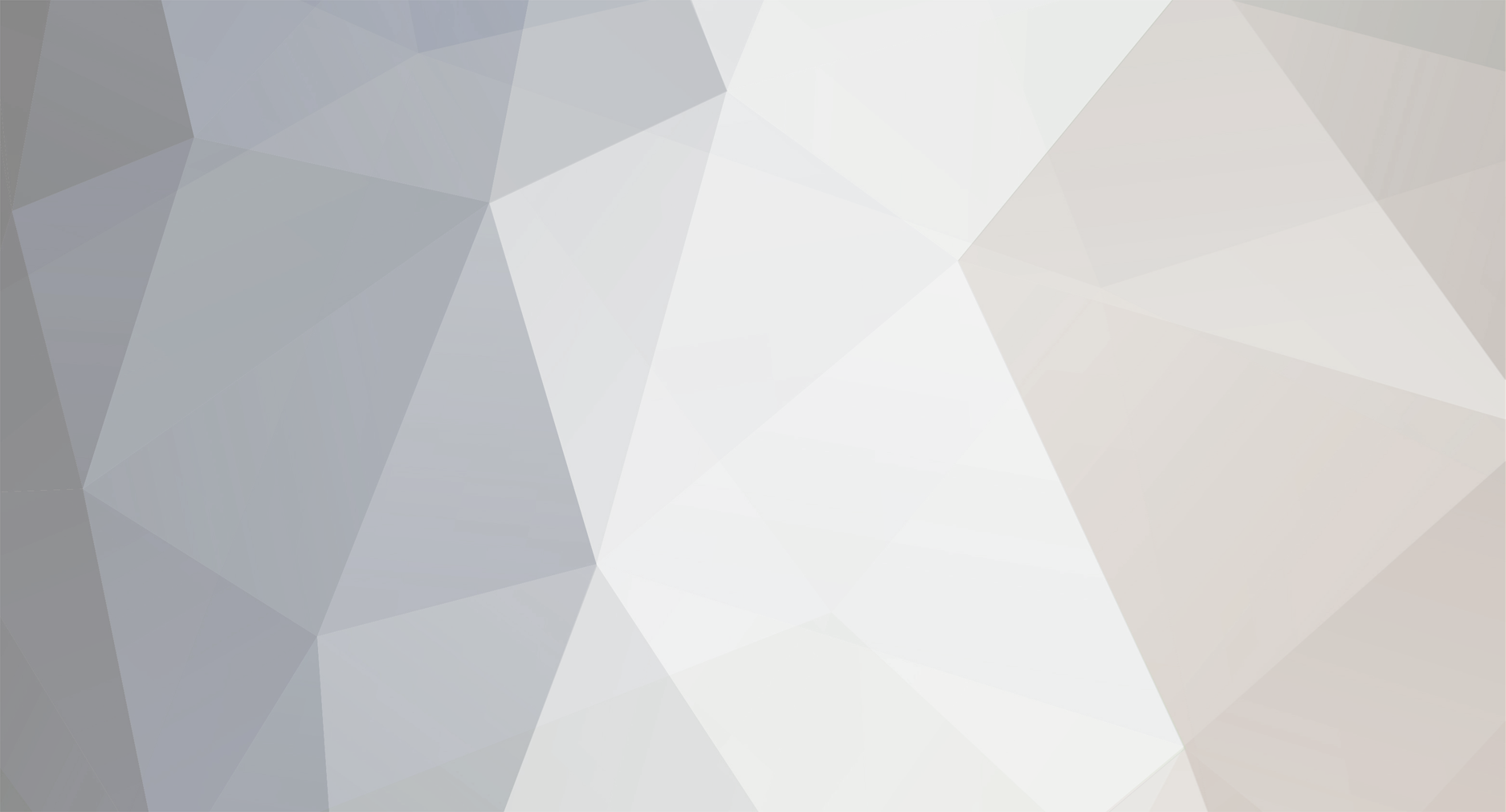
mattinker
-
Posts
59 -
Joined
-
Last visited
Content Type
Profiles
Forums
Gallery
Blogs
Events
Articles
Store
Downloads
Posts posted by mattinker
-
-
Steve, to what accuracy do you believe the cylinders have been bored to? Have you tried to measure them? How concentric do you think the recesses are to the main bores (although in this case this isn't really critical)? Do you know how your friend set up to find the centre of the bore before cutting the recess? Another mystery to me that you can perhaps explain is how do they set up the boring bar to the centre of the cylinder when what they are presented with is often a bore which is oval with non-symmetric wear?
