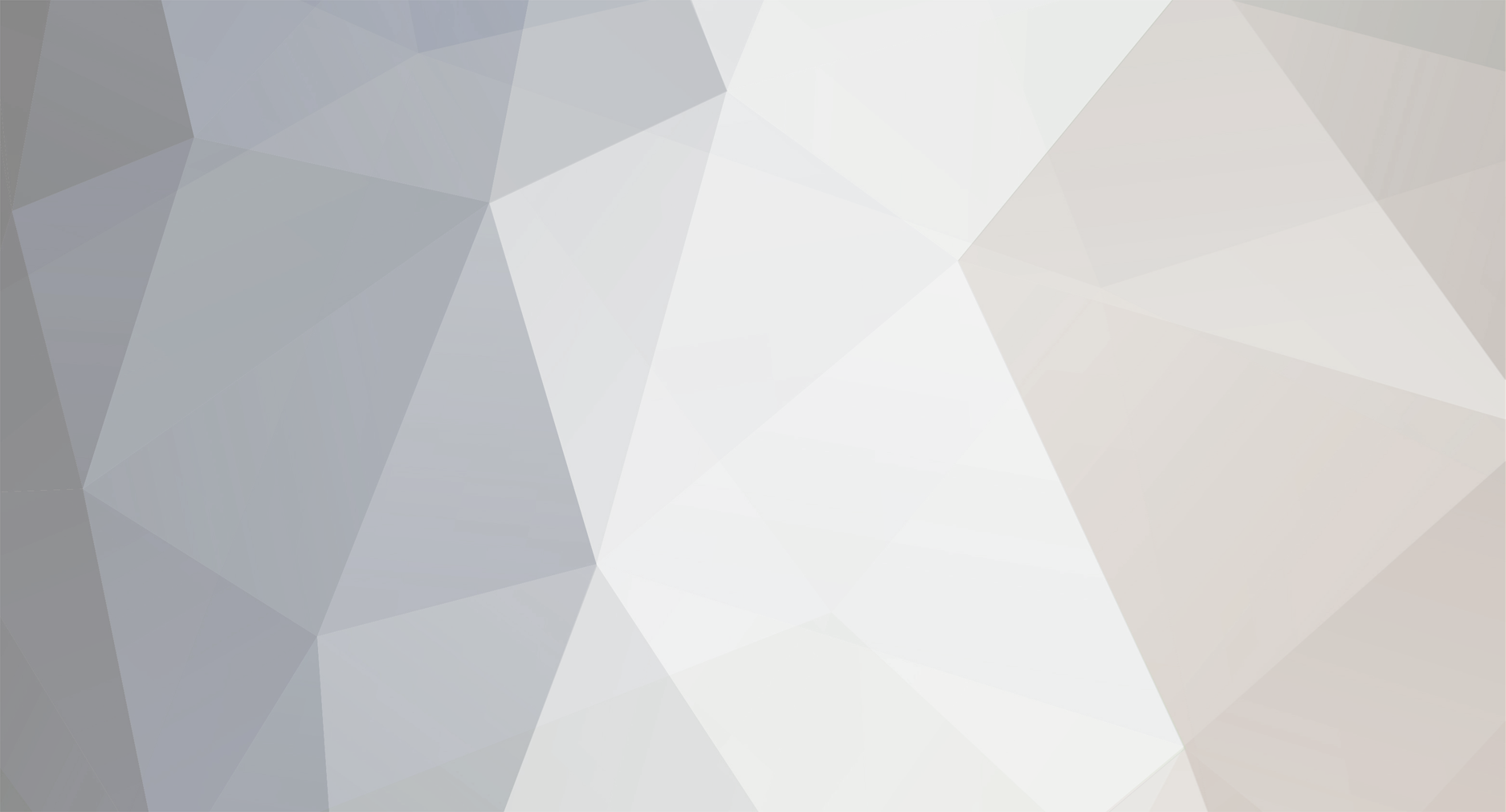
mazungumagic
Members-
Posts
230 -
Joined
-
Last visited
Content Type
Profiles
Forums
Gallery
Blogs
Events
Articles
Store
Downloads
Everything posted by mazungumagic
-
The Restoration of Austin Champ 1824
mazungumagic replied to mazungumagic's topic in Blogs of MV restorations
As mentioned last week, I replaced the C50 fanbelts with C51s which I managed to instal with the minimum of fuss… The vehicle is now near enough to finished and we moved it last Monday, from the Workshop where it has been for over twelve months, to my place - where it will be for a little longer. There are a few things which still need to be done, but I can easily do these minor tasks at home rather than cycle the two hour round trip to the workshop and back ! I still need to swap over the brake hydraulic switch which just arrived from the UK at a cost of $A26 delivered, compared to $A48 from a local brake shop ! A bit more tidying up and the vehicle will be taken to the licensed vehicle inspector (a Veteran Car Club appointee) for his roadworthy check and, all being well, the licence/registration will follow. At this point, I need to thank the four people together with the occasional "ring in", who helped immeasurably with this restoration. The work could not have been even contemplated without the team of Tony, Murray, Brian and Peter. Thanks to you all. Bravo Zulu. -
Thanks monty2 and shane.c Richard - the Col Anderson vehicle is one of the brass radiator type, ie prior to 1917. So the body is quite different to the one the War Dept seems to have opted for, in their last run of model Ts. This slightly flawed photo (it got stuck to some plastic), taken from the Aug 08 edition of the VMVC Newsletter, shows man and machine on what looks like a cold Shepparton day. Jack
-
Thanks for the help, Gus. I bought 50 new spokes from the Stutzman Wheel Works in Ohio and picked them up on a trip to the US (after visiting Hershey - Oct 2011). They were then given a few coats of marine varnish and pressed into the fellies, using my version of the John Regan wheel press. They are a quality product and very tight in the fellies. I've just fitted the tyres on the rim and bolted them to the wheel... So, four years after bringing the bits home, the vehicle is about to roll. Jack
-
Now that I’ve just about completed the Champ restoration, I can get back into the build of a 1917 Model T Light Patrol Car. I've read in a number of places where the British had close to 19,000 Ts during the War - an extraordinary figure ! Knowing nothing about these unique vehicles but happy to learn, I started with this in 2009. … and reached this stage in late Nov 12, when the Champ intervened. I believe that the vehicles issued to the Light Car Patrols were all sourced from Ford’s English plant in Manchester (Trafford Park?) during the War. The post 1916 vehicles had bodies which, it would appear from the available photos at the IWM and AWM, were built to a standard design. The difference was that while the US version of the T (ie LHD), had an opening door on the right and a false door on the left, the British design was a mirror image, taking into account the RHD drive configuration. That meant I had to make a LH door from scratch - the US suppliers of Model T parts obviously cater first and foremost to their own market. As you can see from the second photo, all the mechanical work has been done and the rear body is complete. What remains is the sheetmetal work around the door areas and the painting. We’ve started to paint a few of the detachable parts – the colour is a Leyland paint called Sand Glow… I’ll leave it at this point for now, but will follow up regularly with progress. If anyone wants detail on any aspects of the work done to date, I’d be happy to respond.
-
The Restoration of Austin Champ 1824
mazungumagic replied to mazungumagic's topic in Blogs of MV restorations
After the fan trouble I had last week, I thought it was time to change the fan belts, The C51s which were on the engine, were very tatty and the breather hose on the genny was hitting the RH mudguard, so reasoning that a set of C50s would solve the length problem, I went and got a couple. That was not the right decision ! I was not in the hunt to get them fitted. So back to the shop and exchange those C50s for a set of C51s. After struggling a bit to get the belts onto the pulleys for a second time, past the tiny gap betwixt top pulley and radiator, then around all the fan blades, I was finally successful. Once the radiator had been unbolted (yes you have to do that on a Champ), it wasn’t that difficult. At full tension, the genny breather hose now sits a good 25mm away from the mudguard, so it’s clear that the old belts had significant stretch in them. i didn't realise they would have stretched that much. My