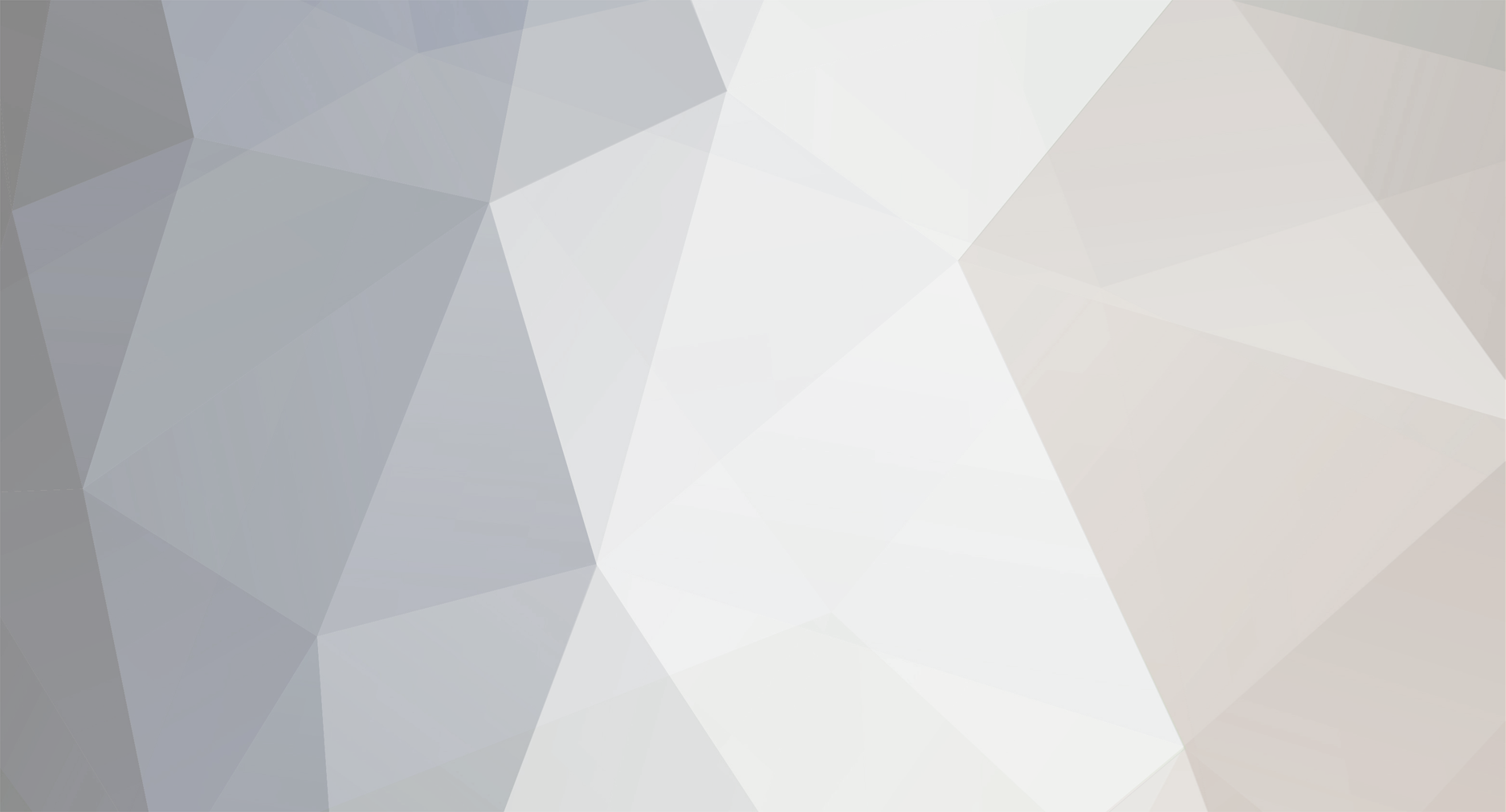
mazungumagic
-
Posts
230 -
Joined
-
Last visited
Content Type
Profiles
Forums
Gallery
Blogs
Events
Articles
Store
Downloads
Posts posted by mazungumagic
-
-
Finished off the preparation of the top of the body shell and then gave it a topcoat along with some sundry bits that were previously cleaned and primed.