Barry.
As Richard says, the bottom of the bore doesn't wear much. The top of the bores, above the Piston Ring travel should have no wear. This area is one of the places that carbon can build up indicating that nothing is in sliding contact. You can feel cylinder wear with your finger nail, sliding up the bore. This is the first thing I do when I take a Cylinder-head of, to have a rough idea of the cylinder state.
Regards, Matthew
PS Nice to have a "Thorny post" glad to see your back at it!
-
When we filled the Radiator yesterday, several of the small leaks re-appeared - the filler that we put on them last year has "given up" - and really not surprised at that! So the plan is to clean them up and then put a similar seal on them again for this year - and pattern make this winter so that the new tanks will be ready for next year. At least that's the plan! So much going on at the moment with the Thorny engine!
Tony
I realise that I' left out an essential word in my message making it incomprehensible!
I've been thinking about how you could use the existing headers as patterns, extending the length and width of the flanges, that are used to bolt it to the radiator core. I've not seen it up close, but I would have thought that these are only critical dimensions, the shrinkage over the tanks them selves not being critical. Body filler could be used to make things smooth on the inside to make a core mould and to extend the flanges.
Regards, Matthew
-
Something came to mind when reading this. Many years ago, I had a header tank leak on my '52 Land Rover, the only thing I had on me that was vaguely sealant was some glaziers putty, so I applied it to the leak, it sealed straight away and gradually hardened. The "temporary" repair lasted several years, at least until I'd sold it without hiding the repair! Before writing this I looked up "traditional glaziers putty, I knew it container linseed oil, which is a drying oil, but I wasn't sure what was mixed with it. This turned out to be chalk. If the putty is painted over with oil paint it can take thirty years to harden and remain flexible. It is used for joining materials of different expansion rates Completely reversible (with solvents), it could be a substitute for lead/tin solder!
A passing thought!
Regards, Matthew
Quote - "If silver solder is a no go then a dab of devcon on the outside could stop the weepage".Interestingly, the cylinders on our Military Autocar are cracked and have been repaired or just sealed with soft solder! Presumably this was done in France where it spent most of its working life - and these have never shown any signs of leekage!
Tony
-
Electrochemical series is here: http://www.chemguide.co.uk/physical/redoxeqia/ecs.html
This also explains why die-cast "pot metal" is so horrible once it starts to corrode, it's "Mazak" - an alloy of magnesium aluminium and zinc, so you've got the top three right there. Add the fact that car door handles were cast in this, then copper plated as a base for the final chrome, and once you've got a pinhole through the plating, it eats itself from the inside.
:argh:
Chris,
Chris,
I'd never heard of "Mazak", only "Zamak" I thought that it was "pot metal". I've made ZA12 ( a form of Zamak) using 11 parts Al, 1 part Cu and the remaining 88 parts Zn. Casts beautifully (at around 450°C) and is a pleasure to machine. I can see where the corrosion comes in! Old Carburetor metal.
Regards, Matthew
-
If a hand push fit of a cast liner in a alu block does the job with the expansion of aluminium being more than double of cast iron, then a cast liner in a cast block should be no problem at all. A tight press fit would only be necessary if there were no possibility to put in a shim. Not sure if I would use loctite, if the liner has to come out for any reason that would be nearly impossible without damaging it. I am also not sure about the heat transfer rate of the loctite but if the liner expands more than the surrounding block it could cause serious damage (this is only a speculation, if have no experience in this matter).