duckboards are now nearly completed – just the RH rear one to finish and they’re done. I’ve now got the indicators working. I had initially used an old 24v flasher can I’d had sitting around for a few years, but it was clearly inoperative, so I ebayed a three pin can and fitted that. The result was perfectly functioning indicators as well as the tell tale light, positioned in front of the driver. The panel light is now working. Not sure what I did there, but it’s now good to go. Shouldn’t question why, when problems fix themselves – it happens so rarely. I’ve now narrowed my problems down to a mere two in number. Neither the fuel gauge nor the temp gauge, is cooperating. Not sure I can do anything about the temp gauge (they seem to be a universal complaint with Champs), apart from installing another modern capillary type, tapped into the unused plug in the water pump. The fuel gauge though, may be fixable if, as I suspect, the problem lies with the sender unit and I can locate a serviceable replacement. I’ve got power at the sender unit, but nothing registering on the gauge. The gearbox cover is now on – I forgot to run a tap down the myriad of ¼” UNF captive nuts before engine and gearbox were installed. They should have been attended to when they were easily reachable. Everyone of those nuts, needed attention before the bolts would start and at that stage using a tap in the very confined spaces, was a true test of stamina. -
Good to see another Champ owner being brave enough to go public. I second the call for pictures ! Jack
-
The Restoration of Austin Champ 1824
mazungumagic replied to mazungumagic's topic in Blogs of MV restorations
The fan noise from last week created a gnawing suspicion that I might have assembled the fan incorrectly when I was putting it together, many moons ago. So I found another fan, pulled it apart and checked it, as well as re-familiarising myself with its features, via the Tech Manual. Once I was happy knowing how it was way it was designed to work, I took it over to the workshop. Today we removed the radiator and the original fan, to find that one of the five nuts holding it onto the fan boss, was missing and the remainder were untight. The stud which was minus its nut, was so badly scored and bashed, that I was obliged to run a die down it, before I could start a nut. The other thing that was noticeable about the radiator and particularly the shroud was that the fan had been fouling the canvas closest to the metal ring. That was what had been making the noise on the first start up. That done and the fan secured, the radiator went back in and was bolted down with all tubing re-connected. The fuel line was next. I had completed the run of the line from filter to pump, during the week and now it was time to test for leaks. A few gallons into the tank – no leaks at that end. Much priming at the pump produced no result, so we added some compressed air to the tank and were rewarded with some fuel exiting from the top of the filter. We realised after a few false starts, that the aluminium washer on the top of the filter, was not seating properly and gave the top a good clean. That produced the desired result and we then got fuel through to the pump and thence to the carby. Again no leaks along the fuel line following the chassis from rear to front, so we started the Champ again and - the canvas shroud rubbing noise re-appeared. We spaced the shroud away from the fan with a set of 1/8” washers and the noise has now been eliminated. Perhaps the repro shrouds may be too bunched at the ring ? During the week I had removed the LH headlight to check the earth circuit and found the wiring connection to the globe needed a bit of cleaning, which was done and I now have perfectly balanced headlights. The only electrical problems left are the indicators, which will be fixed as soon as an ebay purchase of a three pin flasher can arrives (shortly) and the non functioning instrument panel light. I may have to pull out the speedo portion of the panel and check how/if I connected the IL wire. I’ve also now picked up my upholstery and installed the front seats – the rear ones will have to wait a few days till I’m completely satisfied that I can secure the rear axle cover, before they (the rear seats) are attached. -
Charawacky, An interesting picture - one I hadn't seen before. The vehicle does seem to be from a Light Car Patrol, but a quick check of the 1st Australian Light Car Patrol's War Diary for that period (Sep-Nov 18) doesn't mention Megiddo, so it may have been a vehicle from another patrol. The fellow next to the Model T does appear to be wearing a slouch hat, though. There appear to be at least seven men in the shot and a couple of horsemen in the middle distance, so I guess there is more transport out of camera range. I see the photo appears on Wikipedia, but it's unattributed - do you know where the original came from, or do you happen to have a hi res version ? Jack
