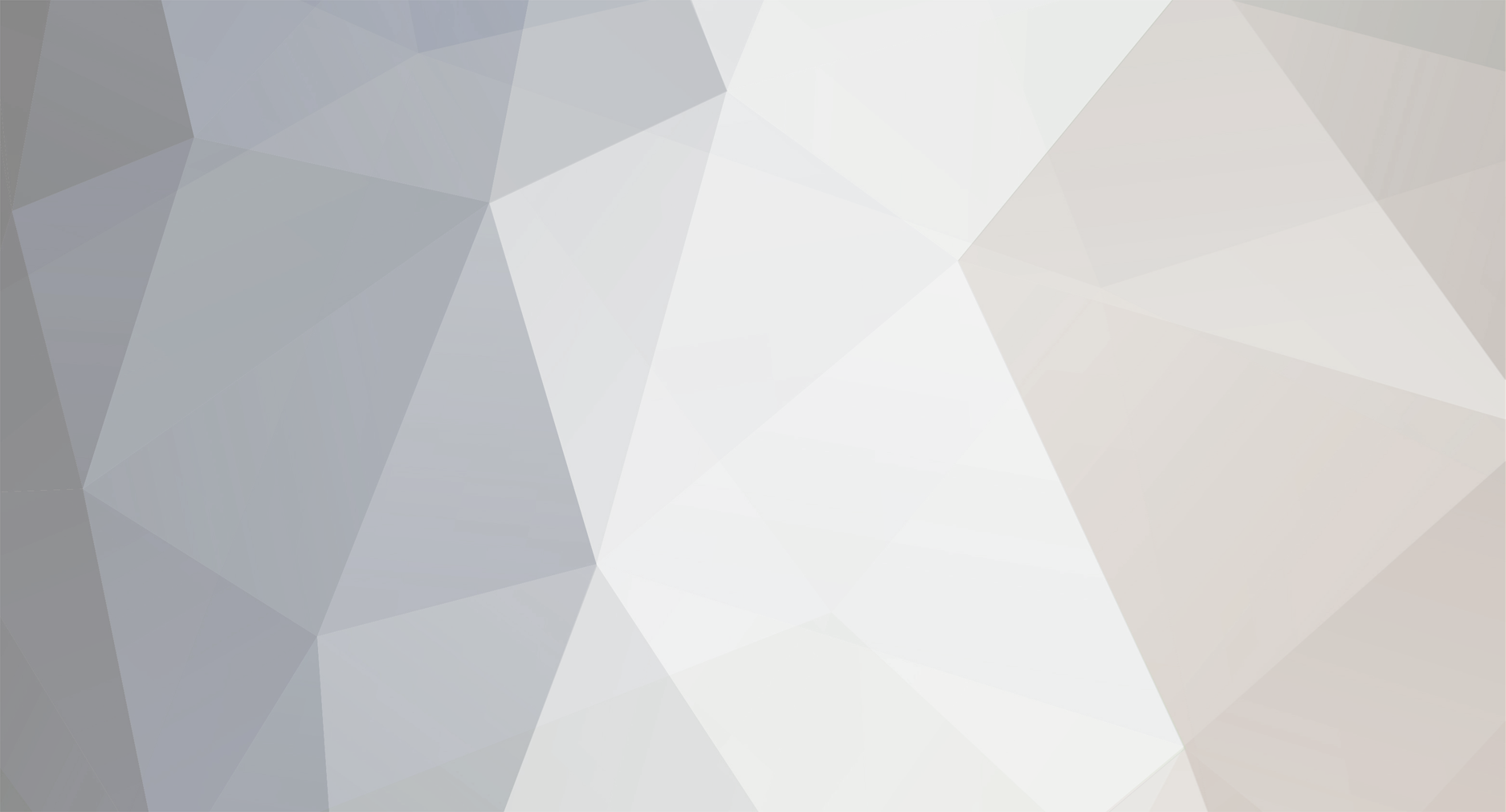
Doc
-
Posts
243 -
Joined
-
Last visited
-
Days Won
6
Content Type
Profiles
Forums
Gallery
Blogs
Events
Articles
Store
Downloads
Posts posted by Doc
-
-
My brief to Suffolk is now at an end but not before refitting the petrol tank.
