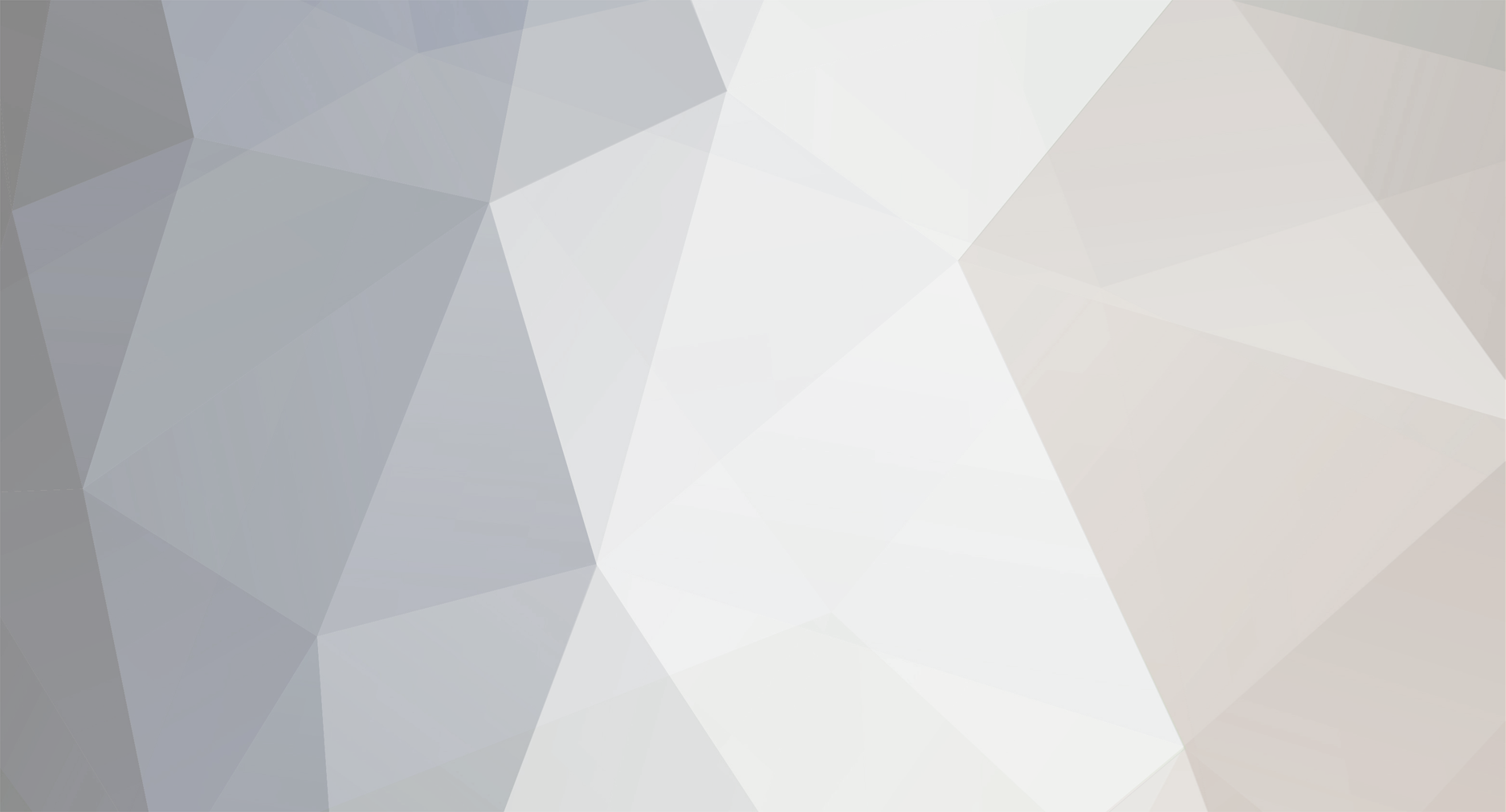
Doc
-
Posts
243 -
Joined
-
Last visited
-
Days Won
6
Content Type
Profiles
Forums
Gallery
Blogs
Events
Articles
Store
Downloads
Posts posted by Doc
-
-
-
For many restoration projects it's the small details that make a big difference; the Leyland workshop certainly falls into this category.
David is very fortunate to have an original Austinlite switchboard but this is missing five out of seven fuses. Back in early March I sourced some Tufnol tube to make replacements however this didn't arrive in Bristol until long after I had scarpered.