-
The Restoration of Austin Champ 1824
mazungumagic replied to mazungumagic's topic in Blogs of MV restorations
Thanks Jerry - there were some who said it couldn't be done, but it was. It is really a tribute to the skills of my fellow workers and their perseverance, though I doubt I could convince them to sign on for a Stalwart ! The Model T is next - I'll get a blog going on that - it only needs a few weeks work to complete it. Then we transition into the Lohner Dodge. Jack -
The Restoration of Austin Champ 1824
mazungumagic replied to mazungumagic's topic in Blogs of MV restorations
While rubbing back the Model T parts we painted last week in preparation for their final coat, we did manage to get some Champ jobs done. Adjusted the brakes and obtained an improved pedal. Also adjusted the handbrake and managed to get that working well, at the fourth notch. After that, we started the Champ and did a few adjustments on the carby and the distributor, to the extent that the vehicle is now running very well. There was some rhythmic noise from the fan which sounded like the fan blade ends were contacting the circular metal of the shroud, so we shimmed the shroud a little further to the front of the vehicle and the noise has now abated. It could be that the fan and its internal gubbins may be faulty, producing a bit of wobble so I will dust off the spare that I have and tart it up. If we have to replace the engine fan, it won’t be a major drama, though removing the radiator to get at the fan at this stage will be a minor and unpleasant challenge. The electrics are now mostly sorted – the indicators weren’t working, but a change of flasher can has proven that the original Hella type I had installed, was faulty. The new one is only a two pin, while the original was a three and that’ll require a bit of thought to rig it, so it works externally and lights up the internal tell tale. I’ve also got one headlight (LH) which is dimmer that the other – possibly an earthing problem, but now that the grille is in place, the light and its surrounds are proving difficult to extract, to check what the problem might be. I’ll keep working on that. A working 24v horn is hard to find and those that are available, are ridiculously expensive, so I picked up a modern 24v type for $20 and wired that up inconspicuously, while leaving an original looking (but only 12v) horn, prominent on the RH side. The setup works well. The last of my electrical problems appeared when I connected the batteries - the brake lights were on. It wasn't hard to trace this fault back to the brake light switch, which is obviously stuck in the closed position. I'll have to get a new one and work out some way of preventing air from entering the system while I change the switches over. Still have to complete the fuel line from filter to pump, but that’s coming along and I should have that finished and secured in place, this week. No pictures this week, though I’m working on mastering the camera so that I can get a sight and sound video of the engine running. -
restoration Restoration of Champ 1624 in Sydney
mazungumagic replied to simondema's topic in Blogs of MV restorations
Simon, At first glance the engine looked to be painted black, as some of the earlier 2A ones were, but I gather from some of the scrapings on the tappet covers, that the black is just oil residue. The fuel tank looks good on the top side - but time and water normally affects them underneath particularly where the straps are located. How was yours ? Jack -
The Restoration of Austin Champ 1824
mazungumagic replied to mazungumagic's topic in Blogs of MV restorations
There’s not too much to do on the Champ now, though I did manage to get some work done on the electrics. The problem I had with the inoperative lights, was traced to the fact that I had no live feed (Aux Pos wire) from the Distribution Box into the switchboard. Hardly any wonder that the lights didn’t work ! I didn’t get a great deal of time on the Champ today, but did manage to rectify that omission. I was also able to do a wheel alignment with a tool that I welded up out of scrap. It worked very well, once we got the hang of the track rod adjustment set up. We also attached the canopy bows and are now waiting for the canopy to arrive from the UK. This Friday, I should be able to collect the front seat upholstery from a motor trimmer and I’ll also drop off the rear seat metal work for him to complete the job with the slightly more involved rear vinyl. We spent most of the day rubbing back and painting a few of the Model T parts that I’ve had in the workshop for around a year, while our main effort was focussed on the Champ. With that work now coming to an end, we are now switching to the T. So, today we got out the two pack “Sand Glow”, mixed it up with some thinners, a dollop of hardener and a little flattener (to take off some of the gloss). The Sand Glow is a Leyland colour and while no one seems to be able to provide any positive evidence about the colour used by the Light Car Patrols in the Sinai and Egypt, I’m quite happy with the result. So, I'll be fading out of the Champ restoration blog soon and opening up another, on the completion of the Model T. -
