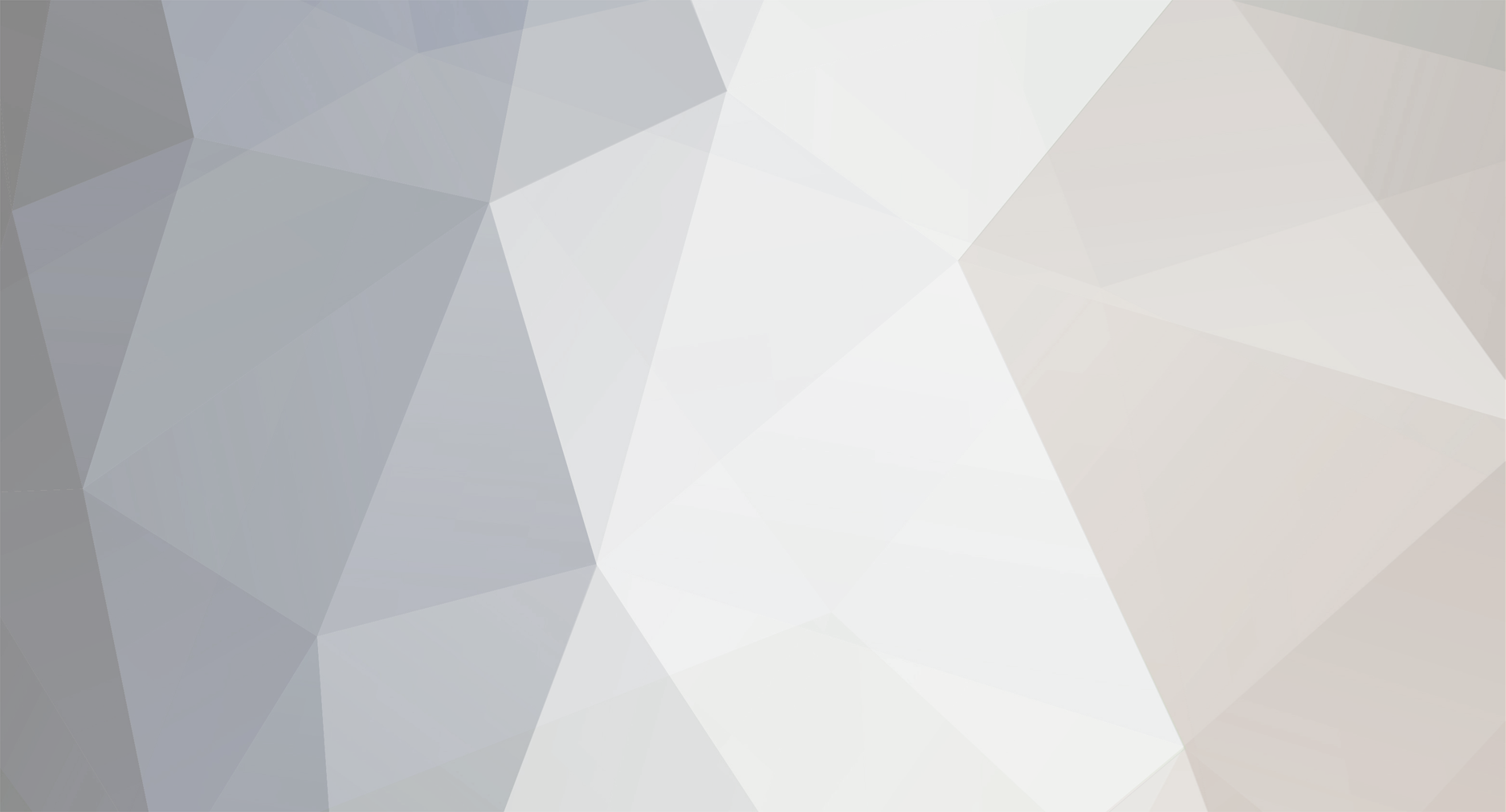
Doc
Members-
Posts
243 -
Joined
-
Last visited
-
Days Won
6
Content Type
Profiles
Forums
Gallery
Blogs
Events
Articles
Store
Downloads
Everything posted by Doc
-
I've been encouraged to share a few more details of the punching machine. So here you go... Close-up of the front of the turret: smallest punch is 1/8"and largest punch is 1/2" Full range of punches available. Can punch 1/2" diameter through 1/8" material. Doesn't say what material! Side View It sees a lot of use nibbling out gaskets, though you would never know as I swept up before taking the photographs.