As soon as the paint was dry (actually we did it before the paint was properly dry – and we’ll pay for that), the chassis was lowered so the wheels touched the ground for the first time in around six months. We then manoeuvred the body shell onto it and the two separate bits got married, like this –
The spirit level indicated the body was sitting about 1/8" lower on the left, but that'll be easily rectified with some suspension adjustment.
While all this was going on, concurrent activity was taking place on the engine. The head bolts were removed via a very handy stud remover tool
..... and a tool was made to remove the larger core plugs -
All three of those came out easily and flushed with success, a second tool was made (smaller this time) to get the next smallest group of core plugs out – why did they design three different sized core plugs needing three different tools ?
Anyway only one of the No 2 sized core plugs came out with the second tool – it was a little too flimsy, so we resorted to harsher measures and welded a nut onto the recalcitrant bugger. It came off then !
If there's room under the manifold, we might leave this nut on when we replace the plugs, just in case.
There is a third group of two plugs inside the tappet covers, but we reckon they are probably pretty good and we’ll leave them in situ, with fingers crossed.
After that work, we gave the engine a tub and a bit of degreaser, to prepare it for the next phase – re-assembly.
Having the two parts of the vehicle married up, made for quite a big day from a satisfaction point of view and we can now start the cosmetics on the side panels of the body, together with further work on the engine re-assembly.
-
Bosun Al,
As far as I know, the British Army used Model Ts which were produced in their Manchester, England factory. I'm not sure about what was produced there - ie whether during the Great War, it was the whole car or whether like other countries, it was just the body with the chassis and motor shipped out from the US or Canada.
Regardless of that, the English vehicles were RHD and all the photos I've seen are consistent in that regard.
The external paint colour would have probably varied from theatre to theatre and the exact colour would be difficult to determine given that black and white was pretty much the only film available. Some form of khaki green would have been appropriate for the Western Front, while a yellow/brown tint may have been used in the Middle East. The replica I'm producing will be yellow/brown.
Without exception, the vehicle numbers I've seen in the Middle East have used the prefix LC (for Light Car), broad arrow and then the vehicle number. I agree with you about the Western Front - I've seen the M prefix there too.
Jack
-
Priorities please, ladies.
Champ first.
-
One “Rookie Mistake” which will never be spoken about again, has been fixed.
After removing wheels, front torsion bars, brake lines, rebound rubbers and a whole lot of bolts, I was able to gently lower the front diff sufficiently to allow the propshaft to be inserted into the hole provided by the designers in the chassis and slid through to the rear diff.
Easy peasy.
Then using a very handy hydraulic trolley, I raised the front diff back into place and as the books say “reassembly is the reverse of removal”. I had to do a bit of jiggling, but not much – the whole lot went back together very smoothly.
Lastly, it was a matter of cutting new 7/16th bolts to the right length, so that breathers and grease points don’t get neatly removed on the first time run and the propshaft was secured.
and
With a bit of luck, this will be the last time I have to stop "moving forward" to rectify an RM.
Very hot today, around 39 degrees C with the additional bonus of high humidity.
-
Tom,
I hadn't thought about the spring shackles, but you might be right. What really interests me is that I've only seen this device on a staff car ! I've looked at any number of Model Ts in the Light Car Patrols, but there's been no sign of these limiters on them. It's probably one more example of the folk at HQ getting all the good kit before the PBI, or its equivalent in the LCPs.
Gus,
Rear shots are very rare and frustratingly so, at times. Only a small percentage of the Light Car Patrol photos I've seen, display the rear of the vehicle - though I've seen enough to make a pretty good guess at how it was constructed. As I'm sure you have.
KK,
No doubt the design was compiled by a K©areful Kiwi and the rest of the Division was too tired to care.
No, I'm sure that's not correct - I think (being serious now), that the boomerang from a heraldic viewpoint, is always displayed this way, ie facing up and it was aesthetically acceptable that the fern be intertwined on top.
Jack
-
I stumbled over this image of LC 1357 today, while I was checking the place names mentioned in a War Diary of the 1st Light Car Patrol (or the 1st Australian Armoured Car Section, as it was initially). The pic was in a book titled "Chauvel of the Light Horse" by Alec Hill and I found it interesting because of the limit straps on the rear axle.
Never seen these before on a WW 1 Model T, but I guess they would have been a valuable addition.
Jack
-
Did a little bit of extra work today - out of session so to speak.
