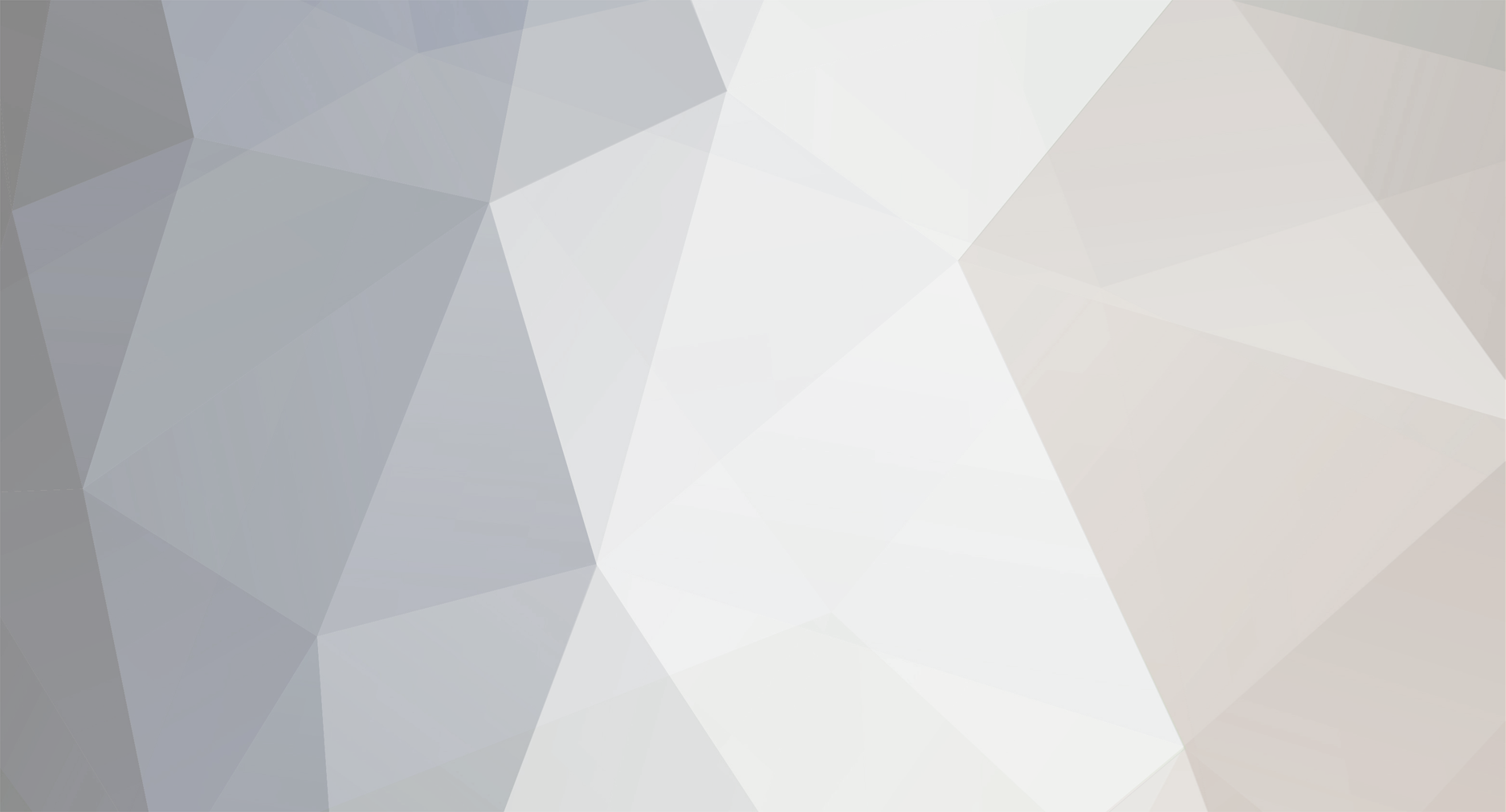
BenHawkins
Members-
Posts
861 -
Joined
-
Last visited
-
Days Won
3
Content Type
Profiles
Forums
Gallery
Blogs
Events
Articles
Store
Downloads
Everything posted by BenHawkins
-
Yes, 24 years old and 210k miles. Might consider it run in before too long.
-
ProFormance Metals have been very helpful and supplied the 8swg tube very quickly at a reasonable price. I have made new bolts and castellated nuts to complete the set for the ball joints. The ball on the drop arm is a good fit in one of the sockets. The other socket is a rattling fit on both balls (slightly worse on the one in the photo which is a little worn). I will check what other balls I have in stock but expect to end up making an oversize ball.
-
I have been a bit distracted this week, the weather has been good so I did some trench digging for the smithy and repointed approximately 20m2 of brickwork (long overdue). One of the modern cars needed some work for the annual MOT test (perhaps modern is the wrong term as our everyday cars average over 20 years old), but I did manage to machine the coupling for the speedo drive. The speedo cables were threaded 3/4x26tpi and the drive I am copying had the bracket threaded 1-1/6x26tpi.
