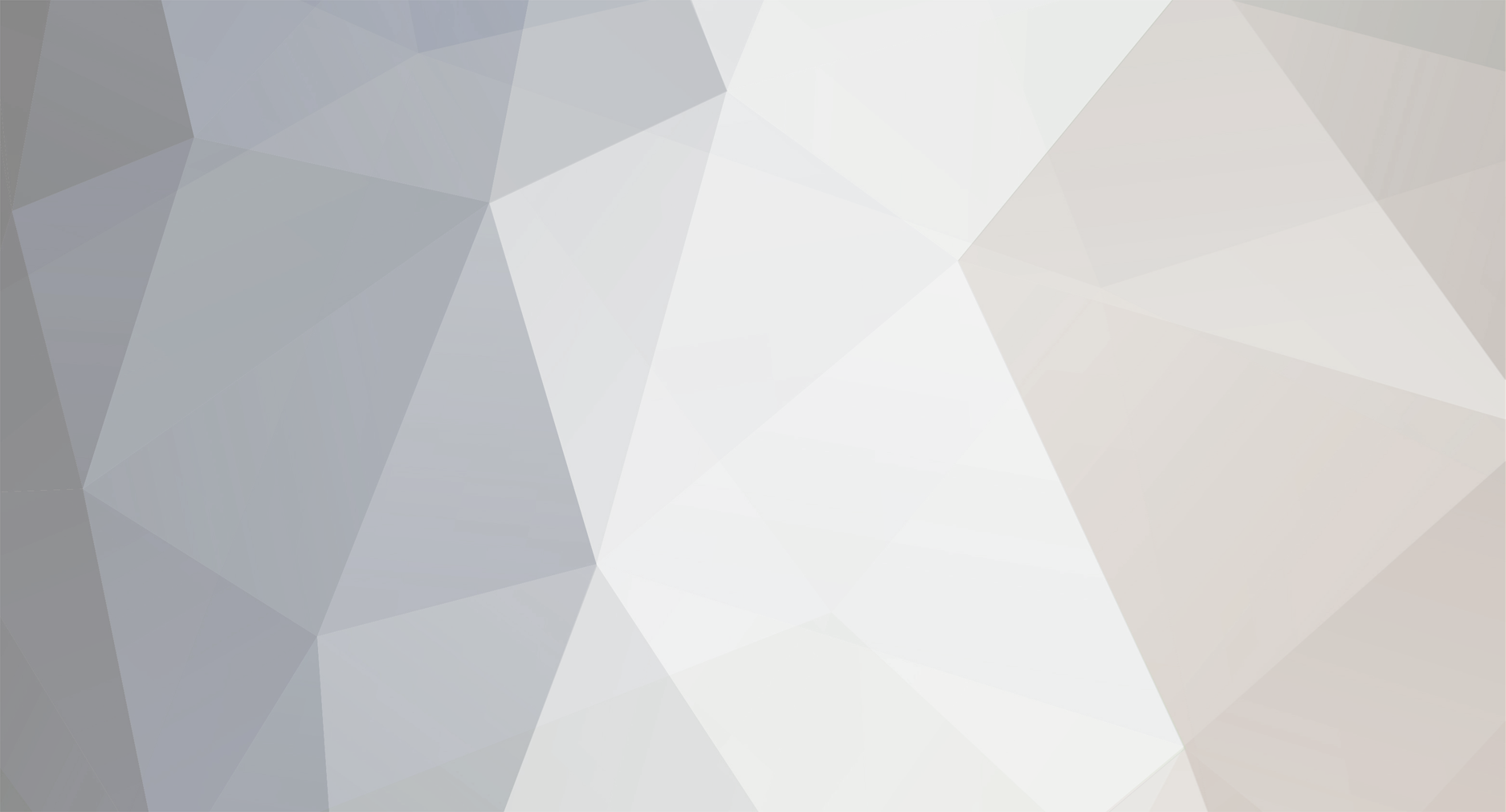
Doc
-
Posts
243 -
Joined
-
Last visited
-
Days Won
6
Content Type
Profiles
Forums
Gallery
Blogs
Events
Articles
Store
Downloads
Posts posted by Doc
-
-
Another week in the workshop fiddling with my small parts. It's lockdown who can blame me?
I'm tempted to ask "Can you tell what it is yet?"
In reality, "they" would be more appropriate.
Hose barb fittings for the gas pipe to the headlights.
Here's the pipe clipped to the front of the bulkhead. Most photos show the acetylene generator on the front of the step.