Marcel
This post is virtually the same as Barry's, I tried to delete it but failed! Dry liners are usually pressed into cast iron blocks, they are then bored in place to bring them up to the same diameter as the the other bores and to compensate for the reduction in diameter due to the interference fit. The shade tree mechanic method for removing dry liners (they can never be reused under any circumstances replacement is the only reason for pulling them) is to run a couple of beads of weld down them!
Regards, Matthew
-
Hi,
I like the advice about not doing anything irreversible, I hadn't thought of that, I suppose it's because at worst I can always find "another" new or second-hand. I'm a real fan of metal stiching, having seen it use on a Leyland 410 engine burnt between two cylinders. Their technician cut out the offending area, (we'd already removed the liners) he then cut out a piece of cast and fitted it into the hole. He the "stitched" it in place it was machined on-site, at the same time as the liners were bored to size.
There's just one, thing I find, that there is so much interesting stuff I have to go back and re-read parts to refresh my memory!
I understand the trepidation, but there will always be a solution!
No Brighton for me this year can't make it over!
Regards, Matthew
-
Just out of curiosity, sometimes people who are very organised and focused succum to the simplest errors.
I know the piston rings look very neat all lined up, but you wouldn't ever assemble an engine with the gaps all inline now would you.!!!
I remain in awe of your acheivements. You are an inspiration to the rest of us impatient souls.
I agree with you entirely, but, my instructor, whilst training as a motor fitter said "there's nothing to stop piston rings turning" he did add that he had no proof either way.
Regards, Matthew
-
Steve,
Whether you can get away with one liner will depend on the state of the other cylinders! If they,re OK, there's no reason why not. I'm curious to know what the pistons are like, do you know what the original bore sizes were? I wonder whether it's already been re-bored! Maybe how many times it's been re-bored! Nothing written on the pistons I imagine!
"We too are reaching the conclusion that dry liners are going to be the answer. The question now is whether we have to do them all or can just get away with the worst bore. I haven't seen the bores since Father has cleaned them up but will have a look this weekend as I am going down for the Brighton run on Sunday.
It is now a whole year since the Dennis took us to Brighton. Where has the time gone?!"
It's been a year since our paths crossed briefly in Brighton! I'm really glad you've started the "Thorny" I hope maybe our paths will cross again and I'll actually get to see the Thornycroft! I look in most days, "can't help it, too interesting!"
Regards, Matt
-
I'm a little bit frustrated by not having any actual dimensions! I've drawn (roughly!) a diagram of how I have made bore gauges, if there is enough space to get a lever type dial gauge in the cylinder. A straight edge, with parallel sides will "follow" the inside of a cylinder. Once the straight edge is in place it can be clamped in place or simply held by second person. With an "L" shaped "saddle" to carry a dial gauge, you can determine the depth of the pitting. I still think a dry liner is a workable relatively inexpensive route!
Regards, Matthew
-
Interesting the different aproaches! personally, I wouldn't use heat!
Regards, Matthw
-
I like your stud drilling jig!
Have you heard of this kind of cold repair for Cast Iron?
http://www.locknstitch.com/Metal_Stitching.htm
Regards, Matthew
-
From memory, dry liners are 1.5 to 2 mm thick, with a band around the top of the cylinder, 3 to 4 mm thick. What diameters are the bores? It wouldn't surprise me if they are a standard imperial size. I'd take the cylinder and a good piston to some one who does reboreing, they may well be able to bore out and fit a standard liner from something else. Heavy pitting at the bottom of the cylinder would behind a dry liner would not be a problem. Even if the cylinder walls are thin, which I doubt, from that era, a dry liner shouldn't be a problem.
Regards, Matthew
-
It appears that there will be no alternative other than to re-bore this cylinder.