Now things are back to a version of normality that if not normal is becoming scarily familiar, I've found a few spare moments to start fuse making.
"A picture speaks a thousand words" they say. So to spare my writing and your reading, here's a selection of photos depicting the process:
Parting off tubes
turning the shoulders
drilling out the bore
harvesting blanks
turning the outside diameter
drilling out the clearance holes
breaking sharp edges. We'll not say too much about that...
assembled (with a dab of superglue for good measure)
with an original for comparison. I have a length of brass square to make the end connection blocks. There's several hours work ahead of me. I'll keep you posted.
-
8
-
-
Work - life balance is still all out of kilter but I'm managing to get a few odd jobs done once again. I ordered some mild steel blanks to make new exhaust flanges. When these arrived Jon volunteered to do the machining. Well, what could I say, other than "thanks".
The thin flanges bolt onto the silencer end plates (with the bolt heads on the inside). The shouldered flanges are brazed onto the exhaust pipe. The flange pairs are retained with nuts and spring washers.
Somewhere down the line a communication mix-up resulted in the shouldered flanges getting 3/8"bsf threaded holes and the mating flanges clearance holes.
I considered putting them all in a bag and giving them a good shake, see if that would solve the problem. With no Debbie McGee on hand, I settled on a more sensible approach:
Fortunately the "extra" holes will not be visible.
-
3
-
-
-
If one day was much the same as another during lock-down in rural East Anglia, it's fair to say not much has changed upon my return to the big city save for my being unable to nip into the workshop to tinker with the Karrier. Basically, if it's a dry day I'm attending to the previous 4 months of neglect in the garden, if it's a wet day my efforts are expended indoors where I wasn't exactly houseproud before I left.
Here's the first of an occasional series of posts filling in some of the gaps that didn't make it at the time, in this case May 2020.
The Tylor engine fitted to the Karrier is rated at 50 HP at 1000 rpm. The 5 inch bore x 6 inch stroke engine is a bit of a lump, fortunately the makers fitted a half compression device to aid cranking. Through the action of a lever on the outside of the timing case the camshaft can be translated length-ways bringing into action a second set of cams that hold the exhaust valves open, releasing some of the charge.
After 40 odd years of standing it was not clear whether this was working or if some part of the mechanism was stuck. While the radiator was out of the way I took the opportunity to investigate.
First to be removed - the retaining bolt and washer.
Followed by the starting dog
the fan pulley
This distance piece
Followed by the timing cover.
and the oil thrower.
The steel pin on the camshaft axis was sliding freely - a good start.
With the timing case removed, I hastily replaced all the loose bits back on the end of the crank-shaft, lest they get knocked over. Having removed the split pin and castle nut from the end of the camshaft I fashioned a rudimentary puller from steel plate.
Very little effort was required to persuade the timing gear to move.
Revealing this large spring.
And the drive dog to the cross shaft gear behind. These were also removed inspected and replaced. Oily hands precluded photography, so I will describe. The gear that drives the cross shaft "magneto spiral" in Tylor nomenclature rotates freely on the outer surface of the front camshaft bearing. The part keyed to the camshaft with the dogs across the front face engages with a similar feature milled across the back face of the timing gear. These two parts butt up hard against each other and a shoulder on the end of the camshaft. There are also dogs projecting to the rear that engage with the "magneto spiral". The large coil spring is positioned between the two gears. Nothing appeared out of order so everything was reassembled. In a moment of clarity I realised that the camshaft would only move when the auxiliary cams were not in line with the tappets. Setting the crank to top dead centre (based on timing marks on the flywheel rim) and a stout pull on the lever and the camshaft moved as required. Turning the engine via the crank handle the camshaft returned against the internal spring. So all appears to be working as it should.
If that's still a little hazy, I've included the appropriate illustration from my photocopy spare parts book along with drawings of the Tylor engine from"The Automobile Engineer"
-
3
-
-
Rightly or wrongly, after twenty weeks away, I took the decision to return to Bristol. I will have plenty to do taming the wilderness that was once my back garden, but lorry work will be on hold for a while. So I'll share the last few jobs undertaken immediately prior to my departure with occasional posts of things that didn't quite make it to the blog at the time.
First up, big thanks to Jon for sending me a box of goodies, including a ferrule to repair the exhaust pipe. Using a Jubilee clip as a guide, I first cut the rotten end off then drove in the ferrule until the shoulder came up against the end of the pipe.