-
So despite (or possibly because of) these uncertain times, I have found time to go into the workshop. Stopping short of rubber solution and sticky back plastic, I did my best "Blue Peter" and made a cardboard prototype handle for my repaired valve-chest cover. Kellogs "Fruit and Fibre", though other cereal boxes can also be used. Cut four blanks out of mild steel and punched the rivet holes using a natty little turret punch. Punch was found on the heap at our local scrapyard. Next to the fly-press and bent to shape. Two handles riveted into place. (1 coat of red-oxide primer on the mating faces first). Then a coat of red oxide all over. While I had the brush in the pot, the silencer brackets got a coat too!
-
Evening. Funny how most things yield when you show them the hydraulic puller. Pretty sure the part you require is on one of my brother's spare engines. Once movement restrictions have been relaxed you'll be able to come see for yourself. Was tidying my desk at work this week in preparation for "working from home" and stumbled across the list of new felt seals I had made for David's lorry. So, when the time comes, give me a shout and I can send you the list and put you on to the company that made them, or I can get them for you. Regards Doc (Andy)
-
So, via a circuitous route, I've been introduced to Geoff Lumb from Huddersfield. Whilst we have yet to meet, we've had long conversations by telephone. He's clearly spent an awful long time immersed in all things Clayton & Co and Karrier. Geoff was present when my lorry was recovered from Manor Farm in 1977. In the photograph below, he's the gentleman on the right of the picture. Does anyone recognise any of the other faces? Am feeling extremely grateful right now as Geoff has sent me this drawing of a "Petrol Motor Lurry To Carry 4 Tons" based on the Karrier chassis, and given me permission to reproduce the drawing here. Not only is the drawing fully dimensioned, but it also indicates the different timbers used in the construction, including Ash, Oak, Birch and Red Deal. I have re-drawn the lurry body in Autocad and superimposed it on the drawing of my chassis. The chassis length in this drawing matches mine! This is the first concrete evidence I have found of different chassis lengths. Also reassuring that when my chassis was repaired all those years ago, it was done to the original specification. Just look at the sizes of the timbers: Longitudinal Runners 6" x 3" x 10'9" long. Floorboards 1.1/2" thick Red Deal. Front Bolster 3" x 11.1/2" x 6'6", Rear Bolster 3" x 12.7/8" x 6'6" Headboard has 3 off 7" x 1" x 78" Oak planks and 1 off 9" x 2" Ash Rail. I assume that all other framing was Ash. Note: the body slopes up towards the back by 1.3/8" or approximately 1 degree. Curious. Am also working on a Solidworks 3d cad model of the body which may appear on here in due course.
-
Valve chest covers. Earlier engines were fitted with cast iron valve chest covers, but by the time my engine, #6616 had been built these had given way to pressed steel. Cost reduction is not just a modern phenomenon. The rust moth laid her eggs on them and it seems most hatched! That said, there was enough metal present to make one out of the remains of the two. The second will need to be made from scratch. Many thanks to Stuart for changing the gas on the TIG welder from Ar to Ar/CO2 mix and staying late after work to do the welding for me. Rotten corner excised from the "good" valve chest cover. Donor and remains Copper heat sinks clamped in place First tack welds Nice neat weld under trying circumstances - thanks, Stuart! After fettling with the Dremel Weld peened with a blunted dot punch to blend it in to the rust pitted substrate. Note there's two folded handles required. These were rivetted into position (rivet holes visible in this picture.
