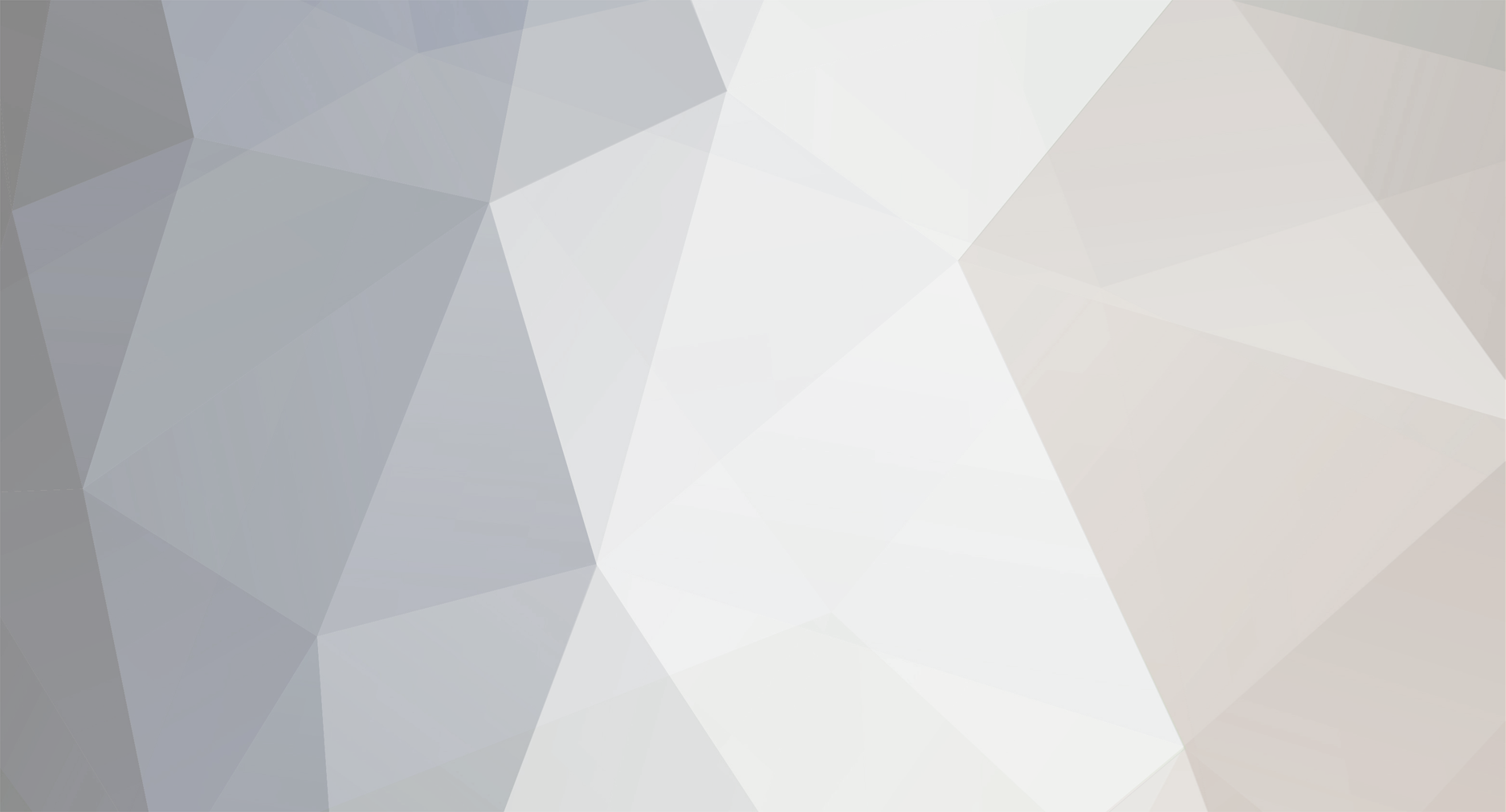
BenHawkins
-
Posts
861 -
Joined
-
Last visited
-
Days Won
3
Content Type
Profiles
Forums
Gallery
Blogs
Events
Articles
Store
Downloads
Posts posted by BenHawkins
-
-
Did you have to soak the felt seals in oil before fitting?
I don't think this is essential for felt seals but I always at least dip them in oil before fitting. It should prevent them rusting to the shaft as it could be years between a component being assembled and the vehicle being driven.
The welding of the second transmission brake arm is complete so it was all loosely put in place to check I had the alignment right this time. It all looks to be OK.
The arms then had to be removed for drilling and tapping 1/8 BSP
To accommodate Rotherham's screw down greasers.
-
Gravity naturally wants to make the brake shoes rotate on their pivots allowing the tops of the shoes to rub on the drum even when the brake is released. One of the holes is tapped 7/16 BSF so a set screw can be used to limit how far the shoes rotate. The other hole carries a spring and presumably this prevents the shoes from rattling when the lorry passes over bumps.
I though the arms would be better in steel. The steel foundry I use is very slow (possibly as long as six months for a casting). The laser cutters usually have the profiles ready for me in 3 working days.
In terms of man hours to make the pattern or fabrication they are probably fairly similar in this case.
-
I have machined some bosses from EN3 steel and welded them to the S275 steel laser cut profiles to complete the first of the transmission brake arms. It has been blasted and primed but I still need to repeat the procedure for the second one.
Opening the holes up with a reamer should sort out the minor misalignment of the various parts.
-
The gearbox was manoeuvred and jacked up to height on a pallet truck
And then some 5/8BSF bolts were modified to fit around the fabricated reinforcements. I still need to modify four more bolts and fit Grover washers and split pins.