The governor linkage and choke rod are now fitted.
I've also made one of these...
the missing knob from one of the crankcase doors.
and finally, a bit more progress on the advance and retard linkage.
-
5
-
-
-
I have a theory, born out of experience that if you look forward to something too much, it inevitably disappoints. So if you were expecting another carpentry instalment... sorry. No crane either. But some heavy lifting.
It's now 4th August 2018. Careful measuring had determined that the roof trusses were tall enough for the workshop body to pass comfortably underneath. More careful measurement revealed that the doorway was lower than the roof trusses and it was not going to come out of the shed where we had built it. Well, not on the railway sleepers we had used as a base. So we had to jack the body up - one end at a time - drag the sleepers out and replace them with pieces of 4x2. Then, with inches to spare, slowly... the body was out in the sunshine.
Then over to a flatter part of the yard where there's room to manoeuvre...
Then with the trailer out of the way and the Leyland chassis shunted into place, it was time for the lift.
Note the temporary timbers bracing the structure. These formed the base of our makeshift roof to keep the sun off at Dorset. Kept the rain off too.
The following weekend and it was back out into the fresh air to lift the top panels back on. First, the as yet untouched near-side panel.
Followed by the new rear and off-side panels
There was still a myriad of small tasks to complete, which saw all of engaged in "essential war work". Finally we were ready for Dorset.
200 miles to go...
-
12
-
-
Correct: tongue uppermost, no tongue on top board, no groove on bottom board. No secrecy so far as nails are concerned. Subterfuge, maybe. Nails and screws were all sunk below the surface of the boards and hidden with linseed putty.
Elsewhere (e.g. floorboards, front wall boards) screws were used. So we sourced genuine slotted screws as per the original construction, not one of which will ever be seen!
We rightly consider the carpentry craftsmanship, but it was simply how things were done.
Ian, our builder friend, was able to read the remains of the original joints and know exactly how the thing had been built and why.
-
1
-
-
Hi. Good question. The tongue and groove is nailed to the frame. Nails at the ends of the boards are driven in at an angle.
When I post pictures of the repair of the near-side top panel, this detail may be more visible.
While we're on details, there's a thin wooden strip on the top edge of the rear bottom panel. This was fixed with alternate screws and panel pins, just like the originals on the corresponding side panels.
Doc.
-
1
-
-
2018 Great Dorset Steam Fair my brother was greeted by a fellow WW1 exhibitor (who will remain anonymous) hollering across the showground "I'm envious of your body!" I'm not sure why this should come to mind as I prepare to share photographs of my small parts...
So I've been making parts for the Yorkshire-built lorry on my Yorkshire-built lathe: knob for the choke rod and collars for the governor control rod
Back collar in position with a small tap wrench clamped up snugly behind
then transferred to the milling machine to drill the split pin hole
The mill was not made in Yorkshire. It's actually a 1980 vintage Tos Kurim FNK25A built in Czechoslovakia. The DRO must be a museum piece by now, but it still works.
Back in position to account for the position of the front collar
and the tap wrench to put a little preload on the spring. The position was measured with a Vernier calliper before dismantling and returning to the mill.
well the holes all line up
control rod trimmed to length and a final trial fitting before being removed to the paint shop.
-
4
-
-
Who knew that "beer shaming" was a thing. It's a bit earlier in the day and as I'm sat here contemplating this weeks update, I'm finishing a cup of tea. Comments, criticisms...
Anyhow. I start on 23rd June 2018, GDSF is looming ever closer and there's still loads to do. Woodwork was generally an evening job after Ian had spent all day on the refurbishment of the house; generally speaking, he would set up the morticer and David would chase in the mortices, meanwhile Ian would be cutting the tenons. Between them they would complete the necessary parts.
This first section concerns the upper rear panel. In reality, many components are common to the analogous side panel and were therefore made as a batch. The offside top panel was beyond repair and was thus replaced. Actually, I should clarify that by saying the woodwork was replaced; all the iron fittings are original. Around this time we bought all the remaining stocks of 1/2" Whitworth coach bolts from our local iron mongers, and by the time this project was completed, had got a good way through them.
The completed frame was offered up into the body for a trial fitting, then removed and boarded with 3/8" tongue and groove as per the original.
Then back in place to transcribe the bolt holes for the hinges. Note the steel reinforcing strip on the bottom edge.
Now it was our first attempt at applying canvas. Thanks to Seb Marshall for advice on what to use and where to get it, also such vital advice as "make sure they send it rolled up - if it's folded you'll never get the creases out."