Austin Champ parts catalogue
mazungumagic replied to simondema's question in I may be stupid, but......
Simon (and Richard), The Spare Parts List is the British War Office variety and like the Champ, it is very difficult to follow ! I'll see if I can walk you through it using the FV 15653 Bracket and Bush as an example. Firstly, look at the Numerical Index to catalogue Numbers in the rear of the book and you'll notice that the numbers themselves are in order - if you ignore the letter prefixes eg RE, FV, GB, CU and whatever else. Here on Page ix, is the part # FV 15653, about a third of the way down in the second last (RH) column. The last column (on the right of the part #), shows the actual listing in the Parts List book, which in this case is G2. So we head off to Page G2 and here's where it gets confusing - as if you're not already ! There are two pages marked G2. One is the actual listing of parts - ... and the other is a Plate diagram. So first we go to the parts list page marked G2 and scroll down the "Catalogue Number" column (the second one) till we come to the part # in this case FV 15653. In the first column marked "Item Number", it is #52. The description is "Bracket control lever with bush". From here we move laterally to the "Plate Reference" column and find the numbers 1-5. Directly above these numbers is one in bold type - in this case G3. The G3 figure is the plate diagram number and the 1-5 are the actual numbers on the plate diagram. Easy isn't it ! BTW, that's a nice looking steering wheel ! Jack -
The Restoration of Austin Champ 1824
mazungumagic replied to mazungumagic's topic in Blogs of MV restorations
Correct, Gordon. I agree with your estimation of Champs - I doubt I will want to do anymore. I'll move on to finish off something a little simpler - say, a Model T Light Patrol Car ! Jack -
The Restoration of Austin Champ 1824
mazungumagic replied to mazungumagic's topic in Blogs of MV restorations
The first part of the morning was spent on our new project, a LohnerWerke Dodge. As I mentioned last week, this is a WC 51 which was refurbished by the Austrians after WW2 as a radio van and, after spending a part of its new life in the Austrian Army as a chook vehicle, it ended up in Coober Pedy, in the back blocks of South Australia. After various adventures, it was purchased by one of our crew and is our next but one, project. We tasked ourselves today, with removing the Dodge's rear radio shelter and the cab. The process was not overly professional, but nonetheless everything came apart. The vehicle is now in three pieces, waiting for a good clean and a start to be made on the restoration plan. Back to the Champ - I’ve now completed the wiring front and rear - …. and today, I ran some jumper leads from the 24v Pinzgauer to the Champ’s battery leads, to see if I had successfully managed the task, or if I failed. It was a 50 percenter. I was able to get the ignition and oil lights glowing, when I turned on the ignition and the starter turns over, but the head/side/tail lights are not working. Probably just an earth somewhere, though given the fact that all the lights are non functional, it may be that the live wire (Aux Pos) from the Distribution Box, needs checking. Anyway, it’s probably not too much of a drama and I’ll have a good look at the wiring path during the week. The shed is also now home to a 4.2” towed mortar which was recently bought from an Artillery Historical Society. One or two items are missing from the CES, but we can fabricate them – it’ll be a good accessory to the jeeps in the fleet. Also made up a wheel alignment tool during the day, to check the alignment of the Champ's front wheels (and any other vehicles we restore) – I’ll try to remember to get a photo of it during the week. -
The Restoration of Austin Champ 1824
mazungumagic replied to mazungumagic's topic in Blogs of MV restorations
