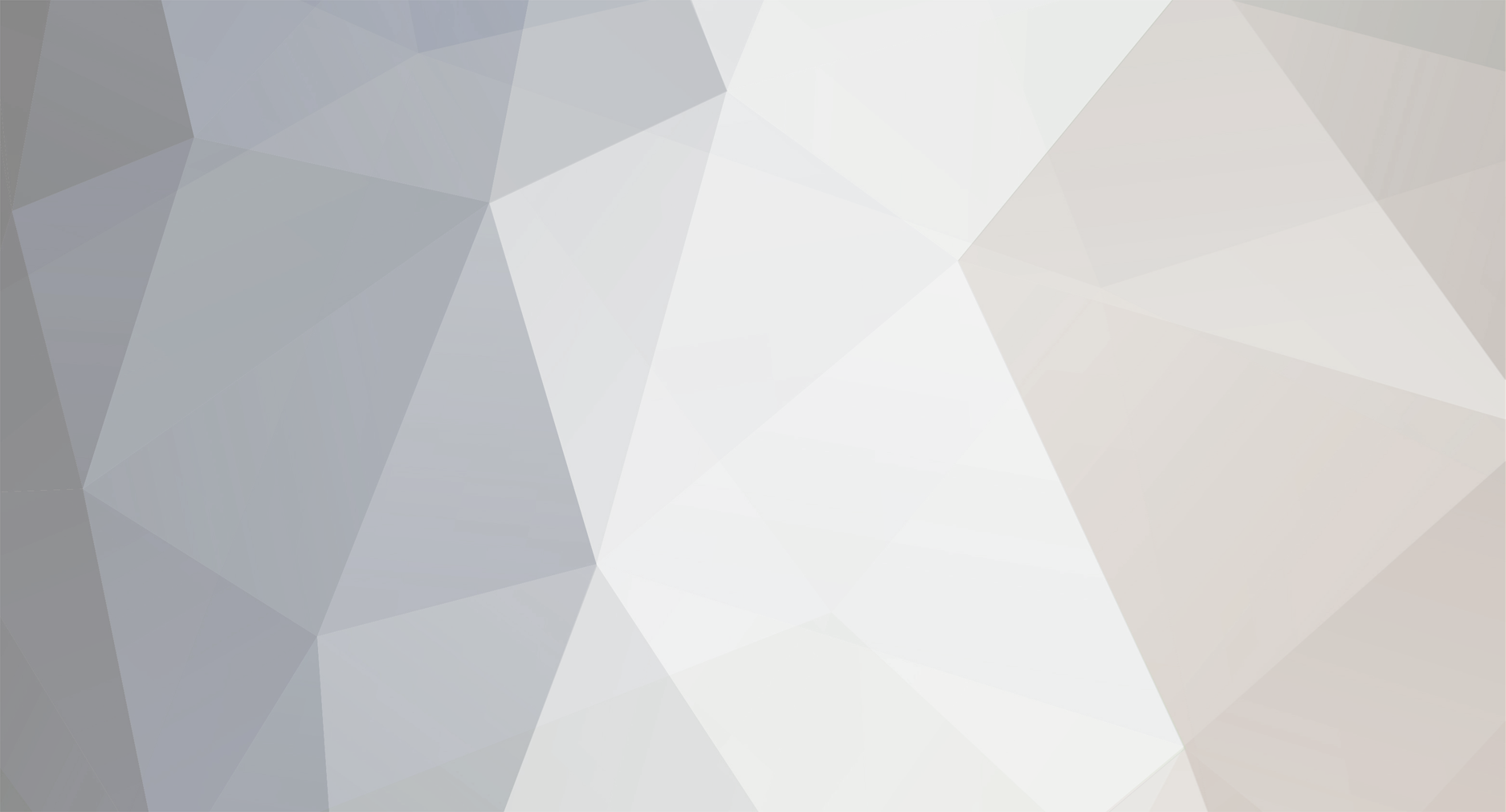
Tamber
Members-
Posts
236 -
Joined
-
Last visited
Reputation
11 GoodRecent Profile Visitors
The recent visitors block is disabled and is not being shown to other users.