Next step was to weld the two parts together (thanks, Gerald).
Followed by a bit of fettling and a dab of paint (most of which will be burned off when the new flange is silver-soldered on).
Also in the box were a few bits and pieces from my toolbox at work; 1/8" BSP taps and dies along with a cunning little adapter I made for my die stock. There's a set of bushes in a range of diameters to keep the die running true over a long distance.
I've had 3/8" heavy wall steel tube (the nearest one can get to 1/8" pipe in the UK) and a selection of malleable iron fittings in stock for a while now. The arrival of this tooling allowed me to make a start on the acetylene pipework for the headlights.
The tube cutter does a neat job but is inclined to raise a burr on the end of the tube. This needed to be ground off before attempting to cut the thread.
That's the first thread cut. (perhaps if my workbench wasn't such a mess the auto-focus might have selected the item of interest!)
The completed front section that sits under the radiator bottom tank and feeds the headlights. There's a long length from the Tee in the right-hand leg that connects to the acetylene generator. I'm waiting until the bulkhead is in place before cutting this piece to length.
The drain tap is shown in the parts list. Presumably there's some moisture carry-over / condensation when preparing acetylene from calcium carbide. I still need to make the hose barbs and source some rubber tubing to connect to the lamps.
Into the paint shop and a coat of red oxide primer. That should keep the rust at bay until I get back.
-
3
-
-
-
Seems I might have to take a trip to Huddersfield and do some exploring when things are back to normal. Thanks for sharing the photograph and map locations.
Shed roof repairs have taken up a lot of time this week, however I've still managed to get a few jobs done. As I sit down with a cuppa, I'll share some of these.
Earlier in the week I spoke to an ever-so-helpful lady at Hayley Bearings about vee belts. She informed me that B51 was a 17 mm wide belt, 51 inches long. Yes they had some in stock, but only endless belts, not link belt. I had read that the Karrier was originally fitted with a link belt, possibly of the Whittle type with alternate leather and steel links. Onto our favourite online auction site, and new unused B - profile Brammer link belting was available; two metres arrived a few days after placing the order.
Fan parts have been dismantled, cleaned and repainted. The water pipe between the pump and the front of the cylinders and the governor assembly have received similar treatment, as has the starting dog and fan drive pulley.
Incidentally, if anyone else finds themselves having to dismantle a Tylor JB4 engine, the large bolt in the end of the crankshaft is Right Hand threaded.
This job would have been easier had I decided to tackle it before I re-fitted the radiator. Live and learn.
Guide studs re-fitted
Followed by the belt tensioner
And the spring
Followed by the fan unit. The spring adjustment and its lock nut are just visible below the greaser on the side of the bracket.
Fan belt fitted. You need strong thumbs to join up Brammer belts. Incidentally, the link pitch is 7/8" which does not "go" into 51. 51 x 8/7 = 58.3 Next number of links would have been 59, which to my eye is not just odd, but prime into the bargain. I used 60 links and it looks fine.
Governor housing freshened up. I need to find a replacement Rotherhams oiler with the flip top intact.
And the governor link arm. I need to make the rod connecting from this to the throttle butterfly, but need to consult the spare parts list to get this right.
-
2
-
-
It seems that the government are encouraging us to spend our way out of the covid - induced financial crisis; I am doing my bit... sheltered safe from harm behind my computer screen! Mask free. These beauties arrived in the post today:
(All of these images are in the same orientation on my computer. Any suggestions how / why this blog editor rotates them gratefully received)
And alongside the motley selection they are to replace:
Don't they look nice!
-
5
-
-
Another week behind us; time for a quick update. We enjoyed the company of visitors this weekend. Most welcome as we emerge from these strange times. Actually shook hands prior to their departure which was my first physical contact with a fellow human being since before lock-down. That said, I did wash my hands with soap and water afterwards, at my earliest convenience.
So there have been a few tidying up jobs done this week.
Advance and retard linkage and throttle linkage, prepped and painted, ready to go back on. The short link with the brass ends is not original, but did yield two 1/4"BSF single chamfer nuts.
For comparison, as rummaged from the tea chests, freed off and loose fitted to see where things belonged.
One original ball-joint from the advance and retard link between the magneto and the bottom bell crank and a modern replacement. Not identical, but pretty close.