-
I don't remember seeing anything on early J types/L4 engines during my visits to the archives but I will go through what I have and see if there is anything relevant (I tend to photograph everything I can, if permitted). Visiting archives in the UK has been nearly impossible for a year due to the Covid situation; hopefully access will improve later in 2021. I have more Thornycroft stuff to go through so I might turn something up. For one of my other projects I put in a request to the Toyota museum in Japan earlier this week; they responded within 24 hours having taken 20 photos of a vehicle for me - Japanese efficiency.
-
Sorry, yes 8swg does appear to be available. Not through my usual suppliers so I will have to shop around.
-
For the drag link I had expected the braze to be holding the tube in place fairly well. However as I machined off the tube it became obvious that there was quite a bit of clearance between the original 1-1/4x10swg tube and the forgings. As I turned down the diameter of the tube it started to tear so I peeled it off. The braze was only at the very end. I believe the first end was as it left the factory, the second end had been repositioned as part of the trailer conversion. For this end I used an angle grinder to thin the tube on both sides and then peeled it back. The braze had penetrated a little deeper on this end. With the tube removed it exposed a series of holes and chisel marks from the last time it was removed. In this photo I have already welded back on the 3/16" thick piece I cut off the end during disassembly. I then filled in the holes and grooves with some more weld. Initially I had just intended to silver solder the ends into some new 1-1/4" x 10swg tube. However the tube I have been able to purchase is on the bottom limit of thickness so the inside diameter measures 1.025" and once I have cleaned the forgings back they are around 0.975" diameter. Such a gap is a bit wide to expect capillary action to draw the alloy into the gap. Something to think about as there are plenty of things to be getting on with before I need steering. Suggestions welcome.
-
Thanks for the suggestions, I think the face is celluloid. I am much more at ease with metals and not sure if pigments in wax might transfer into the face Some time ago I cheaply purchased a pocket watch holder, it was missing the majority of the insides but still had the velvet in the front section so I purchased some more to match. One turned up on eBay recently so I was able to see how the cushions should look. There is an outer ring of wood that is fastened in place with two wood screws; covered this with wadding before fitting the felt and then stitched a small circular cushion to fit in the middle. Then there was the simple job of fitting it in the cab.
-
It is a 30mph Smiths speedometer. I purchased it at the Banfield auction right at the end of the first day. The auctioneer really wanted to finish so ran through the final lots at a fast pace; I think this is the only reason I could afford it. The red 12mph speed limit is quite faded and I cannot decide whether to paint it back in. One of the things I really like about the speedo is the second pointer that records the maximum speed achieved. The rest button can be locked off with a lead tag. The owner of the lorry (Ernest Shentall) was a JP so I could well imagine him choosing this model so he could keep an eye on his drivers. After drilling and tapping the split pulley I mounted it up on the milling machine and bored it out to fit the propshaft. I clamped some packaging card between the two halves to make sure it would clamp at the nominal diameter. I skimmed a bar end of steel to the same diameter as the propshaft and clamped the pulley onto it. This may have been good enough for the turning forces but I decided to drill a radial hole in the steel and tapped the hole 1/4BSW, then fitted a screw so the pulley could not rotate on the shaft. I skimmed the belt surfaces and gave them a bit of a polish, just following the shape of the casting by eye. I also started machining the belt tensioner parts. The bearings are in the post; I will finish it when they arrive.
-
I finished rebuilding the spindle on the Bridgeport milling machine. Some bar ends of aluminium out of the scrap bin have been machined into fixtures for the radiator sides so I can machine the mating surface flat. I sent a pattern for the radiator filler cap to the foundry along with a box of other patterns and was able to pick the castings up whilst passing on Friday. It didn't take long to machine it to size and knurl the edge. The 1/8" hole in the middle is so it can be rivetted to a chain. When I worked out these radiator caps were just a push fit it made sense that CP&Co only fitted the Commercial Motor Users Association mascots to the Leyland radiators; theses caps are probably not secure enough for a mascot. Despite the poor weather forecast for this weekend we were able to do a bit more towards building the smithy. I need to get that built so I have somewhere to install the fly press and can start punching out radiator gills.
-
I was able to get the patterns dropped off at the foundry, and collected the castings as part of an essential journey on Friday. Quite pleased with how well they have turned out as they had some of the thinnest walls I have attempted. The large pulley is now finish machined, there are still a few hours of work in the other parts.
-
I have just purchased a photo of a Dennis WO Subsidy lorry in civilian use. It shows the lorry crossing Conwy suspension bridge which certainly makes for a nice photo. The lorry is operated by Co-Operative Wholesale Society Ltd
-
We are slowly collecting parts and information for this project. The Thornycroft BT with T4 engine was not made in large numbers and shares very few parts with the post-WWI model (although the three speed gearbox appears to have been kept for a few years before the (very different) four speed gearbox was adopted. I identified this negative on eBay as being the same model so purchased it. According to the Thornycroft records this BT Box van was chassis number 1806 and fitted with engine T4-458. Period photos can be just as useful to restorations as the parts books and drawings.
