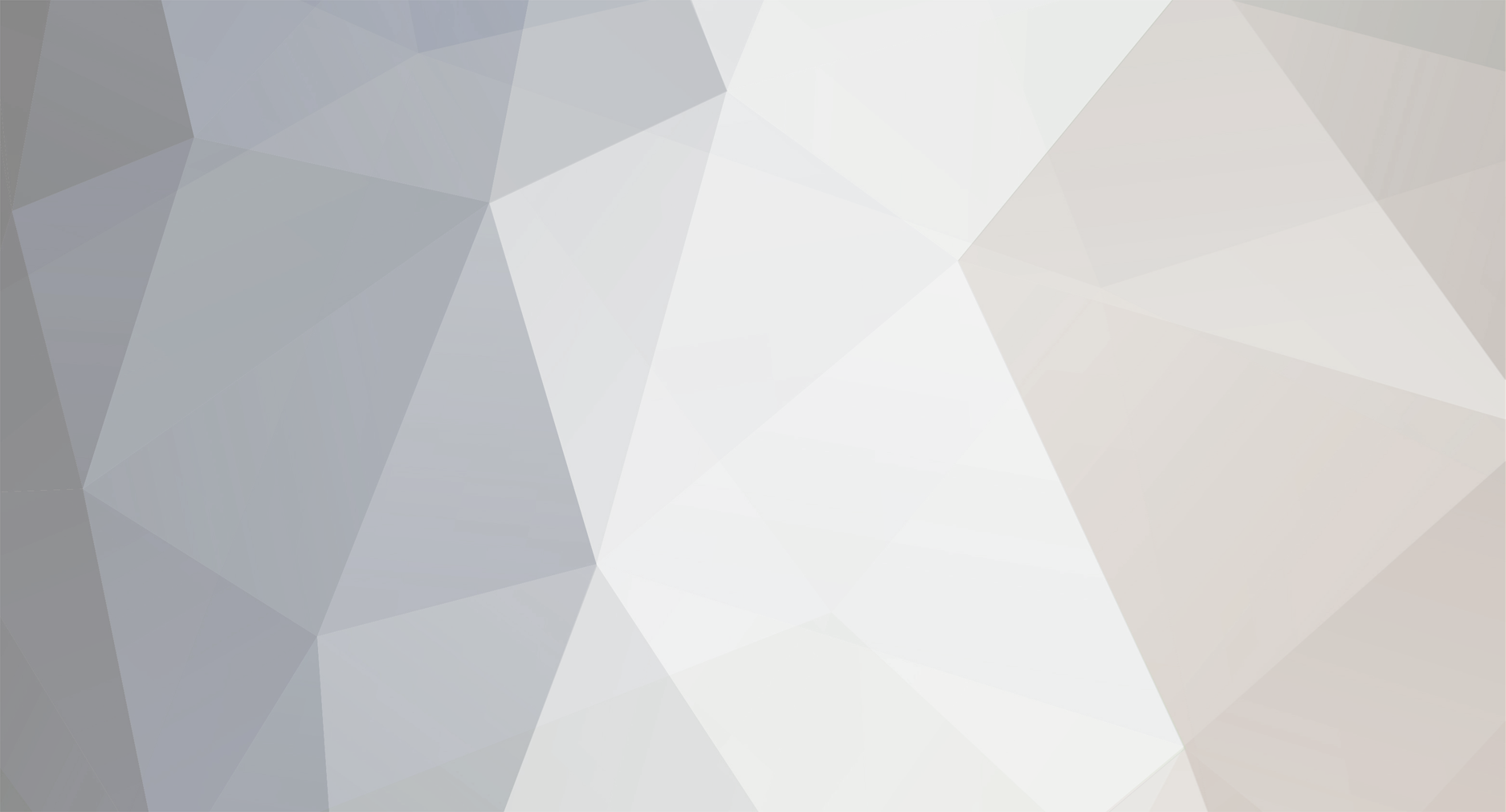
64EK26
-
Posts
563 -
Joined
-
Last visited
-
Days Won
7
Content Type
Profiles
Forums
Gallery
Blogs
Events
Articles
Store
Downloads
Posts posted by 64EK26
-
-
Hi
It's a scam
vehicle is located in Japan !
see https://www.autolink.co.jp/12392-japan-used-land+rover-lightweight-1980-suv.html
Cheers
Richard
-
Hi
I have a set of machine readable manuals for the FH70, PM me if you want a copy
Cheers
Richard
-
On 12/30/2020 at 8:42 AM, john1950 said:
Thanks for the reply, I think pilot shaft, gearbox bearing, fuel chang over tap, and as you say Radiator cap all for Bedford.
Hi
The bearing is from a Bedford Gear Box - equivalent to an SKF 6307
Cheers
Richard
-
1
-
-
Hi
A bit of a long shot, but I am looking to reproduce a data plate for my MWC. The plate relates to priming the power pump before use.
I was thinking about getting one etched, but I think the etching depth won't be enough. The size of the plate is 2.5" x 2.5"
Does anyone have one of these I could borrow to make a copy or better still does anyone have one for sale?
Cheers
Richard
-
Hi
Have you asked on the facebook "Bedford lorries past & present" forum ? May be worth a try
Cheers
Richard
-
1 hour ago, 67burwood said:
And just to add insult to injury my wife sticks her head out the window, smiles and utters those words “ is it broken “ As you can imagine the reply can’t be posted on this blog 😬
Not broken... just re-positioned and re-shaped 🙂
-
1
-
-
Hi
This is the connector for the R216 reciever
For the SUR45 power supply you need a free plug of the same type
The pinout looking at the reciever are
this is from
https://www.radiomuseum.co.uk/R216.html
this web site also has details of a "home brew" main power supply. I doubt if you will find a SUR45 which has a DC input (think it is 24V), or a No. 24 power supply which is a mains supply one, in either case the the output socket is a plessey Mk 4 12 pin fine thread
Cheers
Richard
-
Hi
I assume it is a Plessey Mk4 12 pin free socket, is it a fine thread or coarse thread ? I am sure I have some lurking somewhere
Cheers
Richard
-
Hi
You have been lucky, they look really good, I have been looking for those strainers for a long time but without success.