Meanwhile, on the near side, valve chest covers re-fitted and looking magnificent.
I also took the opportunity to replace the 1/2"UNF bolts and nylock nuts on the near-side engine mounts with something a bit more in keeping.
One at a time...
-
3
-
-
6 hours ago, andypugh said:
If time is more important than money, RS components hold a surprisingly large selection of gland packings:
That's worth knowing. Thank you. It's not on the critical path; I can wait on this occasion.
Andy
-
Dave,
That's very kind of you. I'll have a measure up later and PM you the dimensions.
Thanks,
Andy.
-
Last night, when I came to write the latest update, I realised I didn't have all the photographs I needed. So I just popped out into the workshop to remedy the situation. (I may be working from home, but I'm still entitled to a tea-break.) This week has seen the various nuts and bolts work their way up to gloss. Also I have freshened up the cylinder blocks. Finally, have re-fitted some of the shiny bits...
Fuel filter. As received, the stop-tap had rusted off to a point projecting just beyond the gland nut. I took this to work and drilled out the remains, re-cut the internal thread and turned a new needle, handle and packing washers, before assembling and soldering it all together. Still require packing material for the gland.
Repairs to the original head-light brackets.
Ready for trial fitting.
Headlamps were a bit of a fiddle to get on, but really change the appearance.
Cylinder blocks after a lick of paint.
I've had these in stock for a while now. Finally time to use a couple of them.
Rather magnificent brass inlet manifold containing the governor-controlled throttle.
Steadying bracket bolted to the side of the sump.
And almost hidden from view the Claudel Hobson carburettor.
(OK - tea break took a little longer than planned)
-
2
-
-
OK, if you felt a little cheated by the last post, this one has more substance to it. General topic: getting stuff off the floor and back on the lorry.
I needed a small quantity of 5/16" BSF single chamfer nuts. There's a bag of them on the kitchen table in Bristol, but they're not much use to me there. Strangely, in my haste to get back before the lock-down all those weeks ago, they were not top of my list. I don't currently have access to a lathe either. I remembered that I had a quantity of BS 190 1/4" Whitworth nuts, so set about drilling and re-tapping them 5/16" BSF.
Nut suspended on 1/4"Whit tap and clamped in the vice.
Drilled 17/64"
Tap started in the chuck of the drill
Finished off by hand.
Fruits of my labours: six done, two left to do.
This allowed me to fit the foot-board brackets.
(sorry for the poor quality of this photograph)
Next up was the radiator. Last week I had taken the air line too it and blown out forty years accumulated dust and cobwebs from the core. Next I gave the tube fins a good daub off phosphate conversion coating. This weekend I masked the radiator with tape and newspaper before giving the core two good coats of matt black paint. Once dry and the masking removed, the radiator was lifted onto a table placed in front of the lorry, then from the table onto the mounts. These were lined with 1/16" thick rubber sheeting (perished) so two new linings were cut and fitted prior to mounting the radiator.
With the radiator in place, it was now time for the bull bar and headlamp brackets to be re-fitted.
Parts laid out ready
Bull-bar and brackets fitted (with a little help from David, who also helped lift the radiator)
Some of Trojan's rather beautiful new 1/2"BSF bar-turned bolts
Next the front bonnet support was lifted into place.
and in a small departure from originality was fitted with countersunk screws, nuts and spring washers; originally, this was riveted. The "spare" hole takes the last bifurcated copper rivet for securing the end of the felt.
Felt pegged out of the way while the screws gt painted up to black.
She's starting to look like her old self again now...
-
7
-
-
-
Just popped in the house to study Karrier front mudguard brackets and the heavens have opened. No choir of angels, rather, it is pouring with rain here. So while I'm sat down, I'll give an update on the week's progress. I have the original foot-board brackets, though one is a little tender. So I cut out the offending material with the angle grinder and a slitting disk. Next I fashioned a piece of scrap copper busbar to fit inside before cutting a patch of replacement metal. Thanks to my brother Gerald for the welding.
A bit of fettling with the grinder and it was ready for the paint shop (after re-drilling the bolt hole).
The new valve chest cover has been worked up to black, though I'm not happy with the finish so have sanded it back since this picture was taken and will have another go...
Meanwhile, I have had another go with the front mudguard brackets. These, of course, had to wait until the front wheels were back in place.
Drilling the mounting holes on our ancient pillar drill
Trial fitting and sighting the position of the first bend.