I changed over the RHF lower rear wishbone for one which hadn't been tampered with and then managed to fit the torsion bar, so all is well on the suspension now. I also adjusted the 16 brass screw bushes on the outer end of each wishbone arm and fixed them with the 5/16th bolt and tabbed washer.
Then I thought I'd have a go at fitting the long prop shaft, connecting rear diff to front diff and found that I don't seem to have enough wiggle room to feed the prop shaft through the chassis tunnel (from the rear to the front - I think I'm right in saying that's the only way it will fit).
Is this a rookie mistake ?
Should I have done this while the rear diff was still on the bench - and am I going to have to remove and re-bench while I feed the prop shaft through that teensy hole ??
No pics today - forgot to take the camera.
-
Thanks, John.
I hope to get the last torsion bar on soon - once the replacement wishbone arm has been painted - and then I can get to the adjustment.
Jack
-
Caddy,
That comment wasn't meant to cause envy - around here 40 degrees is known as "bloody hot". So our Christmas may be a little uncomfortable but that said, I prefer it to what will be happening in the Northern Hemisphere !
Antar - I know nothing about adjusting the torsion bars other than what I read in the EMERs and that doesn't spell it out very well. It simply gives the measurements, if I remember correctly. Can you provide more information on the process ?
Jack
-
Jerrykins and fesm_ndt - Nice to see you reading the thread.
The Pinzy belongs to the owner of the unit where we do such fine work - he also has a coterie of jeeps and trailers as well as a fine collection of tools and machines, to which we are allowed access. All in all, a pleasant environment for our Wednesday's work group.
So a little more headway was made yesterday, but work does seem to be slowing - Christmas is getting in the way of progress !
The torsion bars went on - well three out of the four are now assembled onto the suspension. The fourth is not quite there yet. The lower wishbone arm to which this RH front torsion bar is bolted, was the one we inadvertently "modified" by knocking out the soldered core plug when we were trying to discover how the whole thing fitted together, ages ago.
The core plug was replaced by one I had in my collection, but it didn't indent far enough into the arm and that has in turn meant that the torsion bar won't seat far enough into the wishbone arm to allow the adjuster end to be bolted up into the saddle. Those who are familiar with Champs, will probably know what I'm speaking about.
A pic of the offending wishbone arm, with the ersatz core plug -
So, the long and short of it is that the arm needs to be replaced with a spare which is currently being cleaned and painted. I hope to have that on within the next week and that'll allow the final torsion bar to be installed. Then the vehicle can be lowered off the drums onto the ground and the height levels, adjusted.
Some work on the brake lines also occurred, with the rear setup now complete.
You'll probably notice straightaway, that the brake line junction sitting on the rear of the cross member has been altered from a three way to a four way type (actually it's a five way, but I've blanked off one of the outlets), so I could fit a brake light switch. You can see it if you look closely.
The location of the line from there to the junction nearest the master cylinder was a bit of a puzzle, but Brian worked it out from the book diagram (not that easy to interpret) and a good look at the outside of the RH chassis rail. The unique line securing clips were still place, delineating the route along the chassis rail and from there it was easy to fabricate a line. That part of the system is now finished and I think the front section will be a simpler undertaking.
I've still to get the master cylinder sleeved - none of the three I have were usable. The bores were too far pitted to hone without affecting the sealing characteristics, though I tried hard.
More priming of the body shell top occurred as well -
.. but it was still too wet to sand by the time work ended yesterday, so that will be done this week and a final top coat (s) will be applied once we return from the Christmas celebrations - on 9 Jan.
A little more work was done on stripping the motor and we found three out of the four inlet cam follower seats were too deeply pitted to be used, so I'll have to find more of those. I guess the exhaust followers may be in the same condition. Cylinder bores look very good, though two of the piston rings were broken !
This will probably be my last post before Christmas (it's forecast for 40 degrees C here, on Christmas Day), so all the best for the season - enjoy the family time.
Jack
-
I think I've found most of the problems - have a look at the blog -
http://hmvf.co.uk/forumvb/showthread.php?28539-The-Restoration-of-Austin-Champ-1824
There are two main issues - rust and a lack of preventative maintenance. Unless you're exceedingly lucky, I don't think anything you will buy these days will be free of at least one of those and the odds are you'll have both to deal with.