Started to connect the wiring thingameejig, a few days ago. I had done a little bit of this last week and actually bolted up the instrument panel, but then on the bike ride home, I started to realise, I may have been too hasty. So I unbolted the panel, slid the combination out a little and found there were some missing wires. I noticed for example, that the wiring diagram details the earth wire for the fuel sender and the panel lighting, is funnelled directly from the large distribution box earth, so having had that made clear, I ran a wire from battery earth directly to the Lucon connector behind the instruments, joining up the two earth wires previously mentioned. That fixed that ! There's a bit more to do, but I'll follow the wiring diagram, marking off connection on it, till the page is a sea of pencil marks. I have done the rear junction block and the front lights/horn, with all the wires now back at the instrument panel ready for the cut and the Lucon connectors. I managed to find enough of the little yellow wiring descriptors, which aids identification and now just need the essential double check, to ensure all the wires are connected to their mates. A pic of the instrument panel as at 4.00pm I’ve also been thinking about the 2 x 12 volt batteries and after reading the description of the battery box base (which I didn’t really understand), I’ve devised some battens to support the batteries and will cover them with a sheet of 5 ply, on which the batteries can rest. Might even add a rubber mat. also painted the last of the metal work - the canopy bows. Other than that, the day was spent soldering wires, cutting out a rear number plate holder for the Champ and for some light relief, removing a tyre from an old and rusty Dodge WC rim. This vehicle had been converted by the post war Austrian Army into a radio van, which subsequently found its way out to the diggings at Coober Pedy in South Australia – thence to WA. It’s our next project and some of our effort is now being diverted to the stripping of body from chassis. -
The Restoration of Austin Champ 1824
mazungumagic replied to mazungumagic's topic in Blogs of MV restorations
First up, we finished the parts painting – or so we thought ! It was only when we sat down at the end of the day to our usual refreshments, that the canopy bows were mentioned. Oops – they were primed the other day and hung up out of the way – so far out of the way, that they were completely forgotten during our very last paint ! A job for next week. A canvas hood has been ordered from the Worthington’s in the UK, to go with the newly painted canopy bows ! The snorkel got another coat, as the support rod and clamp hadn’t been done in DBG. The rear seat base was also treated at the same time A bunch more wiring was also completed, mostly concentrating this time on the instrument panel, ie the switchboard and gauges. I’ve still got a bit more to do here, mostly related to the lighting and horn, but managed to get the instrument panel back in place. It's a very tight fit and a bit of jiggling was required, but it'll probably be easier the second or third time around. I found a few problems with a test run of the Lucas SD 84 indicator switch, using a spare set of lights. Couldn’t get the organic tell tale light to function, when switched to the right. The lights would all blink as they should, but the internal switch light would not function. I guess there must be something awry inside the switch, or I wasn’t connecting it to the correct wires, so I decided to forgo the internal light and patch in a separate light located more centrally to the driver’s vision, ie in front of the steering wheel. The picture above, tells that story. The vehicle is now well on the way to being another finished product – I’ve been thinking of embellishing the vehicle, as it’s a bit bland and because I served in the Royal Tank Regiment (1RTR) in the second half of the sixties, I thought that would be the appropriate livery, with which to decorate the front and rear of the vehicle. Does anyone know what the respective tac signs (unit and formation) would have been for that period ? Any photos available ? I regret being inattentive at the time. -
The Restoration of Austin Champ 1824
mazungumagic replied to mazungumagic's topic in Blogs of MV restorations
Hello Rick(a)Dee, Your list of vehicles continues to be impressive ! Thanks for your help yesterday. So... onto progress to date - The last of the metalwork was attacked today – the rear seat base. It had been loitering in the darker area of the shed till now, but with the vehicle pretty much finished, it was time to remove the last of the rust and fix this item structurally, so that the rear upholstery can be attended to. The seat base is made of very light sheetmetal and as a result, it has weathered poorly. A couple of significant rust patches were evident where the design called for a double skin and there were a number of tears in the metal combined with some stretching and general springiness. First job was to cut out the rusty bits and make up new pieces to be sewn in. After a fair bit of work, the new patches were welded in and the result was quite satisfactory. As mentioned above the metal had stretched, where loads had been