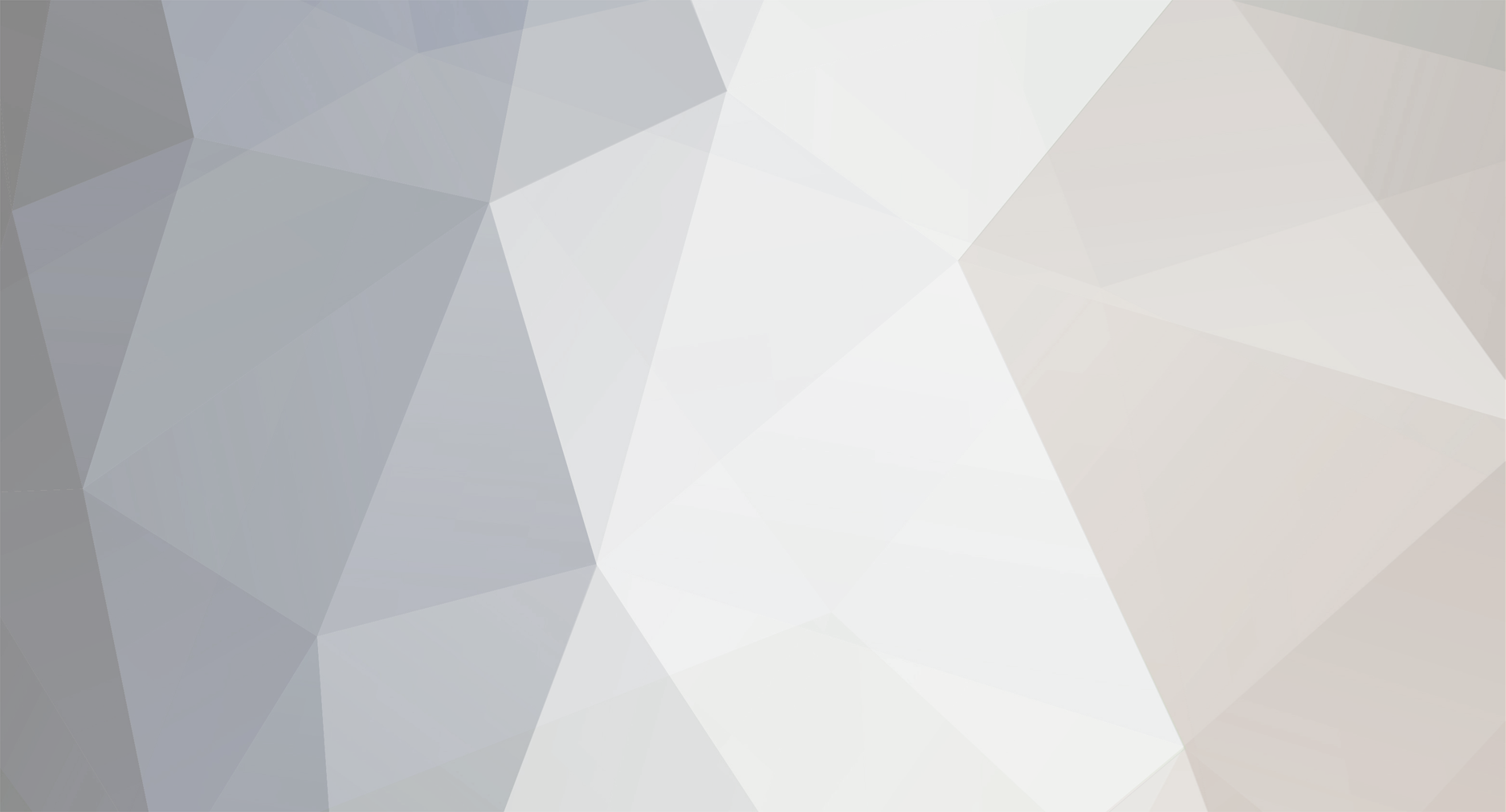
diesel1
-
Posts
165 -
Joined
-
Last visited
-
Days Won
1
Content Type
Profiles
Forums
Gallery
Blogs
Events
Articles
Store
Downloads
Posts posted by diesel1
-
-
Im sure they will hold up ok, when I get time I will be put a section of 15 on the sabre and abuse them as much as possible on the concrete, I have some abrasive concrete in my yard, if they survive that they should survive anything !
-
-
-
You would be very welcome!
-
I have one, will pm you some pics
-
Thanks for that information everyone!
Regards Andrew
-
-
Anyone know the weight of a track section or complete track, need to know for shipping.
-
Wanted, your old used, worn out track pads, wanted for the backing plates. For money of course!
-
I have 2 new sets of cvrt track that I'm thinking of selling, not sure what they are worth so message me with your offer.
-
Anyone know how bigger job it is to change a gearbox in the CET?
-
4 hours ago, SebBrady said:
Hello all,
Just to keep this all updated and show this isnt a pipe dream! Got a final set of drawings back from the factory. I am now in the process of working out how to bill anyone who is interested in the pads so that we can get the process made and get the final price per pad nailed down.
As mentioned at the start I am not in this to make any money at all and just want to help everyone out if possible! Getting a new supply of pads would be a great benefit I feel to the community.
If you know anyone who wants to join in on the order now is the time. As once I have committed to the mould that is when we agree the pricing and get them ordered. Looking like the cut off if work is kind to me will be January/Feb and delivered a couple weeks later.
