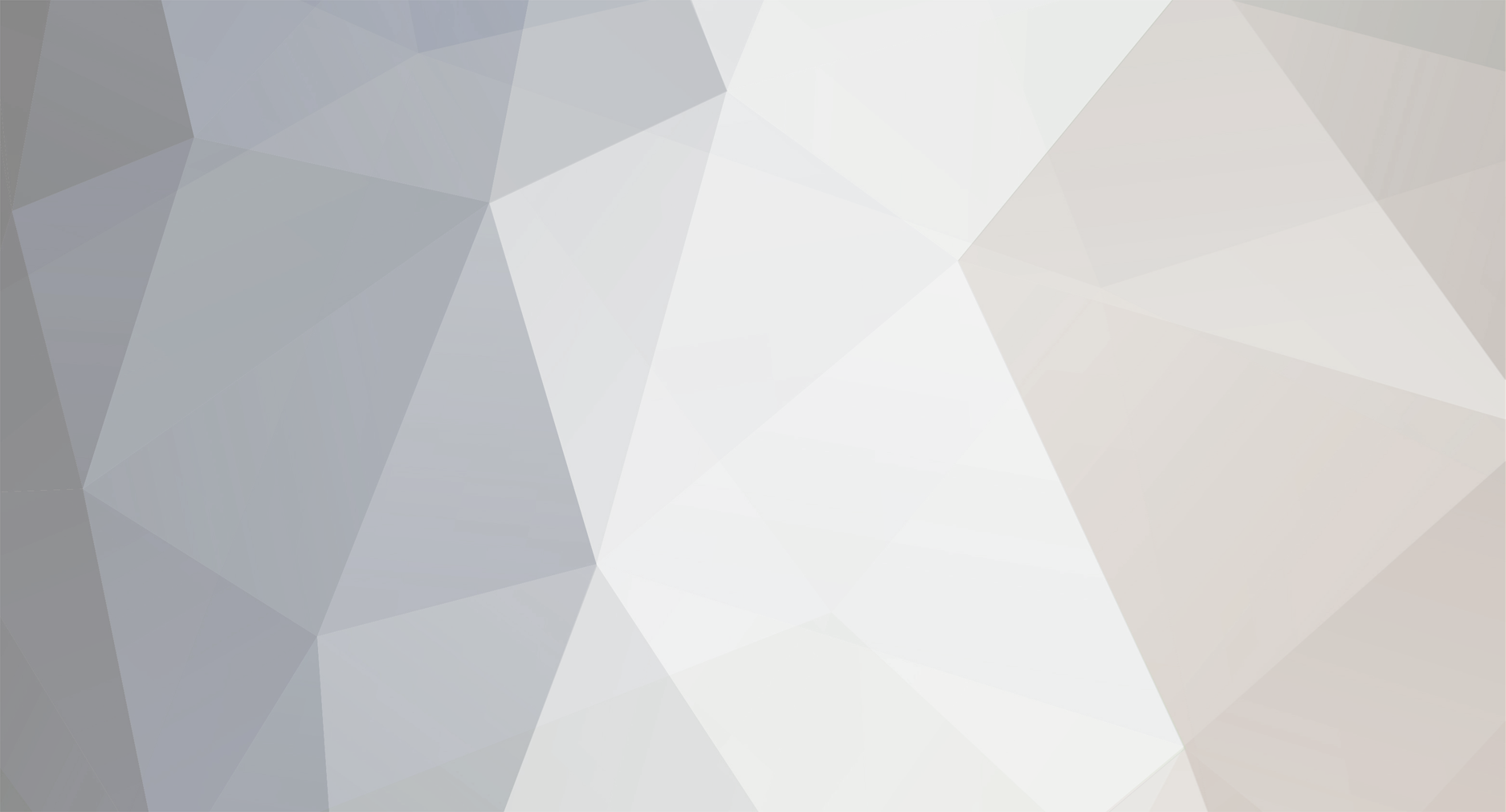
BenHawkins
Members-
Posts
864 -
Joined
-
Last visited
-
Days Won
3
BenHawkins last won the day on March 4
BenHawkins had the most liked content!
Reputation
15 GoodPersonal Information
-
Location
Birmingham
-
Occupation
Engineer
Recent Profile Visitors
The recent visitors block is disabled and is not being shown to other users.
-
Barry, the taper on the originals appeared to be 10:1, I considered boring through but found I could buy a Chinese reamer for under GBP9 including delivery so went with that so it is in stock for next time I need to make taps.
-
-
A few photos taken whilst we had the lorry at the Black Country Museum for an event earlier this month. We took the Dennis on the Saturday, and the Singer on the Sunday. Saturday was a bit rainy at times, a good way to test the "ample protection for the driver". It dried up for the cavalcade, it is a lovely site for taking photos.
-
All the cylinder blocks are now cleaned up inside and out. None of the bores are perfect, some have light surface rust like this one and there is also the score from the gudgeon pin mentioned previously. I have decided that it would be best to get a professional to perform the boring, lining and honing operations. I have decided to move away from the press fit pins, so I will make floating pins with bronze buttons at the ends.
-
I have part machined one plunger and two set screws for the replacement cam followers. I had made the lock nuts years ago. The set screws still need facing to length and counterboring for the fibre pad that goes in the top. The pads appear to be made of red vulcanised fibre (like plumbing washers). I suspect these were originally cut from 1/4" sheet but the thickest I can find now is 3mm. For another project I have turned them from Tufnol but I am considering gluing sheets together for this one.