Now depending on how much has to be taken off and that there is enough metal there to play with for re-boring, it will then require a new piston. Can we get away without re-boring the other three cylinders?
The cylinders are of 4 1/2" in diameter but as this is a slow turning engine, will it be significantly out of balance if one of the pistons is marginally bigger than the other three?
This is something that we have not been confronted with before and would appreciate some advice and comments on this one, please!
The dry liner option would appear to be interesting as there is visibly a lot of metal to take off. I would have thought that an engine of this age would have quite a lot of meat in the cylinder walls. The determining factor will be how much needs to be taken off it has to be re-bored anyway, so why not start with that and see? If piston weight is the only problem, the new piston could be lightened to make it the same weight as the others. I have no experience of running an engine with one different sized bore!
Regards, Matthew
-
We think just grind them back as they are if there is enough metal there - we need to have a closer look first of all! The top certainly must be made flat.
Tony
This sort of thing is quite often finished with hard casing, if there's enough metal, Casenite or something similar after grinding preferably with a tool-post grinder) and polishing. If there isn't enough metal, but enough to weld, a hard facing rod would do the job. I would see a welding rep for someone like Castolin Eutectic. Obviously practice first or farm it out! My Castolin rep (here in France) will give me samples if I only need a small amount, although it might be to get custom!
Regards, Matthew
-
I "discovered" another useful way of getting rid of rust, plain white vinegar, either submerged in a "tank" or with a rag soaked in it placed in such a way as to have full contact with the metal to clean. wash with water and protect immediately. Easier than electrolysis, it dose smell, so I put the whole thing in a plastic bag, bin liners are good for big parts!
I like you swage block in the back-ground, I hope nobody else dose!
Regards, Matthew
-
Thanks for that Robert. We are always worried aboutblem though. This was our first experience of extracting pistons and we were not looking foward to it at all. Fortunately they were not too painful in the end. One of my friends filled his pistons with diesel and then set fire to it with the acetylene torch! It worked for him but he is braver than I am!
Good luck with the Leyland. We shall look forward to hearing of the outcome!
Steve
Steve,
please don't stop "boring everyone to death with mindless detail!" it's what makes this thread so interesting! I have quite a lot of experience with "modern" engines and mechanics in general. I really enjoy seeing it all coming appart and going back together again!
Keep up the good work!
Regards, Matthew
-
Not too sure about their film prop. From a distance and if you ignore the wheels it probably does not look too bad as a film prop. I am pretty certain that they wont be able to obtain a real one. Even if they did i dont think that real WW1 trucks are suited to appearing films. He has got a little carried away with his description though. I am sure it will make a re-enactor very happy. GS wagons look nice though.
I work building sets and machinery for theatre, cinema and television, historical acuracy depends a lot on budget, the rest is the director and the set designers "idea" about how things should look which is a a variable! The older I get the more mistakes there seem to be. One of the things that is great to do is transforming a street into another era, I once put up wooden hoardings around my Bank! It was the only façade that wasn't 19th century in the "square"! Quite something in a town as big as Paris!! The Lorry in question looks to me as though there isn't much "Thornycroft" in it! Apparently all that is identifiable isn't, so I would doubt the chassis too! It's much easier to use a chassis with the wrong axles than to adapt the wrong axles to the chassis.
Your strange sump might have been made that way to stop it falling out suddenly and dropping into the old oil when removing it. I've seen something similar on radiator drain taps. The ground down bit doesn't look original to me, maybe somebodies modification to drain of a little oil when overfilled?
Regards, Matthew
-
the more brutal approach of hammer and chisel was required to loosen them.
It may seem surprising, but splitting nuts with a hammer and chisel is in my view an elegant solution, the studs are undamaged and you get the job done! I learnt this method years ago and have never regretted it!
Looking forward to following this thread!
Regards, Matthew
-
Hi Matt and Niels.