injudiciously placed and we tried with some success, to heat and then shrink the metal which resulted in a much firmer and flatter base. You can probably see evidence of the heated areas of the metal. Very satisfying when the metal does what it is supposed to do. The fuel tank and the guard were installed today, though not without some drama. Rubber strips were attached to the tank where it contacts the upper parts of the vehicle and above the bottom securing straps – perhaps that rubber may have been a tad thick (it was about 3/16”), because when the guard was lifted into place, we found it very difficult to locate the various bolt holes, at the rear of the guard where it is secured to the tailgate area of the body. So some re-arrangement of the guard was in order and sad to say, we were obliged to resort to a BFH. “When in doubt give it a clout – the bigger the doubt, the bigger the clout.” Using that motto, combined with a tightening of the tank securing straps, we finally managed to get all the components in place and have crossed off that job. A start was also made on the electrics at the rear RH junction block, though I didn’t get a photo of that, yet. -
The Restoration of Austin Champ 1824
mazungumagic replied to mazungumagic's topic in Blogs of MV restorations
We didn’t get a lot done today, though we did sort out the fuel tank. Decided not to use the POR 15 on the tank, as it looked very good on the inside, but in lieu we put a little petrol in the tank and checked for leaks. There were none, so we undercoated the tank and will top coat it next week, before installing it. I’ll use the POR 15 product on a Model T Light Patrol Car that I’m also restoring. It is a much simpler tank and only 10 gallons capacity, so swinging it around to swill the mixture into hidden nooks, will be much simpler. One of the work crew brought in his Chev Blitz as it needed a winch rope installed and we spent a little time during the day, doing that. The rope was 5/8” and went on relatively smoothly, after a trial run, which gave us the length we needed to fill the winch drum – there doesn’t seem to be any detail on winch rope length in the various Blitz manuals. Then we turned to the remaining section of the exhaust. I am fortunate to have an exhaust business located near me and they pretty much always have a bin full of offcuts, which seldom fails to produce the bits I need. It didn’t let me down this time either. I got a section with a right angle bend which I needed for the last part of the system, where it comes out of the muffler and exits near the left rear tyre. This was trimmed for length and test fitted before welding to a couple of flanges I’d made up and then bolted to the rear lateral bracket. The Champ now has a reasonable facsimile of the genuwine article. We didn’t make it for ANZAC Day (on tomorrow), but that was looking very unlikely quite a few posts ago. -
The Restoration of Austin Champ 1824
mazungumagic replied to mazungumagic's topic in Blogs of MV restorations
G'day Mike, One of the team has a cement mixer and we thought about doing just that, but the mixer probably wouldn't do the whole tank - as the tank is long and narrow, it would only fit into the mixer lengthways, so there would be areas at the mouth of the mixer and above which wouldn't see any of the secret ingredients. I suppose though, it would just be a matter of mixing one end for a few minutes and then end for ending the tank in the mixer and begin again. Must give that some thought - it might be easier on the team ! Jack -
The Restoration of Austin Champ 1824
mazungumagic replied to mazungumagic's topic in Blogs of MV restorations
First task today was the fuel tank guard which needed to be test fitted and then have the forward angle iron strengthener, tack welded, before being removed again to finish the welding on the bench. As has now become normal, very little lined up, probably due to the fact that the guard originated on a different vehicle and has also had a number of rust areas, patched. That would have caused a certain amount of distortion and the result was that one or two of the bolt holes in the rear, didn’t line up with the captive nuts in the body. That problem was soon eliminated, but we then found that four of the other holes (with captive nuts) which should have been in the rear body, weren’t. They hadn’t been noticed when we replaced the rear tow hitch panel. Anyway, that was soon fixed as well and the fully welded tank guard was then painted and left to dry. Next task seeking attention, was the exhaust system. As everyone knows, the Champ system has a flexible steel pipe between the forward exhaust pipe and the muffler. We used some (expensive) stainless steel pipe here and the complete contraption was test fitted with excellent results. Before that could happen however, the