-
At some point in the history of this engine it has been separated from the correct valve cap spanner. As a result the valve caps have been the subject to the use of pipe grips, knurling the outside diameter and damaging the sealing face. So, I have turned up a fixture with an internal thread to match the valve caps (11tpi Whitworth form). Then screwed the valve cap into the fixture and added a bolt for security (of the horrible metric type). Then refacing was the easy bit. That should give a better chance of keeping the compression in. Half of the valve caps are hexagonal and have twin angled holes this make it more difficult to use a bolt to secure them, so I used the lathe centre. Suitable soft copper washers are available off the shelf but I think I will probably get copper wrapped (asbestos substitute) washers made for when we reassemble.
-
I have not yet used commercial dye-penetrant on any of my lorry parts. However, if I am concerned I have been known to use the low cost option. This shows me painting thin oil onto casting marks on the next cylinder block. After it has had a few minutes to soak into any cracks it is wiped off and talc is dusted on. I set this up with two pieces of steel clamped together and followed the same procedure. The oil has been drawn out of the crevice and clearly discolours the talc. As far as the water jacket is concerned, it is a vented system. The coolant pressure is much lower than on a modern engine so the leakage rate from tiny through porosity is likely to be insignificant.
-
We decided to clean up cylinder block number 3 to get a better view of the casting before committing to getting it sleeved. The first part of this was just to scrape the worst of the paint off. Most of the green paint came off very easily and exposed the red underneath (from the history of this engine in a fire salvage tender). We then used paint stripper to remove the more stubborn paint. Having found no frost damage or other defects (in fact it is a very clean casting), we decided to brush on some primer. The date code in this casting is 5th September 1910. We will clean the other three before doing anything else with this one.
-
The engine is missing two of the cam roller followers. This photo shows one of the original cast iron sleeves at the front, an iron unmachined iron casting at the back and the two machined castings. The six surviving followers have worn spindles and rollers so I need to make eight of each of those but only two of the plungers and setscrews as the six remaining seem servicable.
-
I decided to make the carburettor throttle lever. Starting with a bar end of brass I machined it into a rectangular section and drilled the holes required. The next stage was to create a counterbore for the cam, this was done by mounting it in a four jaw chuck in the lathe. The cam was also made from brass bar, after drilling the holes I indexed the blank around in 10 degree increments; each time reducing the diameter. After parting the cam off the end of the bar I polished out the steps and stamped in the numbers. There was a little more milling to shape the lever. A 1/8" rivet holds the cam in place (with a spring on the underside to hold the cam in location on the 1/16 dowel). The clamping bolt was machined from EN8 bar. I had to make a 1/4BSW brass bolt to blank off one of the holes in the carburettor so I made several more of the correct length to retain the water pump cover. Making the water pump is a job for the future.
-
I was a bit concerned about using anything that might change hole sizes on the carburettor so didn't use anything aggressive. I have used ammoniated clock cleaning solution on several of the brass/bronze parts, this photo shows before, during and after immersion.
-
I had to work in America last week so didn't have time to make anything. However, a couple of evenings in a hotel room with nothing to do meant I could sketch up the carburettor lever and air admittance disc (which allows the mixture to be leaned off by allowing air into the throttle chamber through the spindle). Now I just need to make it.
-
I have been cleaning the carburettor. The inlet trumpet was very dented but was relatively easy to tidy up using a hammer and the bick of the anvil There is also a carburettor heater that gets plumbed into the cooling water circuit. A nice bronze casting that cleaned up really well. I didn't go overboard with the cleaning of the float. The inlet pipe was cracked so I made a new one and soldered the original fitting back on. The White and Poppe carburettor has a variable jet, as the throttle is opened the jet size increases. That is achieved by having this cap over the jet which rotates with the throttle barrel. The orifice had become worn so I cleaned only the wear area and soldered it before scraping the solder back. I don't think this really makes any difference to performance. This picture shows the fixed jet in the carburettor body. The top is shiny because I have put some brass polish between the fixed jet and the cover and lapped them together as scratches in this area prevent the correct control of fuel flow. This is the throttle barrel before it was fitted to the carburettor body. I am missing the lever that fits the throttle spindle so need to sketch that up and get on with making it.
-
I have been trying to get a Bosch D4 magneto rewound for several years. It has been to a couple of people who eventually reject it; not because there is anything intrinsically wrong with it but because everything is so much bigger than a magneto from a few years later and does not fit their tooling. Obviously I could fit a later magneto but it would look quite different. The current magneto specialist was keen to work with me so when he stated the points insulator and distributor end cap (made from fragile ebonite) were not serviceable I took the dimensions from my donor magneto turned up new ones in black acetal. I had the straps for securing the magneto but several parts were missing that I have had to make. The first was the coupling, a relatively simple turning and milling job, especially as I had the engine side and a drawing for the part that fits the magneto, so it was only the length of the intermediate piece that was guesswork. Then came the dovetail packer underneath, this is a 5" wide aluminium plate, 17/32" thick to make up the centre height of the magneto. The magneto fits on the centre line, the final part being the clamp than has two 30 degree chamfers to pull the plate down onto the crankcase. A washer and 3/8 Whitworth castellated nut finish off that job. Just have to hope the D4 magneto will eventually come back working!
-
Although this van probably only had magneto ignition, trembler coil (secondary) ignition was an option. The engine I am fitting started life with Liverpool Salvage Corps and had the remains of a distributor, so I decided to make the missing parts (mostly informed guesswork as it is not a type I have drawings or photos for). The base of the distributor and vulcanite commutator came with the engine but nothing else. I have been collecting scraps for the last few years and had enough to build it. I counterbored a bit of brass plate. I then silver soldered a scrap bar end into the counterbore. And then put that part back on the lathe for machining. I made the brush carriers out of bar ends of brass with the insulators from black acetal. The brushes themselves are WW10001 magneto earth brushes.