The final job for this week was drilling and tapping the universal joint hub to accept a lubricator.
-
I have collected another batch of laser cutting. This has included profiles for the brake arms so these were checked for alignment.
There was also one for the front cover on the gearbox. I am considering mounting a similar support frame at this point.
The gearbox was lined up under the chassis and the shaft that connects to the gear stick marked for trimming.
-
I fitted the transmission brake but then found there was not enough space left for the selector rod cover. Luckily when I checked I had left the drum about 1/4" deeper than the brake shoes as I was not sure what the exact position was meant to be.
So the brake drum came off, was mounted on the lathe and 3/16" was take off the back face.
This then left around 1/8" clearance, and the drum approximately centred on the brake show pivots.
-
I had a couple of lunchtimes to fill whilst waiting for bearings to arrive. One was used to drop the flywheel casting off at a machine shop with a lathe big enough for the job. The second was used to machine a cavity in the centre of the universal joint hub to allow the grease to pass from the screw down greaser to the oil grooves in the pins. This was done with a T slot type cutter and a rotary table.
I just need to drill and tap for the lubricator now.
-
I have had new felt seals punched out for the input and output shafts.
The input shaft seal is retained by a washer with six 3/16BSW screws soldered in and nuts fitted on the outside.
Just the output shaft cover and transmission brake to fit.
I had to stop there and tile the kitchen; the glamorous assistant can have strange ideas about prioritisation. This gearbox has needed repairing for many decades, I have only been putting the tiling off for a couple of years.
-
-
-
The photos are not too exciting this week as I spent much of it in Warsaw.
After some more cleaning one of the bearings on the countershaft was still noisy so we pulled it off and pressed a new one on. The output shaft bearings were also noisy but I don't have one of the replacements yet.
But at least I could cut out the new gaskets.
-
I have picked up the flywheel casting. It is quite heavy (ca. 70kg) so can stay in the boot of the car until I drop it off at a machine shop (sadly, it is too big for my lathe).
After bolting the stuffing box to the front of the gearbox I was able to push down the detent plungers with a screwdriver and push in the selector rods; starting with reverse and fitting the taper pins to secure the selector forks. Reverse uses a lever that pivots on a shoulder screw through the bottom of the casing.
I then proceeded to fit the other two selector rods & forks.
But as one of the bearings is noisy I have not fitted the shafts and gears yet.
-
I was sent this photo of some Carter Paterson vehicles recently and it shows them carrying radiator badges.
So I have found this one. It is in fairly nice condition but there is a little damage to the enamel. Perhaps I need to look into the process of restoring the enamel.
As I was visiting the foundry I have had the missing cam follower sleeves cast for the engine. No rush to machine these but another part in progress.
-
There is a hole in the bottom of the gearbox to allow the taper pins to be extracted, it also gives somewhere for the end of the taper pin reamer to go.
Unfortunately one of the taper pins has never properly lined up with this hole so although it was started in-situ it had to be finished on the bench. Once this hole was reamed out to remove all of the previous hole I found I did not have a taper pin to fit. I have ordered some more and this will give me a chance to clean the swarf out the gearbox and start making gaskets.
-
I want to fit the gearbox fairly soon but the selector fork was not fitted to the new selector rod. We put the shafts and gears back in the gearbox so we could make sure we were putting the holes in the right place.
The selector fork was already drilled and tapped 3/16BSW so I used that hole to clamp the fork in place whilst marking the hole positions.
Then took the selector rod out again, used the centre finder to pick up my previous marks and drilled the pilot holes.
-
-
-
-
-
We have been thinking about the cab build. My original sketches based on the catalogue and factory photos looked OK but I was not certain enough to commit to buying and cutting timber. Spending a few pounds on a couple of sheets of MDF seemed like a sensible idea and I cut them out with a jigsaw to see how it compared to the factory photo.
Bringing it outside to get a better look at the proportions.
Not too much space wasted between the door frame and the cab!
It looks about right.
And I have begun to modify the frame to allow for a more sensible clearance.
-
I centred the clutch on a rotary table to centre drill the holes for the clutch hub etc.
When I built up the old clutch into a pattern I had to reverse the taper so it would pull from the sand. With the head tilted to 12 degrees on the milling machine I decided I could return it to the original design.
After a few hours.
And finally back to a consistent wall thickness.
-
Nice progress Ben, I really enjoy your threads as I do like to see how parts are machined with cunning setups :thumbsup:
Oh and I too have a shaper :-D
Thanks Bernard, I certainly enjoy the challenge of making the parts with what I have available.
I could survive without the shaper but it is a cheap way to make swarf (no expensive cutters) and can often get on with the job whilst I am working on something else.
-
-
The boring head was then used to open the hole up to around 0.990".
The hole was then reamed out to 1"
Trial fitting of the drive pin
The procedure was repeated for the second hole but a clamp was also used. This hole partially intersects the first one and I was worried the loads may be higher when breaking through.
And trial fitting the shoulder bolt. This bolt had to be polished slightly as it was a few tenths larger than 1"
1914 Dennis Lorry
in Pre WW2 vehicles
Posted
The brake parts have been painted, the split pin holes cleared out and slotted nuts sorted out for the various components. New adjuster bolts need to be made as the ones I have work out to be slightly too short and the heads are no longer hexagonal.
The machine shop working on the flywheel called me up. They have uncovered a void in the casting.
It is probably about 30mm long in total; continuing below the machined surface around the circumference. It will not be entirely machined away and if it was slightly deeper in the casting I would never have known about it.
The void is in the engine end of the flywheel (and therefore the thickest part). Obviously there is a need to balance the clutch but I am unsure if there is any reason not to proceed with the machining and continue to use the casting.