Now some pictures of the construction of the off side top panel:
Note the dowel holes (and no wedges). Only the intermediate timbers had wedges fitted.
So I'll close this instalment with a couple of pictures of the off side top panel in position. Looks much better without the window!
-
7
-
-
It's that time again...
Are you sitting comfortably, then I will begin.
It's now early May, 2018 and time for a trial fitting of the back board and it's new hinges. First the backboard was clamped into place then the hinges fitted on their long pin and clamped up against the backboard, before the holes were drilled through for 1/2" Whitworth coach bolts to secure the hinges in place. One fixing in each hinge forms the pivot for the legs; this is screwed into a nut, rebated into the back board, and the thread peened over to prevent the nut from coming off. Rebates were also cut for two steel catch plates that protect the backboard as it is closed over the securing pins.
I recall staying late at work to make the hinge bolts for this and the upper panel, also the legs. Not done that in a while...
Slightly out of sequence, chronologically, but here's the trial fitting of the hinges for the upper panel.
May 19th: trial assembly of the front wall framing prior to a quick sprint across to the paint shop.
We're now into the last week of May. This was the week before Woolpit Steam. So we've all taken the week off work and are up at the showground from dawn till dark getting everything ready. By rights, the evenings (well from about 9.30pm) would be spent in the pub. Remember when we used to do that? They'll write books about it... Anyway, we voluntarily forewent beer drinking and spent a couple of hours each night on carpentry instead.
With the show out of the way, we were able to dedicate more time to the workshop body and complete the boarding out of the front wall.
As this weeks instalment draws to a close, I'm going to give my full attention to a glass of Shepherd Neame & Co's India Pale Ale.
Doc.
-
5
-
-
Hi. I looked back over the post and realised that this is turning into one of those authentication tests "tick every box with a wheel in it"
The wheel in the background of the picture titled "old and new" is IHC 12-25 Mogul.
But in the second of this week's pictures there is a Saunderson on the left. This is a work in progress and the project that was paused when the Leyland came along.
Doc
-
It's now 22nd April or at least it was when this next back of pictures was taken, detailing the trial fitting of the bow ends. This really felt like progress as they gave a tangible impression of the finished form. The majority of the iron brackets are originals.
Note: the top fastenings form part of the hinges but as a temporary measure 5/8" bolts were used. The lower ends were secured with square head 3/8" coach screws. David scoured our favourite on-line auction site to find enough to complete the job. After this trial fitting, the frame was dismantled and off to the painting shop.
Only these light iron corner straps at the front as it is boarded from top to bottom. Here's the remains of the original:
And the new boards in primer. The paint shop was full; this is actually David's living room! As I mentioned in a previous post, we had the builders in...
The rear end panels are long gone - these were discarded when the body was converted into a shepherds hut, so have had to be constructed from scratch.
Basic shape of the tailboard section
New laser-cut hinge blank alongside an original from one of the lower side panels.
Old and new...
Forming the hinge.
Sorry, no crane pictures again this week. Will fire do instead? I like fire.
-
5
-
-
Karrier progress has been slow of late. On account of my extended period away from work I've not had access to the machine shop. The last few weeks have been spent commissioning my own workshop. First machine to see action is my Dean Smith and Grace lathe. This would have been scarcely five years old when the Karrier was recovered in 1977; it's still got plenty of years left in it. A very different machine to the Harrison M300 I'm used to, it has to be said.
I repurposed an old copper drift, turning it into a mandrel to support the broken steering ball joint so it could be welded back together.
Thanks to my brother Gerald for doing the welding.
So now I was able to complete the fitting of the drag link.
Another small job crossed off the list.
-
2
-
-
-
This weeks instalment starts on 1st April 2018. Pinch, punch, first of the month and no returns. Now that's out of the way...
At the same time as we were rebuilding the workshop body, the house was also undergoing a thorough going-over. Our builder, Ian, has a fully equipped carpentry shop and after a full day at the house would think nothing of giving up his evening to oversee the complicated joinery required for a faithful recreation of the workshop body.
The corner posts are tenoned into the frame; these joints are reinforced with iron straps. We re-fitted the bottom side panels so as to ensure that posts were correctly aligned.
I mentioned in a previous post that the it was not possible to read the joint design on the top of the posts. Fortunately the body at Duxford has a roof plank missing, so this joint is exposed. The curatorial staff there, whose praises I will sing at every opportunity, allowed us to bring a step ladder into the museum so we could inspect, photograph and measure this joint.