-
Thank-you! It's a little of column A, and a lottle of column B, I think. π (Well, and a big helping of sunk-cost fallacy! But that's neither here nor there!) As for writing about it, I think that's genuinely a big part of what keeps me going; between the people who find it entertaining, the people who find it useful as reference material, and the warm fuzzy glow of adding to the archives as it were... (It does bring me great joy to find that others are using photos and material that I've contributed, particularly during my various teardown phases, as reference for their own projects and whatnot. Which reminds me, I do need to get back on adding stuff to my little reference site... I only started out making a chart of all the various lubrication capacities and whatnot, and oh boy did that escalate!) --- Since my last update post here, I've not done a whole lot. (Beset by The Agonies again, alas. Thankfully, it's been a short work-week. The painkillers help, but I turn into a pumpkin when they start wearing off.) I have got another big bucket of golden yellow paint, and that's now in my paint cabinet awaiting a paintbrush day! I have also gotten some more air fittings; two elbows to come out of the compressor -- unloader return, and compressed air supply -- and a T so that I can attach my unloader to the supply hard-line. I've attached a little bracket to the nearside front cab mount bracket, with a bolt welded to it, so that I have somewhere to bolt my new hard-line pipe to; since the original, while also being a hard line, was formed with multiple bends that I do not have the capacity to replicate. At the other end, there'll be a tab that I should only have to drill a hole in the spare wheel carrier bracket to support. The replacement is a straight-shot from just in front of the cab mount, to underneath the spare wheel carrier; which will have a flexible line at each end -- stainless-braided teflon, as is common on modern trucks-- to connect to the compressor and the dryer unit's inlet. The return from the unloader to the compressor's inlet, I think I can get away with regular air-brake hose, which I will support with a rod welded to the tab for the supply (But it's easy enough to change out to a similar setup as the air feed, if I have to.)
-
Absolutely. I've lost count of how many times I've missed the hub-ring step on the way down and found myself at the floor a lot earlier than planned. ...it's even worse when you can only get in through the passenger door and have to climb over the engine to get to the driver's seat. Not a lot of places to stand!
-
It's all part of the charm!
-
Anywho! I've had a fairly productive week/long weekend so far, away from work (Which has been the land of gearbox/clutch hackery...) The 26th I got my new MIG torch in, so I celebrated by welding on my remaining two side-marker light brackets on the offside. Which, if my doctor's reading this, involved exactly 0 crawling or kneeling on the floor the day after having some exploratory work done on my knee. (Did you know they made needles 80mm long? Neither did I 'til then!) One at the front. And one at the back. Happy days. The 28th Got some tracing paper in, so I could take advantage of having put the truck too far away from the wall, and trace out the signwriting on the offside. Well, what's left of it, in some cases. See, I managed to wipe out the same bit on both doors before I managed to get a tracing of it. Thankfully, I have enough pictures that I can reassemble the missing bits pretty close to how it used to be; they won't be exactly identical, because I'm probably going to move the "vauxhall" and "bedford" bits down to miss the mirror bracket, but... ...that's alright, because they weren't identical to begin with. π The 29th Dragged the locker out from the nearside, and stripped all the old mud, underseal, and paint. It's in pretty good condition underneath, all things considered. Much better than the locker in front of it. A nice heavy couple of coats of primer... The 31st Not a lot of pictures from today, because my phone was on music duties again. I did interrupt it in order to grab a snapshot of the whole ridiculous mess that was reftting the locker. I should note, this was 2-1/2 hours into proceedings; I had to give every enclosed side of that locker a coat or two of black paint, which thankfully dried pretty quickly in the warm sunlight. And while it was drying, I made up a mounting bracket for my air manifolds. (Unpictured. I'll have to grab a snap next time I'm down there.) I also went and tack-welded in the bolts at the forward end of the locker, because there's no way to get a spanner on them in order to prevent them spinning. I'm not entirely sure how they were originally put in, because there's a floor above them and they're inside a C section in such a way that you can't hold a spanner in from the side even if the forwardmost locker wasn't there! This was round two of trying to fit it; the previous round, the bike jack launched itself out as I tried to squeeze the locker into place atop it, and I ended up making an attempt to fit the locker by lifting it a bit at a time and blocking it up... only to find out I only drilled the mounting holes to 8mm, and the mounting bolts are 3/8. π Redrill holes, reassemble the whole silly stack. Discover that all the bumping and banging has tweaked two of the mounting bolts... Make up a special tool (bent stick) in order to reach in through the narrow gap and pull the bolts back into place, then pump the jack to shove the box over the bolts before anything else moves out of place! And, of course, this results in scraping off a non-zero amount of the paint I put on this morning. π ...but most of it's still painted so that's something. The worst of the paint damage is on the underside, which I can still get to in order to repaint it. Tada! I will, of course, have to clean and paint the inside of that; which promises to be fun. Oh, and strip & paint the face of it that has the door on, of course. But I might leave that 'til I've pulled the door off and repaired/re-made it, because it's suffered quite badly from The Rot. Then, three hours of tin-bashing, heating & forming, welding, grinding, more bashing... and we finally have the nearside-front rear wing put back on! It's only partially welded in place, the rest of it's just tacked for now, and I've just hosed over the welds with the zinc primer for ... I don't know why I did it, really, I'm only going to end up taking a bunch of it off when I grind them down. Makes me feel better, I guess? No it's not pretty. More work to do on it, which will neaten it up a good bit; but even then it will probably still show the scars of the repair, and I'm fine with that. π Still some bashing and fitting to do in order to close up gaps before fully welding, but it's on now which is good news for multiple reasons: 1. It's not floating around for me to trip over and damage 2. Another piece goes back onto the truck! 3. It's been holding up figuring out where I can put the compressor's air supply and unloader return pipes. So now I can make the bracketry to fit those! (Just in time for me to run out of gas for the TIG welder, I'm sure.)