Had to include this picture just for the colours
Welding where the notch had been taken out
Another trial fit. Showed up the first bend was not correct. So this was split, straightened out and the notch filled in.
Looking a lot better now. Position of the final bend being estimated with a thin strip of steel bent to the correct angle and slid along the bracket until the radial distance from the tire matched the front bracket.
Marking out the last notch
More gratuitous pictures of fire - it's a boy thing!
Learned my lesson. Split and notch not welded up in order to leave the bracket malleable.
Trial fitting. Still over-long but looking good. Wish I'd scraped the runs of red oxide primer off the tire before I took the pictures!
And for good measure, I laid one of the new mudguards on for a quick look-see.
Satisfied with the shape the bracket was trimmed to length and the notches filled in. Work on the off side bracket was cut short by the aforementioned heavy shower.
-
3
-
-
9 hours ago, andypugh said:
I love the attention to detail, especially the careful pre-rusting 🙂
Made from an offcut of steel salvaged from under the guillotine.
You may well joke about pre-rusting, but...
The bulkhead is braced by two vertical strips of 3/8" x 2 1/2" steel. The originals had been discarded in favour of new metal in the late 1970's. When I dismantled this some weeks ago I discovered unpainted and nicely rusted metal on the mating faces. I have turned these round so the pitting shows on the exterior faces; looks a whole lot better!
-
Have taken the first two days of my annual leave entitlement. To be fair they were not unlike my recent work days save for not actually having to do any paid work.
A couple of small jobs now ticked off the list:
1) Front bonnet support. This was lined with felt. I have a sample of the original material in a bag, somewhere. I had some off-cuts of 3 mm felt from a work job, which was ideal. This was cut into strips, or to the arch profile, holes punched and riveted into position with nickel-plated bifurcated copper rivets.
2) Valve chest cover.
Having made one good valve chest cover from the rusty remains of the original two, a replica was required. I've been putting this job off for a while now, but decided to make a start yesterday evening. First a piece of steel was cut to width and the two long edges upset to form a shallow U.
We had a "scrap" shaft, 4" diameter, as luck would have it, exactly the same as the bend radius of the valve chest cover. This was converted into a rudimentary bending jig and, after heating the returned edges, the first bend was pulled round with ease.
The second bend required a bit more care to get it in exactly the right place.
Next the ends were cut to length, corners notched out and flanged up.
By way of comparison, alongside the original.
Trial fitting on the engine.
Finally the two spare ears were riveted on. Job done.
-
7
-
-
Sunday evening at the end of week 13 of lock-down (can you believe?!) and time for another update.
It was time for the front wheels to come off the stand and be reunited with their respective stub axles. First the off-side wheel, which had to come up over the top, before being stood out of the way.
Next the near-side wheel was lifted off the stand and manoeuvred to a convenient location.
Off-side wheel was re-fitted first; I was offering the wheel up to the stub axle while David raised or lowered the front of the chassis with the chain blocks.
Next the turn of the near-side wheel. Copious amounts of grease were applied to the stub axle, thrust faces and floating bronze bush before the wheel was slid into place.
Next the front wheel greasers were re-fitted.
Followed by the hub caps.
I'll be on the phone to Trojan Special Fasteners in the morning - the 3/8"BSF x 1 1/4" bolts and nuts used on the hub caps had previously been allocated to the bulkhead buttresses. I'll be needing some more.
I have also sanded the chassis from one end to t'other. I'm hoping to get top coat applied over the next couple of days; I fully expect every fly, gnat, locust, moth and other nameless flying pestilence to descend on my little corner of Suffolk as a consequence.
-
4
-
-
Ben,
Pleased to see you've bought the Coventry Simplex generating set. I was under bidder on it at the Crawford reduction sale last year. Part of me wishes I had persevered, but you can't have everything. Good to know it's gone to a good home.
Andy
-
9 hours ago, EdB said:
Sorry these have taken so long but it's only recently while extracting some hay making equipment that I've had a chance to get anywhere near our old Karrier (or remains of).
I seem to remember there was a query about the prop tube, anyway our chassis still has it fitted, hope pictures are helpful/of interest. Keep up the great work!
Regards. Ed.
Ed,
Many thanks for taking the time to photograph the torque tube details and post them. Brass plate indeed references Spurrier's patent, as I suspected. Any chance you might do a bit of brass rubbing. It would be great to be able to get a replica made for mine.