April 9th and the frame was starting to take shape. It needed to as not only was the GDSF getting ever closer but Woolpit Steam was looming too. Anyone who has been involved in the organisation of an event of this type knows how all-consuming it can be.
David considers it a grave sin to have an empty paint shop so while the framing was undeway the original timber support for the pillar drill was repaired and prepared for painting.
Sorry, no crane shots this week or indeed for the foreseeable future.
Doc.
-
5
-
-
It's that time again. This week's update is from 30th March 2018. The workshop body had been built up to floor level on the Leyland chassis but the shed in which it was being built was not tall enough to accommodate the full height of the vehicle so we had a bit of a move around. First the Leyland was towed out of the shed and steered into position under the crane - that object of envy.
Next the body was lifted up into the gods and spun through 90 degrees (so the iron brackets would clear the beam of the crane) allowing the Leyland to be towed out and shunted out of the way. Afterwards an old seed drill transport trailer (a farm-sale purchase that looked like it would come in useful one day) was backed into place ready to receive the workshop body. This, being much lower to the ground, was then returned to the original shed for the build to continue.
The trailer was let down onto blocks and shimmed to get the bed level so we could use a spirit level in the subsequent construction.
Photographs below should be self-explanatory.
And now a sneaky peek at next week's instalment:
-
6
-
-
The originals were tongue and groove; we've replaced like for like.
Doc.
-
1
-
-
There's snow on the ground this first weekend in February. This week in 2018 saw the floor starting to come together. The bearers had taken their turn in the paint shop and were soon reunited with the chassis. Meanwhile, replica angle iron brackets had been made based on the Duxford examples.
The tenons and mortices had been cut in the sill beams, marking the start of the structure of the body. These were trial fitted on the bearers then the bolt holes drilled in-situ and rebated out to receive these rather curious square headed bolts. A full set of 10 bolts had been made; several were rusted through and one was badly bent. Turns out the bent one was on account of the hole having been drilled too close to the floorboards - the rebate would have broken through the side of the sill beam. So this old bent bolt has been re-used. Whoever it was that succeeded in hiding their shoddy workmanship for 100 years... you've been found out!
With the sill beams defining the footprint of the body we were now able to fit the new floor. 1⅛" Douglas fir.
Once it was all assembled it was time to take it apart again and cart it, piece by piece, across to the painting shed - heated I should ad - as by now we were in the grips of "The Beast from the East" (no, not Matty Hancock). Once the paint was dry, the return journey was made across the yard and final assembly commenced.
No sneaky peek again this time; there's little else to look forward to at the moment.
Doc.
-
8
-
-
Part Three. January 2018. (34 weeks to go before Great Dorset Steam Fair).
The cross bearers were a bit rotten on top and to a greater or lesser extent on their ends but are big heavy timbers 8" x 2 ¾" so the decision was taken to repair rather than replace. There's a theme that permeates this little corner of cyberspace "old = good, new = bad" This does not apply to circular saw blades; modern blades will cut through anything! So the rusty remains of nails and screws posed no problem.
New pieces of ash were glued and screwed to the top faces.
The front bearer was the roughest by far and beyond repair, but this yielded sufficient timber to repair the others as the following photographs will demonstrate.
Small repairs were made where bolts had rusted and split out the ends of the timbers.
With all the repairs completed and a replica front bearer made it was time for a trial fitting.
This final photograph takes us to February 2nd (30 weeks to go) and the bearers are in the paint shop. The hawk-eyed among you will have noticed that this workshop was originally blue - RAF but the base colour on the lorry chassis was olive drab. So an executive decision was taken to paint the workshop olive drab to match.
No sneaky peeks this time...
-
5
-
-
-
Yes, that looks like the same building, though the terrace of houses has been lost, along with the factory building in the near distance.
As soon as Boris says it's ok, I think I need to take a train ride to Huddersfield and do some exploring.
All very interesting...
-
If the building could be protected I would say "Not before time." We've lost too much evidence of our engineering prowess as a nation already. So where is this building in relation to this one:
(can no longer remember the origins of this photograph - I likely found it on Google - reproduced for research/educational purposes)
I thought I had seen a picture of the stones from the Karrier Motors frieze on the ground. Is this a different building? Does it still stand? Please excuse my ignorance.