I'm still in two minds about the orientation. This is the position it was in when I received the lorry but period images show it mounted differently.
It will just squeeze on this way round but the tank is only partly seated on the near side saddle with the strap hard up on the seam.
Perhaps this reproduction tank is a little short or maybe in civilian use the tank was mounted differently.
One of the last jobs was to sand off and topcoat the front mudguards. Mercifully it's not flying insect suicide season in our corner of Suffolk.
-
4
-
-
Last summer, inspired by various posts on this forum, I thought that I would have a go at cleaning out the Karrier petrol tank. Molasses were bought from the local country store and diluted down. The wasps were fascinated by the whole affair. After several weeks in the tank, which was periodically rolled from side to side, the festering brew was drained into pails. It's true to say that I was less than impressed with the results.
Another forum regular (Mr Pittock) had mentioned having tanks acid washed so I thought I would give that a go. The tank was delivered at the beginning of June (just before I returned to Bristol) and was ready for collection by the middle of July. I had said that I wasn't in any particular hurry for it. Well, what a transformation!
So I'm back in Suffolk for a few days and have sealed the inside of the tank with "slosh". My godfathers, that's got expensive! But now the eco warriors are adulterating our petrol with ethanol, you can't be too careful.
After it's little adventure the tank was not looking its best, so a bit of a sand and a repaint was required.
Meanwhile, at the other end of the paint shop:
Leyland bonnet. I didn't know David could move so quickly as when I pointed the camera in his direction.
In other news I've refitted the front mudguards and started painting the top surfaces.
-
8
-
-
Hi Pierre,
I've had a chat with my brother. He used Gorilla glue. There were some screws were the timber was thick enough to take them. The joint was cut to give maximum glues surface while retaining as much of the original timber as possible. That and he's far more comfortable working in metal than wood. He commented that the two bolt-holes visible in the picture are for an angle-iron bracket which spans the joint, adding strength. Were this not the case he says he would have cut a notch across the joint.
I hope this makes sense. Good luck with your project.
Andy (Doc)
-
Tomo,
No worries. Does no harm to be cautious. Though in reality there was no "added value" as I bid less than £10 (though would have been prepared to pay more).
Steve,
Thanks for sharing the pictures of your H&B horn. Details such as the rib behind the rolled edge look identical.
Doc
-
1
-
-
Hi. Not posted anything for a while as I've been back in the big city, far away from the Karrier.
Sat at my kitchen table, working from home, mask free, there was a knock at the door. Royal Mail delivering this shiny piece of loveliness (courtesy of our favourite online auction site):
Hopefully I'll soon be able to return to Suffolk and see about fitting this in place of the Lucas horn.
Need a replacement bulb of course but I pursed my lips and gave it a blow; a pleasingly resonant tone was produced.
Doc.
-
4
-
-
12 hours ago, Scrunt & Farthing said:
Mungo Jerry lyrics, you can live your life by them!
Glad you liked them. The Karrier was still languishing in the raspberry patch when Mungo Jerry were enjoying their chart success.
Tis true, some of the lyrics don't stand up to the scrutiny of this modern age... But I hung the mudguard brackets outside in the sunshine to harden off between coats and the tune popped into my head.
-
1
-
-
-
My company were not so generous. "Use it or lose it" they said. I did not need telling twice!
-
1
-
-
Woolpit Steam was sacrificed at the altar of the new world religion again this year. My apostasy aside, I have gained an extra week of holiday to spend on my own projects.
This week's task: mudguard fitting.
Having satisfied myself with the positioning, I first marked and drilled the front holes before bolting the mudguard in place.
Then, with the aid of my wooden prop, I got the back clamped roughly in position before wiggling and tapping to get the thing to sit right.
I marked the position of the rear bracket against the inside of the mudguard before removing them once more to mark out and drill the bolt holes.
Nearside was the repeat of the above save for the lack of photographs.
The bolts are only temporary; I found some 3/8" x 1" coach bolts in the stores, that have now had the squares filed off, which I plan to use.
