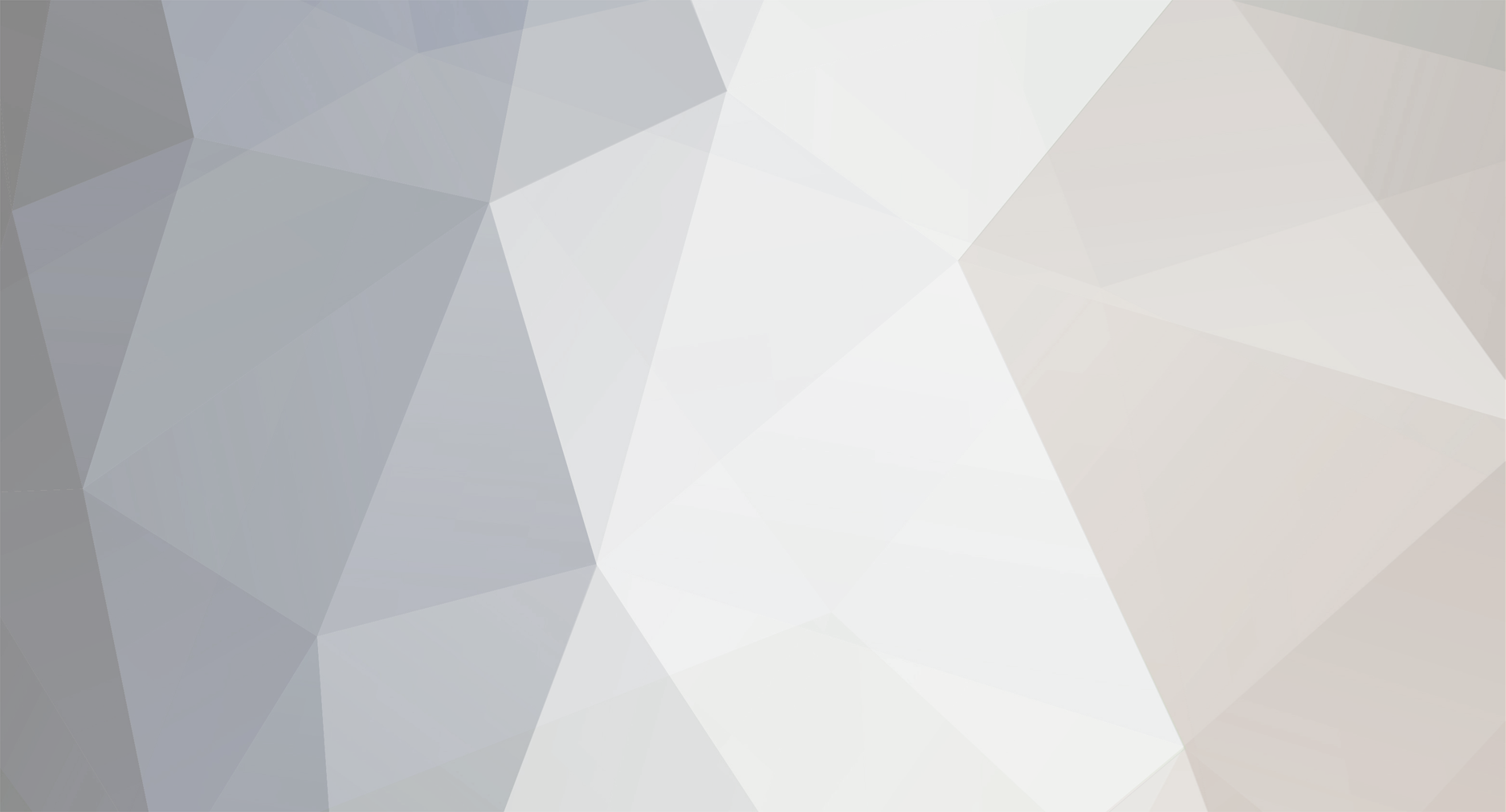
Doc
-
Posts
243 -
Joined
-
Last visited
-
Days Won
6
Content Type
Profiles
Forums
Gallery
Blogs
Events
Articles
Store
Downloads
Posts posted by Doc
-
-
On 10/5/2022 at 3:19 PM, General Dogsbody said:
Brilliant restoration. Saw the one at Duxford at the weekend. Are there any dimensions/plans available for this?
I'm not aware of any original plans or drawings having survived.