Thanks
Andy
-
The last instalment of this tale left the workshop body reduced to floor level, surrounded by a plethora of decaying timbers. Today I'll describe the start of the reconstruction. We have tried to salvage as much of the original timber as possible. As built, the workshop body sat on two steel plate reinforced longitudinal timbers, 2½" x 6" x 12' 4" long. After a lot of ringing around we managed to find a sawmill that could supply these and our other requirements in English ash as originally used. The first job was to make these fit onto the chassis, boring clearance holes at regular intervals corresponding with the various protruding bolts and rivets.
With these in position on the chassis, the original floor was carefully lifted into place in order to mark the positions of the cross members.
With everything marked the old floor was lifted back onto the Vulcan chassis and dismantled.
Floorboards were numbered and layed out as a floor once more so we could account for all the bolt holes - evidence of machinery placement.
The steel reinforcing plates were bolted into position with a mixture of 3/8" and 1/2" coach bolts and BS190 nuts. The curatorial staff at Duxford were very accommodating in allowing us to measure and photograph these details on their workshop body so we could get everything "just so".
And now a sneaky peek at next week's topic:
-
8
-
-
Glad you're enjoying the post. I'll have my curator's hat on again later this evening, sorting through the next batch of photographs to accompany a 2nd instalment.
-
I don't know how people are feeling right now, not able to get out and about. So with time on my hands and to help keep peoples spirits up, I have decided to share some pictures of the restoration of David's workshop body.
This first batch of photographs documents the dismantling of the remains.
These first two photographs show the body arriving home July 2017. We had spent a day on site bracing the structure to make it fit for the journey. The tarpaulin was an added precaution; we didn't want to risk pieces of rotten timber being blown off, especially on the motorway.
As evidence of the fragile nature of the body, this is the near-side rear corner. The timber in the left of the picture running backwards is the top of the upper panel; the top rail of the body has almost entirely rotten away.
And here it is again, from the other direction.
Dismantling proceeded almost immediately. Ratchet straps were thin enough to be worried in behind the hinge pins. The travelling crane (the object of crane - envy amongst some regulars on this forum) was particularly useful.
Near-side top panel removed in-tact.
Off-side top panel was much more fragile and had been fitted with a window when re-purposed as a shepherd's hut.
With the top panel safely on the floor, the hole for the stove-pipe in the lower panel can be seen.
Off-side top rail has survived comparatively well - a useful pattern.
The front wall comprised a mixture of original and replacement timbers.
During the dismantling process we were at pains to record and preserve the various carpentry joints used in the original construction.
Above, the off-side rear corner joint exposed. This was strengthened with an iron brace which had fallen off. Fortunately this had been gathered up and placed inside the body.
Floor-level joints have survived comparatively in-tact, however the post tops have not fared so well.
This is a replacement post; all joint details have been destroyed.
I'll end this segment with a teaser:
-
9
-
-
On 1/11/2021 at 9:08 AM, Scrunt & Farthing said:
Looks very smart. David must be very pleased with it.
Dave
You're quite correct; he's pretty chuffed with the drill.
I found this advert today.
(was landscape when I took the picture)
If anyone knows the whereabouts of one he would be thrilled to hear about it.
For more details, there's pictures of the Duxford workshop body earlier in this post.
Doc.
RAF Leyland workshop lorry
in Pre WW2 vehicles
Posted
Evenin' all. Sorry no post last week. Was busy with other things... So we had our week in the sunshine at Dorset; rain too but we stayed dry under the temporary roof. At least it didn't snow, unlike here. Yes, it snowed in our little corner of Suffolk this Easter Monday morning.
So having returned from Dorset, with "I'm envious of your body" still ringing in his ears, David proceeded to remove the near side top panel for repair. The following photographs chronicle the process.
This is the bottom rail, feeling a little fragile and sorry for itself.
The top rail was basically intact but did have a section of rot in the middle.
To repair the bottom rail first the damaged timber was cut away
And a repair piece cut to fit
Along with a false tenon that was lap jointed to the original timber
And the whole lot glued and clamped together. While the glue was setting, attention turned to the top rail...
Out with the rotten. (If only we could do that right now. Matty Hancock... Just saying...)
In with the new
Glue and clamps. Repair patches were cut over size and planed to finished size once the glue had set.
We ummed and arrghed over the tongue and groove before deciding, reluctantly, that it was too far gone. Rest assured the replacements are exactly as the originals.
To support the repaired sections, we had these reinforcing plates laser cut from 6mm steel. They're clearly not original but they allow people to "read" the repair. We're actually rather pleased with them in that respect. They point to the originality of the underlying structure but say "it wasn't really strong enough, but we elected to keep it anyway." Any of us feeling a bit fragile in these difficult times could hope and wish for the same.
Doc