Is the hinged strainer made from aluninium or galvanised steel ?
However, I did manage to find a later type strainer which is not hinged and is made of steel which will suffice until I find an original.
Cheers
Richard
-
A great guy, who will sadly be missed
-
1
-
-
Hi
Thanks, just had a look at their on line catalogue but can't see any, will go and have a look when we are out of lockdown
Cheers
Richard
-
-
Hi
Been doing a bit of tinkering in the "shed"
Gun Mounts coming along nicely
Wiring slowing taking shape
Decals for master switch from Simon King (on this forum, I think he has some left)
does help having a A0 wiring diagram to hand
Also taking the slack out of accelerator linkages using home made brass bushes
-
6
-
-
Hi
You can get the shackle bolts from the states see
https://www.currieenterprises.com/CE-91128
I will see what I have in the shed, but I think they are a bit larger.
Are your shackle bolts 1/2" in diameter , or is that the thread on the end
The 10cwt trailer parts list is not very helpful in the size of the shackle bolts
Cheers
Richard
-
-
Hi
Just tried uploading some photos, but I get the error
"Sorry, an unknown server error occurred when uploading this file.
Please contact us for assistance."
Who is us ?
Cheers
Richard
-
Hi
I am after a Bedford 28HP timing chain for the power pump on my MWC
Any used but generally servicable one (i.e not totally rusted up) would do fine
Thanks
Richard
-
Hi
Not posted for a few weeks, but I have been busy
I have spent some time making bits for the power pump, the one that I acquired was for an early MWC (see notes in previous posts) and needed some some modifications. The outlet of the pump did not well under the tank and also it did not have a third port for the pressure releif valve, so new top made
This is the original output (the "Y" is the output ports)
and this is the newly manufactured one fitted to the pump (it is not an exact copy but it will do what an original one does (thanks to Tomas Higgins for some additional photos of the power pump)
Thanks to Pete Ashby for take the measurement of the pressure relief valve, ny truck need three of these , one on the power pump and one on each of hand pumps (still looking for these)
I had already made the front pump support, the rear was proving a bit more difficult as the reat of the pump is 3" in diameter and the clamp width is about 1". On eBay I happened to come across a sanitary/kitchen pipe clamp which was advertsed as a 3" pipe clamp (just perfect I thought), the clamp is american made but made for a 3"BSP pipe. So I turned up an Aluminium split shell to fill the gap between the pump and the clamp.
Welded up a support backet that sits on the chassis cross member, the clamp bolts though into this (3/8" UNC bolts, these are what came with the clamp) nett resut
Next job is to convert the drive mechanism to a chain driven one. This will unfortunately means cutting the drive shaft as it is a bit too long. The modification I will be doing will mean that it can be returned to its original state at a later date.
Due to the rotational direcion of the pump, all the threads on the end will be left hand ones. The chain is the same as the timong chain that used on a Bedford 28HP (looking for a scrap one of these)
Next update in a couple of weeks
Cheers
Richard
-
4
-
-
Hi
I have similar one made by Marples (not for sale as it was my late father's), still one of the best screwdrivers I have ever had. Doesn't have a square bit on the shank.
Have you seen this
Cheers
Richard
-
Hi
Hopefully this is the rigt place to post
Has someone been playing with the web site as I can't see any photos on my windows laptop (same on my phone)
also on my laptop there are some additional user names being displayed for no apparent reason
Cheers
Ricjard
-
Hi
May be of interest to someone
Cheers
Richard
-
Hi
Never seen a complete list of ZA to NSN's, I have a few of the ground spike and will dig them out over the week end to see what numbers(if any) they have on them, I assume that this is what you are talking about
Cheers
Richard
-
Hi
Not much progress this week, limited time at the "shed", but did manage to get the hand pump supports brackets partially made
Thanks to Pete Ashby for supplying me with pattern for the supports (and some useful photos), hopefully will be cutting the back in the next couple of days and welding them up next week, this is what the should look like
Next on my list is to attemt to make the facy valves that goes at the bottom of the pump (unless anyone has any of these that they wish to sell),
this is specially for MWC's as other bowsers have a different arrangement for selecting hand pumping or power pumping. When the power pump is used, the water flows though the hand pump to the filters
Cheers
Richard
-
2
-
-
11 hours ago, Zero-Five-Two said:
I've had it apart, hoping there would be seals that could be replaced or something, but the main gubbins inside fits metal to metal, and too much of it has worn away over the years.
Don't know what the internals are like, I assume there is a piston that goes to and frow. Would it be possibe to re-sleeve it and/or make seal on piston ?
Would be interesting to know what the internals look like
Cheers
Richard
Fordson WOT6
in Blogs of MV restorations
Posted
Hi
A couple of observations / comments...
As you are welding old steel to new steel, the old steel may well have rust and other impurities that will stop a good flow
Also when welding old to new steel. The old steel needs to be really really clean, clear of any rust and thoroughly de-greased (likewise for the new steel). If you don't do this then rust will soon bubble through. (Learnt through experience)
Also good idea to give welded items a light coat of paint to prevent surface rust, especially important as it damp at the moment. Any small unseen voids can also be sealed with seam sealant.
Hope this helps