I have a 3d cad model of the basic frame. It's dimensionally accurate, especially in detailing the carpentry joints. Everything else was reproduced "on the fly" by copying what was there.
If you would like to use this as the starting point to create a more detailed model, that can be arranged. Its modeled in Solidworks but I can export STEP or IGS if that's any use.
Doc
-
1
-
-
Back east again this weekend.
The forge was missing a 1/2" Whitworth left-hand threaded nut to lock the crank handle onto its shaft. I considered making one but don't have the necessary tap; neither did our favourite online auction site. They did, however have a nut. Expensive, but considerably cheaper than a new tap.
The weather was unseasonably warm and dry this weekend, so we dropped the back of the lorry and stowed the forge. First we lifted it as high as the scissor-lift truck would go before rolling it over the edge into the body. Then back onto its feet and into position.
The "long" feet look odd but they are discernable in the Leyland works photographs. They happen to be the ones that were rusted off so we're not sure the exact length. One thing that's for sure is that the forge is inclined to topple over if they are short like the front two. When stowed for transport, the forge, like everything else was screwed down.
-
11
-
-
A quick update on the forge. A few repairs have been undertaken: two of the feet were rusted off so new ones have been bent and welded on. The blower assembly was worn, resulting in the fan grating on the volute housing. To fix this, a new dead shaft was made to accommodate the wear in the fan bearing. After reassembly, all is behaving itself again.
All parts have been wire brushed and painted with two coats of blackboard paint. The hope is that, given time, rust will start to come through in some places, making the forge look less "new".
-
13
-
-
Bright blue skies in sunny Suffolk today; I've spent a good portion of the day in the workshop under artificial light.
I dismantled my motley assortment of priming cups, keeping the parts separate, just to be on the safe side. Next I prepared a long length of brass threaded 1/4"BSP parallel and drilled and tapped up the middle 5/16" Whitworth. The taps were turned down and threaded to suit before being screwed into the end of the threaded rod (with Loctite) and sawn off.
The valves were returned to the lathe for the new threaded ends to be faced off square before being reassembled.
They are not all four identical, but they are pretty close. Finally the priming taps were fitted to the cylinders.
Another job off the list.
-
10
-
-
Oh how time flies!
This coming weekend (28th - 29th May is the first "Woolpit Steam" since 2019. I've almost forgotten how/what to do. Fortunately, I have my brothers to remind me, which they do, at every conceivable moment...
But it hasn't been all work, Jack (me) found time to play:
Used my shiny new 1/2" tube benders to make the last of the petrol pipes, between the tank and the fuel filter.
Warning! Please don't travel to Suffolk hoping to see the Karrier; it's staying home in the shed. But we are exhibiting the Leyland workshop...
Doc.
-
3
-
-
13 hours ago, Asciidv said:
Of all the things that I saw in this last post, what I liked most of all was the use of a proper old fashioned flat bladed screwdriver with a wooden handle. A period tool matching the vintage of the machine being worked on.
Was I the only one thinking that the "vintage screw driver" was used to pry the lid off the tin of grease?
Doc
-
-
10 minutes ago, andypugh said:
Indeed it does. Though there seem to be witness marks for an alternative fitment on the tank itself (possibly very recent, though)
The marks are where I peeled the felts off prior to turning it round.
I placed the tank as it was when I received the lorry. Photographs of it "as found" do not give any clues as the tank is largely hidden by the seat box. I'm pretty sure I've got it right now.
-
On 4/22/2022 at 11:19 PM, mammoth said:
Clayton & Co qualified for the subsidy scheme following trialing their example in the War Dept trials.
Clayton & Co. Huddersfield, makers of Karrier lorries.
Clayton and Shuttleworth of Lincoln were not, so far as I am aware, afforded the opportunity to trial their example.
-
I have found a few more details.
The lorry was entered as an exhibit at the 1915 Royal Show held that year in Nottingham with an £800 price tag.
The Commercial Motor's report of the show states: "On Clayton and Shuttleworth's large stand (284) only one example can be correctly described as coming within the scope of this journal. This is a three-ton steam wagon on rubber tyres..." The no-show at the Royal might explain the excitement with which the lorry was at the Smithfield later that year.
The implement and machinery section of the 1916 show was limited to ease pressure on the railways, so the makers were unable to exhibit the lorry at Manchester. .
The lorry was not entered in the 1919 Show, which was held at Cardiff.