Jack
-
I’m trying hard to maintain my positive opinion of the Champ designers, but today I suffered a lapse. It all started when I found I had difficulty in getting the brake drum onto the rear RH side. Despite all obvious remedies, the drum seemed too small to go smoothly over the shoes. Tony discovered the problem when he looked at the rear brake diagram in the EMERs and noticed a RH and LH plunger in the brake adjuster. Once we realised they were handed (really !), we changed their relative places and hey presto, the drum fitted.
Couldn’t believe the brake adjuster designer had done this, but the book is never wrong.
Anyway, we installed hubs, adjusted bearings and fitted the front brake shoes – the rears had already been attached.
The front brake return springs are gorilla sized and it took some leverage to fit them in place, with the occasional victory marred by the realisation that the brake adjuster wasn’t working, which could only mean that we had gotten the shoes around the wrong way and the adjuster post on the shoes, was not in contact with the eccentric adjuster built into the backing plate. That in turn meant we (I) had put the wrong shoe on the wrong side. Off with the shoes and swap them over, struggle manfully to get the return springs in place again and … job done.
Drinks all round, again.
The brake steady posts took a bit of juggling to get them lined up so the shoes were square with the backing plate but that was all done and the end result was quite pleasing, though we’re still struggling to comprehend the mind of the person who designed the rear brake adjuster.
At that stage we decided to fit the front diff. Using a hydraulic trolley, we lifted the diff into place and bolted it up with only minor difficulties getting the bolts in place – especially the front support plate bolts, which are engineered with very fine tolerances. Flushed with success, we did the rear diff as well. The second time was much easier and we now have both diffs on, incl wheels and tyres.
Front -
Rear being tarted up on the hydraulic trolley (magic piece of kit), before installation -
...and in place -
Next week, we’ll concentrate on getting the torsion bars into place, the vehicle off the drums and onto its own rubber radials. With a little luck and some preparation, we might also get the body shell on, too.
Engine and gearbox are next on the list.
-
Thanks for the info I can say that I have fired something like this when I was in the army it was a Energa anti-tank rifle grenade which I fired from my SLR and I can say it had some kick back and yes one of the lads put it to his shoulder and went arse over tit :nut:. Cheers Bill
The Energa was fitted over a grenade launcher which itself was (in my time), fitted over the barrel of an SLR and secured to the bayonet boss. Again a ballistite cartridge was used rather than a ball round and the launcher had some rudimentary folding sights. Like the rifle projected grenade, it wasn't accurate or an enjoyable firing experience. Thank God for the M79 and its big brother the Mk 19 !
Jack
-
G'day Rick(ety)
The paintwork does look good - more of that later. I don't want to get diverted from the real message, by trucking your wet wheat to the silo ! (Insert "smiley face" here)
Last Sunday I attempted to press the big oil seal into the swivel housing, but found it impossible to do. In lieu of paying high prices and postage from the UK, I opted to buy a seal locally, but found the nearest in diameter, was 5.5”. As the housing and original seal housing was machined to accept a seal that was 5.449” in diameter, the problem was obvious.
The solution was to take the housing to an engineering shop and have the housing machined out by around .025", to accept the 5.5” seal. Fixed.
Which meant that we could then complete the assembly of the rear diff/suspension.
I’ve still got the axle hubs to instal, but that won’t be overly complex.
We got some top coat paint on the chassis today…
It looks like a two tone job but it's just the camera flash, lightening up the closest part of the vehicle.
The body interior also got a lick of paint …
… and the front diff was transformed
The paint was from Chameleon and labelled semi gloss, but it's turned out to be more gloss than semi. The effect is very good and I'm very pleased with the outcome. All that insistence on rubbing back the primer and the forced labour involved, has certainly been worth the effort.
Next week, we should get both axles bolted onto the vehicle and the body back on the chassis, which has now had strips of rubber glued into place to seal the two pieces (body shell to chassis).
-
While the fuses might look OK, the fuse contacts are known to be vulnerable to corrosion. Have you checked the power coming into and going out of, each fuse ?
A simple trouble light will tell the story.
Jack
-
Got a little more of the diff/rear end done today but reached a point where I couldn't progress, as I am still waiting for two large swivel seals from my local seal supplier. I should have them by the weekend and will be able to finish off the rear diff then.