Regards
Andy
-
I'm now enjoying a well deserved sit down, so, not content to be completely idle, will take the time to post a short update.
Front wheels have been painted up to top-coat green and now need to wait for the paint to harden before I can consider lifting them.
There was a dawning realisation that if I wanted to refit the front axle then the hooks needed to come off and be cleaned up and painted. So these have been playing catch-up alongside the spring hanger links, king pin covers and hubcaps.
Sorry, not the best picture....
Meanwhile, the spring hanging links were loose fitted to the chassis in readiness to receive the front axle
The front axle was manipulated comparatively easily using the high-lift pallet truck. Fitting the front pins was a bit of a fiddle, but we got there in the end.
Offside front pin and hook were first to be fitted
Followed by the nearside (don't the hooks look handsome!)
With the rear pins in place, the truck was lowered and moved out of the way, giving access to prepare and paint the underside of the axle beam and the fork ends of the radius rods.
Note the odd pin with the greaser mounted at right angles. This is to clear the track rod.
Other work this weekend:
The engine was paraffin washed while the front axle was out of the way. Looks much better for it.
Also made the most of the nice weather and shredded a few wire brushes. The angle grinder cup brushes were particularly poor value for money. But the result was that the manifold and exhaust were ready for painting.
Another thing that doesn't seem as good as it once was: aluminium paint. Used to need two hands to stir it; a far cry from the watery stuff that masquerades as paint now. The pictures below were taken after the second coat. Two more will be required, I think.
The tail end of the pipe still needs to be repaired. I have no idea when I'll be able to do this and I didn't want to waste the weather. So this will have to be touched up afterwards.
-
2
-
-
It's that time again. This week's progress has largely been about cleaning and painting front axle parts.
Don't be fooled by the bright sunshine in the first few pictures - these were taken last week but somehow didn't make it into the post.
Near side hub-cap removed.
End of near side stub axle exposed, also eccentric oil groove cut in the end of the hardened steel knave.
Stub axle with flat for grease distribution, also thrust bearing. Note the absence of felt oil seals, compared to the Leyland for example.
Near side front wheel ready for paraffin washing.
And the same again; this time the off side front wheel.
These parts had clearly been sand blasted back in the 70s and with several coats of paint, all that was required was paraffin washing, sanding down and repainting.
Small parts - hub caps, king pin covers, greasers, pins, spring hanging links have also been prepped and painted.
Above and below: first coat red oxide primer.
The ever-so-helpful wheel stand was brought back inside and now supports both front wheels. These are receiving the same treatment.
Getting a bit crowded in the workshop, so the easiest way to manoeuvre the off side front wheel was to lift it clear over the top of the stand...
...before guiding it onto the end of the tube.
Prepped and in first coat oxide. Note the jubilee clips to stop the wheels trying to escape!
-
4
-
-
Good to hear that daughters are getting involved in engineering. Reminded me of the EDF Energy "Pretty Curious" campaign a few years ago now. There's some short videos on YouTube encouraging girls to get interested in STEM subjects.
Karrier WDS
in Pre WW2 vehicles
Posted
An interesting trip back to East Anglia: the first leg of my train journey saw both the guard and the guys pushing the refreshment cart walking the length of the train. Had I partaken of an over-priced can of beer I could have drunk it in a carriage of socially distanced strangers without submitting contact details. The second leg of my journey had no catering and the guard announced she would not be walking through the train "due to the circumstances"; the circumstance presumably being that she couldn't be a**ed. I had a bit of a wait for David to collect me from the station and contemplated popping in the Kings Arms for a pint but would have had to disclose contact details, which I wasn't prepared to do. Don't you just love the inconsistency!
Anyway, I'm back now and have started on a few fiddly jobs on the Karrier.
First, the choke rod threaded 3/16" bsf.
In position, over length.
trimmed to length and threaded, awaiting a knob.
Next, making a start on the governor control rod.
I didn't have enough 5/16"bsf bolts for the fan, but our favourite online auction site obliged. I've cut them to length and filed off all reference to messrs Guest, Keen and Nettlefolds.
A further purchase to receive similar treatment was a batch of 1/4"bsf nuts and bolts which enabled the bonnet catches to be fitted.
There's been a significant change in the weather; it's turned mild so things are a little moist. Once equilibrium has been attained, I'll be going round with the touching up brush to get some paint on the nuts and bolts.