Many thanks for that one. No, we haven't tried it but it certainly looks worth pursuing. I wonder whether it might be used on the cylinder blocks as we can't get inside them at all? Very good for fragile parts I should think.
You can use electrolytic de-rusting inside water jackets, I would imagine that you can fill the water jackets with electrolyte, the de rusting takes place in "line of sight", in other words, anything between the electrode and the surface to be de-rusted will prevent de-rusting. Multiple electrodes can be used, if you put the cylinder blocks in a tank, you could de-rust both the outside and the inside depending upon where you place the said electrodes.
Looking forward to hearing more about your progress, regards, Matt
-
Hi again,
I did some web searching to see what I could find about hydrogen embrittlment, things seem to be quite vague, I found references, but no one ready to to be clear, I found the following article which seemed well written!
http://www.htpaa.org.au/article-electro.php
regards, Matthew
-
Hi,
I was wondering whether you'd looked at Electrolytic Rust Removal. With all the parts you have to de-rust, clean and un-seize I think, it could be really useful to you.
http://schoepp.hylands.net/electrolyticrust.html
It is possible to de-rust machines bit at a time, lathe beds for example. Hear is a link to electrolytic de-rusting using a cotton pad soaked in the electrolyte instead of a bath, a very useful idea for freeing seized studs etc.
http://www.metalworking.com/dropbox/_1999_retired_files/E-CLEAN.TXT
I enjoy the detail you go into, sometimes I have easier methods, but the most important thing for me is to participate in the pleasure of seeing these machines coming back to life!
Regards, Matt
-
Hi!
first of all, does it have to be a rectangular section? If not, piano wire, formed cold except for eyes, heat red just the end and bend with round nose pliers, (like small cir-clip pliers without the thin points) will be easy for you! Round nose pliers are often used by electricians, I find lots of uses for them. As the spring has a long bending length, there shouldn't be too much work on the eyes, so don't try to temper it, just let it cool slowly, dunking it in water will make it too brittle unless carefully done.
I When I was talking about magneto sparks being better at low revs, it was relative! Hence the transition period when some vehicles were equipped with both coil and mags. I feel it would be a lot easier to start with a de-compressor, I don't want to bore you, but it seems hard to believe that it didn't begin life with one! I am assuming that it's a White Poppe engine. It would make the inertia work for you instead of against you, and, at the same time mean that the mag was turning faster, giving it a better opening speed. You cant break your wrist if the handle is pulled before you drop the de-compressor!
-
Hi,
"The spring then unwinds giving the magneto a sharp flick producing a good spark in spite of the low engine speed."
I would like to point out that magnetos put out a high spark at low speeds, with low speed engines, this was not normally a problem. The coil ignition was introduced to have a better spark higher up the range. When coils were first introduced, a mixed system was often used, both coil and magneto. I am not surprised you have a good spark at low engine speeds! I can't help wondering if the compression is too high! I know I've said it before, but de-compressors were standard at the time. (I've seen a "Gardner" diesel started by one man with a crank) Your engine "bump" starts, not good for the worm! You just can't get it to turn by hand to overcome the compression. It maybe has non standard pistons for pump duty, to run on later fuel. Unfortunately, it's difficult to do a compression test without a starter motor.
In the video of the engine running for the first time, you were all surprised by the low tick-over. This is a long stroke high inertia engine with a lot of turning mass, getting that mass to turn with compression by hand is hard!
Good luck! Matthew
-
Hi,
I really enjoyed seeing you and "Dennis" at Brighton! I'm glad you made it home OK.
I was thinking, didn't the engine have a decompresser? Would have been of the period!
Regards, Matthew
WW1 Thornycroft restoration
in Pre WW2 vehicles
Posted · Edited by mattinker
spelling
Hi.
it maybe to do with it being a fixed head engine, a thread failure could lead to replacing cylinders and pistons, where as on the other engines, the head alone could be changed. It dose seem strange though!
Regards, Matthew