-
23rd Mar. Have I mentioned that my phone's white balance drives me round the twist? Anywho. Turns out, I need more yellow paint anyway. I know I said I wasn't planning on painting the side of the truck 'til I was sure about bracketry and whatnot, but I had an oopsie and my brush slipped. First coat always looks pretty grim; seems like the opacity isn't really there when brushing this stuff. I had enough in the tin to give a second coat to that centre panel, and that looks significantly better; but I suspect I'll probably be three or four coats in before I'm happy with it. And it seems to take about half a litre of paint per coat, give or take. And if I force my phone camera's white-balance to play nice, it's pretty good. And when I got back from doing that, my bolts had come in for putting the locker back on the side; so I'll have to get that in a couple of coats of black and fitted up! Hooray!
-
I have now almost completely stripped and primed the nearside! Only the locker doors to do, now. Interestingly, the paint is a lot harder to strip where it's only the yellow (and brown); where it's painted over the top of the DBG comes off lovely. Well, I guess the DBG comes off lovely, and takes the rest with it. π Just after 2pm today: And a few short hours later: I reckon, tho, that I'm only a couple of hours away from having the whole nearside in primer, which is a good thought. Less fun is the thought of having to do the front of the body, too, but I really should while it's easy enough to get at. Also some tinkering with mockup-bracketry for a tilt happened, because the more I think about it, the more it seems like a very good idea (if only to give me more space to dump stuff π), so that took up the rest of the evening. I'm thinking having it only extend over the length of the lockers, which still leaves the area around the crane exposed for working in; but provide some covered space on the back of the truck, out of the rain. Also considering having the cover made out of the same PVC tarpaulin that tautliner curtains are made of, in a similar sort of yellow to the body. I know, it's a lot of yellow in one place, but anything else might look out of place; and I feel it'd be a plausible commercial modification.
-
Speaking of making way for new paint... Technique that appears to be working the best at the moment is a hot-air gun and a wide scraper. The paint softens nicely and just peels off, rather than turning into dust and fragments. And a first coat of heavy zinc primer, after beating all the pitted spots and filler patches with the wire brush to see what happens Thankfully, none of the pitting or filler turned out to be hiding any big trouble, so I'm hoping I can blitz through this side fairly easily. Only the rearmost section of the body, and the locker doors, to do before I can start thinking about laying on yellow paint. And I'm pretty hopeful that I can get away with not having to repeat the whole process on the other side, thanks to it not having been painted over with the mystery brown paint. 'course, I'm also still undecided on whether (and how) I want to do a tilt, which would then mean I need to add mounting points for that before painting... Would be nice to have a covered portion over the back, though. Maybe I'll just add the brackets, then it doesn't matter if I can't make my mind up.) While I'm waiting for next week's paycheck, so I can pick up the new welding torch and some other assorted bits (New nuts & bolts for the locker I removed, in particular. ...a locker which I need to give a coat of black paint, come to think of it.), I'm giving serious thought to attacking the insides of the lockers with the powered wire brush and hoover... Clean them up and get them at least in primer, because I'm sick of everything being a shower of rust flakes all the time, especially into wet paint! Will have to get a bucket of white paint for the locker internals, too, when I can. (Lockers are a lot more useful when painted white. Especially if there's a light fitted! Now there's an idea...)