-
Marcel, My brother only has the lathe and the switchboard. Switchboard is Austin and has W^D on one of the meters. Differs from the Duxford example in that it is open, not in a cabinet. Also the voltage regulator is built into the panel whereas the Duxford example has the voltage regulator bolted onto the dynamo. We understand it was discovered in a motor repair garage. May have been W^D surplus equipment, re-purposed. Or may have been constructed by Austin for civilian use, using surplus W^D components. He is looking for the following tools: Silver Mfg Co No 24 drill Luke & Spencer grinder Wolf electric drill & stand He also needs an Austin 8 hp, 4 cylinder T-head radiator cooled 110v generating set with 3.5 kw dynamo and shunt regulator. Regards Doc
-
So I was hunting around online and came across this short video clip: https://www.pond5.com/stock-footage/item/87607821-dennis-and-karrier-trucks-parked-road-1918 This rang some bells... going back through some of the "Motor Traction" adverts on Page 1 of this thread, there's an advert for reconditioned AEC, Karrier and Dennis lorries, from which I've clipped a paragraph (below): Advert is from September 6th, 1920.
-
So at "Woolpit Steam" last year, my brother got a lead on a Drummond lathe of the correct pattern for his workshop body. The deal was that we had to find an equivalent lathe to replace it - it was still being used. So a slightly more up-to-date Boxford with all the ancillaries was duly found, dismantled and delivered to its new home. The Boxford was reassembled on site, meanwhile the Drummond was stripped and loaded in the back of the car. This has been thoroughly paraffin washed and allowed to dry before applying linseed oil to bring up the original paintwork. He has a 3-jaw and 4-jaw chuck as per the original specification, though not sure they are the originals, also the face-plate and a steady that can either be fixed or travelling. There's also a selection of change wheels, but not the complete set. These do turn up - patience is required. This lathe looks to have never has a treadle fitted. He is missing the original 110V dc motor, also the cast iron knee that supported it. However, everything else is in wonderful order. There's even the ASC requisition plate below the makers' plate. The weather was clement in Suffolk today and with the aid of our neighbour's fork-lift, the lathe was lifted into place. Preparing for the lift. This platform / side panel was the one which had the hole for the stove-pipe cut through. Note the temporary roof. Shelter from the sun (and rain!) at GDSF 2018. Carefully lifting into position. Note "War Finish" stencil on the end of the bed, just above the leg. Final position. Dimensions measured from the body at Duxford. Many thanks to the curatorial team there, who have been extremely helpful and accommodating.
- 120 replies
-
- 10
-
-
Steve, Thank-you for the contact details and encouragement. I've taken a look at Diane's website - her work looks first class! Doc
-
Thank-you for the recommendation. If you can PM me Diane's contact details that would be great. I'm now curious to know what patent details are referenced on the plate. Am wondering if it relates to Spurrier's torque tube patent GB190316919 (Lancashire Steam Motor Company, Leyland). Time will tell...
-
Ed, Thank-you. My torque tube has two small holes about two inches apart - must have had a similar brass plate. No doubt the rust got behind it and forced it off. Any chance of a rubbing of the plate? Perhaps I could get a reproduction one made. I do have this plate from the near-side chassis rail: The corners are damaged so I've soft soldered it to a brass backing plate to allow me to re-fit it to the chassis. Doc.