Last weekend, when I was pressing (that should probably read bashing) in the two internal swivel seals, I was obliged to replace the springs in these seals because the originals popped out and were crushed. Anyway, I removed a couple of these springs, from the old seals I had discarded and noticed when they (the springs) were pushed into place in the new seals, that they seemed a bit big and it struck me at the time, that they might therefore not perform as they were intended. I disregarded the problem and bolted on the seal retainer, but it plagued me so this morning I removed the boots/seal retainers and shortened the springs. That wasn’t as easy a job as I thought it would be, mainly due to the tapered spring end being a real dog to get back into the hole at the other end. The job was finally accomplished and I don’t expect to see any leakage from that part of the restoration. Maybe.
Then we squeezed the diff into the cradle – not an easy job, but it can be done, albeit brutally and with the potential to damage the rubber swivel boot. The lower wishbone arms were next, after ensuring a plentiful supply of grease was in the pivot pins and that was as far as I could go without the remaining two swivel seals.
The result to date ...
While that was being done, the other two workers were (1) rubbing back the previously primed surfaces and (2) priming the floor of the chassis.
The result for the day looks like this ….
The project is now coming together very well and at long last, we can see progress is clearly being made.
One of the other small parts to be fabricated, was a set of the instrument panel rubber blocks which secure the panel to the bulkhead. I don’t think these can be obtained from the usual suppliers, but they can be relatively easily made. I was able to separate the two identical parts of the cage – they are spot welded – cut out some thinnish reinforced rubber and insert the original bobbin into a hole drilled through the rubber. The whole job was simple, but hopefully effective and certainly better than using the original parts, the rubber in which had eroded and solidified.
Perhaps next week we’ll be able to get some DBG onto the primed metal. That'll be real progress, after almost a year on the job.
-
G'day Rod,
I've been working on my LH door and finally got it hung today.
Jack
-
Progress of sorts today- the diff I got was useable !
Although it's not 100%, it has less wear on the pinion than the other two diffs. There was well over .010" backlash but by re-arranging the packing washers from one side to the other ...
... we were able to move the crown wheel closer to the pinion and reduced the backlash to within the guideline range of .008-.010". Very hard to get a dial gauge into the crown wheel to accurately measure the end result, so all we can say at the moment is that the diff is now set up better than it was. The pinion had some wear and the movement of the crown wheel, will probably mean that the meshing of crown wheel and pinion will now be wearing, at least partially, on new surfaces but we'll just have to put it to the test and see what the noise effect will be.
It took us three attempts to get this result - each time we had to extract the diff centre from the carrier, remove the left and right bearings (they are a very tight fit and we only had tyre levers to get them off), move what we thought would be the right combination of packing washers from one side to the other and re-assemble.
So this is the diff - all buttoned up and ready to be replaced into the cradle ...
After some solid sanding of the metal, we were also able to get primer onto the inside of the body shell ...
... and a bit of body filler onto the front mudguard areas.
I should be able to reconstruct the rear suspension now and once we get some paint onto surfaces, that will enable us to bolt on the front and rear suspensions. So the point at which we can get the vehicle back on its wheels, is not too far away.
-
DB88,
Thanks for this close up on the Lewis gun mount - it clearly shows some of the finer detail.
Jack
-
Took care of a number of smaller jobs today, including the rubbing down of the primer in the engine bay - we are being held to high standards by our resident spray painter, even in the overcrowded engine bay, where only about 30% of the surface area will/can be seen.
A good deal more welding of smaller areas followed, mainly those places where it was difficult to get at when the body shell was on the chassis. Plenty of grinding also and then a coat of body deadener underneath as well as some of the lower internal areas.
Also made up a cover for the winch compartment - we welded a piece of angle iron across the forward edge of the compartment, drilled holes and welded in some captive nuts. Did the same at the rear, bumper end and bolted the lot down. It will serve well as a flat surface and may also be used as storage for those rarely used, but essential items. Could also be a tucker locker on camping trips ?
I will now get some deep bronze green (satin) and with a little more work, we can start the paint job in the engine bay. The rest shouldn't be too far behind, but I think we have now put the welding behind us and can concentrate on the cosmetics.
After the disappointment of finding two sub standard rear diffs, I've now obtained another, which might be fit for purpose. It feels pretty good but we will pull it down and look at the crown wheel/pinion next Wednesday. Fingers very tightly crossed.
-
Glad you joined us, Jack! I have several photos showing Lewis guns mounted behind the passenger seat. As a general rule,
Vnckers guns seem to be behind the dash as you mentioned. Wonder if there was a practical reason for this difference?
Looking forward to seeing your LPC car finished . . .