-
3
-
-
It's been a beautiful weekend here in Suffolk. Sunshine, blue skies, perfect weather for a steam rally but for the fact they're mostly cancelled.
Been in the shed for some of the time, continuing from where I left off a few weeks ago.
Here's the base for the gas generator, screwed down to the front of the step.
The bottom part of the generator clips into place
followed by the basket that contains the calcium carbide. The thimble in the centre appears to have been for water distribution but is quite corroded.
all topped off with the water container and gas collector. There's the remains of a rubber gasket between these parts; I'll make a new one when I get a moment.
rubber hose fitted to the delivery pipe-work and eyed up before cutting to length
all connected and looking fine.
I keep looking at the hideous yet authentic mudguard brackets and thinking they would be less of an eyesore if they were covered up. So today I've had a trial fitting of the mudguards.
They actually don't look too bad. Once I'm happy with the position I'll be marking and drilling the bolt holes. No hurry; I want to walk past them a while and get used to them before I commit.
-
3
-
-
Nice lathe. Longer in the bed than mine. I don't have the swarf tray (will have to make one in due course) but do have the floor mounted suds tray.
But very fortunate here in that we're already connected to a three phase supply.
-
I was in work today, the first time since October. Here's some pictures of the orbital welder used to repair the throttle control tube.
The parts to be welded are mounted in this jig:
The TIG head is clipped into place in the gap in the jig. Not the tungsten electrode. This needs to be at the correct height relative to the work.
The rotational speed and weld parameters are controlled by this box of trickery:
Here's an example of a test weld that's been sectioned:
Thanks again to Stuart for his time and patience in setting everything up, experimenting to find the optimal weld parameters and executing the perfect repair.
-
2
-
-
As I contemplated my return to the city, my mind turned from the practical to the aesthetic. Some might consider all these items practical but you have to admit brass does look good against the green.
This is a Lucas horn; ok for now but will be replaced when a suitable Howes & Burley one turns up.
I had to shorten the coach bolts and remove all reference to messrs Guest, Keen and Nettlefolds. Fortunately their branding was confined to the cardboard box for the 6 x 1/2" countersunk screws.
In due course the gas generator will sit on the end of the step.
Very last job of this extended stay in the East was a dab of primer on the screws and bolts.
Doc
-
4
-
-
-
What a find - a real stroke of luck. But if you hadn't looked you wouldn't have found. Maybe you make your own luck?
-
1
-
-
21 hours ago, alsfarms said:
Nice work on the quadrant. You will certainly be happy when you run the truck while the throttle and spark adjustments will stay in place!!!!!
Al
I can confirm that the levers do stay in place and make a reassuring noise as they move over the quadrant.
1st coat green was hard (should be, was drying in my small machine shop which I heat to avoid condensation) so I have refitted these parts.
With the ignition lever in the fully retarded position and the cam ring of the magneto similarly placed, I was able to complete the last piece of linkage.
This has now been removed for painting.
Next job? Well, there's top coat green to apply to these parts of course. I keep looking at the naked rim of the steering wheel and thinking that a covering of wood might afford it some dignity.
Before that, perhaps I should wash the bird sh*t off the flywheel. Incidentally, by the sound of things we have robins nesting in the crane shed again this year. Don't get me wrong; I like robins but they are indiscriminate sh*tters!
-
3
-
-
CPA Radiators at Grantham had square gills available when I took the core for my Fowler motor plough to be soldered up. This would have been somewhere around 2005 - can't believe it's that long.
No idea if they still do this or at what price, but might be worth a try.
Andy.
-
1
-
1
-
-
Thursday was warm. I took a day off work to get some jobs done and also got a coat of green on the inside of the bulkhead.
This weekend was a fun job that I've been looking forward to, but before I talk about that, I have to turn the clock back. Here's the throttle and advance and retard controls. They comprise concentric 1/2" and 5/8" mild steel tubes, the outer of which is the ignition, the inner being the throttle.
I cannot now remember when I repaired them but it was long before I had thought about writing this account, so sadly there are no photographs.
The outer tube was so badly rusted that it needed to be replaced. The crank on the end is a curious shape, designed to snake around the steering column. Ideally I would have held this and bored out the old tube, but I couldn't get a purchase on it. Instead, I held the tube in the 4 jaw chuck on the Harrison and carefully bored the tube out.