-
Thanks! I have plenty of stuff to get side-tracked into, but these things are sent to try us. π I'm extremely excited by the idea of getting it done; even though I'm slowed up by health troubles. Best I can tell, it would have been towing a QF 25pdr; entirely likely it would've been doing so for training purposes more than anything. (I uncovered the remnants of a marking on the front of it -- and I wish I'd known it was under there, or I'd've been more careful in stripping it back and maybe found more of it -- that I'm now about 95% sure is a Royal Artillery red over blue flash with a flaming torch overlaid.) The differences over the standard cargo variant are detailed in Supplement No. 5 of EMER WHEELED VEHICLES F172 (issued in, apparently, May 1962.) Indeed! Most weeks, it's all I can do to survive through work; but I've got an appointment with the rheumatologist upcoming, and hopefully can start coming up with some answers even if not solutions. Good to hear that parts do still keep coming up! I do enjoy having a rummage through what's available, but I'm not on facebook (As annoying as it can be, sometimes, since so much stuff is siloed within its digital walls.). Thankfully, I'm fairly sure I'm out of the woods as far as needing panels; everything else I need to do should -- and this is where I curse myself, I'm sure -- be a case of relatively simple panel repair and letting in new metal. As far as exterior-facing cab metal goes, I have: a small patch to make underneath the passenger side cheek vent (this will take some shrinking work) the back corners of the cab (basically the rear portion of the front wings! And I have both of those where I cut them off, and just need to let in new metal again before reattaching.) the roof (Which is a bloody teabag. But I think I can do it in small sections, with relatively simple forming.) The rest of it is mostly structural parts that won't be seen unless you crawl up under there, and I'm painting all of that black anyway! π
-
Still taking short bursts at it; I've started rebuilding the rear corner panel for the passenger side which is coming along quite nicely when my welder plays nice. There's something screwed up in the torch that even a new liner didn't fix, so I've got a new welding torch on the shopping list, and in the meantime I'm using the TIG. More metal-forming and welding to do yet before I get it to the stage I can hang it on the truck, but it's all progress. Did take a trundle down to the unit to drop off more workshop equipment (nothing too fancy, just a proper bench grinder because it's a real pain getting things done without one.) and will myself into poking at something, while I was still capable of standing; which turned into scraping and peeling paint π The really big news for today is that thanks to that, I have finally got confirmation of something I've been pretty confident I was right about. So, I took the little body tag off the nearside to let me clean up that little bit behind it to make way for new paint... And on the back side of it, I found some magic words stamped in! TRACTOR 3 TON FA 4x4 RLW CODE NO 43490501361 This not only confirms my suspicions of Field Artillery conversion; but IMO also puts a line in the sand as far as date of conversion, in the form of the vehicle code number using the system that -- according to sources -- was phased out by VESPER from 1964. So, the mystery timeline gains another data-point!
-
Also, for your viewing pleasure, the timelapse of me signwriting the other side of the boom. I did lightly screw up by misreading my notes, and using the wrong spacing for some of it. And I also drew my baseline for the "MAX" a bit crooked, but these things happen! And that's things up to date!
-
Late October 2 hours of stripping... Then I got to the bit behind the locker on the nearside, and noticed a crusty bit. So I tapped it with the hammer, and to absolutely nobody's surprise, it went scrunch. So I thought "Oh, I'll just cut that bit out and fix it" and before you know it, it escalated... It overlaps with the back edge of that locker a good way, and wasn't painted before it was assembled, so I figured there's no point in fixing it as it was -- especially since it appears to have been a panel added in the truck's commercial life, based on there being no sign of any DBG underneath the paint -- and instead I could cut it off level with the back of the locker and eliminate a rust-trap. Like so! You can see there's DBG on the portion that forms the outside of the locker, so that's not been monkeyed with; but it looks like when the body was chopped about, they overlapped this bare steel plate onto the locker and then painted everything they could see when they were done. Still needs some tidying up at the top edge, but it'll do for now. 10 November Well, for whatever reason, I thought I'd tackle that front towing eye beam. It took some heat and violence, but I got the towing eye off it, and that really does let you see how bent it is! While I had the torch out, I figured I'd extract the fittings from the compressor... Inlet from the unloader (top fitting) is 3/4BSP (the other end of the elbow is that funny fine-thread that the rest of the air piping used), compressor's outlet (lower fitting) is 1/2BSP. Thankfully, both of those are dirt-common, so replacement pipes shouldn't be too difficult to get. After wrapping the torch back up, I