-
Saturday I secured this haul of brass:
which allowed me to complete the pipework for the heater jacket on the inlet manifold. Fortunately I had this image in my photocopy parts list as a guide:
The petrol isolation tap is 3/8" BSP where it screws into the tank but takes a 1/2" union. I've not managed to find such a tap so in the meantime I've modified a 3/8"-3/8" tap to suit. I should have taken pictures of it in the lathe chuck but I had dirty hands.
Here's the finished item fitted to the tank:
The union is perilously close to the gearbox input coupling. So this morning we lifted the tank off and replaced it the other way round.
This time there was plenty of room.
though why the tank doesn't completely occupy the near side saddle is anybody's guess.
Doc.
Uploaded from a speeding Bristol-bound train.
-
1
-
-
With nuts and nipples in hand, I've made and fitted the petrol pipe between the fuel filter and the carburettor.
Inspired by this, I set about bending the oil line that leads to the dashboard-mounted tell-tale. It's a bit of a fiddle getting out from under the magneto bracket but I followed the lines of the crank-case and I'm satisfied with the result.
Then made a simple jig to bend the p- clips.
After a bit of drilling and fettling they were looking respectable too. Proof of this pudding was in the fitting.
Masking and touching up the paintwork will see another job finished.
-
3
-
-
So I stumbled across this image of a 3 ton petrol lorry built by Clayton and Shuttleworth and exhibited by them at the 1915 Smithfield show:
Commercial Motor's reporter described it thus:
"On the whole, no departures have been made from orthodox practice, but the company prides itself on having produced the whole machine, with the exception of the engine, in its own works, including such processes as frame-pressing, malleable casting and aluminium casting. The design provides for a Dorman engine.
A more detailed description followed:
The construction is on orthodox lines, bearing evidence of careful attention to detail, whilst the necessity for providing adequate strength to meet all likely demands has not been overlooked.
The specification covers a 45 h.p. four-cylinder water-cooled engine, with Claudel-Hobson carburettor, high tension magneto ignition, thermo-syphon circulation of the cooling water, enclosed valve-gear, etc., etc. A cone clutch and leather-jointed clutch shaft transmit the power to the four-speed-and-reverse gearbox. The latter is fitted with change speed on the gate-change principle, and the box has cast integral with it the housing for the spherical-ended, tubular part which serves to convey the driving thrust from the rear axle, as well as to re-act against the driving torque.
The whole of the transmission, from the gearbox rearwards, is totally enclosed. The rear axle is work-driven, of the type in which the worm is above the wheel. It is full-floating, the load being carried by the double-banjo forged-steel main axle, with cast covers above and below to form a spherical centre portion. Both brakes are in the rear wheels, side by side, in separate drums.
This is a new one on me. If anyone has more information on this vehicle, I would be pleased to hear...
Doc
-
1
-
-
Nuts.
Scant progress on the Karrier of late, but I have made a few nuts for the fuel lines.
In other news, I've found (and bought) a Karrier spare parts list. Not the WDS, sadly, but a BR110. 5 ton, chain drive. Tylor JB4 engine, same as the WDS.
I found a couple of images online which I've reproduced here for educational purposes.
Doc.
-
1
-
-
Thanks for spotting these. I couldn't view the Facebook example - I'm not on Facebook. The eBay Drummond is a 7" lathe so too big for the workshop. But a rare beast, it has to be said.
If you spot a Luke and Spencer grinder or any of the other equipment that populates the Duxford example, please let us know.
Doc
-
Wellington Tube Supplies in Hayes (02082305708) have 7/8" od x 0.128" wall C106 copper tube in stock.
My 12th edition Machinery Handbook (1945) gives the major diameter and depth of 1/2" BSP parallel thread as 0.825" and 0.0457" respectively.
This should leave a minimum wall thickness of 0.0573" at the root of the threads. Is that enough?
regards
Doc
-
1
-
-
We've had another find. Not as magnificent as the forge, but useful nonetheless.
A Drummond lathe, dismantled, for spares or repair, on our favourite online auction site. It has yielded this:
(in the words of a certain entertainer "can you tell what it is yet?")
Platform for the electric motor to sit on, also the hand-wheel for the end of the upper lead screw. For this I needed to make a flat key and a stepped collar to control the end float of the lead screw.
There was also a drive plate for turning between centres. So that's a few more things scratched off the list.