muffler needed attention. This seemingly enormous piece of kit, was well rusted at the rear flange. We wanted to use the original muffler we had and so we cut off around 25mm of the rear end of the muffler and welded on a new end plate, replacing whatever external and internal piping were affected, as we went. The result was pretty good and will hopefully provide a few more years of service to Champ #1824. The indicators have been installed – but not yet wired up. I used some spare light fittings I had saved for a rainy day, at the front and some glass lensed types at the rear. Last job of the day was to fit the inner windscreen, which took a fair bit of time as we found there was a clearance problem between inner and outer frames where they come together, at the bottom. We then noticed that a couple of the spot welds on the rolled steel edge at the top of the outer frame (into which, slides the inner frame) had broken away from the main tube on the right side and had to be removed for welding. Once that was done, we test fitted the inner frame and spent a good deal of time solving the fouling problem on the bottom of the frames. Finally got it more or less solved, but there is still very little room and that will be exacerbated, when it comes time to instal the rubber strip around the inner frame. We need to do more work here later. Also got the snorkel in place. The fuel tank saw a little attention today as well, with a start made on using the POR 15 internal tank sealer. Actually after reading the instructions, we shelved that task – there was talk in the data sheet about shaking the tank for twenty minutes, so there were no volunteers for that - yet. There was a large hole which had been punched in the front of the tank and “sealed” with a cork, so that seemed easy. The large soldering iron was found and we tinned up a bit of steel plate and sweated it onto the tank (hole). Maybe we’ll get started on the POR 15 application next week – I’ll explain to my four co-workers the meaning of teamwork, ie if each of the mutinous swine pitch in, we’ll only need to agitate the tank for five minutes each ! -
The Restoration of Austin Champ 1824
mazungumagic replied to mazungumagic's topic in Blogs of MV restorations
We had a reduced crew at work today, there is some flu/pneumonia outbreaks around and we have not been spared. Nevertheless, the task of bleeding the brakes was on the agenda and we managed to get that done without too many problems, though I must say the bleed nipples are not well sited. At the rear in particular, they are quite hard to grip with a spanner due to the many other bits vying for space there. Anyway, the brakes were bled and we have quite a good hard pedal, though it is only about 40mm from the floor, so there might be a need to do some more brake shoe adjustments. Some of the electrical cabling was inserted as well - mainly the big cables, from generator to generator panel and the one from the panel to the switchboard. The bridge weight sign was bolted up and one of the horns I have been preparing, has been test fitted I’ve been thinking about the position of the front indicators and found that there are few natural places for these. I’ve seen them on the front of the mudguards and bolted onto brackets on the side of the grill, but I’ve decided to place mine on brackets which I’ve now made up, to fit just above the bumper bar, using the two bolts holding each side of the bumper bar stays. I’ll include a pic of these next week, when I’ve got them finished/painted and fitted. -
The Restoration of Austin Champ 1824
mazungumagic replied to mazungumagic's topic in Blogs of MV restorations
After all the torment and fury of the past couple of weeks, we had a more subdued day today. Over the last week, the clutch linkage has been connected and a working clutch has been verified. The accelerator linkage has also gone in – that’s a doozy to install. It’s a job that would suit those equipped with universal joint fingers and ring spanners (wrenches) in lieu of finger nails. Nonetheless, another testing task completed. Headlights and sidelights are also in place. Then it was straight into the final few coats of DBG – which curiously, turned out to be gloss finish, in lieu of the usual satin that we’d been using. It is not of huge concern – the paint finish will be more resistant to weather, though there will be a contrast between the exterior body and the interior, as we painted only the exterior today, finishing off the third 4 litre tin of DBG, in the process. More than I expected to use, but a solid coating of paint on the vehicle. The job underway – Finished painting and back inside - More bits then went on including the air cleaner, which involved removing the carburettor venturi – not really surprised at that. Champ life wasn’t meant to be easy ! Most of the tyres/rims were removed and painted on both sides – noticed one of the tyres is flatter than the others and won’t respond to air pressure. The valve looks to be further down the valve stem than normal and that will probably mean pulling the thing apart and fitting a new tube. Just thinking how far we’ve come in this restoration, as we approach the finish line. Here’s a pic from Day 1 - -