I had managed to source new steel tubing, so I cut and faced a length of 5/8" tubing and turned a brass plug to go up the end. A 4" nail was just the right diameter to pass through the rivet holes so after drilling the holes through the tube and the plug, I pinned everything together with a nail before silver soldering the parts together. The nail was then cut off short and both ends peened over. Next it went back in the lathe to be drilled and bored out.
When it came to the throttle tube, whilst the top had rusted off at quadrant height, the rest didn't look too bad.
We do a lot of high purity plumbing at work and have a rather natty orbital welder, normally used on 316L stainless steel.
Stuart very kindly experimented with the weld parameters using short test pieces of the new metal, sectioning each one afterwards to gauge the quality of the weld. Then I cut the rusty end off the throttle tube and faced the ends in the lathe. Then we did a test weld of new metal to old metal, using the off-cut, before finally doing the repair. It was worth all the messing about to save another original part.
and there's the weld, just below the part number.
So this weekend has seen the trial fitting of these parts. First task was to account for the length of the throttle tube.
then the ignition tube
The detent doesn't touch the quadrant for a couple of possible reasons: 1) the lever is bent 2) the detent is rusted.
I know that the levers are bent. I heated them in the forge and straightened them as best I could but didn't want to break them, so quit before that point.
They look a lot better now than they did!
Anyway, back to the story... I drilled out the rusted detent and turned a new one, filing the flats by hand.
I fitted it with some of that magic riveting solution, that comes in small red plastic bottles, so I didn't end up with the flats pointing the wrong way before peening the end over.
The throttle tube has a slot cut across it to clear the clamping bolt in the lever.
and that's about it for the time being. Need to wait for the paint to dry before I can get any further...
-
5
-
-
That's the ruse, our cunning and slight of hand; we go extraordinary lengths to make it look as if we've done very little. Can hardly blame people for not realising in the circumstances.
-
2
-
-
Hi! It's only me...
Sorry I've not posted for a while - been busy with other things. Hopefully many of you have been able to get on with your own projects too.
I don't know about you but I'm getting completely muddled by dates and times. Turns out these pictures date from April last year when lock-downs were still a novelty and the government's furlough scheme was paying David 80% of his salary to stay home and work on the Leyland subsidy lorry.
This is the lower near-side panel which, when folded out, forms a working platform. The timbers were mostly in good reusable condition and cleaned up nicely with some wire brushing.
The bottom plank had some rot, but we decided to repair rather than replace in order to retain the witness mark where the serial number plate had once been.
The rotten wood was chiselled out and a repair patch glued in. We managed to save the outer surface with it's 100 years of weathered patina - this would have been near impossible to try and recreate.
Meanwhile some bad screw holes were repaired by drilling them out and glueing dowels in the enlarged holes.
This is where a steel edging strip is fitted to protect the timber from wear.
Next, the panel was masked either side of the hinges with thick polythene in preparation for sand blasting.
Quick coat of red oxide primer on the exposed metal before the panel was brought into the workshop for painting.
This is one of the side reinforcing strips. I'd read about "Best" and "Double Best" steel in Professor Jamieson's textbook on steam and steam engines, but had not seen the mark before...
After painting up to top coat, the stencils were marked out through a paper template before being hand painted.
Underneath the word "Workshop" should be the serial number. Until such time as the brass plate turns up, this will have to remain blank.
Finally, once the paint was hard, the panel was man-handled into place in preparation for the painting of the inside.
And that fairly well brings us up to date. I have enjoyed writing this; I hope you've all enjoyed reading it.
Doc.
-
13
-
-
Back in January 1918, when the reporter from the Agricultural Gazette visited, what I have referred to as Elmswell Bacon Factory was known as The St. Edmundsbury Cooperative Bacon Factory. This is how it looked then:
Any squeamish readers might want to skip over the following interior view:
Among the subjects that have not been discussed here are veganism, the environment and the choice of paint shade for my lorry. I may have said previously that the log book recorded the colour as green. Well, green comes in many shades. I wouldn't claim to be good with colour but I figured that a strong vehicle would benefit from a strong colour. I bought a few test pots:
dark and mid Brunswick green, pre and post war SR malachite green, but none of these were really what I had in mind.