-
Ed, I noticed the following statement in your 2008 topic (bold emphasis mine): Chassis is in very good order having been kept dry all its life, not sure where to look for a chassis number - any ideas? There is one small brass plate on the prop shaft tube relating to a patent if I remember correctly. I believe axles are in their original locations but it looks like 2' has been chopped off chassis just behind rear spring hangers. Don't now why as wooden body extends beyond this. Any chance you can look out the patent number from the brass plate? While you're there, can you confirm the orientation of the bung for oiling the prop-shaft front bearing? See attached photographs... Oil bung #11077 shown at top My oil bung (removed in this picture) at the four o-clock position. Has there been a clarity / artistic license decision in the parts list, or is my torque tube orientation incorrect? Perhaps when I remove this part there may be witness marks visible on the spherical head. Thanks Doc
-
Steve, Thanks for sharing this. How to do the job safely without hurting yourself or anyone else. I tend not to like a loud "Boing" followed by the inevitable search for whatever went flying round the workshop. Doc
-
Steering Box Another item looking rather sorry for itself. The ribbed structure of the upper half of the steering box has formed a water trap. 40 years on and the rust had returned. One stubborn bolt refused to budge, so was drilled out. First wash revealed nothing particularly scary. Shafts run in hardened steel bushes. Ball thrust bearings were fitted either side of the worm. Everything was washed in paraffin, de-rusted with a variety of wire brushes of different sizes. Phosphate conversion coating was applied prior to painting. Steering box removed from the chassis Bolts removed. Stubborn one drilled and punched out, cover off, revealing the innards. After first wash. (Image has decided to rotate itself - who knows why!) Phosphate conversion coating. Red oxide primer, second coat. Cold night in the painting shed, so brought parts into the warm to dry. Under coat. Reassembly commences: Steering segment, shaft and bushes in place. Followed by worm, steering column shaft and ball thrusts. Top half of casing in place And finally the steering column.
-
Silencer Brackets The silencer is suspended from two chassis cross-members by brackets. The front one bolts to the cast steel support for the torque tube; the rear one is mounted on the arched cross member with its feet bent accordingly. Both original brackets survive, though the rear one was badly bent. The following photographs detail the straightening operation. Afterwards, both were cleaned up with a cup brush on the angle grinder before being painted with a phosphate conversion coating. In the forge. Thanks to my brother for taking the pictures while I was holding the burner. Getting nice and warm now. Initial straightening was done in the vice. Final tweaks were done over a stainless steel mandrel. The silencer was 7" diameter (same as the Leyland RAF type). I happened to have an off-cut of stainless steel the right size. Added advantage: the low thermal conductivity compared to mild steel made in-situ heating for those final adjustments easier. Both brackets took their turn on the mandrel, though the rear bracket needed more work. All cleaned up and with the phosphate conversion coating drying. Prior to heating these parts were in blue undercoat with just the barest minimum of rust coming through.
-
Thank-you for giving some thought to this, and your comments. The Karrier parts book uses the nomenclature "Relief Valve" although the component they describe is on the oilpump body, whereas mine is external to the engine, on the filter body. Incidentally the Commercial Motor magazine carried a very detailed and informative article on the Tylor engine in their 23rd December 1915 edition. Whilst they described the pressurised lubrication system, they did not disclose the operating pressure. For those of you lucky to possess an original instruction book (or AEC owners?) can anyone shed light on this, please?
-
I have previously made mention of the engine being stuck. Over the last year this has been "fed" regularly with a 50:50 mix of 30 oil and paraffin down the bores. Likewise, the various drilled passages in the crankcase were filled with oil. Valve stems and tappets have also received regular attention. While dismantling the clutch, the flywheel started to move. Some careful cranking while my brother was watching the valves determined that nothing was stuck, though the crank was tight. August 2019. The Karrier was pushed out of the shed and chocked. A long, heavy, split belt was put around the flywheel and N/S chassis rail and the trusty Fordson backed into the belt. The engine was hand cranked while the tractor clutch was let in slowly. The belt pulley on the tractor is crowned, so despite the flat flywheel rim, once everything was in line and the belt tight, things ran well. With a sump full of oil and two hours on the belt at between 100 and 200 rpm things soon loosened off. MVI_3148.AVI The spring was missing from the oil pressure relief valve. A light spring was selected from the box of compression springs. A steady 5 lbs pressure was maintained - plenty enough for bedding in. In due course a stiffer spring will be required. The eagle-eyed will spot some modern plumbing up under the magneto bracket. A pressure gauge and a drain tap. This location is on the end of the internal oil-way that feeds the timing gears. The tap allowed some oil to be let off periodically to clear any sludge / debris that might be present also as reassurance of flow.