The Restoration of Austin Champ 1824
mazungumagic replied to mazungumagic's topic in Blogs of MV restorations
Chris, On a normal engine/gearbox, you could fix the problem by jacking up the rear end of the box just a little and manoeuvering the mounts, to line up. As you'd be well aware, the suspension (torsion bars) on the Champ get in the way of that fix and don't allow a jacking point. You learn a lot by doing - if there was a second restoration (there won't be !), we'd be streets ahead. Jack -
The Restoration of Austin Champ 1824
mazungumagic replied to mazungumagic's topic in Blogs of MV restorations
The plan today, was a. to rub down the Champ body b. to give it the final few top coats, and c. to start the engine on the ground, check for leaks and oil pressure, then instal it in the vehicle. A tall order, given Murphy’s Law. We did roll the vehicle outside and give it a light sand in preparation for the top coats. Achieved that one. We also managed to get the engine started, though not without Murphy poking his head into our business. We had the motor on the ground and supported on a variety of blocks, as well as being held in place by the engine lifter. Oh, I should mention here that the radiator was in place and filled with coolant. After having tightened a few Jubilee clips on sundry radiator hoses, which were somehow overlooked, we rigged up power to the starter and wiring to the coil and the solenoid. Nothing happened. We took the starter off and opened it up to check the innards were working properly – which they were and it spun when we connected power and activated the solenoid. It was about then we realised we needed an earth to the motor and that we needed to make sure the starter was effectively earthed as well. There was a lot of new paint around all metal surfaces. Once that was taken care of, we started again and were rewarded by the sounds of an engine being turned by a willing starter. So, spark plugs back in, fuel up to the carby and a check on oil flowing to the filter and beyond and we were pleased to hear the engine cough to life. Another major milestone in the restoration story. The installation of the engine was a very time consuming operation and a frustrating one at that. For the uninitiated, I can tell you there is very little room in the engine bay, for the motor. It was a significant struggle to get the damned thing in – putting it politely ! We had to remove the clutch actuating lever – that can’t go on till the engine is in place. We found out that that little bit scrapes its way all down the nicely painted chassis rail, if left on. The lowest and smallest water pipe into the bottom RH side of the radiator was catching on the front engine mount and had to be re-arranged to go under the mount. The engine lifting bracket (described in the EMERs) had to be relocated to alter the posture of the engine, to angle tail down and various other bodges had to be undertaken to permit the engine to sit on its mounts. A great deal of mucking about then occurred, once we tried to get the engine mount bolts into place. It was a frustrating time, made no easier by the precise nature of the bolt holes – a little flexibility here wouldn’t have hurt anyone. The job was not helped by the proximity of bulkhead to engine - not much more than a zillimetre there. Anyway, we ended up getting all the engine mount bolts into place, despite one of the captive nuts on a (new) rear mount, breaking off (that shouldn’t happen, should it ?) – which actually made it easier to place a separate nut and bolt into the hole, unrestrained by an immovable captive nut. Up yours, Mr Murphy. Here it is in the vehicle – So we didn’t get to the point where we could give it the final top coats, but that’ll be a job for next week. At the moment however, there are a lot of ancillaries which can now be installed prior to the final coat and a start can be made on the electrics. One other small success story, is that I found something I didn’t know I’d lost. Another radiator turned up and I was surprised to note it had a filter in the neck, held down by a circlip. I didn’t have one of these in my radiator, but now I do ! Concurrently, the windscreen glass is being cut for the inner frame and the front seats are being upholstered. I'll do the rear seats once I've repaired the seat base. Next week a final coat, connecting lots of things up and resisting the temptation to go for a ride !