The shade I have chosen seems to suit the vehicle and, if it were to be parked alongside its military cousins, it wouldn't stick out.
With warm weather forecast for the rest of the week, I've just sanded off the inside of the bulkhead and hope to get another coat of green on sometime over the next day or so. While doing this I couldn't help that notice that, despite being a civilian vehicle it has recently come under aerial attack!
I have yet to identify the enemy.
-
1
-
-
Time for a quick update. Sorry, no slaughterhouse stories this week.
I took the grinder to the rivets on the old quadrant plates, so I could see where they were. Then dot-punched and drilled part way through the rivets before punching them out.
After giving the quadrant a bit of a spit and polish, I glued the new plates into position before clamping the quadrant onto the bed of the mill to re-drill the rivet holes.
I thought I had some rivets in stock but you no what thought did... so I ordered some from our favourite online retailer; they arrived in the post two days later. Can't complain about that.
A satisfying job, all in all.
-
6
-
-
When I was an undergraduate in the 1980's many students would go inter-railing during the long summer holidays. I did not. Instead I worked at the Elmswell Bacon Factory.
Pigs came in at one end (around 3,600 per week) and everything you can make out of a pig came out the other end. They say you can use every part of a pig except its squeal; the maintenance staff found a use for it: the noise that came from the steering of the pallet trucks... but the place was awash with brine, so everything rusted.
Eric King would come on shift at 6am, muttering to himself "f* job, f* job, f* hate this f* job; f* off f* home in a f* minute." This would continue until breakfast (8.30am). Well, he eventually got his wish, retiring from the job he hated, aged 65.
He has since become a part of the folklore of these parts, usually invoked in a phrase such as "This is turning into an Eric King job."
Why am I sharing this now? All will become clear...
Here's the throttle / advance and retard quadrant. The notched plates are badly rusted so I set about making new ones. They appeared to be about 4mm thick (5/32" in all likelihood). I found some off-cuts of 3 mm and 5 mm plate under the guillotine and, since my putting on tool is away for calibration, selected the 5 mm and proceeded to machine a circle out of it.
Actually, before I started I had to make some tee slot nuts to fit the rotary table.
I digress... Next I milled the basic shape of the two plates.
And then the job had to wait for the cutters to mill the slots in.
And this is where it felt like it was turning into an Eric King job. I had ordered 2 three flute 60 degree cutters and succeeded in breaking the first one after around 10 notches. They were on an approximately 2 week lead time and I was starting to regret being so mean as to have not ordered more.
But I finished the first plate,
started the second...
and finished it, all on the one cutter. So I'll put it down to "operator error".
Next job was to release the plates from the bulk material.
After a bit of fettling, they're looking pretty respectable.
In closing, I will bring the story of Elmswell Bacon Factory up to date. It closed, has been demolished and developers are building houses on the site. I wonder if the street names will reflect the history of the site:
Lairage Road, Tray-wash Close, Lard Room Drive,
I guess not.
-
6
-
-
10 minutes ago, Tomo.T said:
I need to find some old style gaskets for these which I hope will take up any slight discrepancies. The originals were asbestos, with thin brass foil each side, so I need to find suitable replacements, in more socially acceptable material. Anyone have any suggestions please ?
Try E Dobson &Co., Keighley.
They made the copper non-asbestos gaskets for my Karrier (and numerous other projects).
Just send them an old gasket to copy (in a self-sealing polythene bag) or knock out a paper template.
Quick turnaround and very reasonable on price (or at least I thought so).
Doc.
-
1
-
WW1 Peerless lorry restoration
in Pre WW2 vehicles
Posted
Hi there.
Here's a picture of the 2 - cylinder Albion engine in my 1915 Barford and Perkins motor roller. (Taken in 2016)
The copper - (non) asbestos gasket rings sealing the valve caps and the spark plug flanges (where low tension igniters were once fitted) were made by E Dobson & Co., Keighley. Valve springs were from Flexo Springs at Kingswood.
Doc.