-
Thank-you ever so much. What a fascinating array of adverts. Indeed the sort of encouragement that is welcome. Have just come in from a cold workshop, reassembling the clutch and ancillary parts. Will post on this when I'm back in Bristol. Now a cup of tea beckons.
-
Congratulations on joining the Leyland club. You have a lot of hard but rewarding work ahead of you. I got the early lorry "bug" helping my brother with his Leyland RAF type which he bought as 8 separate lots of spares from the Keeley sale. He has left over from this project the remains of two Ricardo type engines (like yours) which may be of use to you. He has had the oil pump, water pump and camshaft for his lorry. But there's a very good crankshaft and rods, still with lots of shims. Numerous other bits too. If you are interested, I understand that you can Private Message through this forum. Not sure how, I'm a newbie and haven't tried. Good luck with your project! Doc.
-
Clutch. The clutch required to come apart, as it was seized. Disassembly was in the following order: drive coupling, clutch stop cross bar (with leather braking ring), pedals and pedal shaft. It is clear that a previous owner did not possess a 1 3/4" Whitworth spanner; the use of a hammer and cold chisel had caused significant damage to the retaining bolt. Next the sequence was spacer collar, retaining nut, stop, operating bridle c/w bearing giving access to the large serrated spring adjusting collar. A spanner to fit this was laser cut from 6 mm steel. The parts book makes no mention of a locking grub-screw for the spring adjuster; once this had been discovered (the hard way!) things came apart readily. Spring adjuster coming out. When I started dismantling, the engine was stuck with the grub screw at 6 o-clock. Adjuster free. Cautious removal with intermediate fasteners in position. Didn't want a loud Zebedee-like "Boing!" and the spring disappearing into the darkest recesses of the workshop. The large aluminium cover fits into a register in the flywheel rim. This was tight. Going round with a hammer and hardwood block caused a crack to open up between the cover and the flywheel. Thereafter a lot of patience and WD40 and the cover was persuaded to come off. The clutch cone and centre were slid off the crankcase revealing a brand new lining material which a little red warning label advised might contain Asbestos. This lining was about 8 mm thick and bonded to the cone. It was clear that the lining was too thick as the clutch cone protruded about 1/2" from the flywheel face. Indeed this took up much of the clearance in the aluminium cover such that there was scarcely any movement available to disengage the clutch. The clutch cone was sent to Bristol Friction Services who were able to remove the existing lining and replace it with a modern non-asbestos material. They then put the cone up in a lathe and ground the lining back to the original dimensions. Clutch cone with new friction lining Fully engaged in the flywheel just a little but proud, but plenty of room for de-clutching. I had considered a leather lining. The parts list suggests leather was used, however the pattern of rivet holes in the cone, which is a little over 17" diameter, shows there was only a single joint. This would have been a large piece of leather, suggesting a man-made material was originally fitted. By way of comparison, the clutch lining in my Albion-engined Barford and Perkins D4 roller is in three pieces. Leather-lined Albion clutch cone for comparison.