Thanks for your patience just doing this all in my spare time amongst other things is slowly taking its toll!
Thanks
SebWill the backing plates be totally flat steel or curled up at the edges like the original plates?
-
1 hour ago, teletech said:
It's the bonding primer that's hard to get, without it it won't work, polymer won't bond to rubber well enough without the primer, I've tried it.
A company in U.K. can supply me with the primer but it's £250 for just under a litre, they get it from the states, I've ordered some from the states and it's a lot cheap than that but still expensive.
Plus, when the primer comes and say it doesn't work as well as it should then it's been a expensive lesson.
-
19 hours ago, SirLanceUK said:
So Interested in this so any information is gratefully received. I am looking in to sorting out some CVRT track and "repadding" would really make some economic sense of course providing the track link is up to it, (wear and tear and “good” bushes).
At the moment all the work in making a track like new is starting to look like a more expensive option.
Lance
Next week, I will have a go at recapping a cvrt track section, will be interesting to see what it turns out like, will drill holes into the old rubber after I have cleaned up the pad surface, mould will be easy to make, but will want sealing on the track section with silicon maybe so the liquid polymer does not run out before it starts to set, then removed after 24 hrs, then would need testing, my vehicles are put away for the winter so testing would start in spring or I could post the section to someone to try it out.
-
Sounds good, keep us informed with updates as you get them!
Andrew
-
Any more news on the pads Seb?
regards andrew
-
I've only done full pads at the moment, I did do a test piece by pouring some polymer into a mould sat on top of a old pad that had been cleaned up. It didn't seem to have much hold after it had set.
If recapping pads, the old pad needs to be cleaned up really well, then a special primer needs to be applied to the surface before pouring the polymer. I've got some on order from the USA,, cannot find anything similar in this country but I'm sure there will be somewhere.
I need to recap some pads and test them properly before making too many and finding there no good. Making a new pad is a lot better, but a recapped pad is a lot cheaper to make.
Im using a PMC-790 industrial liquid rubber compound .
Spray a wax based release agent in the mould and leave to dry, mix the part a and part b polymers together making sure they are above 23c, also the mould needs to be warm, once poured the polymer will start to set within 5 mins. I have a hot box for food, bought off eBay for £40, can be kept at a constant 50c for 24 hrs, will hold about 12 mounds.
Will post pics of the mounds tomorrow, easy to make, made another 2 in about 30mins the other day, I now have 10.
Cvrt pads will be very difficult to do, I've some need doing but will give it a miss!
-
25 minutes ago, diesel1 said:
The other day I made 2 fv430 track pad moulds out of steel, after researching the correct type of polymer rubber to use with a shore hardness of A95, I purchased some.
I used an old backing plate with the rubber removed, sand blasted the backing plate to remove all the rust, bolted it in the mould, and poured in the polymer mix. Didn't add any black colouring, as this is just a prototype pad.
I put the moulds in a sealed tin and put on top of the radiators for 24 hrs, they were at a constant temperature of 35 c.
Thismorning I pressed the pad out of the mould, I was impressed how well it looked, seems identical to a new pad in looks and hardness.
Im going to make 5 half worn pads and put them on the abbot to see how well they do.
It was all very easy really.
Andrew
Would look a lot better with the black pigment in it.
-
The other day I made 2 fv430 track pad moulds out of steel, after researching the correct type of polymer rubber to use with a shore hardness of A95, I purchased some.
I used an old backing plate with the rubber removed, sand blasted the backing plate to remove all the rust, bolted it in the mould, and poured in the polymer mix. Didn't add any black colouring, as this is just a prototype pad.
I put the moulds in a sealed tin and put on top of the radiators for 24 hrs, they were at a constant temperature of 35 c.
Thismorning I pressed the pad out of the mould, I was impressed how well it looked, seems identical to a new pad in looks and hardness.
Im going to make 5 half worn pads and put them on the abbot to see how well they do.
It was all very easy really.
Andrew
-
Anyone got a fv180 CET for sale or know of anyone selling one?
-
Also, diesel will be around for a long time yet due to agricultural and construction, will be a long time before they can make a agricultural tractor run on electric for 12 hrs straight!
-
Was thinking about making track pads back in 2016 after seeing the guy in Australia making them, the video he made was interesting. He used a polymer supplier in Australia, he used a primer brush on chemical to make the 2 part polymer mix stick to the existing worn rubber if he was only building worn pads up.
Finding a similar polymer in this country was the difficult part, doing a search on the net makes thing very difficult, a little knowlage in polymers would help, I have non.
The easy bit for me is making the moulds, I would remove the old rubber off the pads and use the existing backing plate, easy!
-
6 minutes ago, terryb said:
choosing the right medium is critical, i seem to remember in trials, a polymer gave the best results.
don't forget the nylon washers!
Yes, a polymer with a 95A shore hardness
-
1 hour ago, terryb said:
gents, there is already a guy down under manufacturing and selling pads
details are on the 432 forum
Yes, I read about this topic some time ago, but wouldn't the delivery costs from Australia put the price of the pads out of reach?
Home made track pads
in Tracked vehicles
Posted
Thanks, release agent was rubbish, I now use grease or gear oil, works a treat.
new pads have about 8-9mm of rubber on at there lowest point, does not seem much, I'm making them with 12-13mm, also will be testing some with 15-16mm