Bosun Al
G'day Bosun Al,
Thanks for the welcome though I've been on other areas on this site, for a while. I'm also restoring a Champ and have my efforts recorded at
http://hmvf.co.uk/forumvb/showthread.php?28539-The-Restoration-of-Austin-Champ-1824
I've attached a picture below of a Model T from the Australian Light Car Patrol on which I am basing my restoration of the LCP vehicle (BTW, it will be numbered LC 303). All the photos I've seen of this black radiator era (ie 1917 plus), seem to have a Lewis mounted in front of the passenger.
The earlier vehicles often seem to have had a Vickers pointing rearwards.
In thinking about the MG post, I've come to realise that these weapons, weighing around 30lbs in the case of the Lewis, would have needed to be solidly anchored. Obviously, the Vickers would be heavier.
I'm still weighing up options for the MG Post but reckon it would have been bolted to the LH chassis rail which would take all the vertical weight and secured to the dash to prevent it moving laterally.
Jack
-
The Champ did not have brake lights or indicators as original equipment so both front and rear harnesses have no wires for these components. If you are reworking original harnesses you need to consider adding extra wires.
Somewhere I have some instructions for adding brake and turn signal lights using the original (spare) wiring. Something to do with the AUX cable, I think.
I've not reached that stage of my restoration yet, but it won't be difficult to incorporate that wiring, one way or the other.
Jack
-
The black radiator and the design of the LH mudguard, suggests to me that the vehicle is a 1917 or older model. It would appear, from the damage to the LH mudguard, that it could be the same vehicle in all three photos.
The MG post behind the front seat is interesting - generally, the light car patrol design put the mount just to the rear of the firewall/dash. The original photo is very well preserved and a little zoom brings up a few interesting items, like the fire extinguisher in front of the passenger in the first pic.
Thanks for finding these pics and displaying them.
Jack
-
The full team was on parade this morning and we were able to finish the welding of the tailgate, dismantle the rear diff and separate the body from the chassis.
The tailgate job went well, though there are a number of areas which will only look good with body filler - these are mainly the result of previous dings which are very difficult to remove in the double skinned areas. We were able to remove a couple by drilling a hole, threading in a self tapper and using a sliding hammer, but our successes there were exceptions. One of the advantages here, is that the rear is pretty much hidden from view once the spare tyre and jerrycan are mounted !
The diff was a disappointment. The first clue to the outcome was the complete absence of oil anywhere and the dirty sludge in the transfer case, which proved to be widespread in the diff housing as well.
The pinion looks like this ...
The teeth are worn to the extent that they are more or less razor sharp, which is pretty much extraordinary. I'm no expert, but I've never seen teeth worn to this degree before. It must mean that the diff was operating without lubrication for a long period. I suppose it must also mean that the pinion was sliding fore and aft, in the housing to some degree. Anyway the long and short of it is that the diff is RS. I do have another which though worn, is in much better shape and we are now scanning the workshop manual to find out how to adjust the excessive pinion/crownwheel backlash.
Anyone know ?
There were some shims between the oil seal/pinion seal housing and front section of the diff housing, but even with these removed, the backlash didn't improve markedly. Can't see anymore shims in obvious places, so we may have to somehow shim up the crown wheel closer to the pinion, to eliminate the unwanted backlash.
So, a bit more work to do there before we can re-assemble the diff and suspension.
We also lifted the body from the chassis and despite our concerns, it came off very easily once we had cut away a small dob of weld which had inadvertently landed between body and chassis and prevented a clean lift. Once that was identified and cut, we were able to remove the body, set it up on the floor and finish off the welding we couldn't access, while it was on the chassis. A few more captured nuts were re-installed and it's now pretty much ready for the cosmetics.
Restoration of Champ 1624 in Sydney
in Blogs of MV restorations
Posted
Simon,
I've done a lot of my cabling already, but have a bit to go yet. To complete the job, I purchased a 30m roll of 4mm wire, capable of up to 15 amps.
http://www.ebay.com.au/itm/30m-roll-x-4mm-single-core-multi-strand-automotive-wire-orange-15-amps-12v-/130701799411?pt=AU_Car_Parts_Accessories&hash=item1e6e6f2ff3
Have a look at the thickness of your old wire and I think you'll find that this 4mm stuff is OK.
I was able to use most of my old connectors, but had plenty spare after having stripped out three Champs worth.
Jack