-
Gearbox re-fitting The method adopted for re-fitting the gearbox was as follows: First the cross members were loosely bolted to the feet of the gearbox. (Cable ties identified their original locations - Front, Near-side and Rear Near-side) Next the mounting brackets were bolted to the chassis. The gearbox was wheeled under the chassis on a high-lift pallet truck and lifted into position. With a bit of wiggling, all the supporting bolts were driven home. With the gearbox in its final resting place (or so I thought) attention turned to the transmission brake. With shoes and linkage reassembled as it was taken apart, the pivot pin of the forked brake adjusting rod was fouling the rear cross member. Drawing the brake shoes forward on their pivot pins overcame this problem but created another: now the brake shoes did not sit correctly in relation to the brake drum. Something was wrong. Consulting the photographs, I had put everything back exactly as I took it apart. Despite that, it seemed that the cross members might be the wrong way round. My brackets were positioned [ ] The parts book showed ] [ Next a rummage through the 1977 recovery photographs. The back cross member was clearly visible in a rear 3/4 view, confirming the orientation should have been ] [ Cradle still in-situ after removal of gearbox From the parts list - not orientation of cross members in top right view The only 1977 photograph that shows a cross member clearly I was not prepared to drop the gearbox out of the chassis, so decided to change the brackets one at a time with the gearbox in-situ. The rear mounting bolts securing the gearbox to the cross member were withdrawn. With the weight of the gearbox supported by a chain block and strap the rear cross member was removed, turned and replaced. The process was repeated at the front, then all four mounting bolts were refitted. One consequence of this work is that the gearbox is now around 1½" further towards the rear of the chassis compared to when I took it apart. This makes sense of a few things: 1) It was not possible to get full travel of the gear lever in its quadrant or to fully engage all gears 2) removal of the front driveshaft was extremely difficult with scarcely any free movement 3) the rear driveshaft had a lot of movement in it, as if the front bearing had collapsed, but, after withdrawing the shaft, the self aligning ball bearing was intact. It appears that the shaft was so far forward that the bearing was not engaged in its housing. Hopefully there will be no further surprises when I come to reconnect the drive shafts. But that is a long way off...
-
Wet and windy in Bristol; "staying indoors" weather. Which gives me the opportunity to sort through the photographs and bring the story a little bit more up to date. Like most vehicles of its age, the Karrier has a clutch stop immediately behind the de-clutching mechanism. It takes the form of a piece of spring steel, bolted across the pedal shaft brackets, onto which is riveted a leather ring. Upon withdrawing the clutch, a brake disk on the clutch shaft contacts the leather pad slowing the transmission. (Visible in the first photograph of this Tuesday's post on gearbox removal) The original leather was rotten and required replacement. I remembered having seen a description of the manufacture of new leather oil seals in "handy1882"s Vulcan VSW 30cwt 6x4. post (before it was comprehensively vandalised by the Photobucket corporation) so decided to have a go myself. There's a 1/4" thick spacer ring between the leather and the spring-steel bracket. A square of leather was rough cut and bolted on before being chucked up in the Harrison lathe. A scalpel blade in a parting off tool holder was adjusted for height before being shown the leather. Slow speed, hand feed on the compound slide. Trepanning the centre out of the leather And out it comes! Riveting underway; bolts removed one at a time, holes counter-bored to keep rivet heads below the surface of the leather. Computer insists on rotating this image for reasons I cannot fathom. Actual photograph is landscape. Huh?? Riveting done. Just the paint to touch up.
-
Off topic... but no, it's radiator cooled. Two tanks at the rear: the larger one was for water for sprinkling the rolls, the smaller one was for fuel storage. Paraffin could be transferred from here to the much smaller running tank close to the engine.
-
Some more pictures from late spring 2019... The blue paint applied by the previous owners whilst not particularly attractive has kept a reasonable check on corrosion. Many parts only required paraffin washing, rubbing down and re-painting. Some steel parts had rust coming through. These were generally cleaned up with an angle grinder and cup brush before being treated with a phosphate conversion coating prior to painting. A few parts required some remedial work. Below is the "Foot brake shoe stop bracket" in Clayton nomenclature. It bridges the brake caliper pivots also the setscrews that adjust the rest position of the calipers bear against this part. It is clear that part of this casting is broken away. Fortunately it is cast steel, so an over-size repair piece was welded on and milled to shape. Now repaired and painted. Sorry for the quality of the picture... Small parts in the paint shop Here you will see not only transmission brake and drive shaft parts but also gear selectors, linkage, gear lever and handbrake lever.