-
9
-
-
Steve,
Thanks for bringing news of your wiki page to this forum.
There's interesting articles on the Commercial Motor archive.
The JB4 engine was announced in their 26th July 1913 edition, followed by a detailed description in their 23rd December 1915 publication.
A further article published May 26th 1925 reported that Tylor's (JB4) Ltd had acquired the whole stocks of JB4 spares from the manufacturers valued at between £25 and £30,000 to support the approximately 35,000 engines then in service.
The link with Guy Motors is interesting; I have heard that before but am not aware of the details. But the reliance on sub-contract manufacture is understandable; a photograph, in the 1915 article, of twelve engines is described as one week's delivery.
The Angus Sanderson car and the Tylor engine that powered it are described in detail in the 1920 supplement to Rankine Kennedy's 1913 three-part publication "The Book Of The Motor Car"
Regards, Andy (Doc)
-
1
-
-
Just returned from a 180 mile round trip (passing signs for places without any vowels in them) to recover this:
In case there's any doubt, here's another one:
There was "SLOW ARAF" painted on the road in various places but we never saw one; guess they're some sort of wild animal peculiar to those parts.
A bit like a giraffe but sturdier, perhaps?
Thanks to Sam for the driving.
-
7
-
-
-
I have a friend with a penchant for leather, though this is probably not the place for that sort of thing...
Actually, a friend of mine worked as an orthotist at the local hospital. When I needed leather clutch linings all I had to do is provide him a template (the drawing office at work had an A1 plotter in those days) he would contact his footwear supplier and the linings would come back in return for a NHS prescription charge. £5 from memory.
Between us, we've relined 3 Saunderson tractor clutches and two Albion clutches.
Our technique is to soak the leather in water for a week and apply it to the cone while it is still wet (and supple). Punch the first two holes, fit the rivets but don't rivet them up, pull the leather up tight, and mark the next hole. Punch the hole half a hole short and pull up tight with the rivets. Continue like this until all the rivets are in place. Then remove the rivets one at a time and replace them with short annealed ones and rivet them up.
I'm not sure how practical this method would be for lining the steel backing strip as used in the Peerless.
As the leather dries it shrinks and pulls up tight to the cone
We then "fit" the cone to the flywheel by blueing the inside of the flywheel, spinning the cone into the cups and filing the high spots with a rasp.
I've never had to uniformly reduce the thickness of a leather lining; I'm intrigued to know how you get on.
Doc.
-
2
-
-
Looks like a Dean Smith and Grace lurking under the bright yellow guard ?
-
Nipples.
Now that got your attention. I turned my attention to the radiator overflow which had been blanked off with a rubber disk backed up by a steel washer. So a new 1/2" solder nipple was required. This and the petrol fittings are all the same size so I planned to make 5. Then David spotted that they are the same size on the Leyland (water heating on intake manifold) and on the Ransomes Wizard stationary engines that are being restored.
So five became thirteen. And one more for luck.
Now I need to find an off cut of brass to make two more nuts.
1/2" diameter steel arrived while I was in the city; I've been waiting for that to complete the radiator stay.
Trial fitting
After its turn in the paint shop. Sorry, not the best picture.
-
6
-
-
48 minutes ago, Old Bill said:
I don't have photos to hand, but the Leyland tank is also very similar. Only significant difference: the Leyland tank is mounting on wooden saddles that form part of the seat box whereas the Karrier and Dennis have the tank mounted on cast brackets bolted directly to the chassis.
Andy
Karrier WDS
in Pre WW2 vehicles
Posted
A quick post to describe the consolidated efforts of a few weekends back East.
Some weeks ago I started measuring up for the plug lead conduit, as I had found a supplier online who was able to supply custom bends in 1 5/8" diameter steel tube.
Move forward a couple of weeks and the tube arrived, over length, so it was offered up again to confirm the correct size.
The eagle-eyed amongst you will notice the brackets have changed orientation. After consulting the 1977 "as found" photographs I realised that the conduit was originally fitted on the off side.
A final check that the lengths were correct...
Next job was to make a swage block to flare the ends of the conduit.
Note: the tube has to be flared with the brackets in-situ as, after flaring, they are captive.
Next, onto the mill to drill the holes for the plug leads. "Measure twice, cut once" was the order of the day here.
Followed by a good clean and a visit to the paint shop
And, first thing this morning, back on the lorry.
Doc.