-
I am sure manufacturing veteran lorry parts is the perfect way to make a small fortune; I just need a large fortune to start with. The punch tool has arrived safely from Andy. Fortunately I have been given a flypress but I need to set it up somewhere. The weather was good this weekend so we have done a bit more work towards building a Smithy at the bottom of the garden. Hopefully we can get the other walls built and a roof on in the spring. When the weather improves it is nice to roll the lorries out into the yard to work on. Linking up the steering and brakes would make this easier to achieve. The original drag link came with the chassis but it had been shortened as part of the trailer conversion. There was a corroded hole just over 6" from one of the joints where it looked hollow so I cut through there. Annoyingly it was in fact a shallow drilled hole. Which means I have shortened that bit by just under 1/4", I might weld it back on but I am certain the remaining 6" length will be fine. At least I could measure the location of the other joint and cut in a more sensible location. I was then able to clean up the centre drilled hole. The hole centres worked well for the faceplate on my little RandA lathe. These lathes were sold through Gamages for motor repair work in the 1920/30s so it is always nice to use it on the vehicle projects. Still more to take off to get back to 1" diameter so we can silver solder into a new length of seamless tube.
-
There are a few reasons I put the primer on first: 1. I find the pattern coat does not sand easily, clogging the sandpaper. The primer seems to be better in this respect. 2. Bondaprimer is quite thin and runs into any porosity left in the print. I know I should really run the print again if I can see a poor layer but as my patterns generally only need to be good for one casting it seems adequate. 3. I virtually always have something to prime that I have made in metal so I like to paint everything I can without cleaning the brush. Anyway, they are now in pattern coat and have been given a quick polish with a nylon abrasive pad. I will have to see if I can drop them at the foundry as part of one of the permitted essential journeys.
-
This week we have printed the parts for the larger pulley patterns on the speedo drive. These latest parts still need some more sanding and painting before the whole lot gets a coat of pattern coat.
-
The Chinese long series 20mm end mill arrived so I have milled the header tank to length and given it a bit of a clean up with some wet and dry paper. I am not sure how polished the radiator should be. I have done some work on the fittings as well. The overflow pipe needs to be shortened but that will wait until I have fitted the filler cap. The filler cap just pushes into the tapered filler neck and is connected to the overflow pipe with a chain so it does not get lost. I am still trying to purchase 0.25mm tinplate for the gills in sensible quantities. It should cost around £2/kg or around £50 for the whole core. Some negotiation required as I will need to take on many more projects to use up a minimum batch quantity of 350kg.
-
It is less deep than a War Office Subsidy 3 ton vehicle at 18 feet. Still planning the next garage. As there are no events on the horizon I have been trying to finish off as many small jobs as possible on the vehicles. Having bolted the speedometer to the dash a couple of months ago I pondered how best to link it up. My gearbox is from the early 1920s; the only difference from the original being the addition of a speedometer take off. It is quite corroded but probably repairable, however it does not match the speedometer ratio. The original speedometer (if fitted) would have been belt driven so I have started making the patterns for that instead. It consists of a split pully to clamp onto the prop shaft and a hinged arm with spring carrying another pully (not yet made).
-
Thanks for all the information, I guess I will punch a couple of hundred out by hand and decide if I would prefer to automate it.
-
Many automotive manufacturers were using the smaller across flats head sizes before it was adopted in the standards. There is a 1924 Commercial Motor article describing this but I have some evidence it was going on as early as 1906.
-
I have started a conversation with a very knowledgeable solder dipper. He stated that for early radiators the tubes were usually solder tinned so the gills could be threaded on with flux; the assembly was then put in an oven where the solder would fix all the gills to tubes. With that information in place it explains why virtually no solder is visible on the gills of my 1908 Singer radiator. This radiator is the closest in construction (horizontal tube) and age (1908) that I know of. Dipping the whole tube would offer better corrosion protection.
-
Merry Christmas! Thanks Andy for all your work on this. Tin plate seems like a good idea, my 1914 Dennis radiator showed some signs of tin or lead on the gills (possibly just solder) before I painted it. My 1908 Singer just has plain steel gills suggesting they were not dipped. I once tried a repair on a gilled tube with a propane torch so know that is a bad idea; the thermal mass of the gill is too low so they burn before the tube is heated enough to solder. A hot air gun will almost certainly be fine but I need to try that. The glamorous assistant purchased a White and Poppe catalogue for me. Here is the page for the engine in this project.
-
I should think so, they look great. Sufficient coffee will also be expensive so I will have to wait until the steel stockholders reopen.
-
-
3/32 but as you spotted I think the original was less.
-
Thanks for everyone's effort on this. Here is a photo showing the recess on the profile from the underside on the "new gills" Here is the best image I have found of the gills used in 1908. I am only reproducing a very small amount of the photo as I am not certain of the copyright. I could easily convince myself that neither the circular (half toroid) feature or the turned over petals are present; I think both these features are to give consistent spacing (spacing looks fairly inconsistent in the photo).