eyed the coupler and thought "I should paint that". Don't know why, but that's what I did. And that got me warmed up enough to tackle making the repair panel for the bottom of the vent in the passenger footwell! While I was muddling around with seeing how everything lined up, I started getting very annoyed with the passenger door swinging shut and eating me. Well, I've got just the thing for dealing with that! Only the inner end of that welded on, for now, because I still have to tweak the step around to close up some of the gaps to the door; but it stops the door from bashing me, so that's good! While we're in the footwell, I threw the floor panel in to see how it all fits, and mark out the missing bolt-holes. A couple of days later, I decided to do a bit more paintbrush-waggling... Then, having overexerted myself, that was me done for walking... It was about a week later before I could next get down there to waggle a paintbrush again! Hmm. This air-tank's in the way... Out it comes, and let's hit everything with the wire wheel and sandpaper before spending some theraputic time with the paintbrush... Plenty more to do, yet, but at least I've hit the stuff where it's easier to get at with the locker out. This truck absolutely needs a good wash, there's so much grot built up everywhere... A few days later... More paint-brush waggling? Don't mind if I do! I also got the bottom of the vent-duct welded in, which has turned out quite nicely. And I've marked out the locations for the holes for the little toggle lever that controls the vent; so here's hoping I've got it in the right place! Then, for a giggle, and because I was tripping over it a bunch while painting the boom, I hung the nearside front wing on the truck. 15 November More air pipes? Sure! This footbrake valve is replacing the built-in valve from the brake servo, seeing as that does appear to be missing parts. Seeing all that crawling around on the floor hadn't crippled me enough, I thought I'd go on to tackle the offside side marker lights! So that's two marker light brackets welded onto the body (out of the 4 total), and also the offside rear wing, because I leant on that and reminded myself that it wasn't actually attached to the body any more. The marker lights on the offside are spaced the same as the ones on the nearside, even though they don't have to dodge any lockers. It's just pleasing to know they match. Lights wired and illuminated, even though not all of the brackets are welded on yet. Then Friday got 5 hours of surprise overtime tacked onto it, thanks to someone driving a loaded 8-wheeler down a farm-track and nearly laying it on its side in a field. Clocked off at quarter to 11 that night, and was definitely feeling the effect of the extended work week. There was no tinkering time on Saturday, either, because I could barely move by the time I'd left work... Sunday, however... It's good, but it's definitely missing something. Something like that. I'm still a little miffed with the two 'A's being different, but it's certainly not bad. Anyway, then I decided I needed just a little more This was rather more perilous to paint! Back to more mechanical matters, time for a little pneumatic action. Relay valve and park quick-release valve for the trailer connections. Yes, the QRV will be mounted properly at some point!
-
October 2023 Remember how I said I wasn't sure how I was going to tackle that side-marker light that was going to end up out of place? Yeah. That's a lot of work for a side-marker light, but... for one, I can clean and paint a lot of stuff I couldn't get to before! and two, doesn't this look good: I've done a lot of measuring, I'm pretty sure that I have room for that locker to fit back in and that I've drilled the holes in the right place to move it over where I need it to be; but proof of the pudding, and all that. A couple of days later, I finished up the rearmost exhaust manifold. It's certainly not instagram-worthy rainbows n stacked dimes, but I didn't have a lot of room in which to make this merge. It fits, but only just... This does mean, however, that Phase Oneβ’ is complete, and Phase Twoβ’ can begin. Unfortunately, I didn't have the room available to use the flexi bits, so there is the risk that the manifolds end up straining something and cracking, but that's just how it's going to be. Sacrifices made for style, I suppose. And that all fits in here... There will be a support bracket, with a rubber doodad, eventually. However, in the meantime... And that's 80% of Phase Twoβ’ done. The exhaust now runs back to where the previous silencer was. Following on from that, now that I'm not blocked from the radiator install, I had to fix the radiator! It's solid enough. It then received lashings of black paint to protect it from all the grot. And that leads us into... With the radiator in and -- after a quick emergency run for more hoseclamps -- all the hoses complete, I filled it with water and chased out the few inevitable leaks. But now there's a full cooling system, I can run it for longer and find out what else doesn't work. The longer run pointed out a few things: I needed exhaust gaskets Starter needs a heat-shield really badly The engine cover is going to need some insulation, too. (The back of the engine hump was unpleasantly hot to the touch by about 10 minutes in.) It sounds real good! Tach doesn't work. Investigation required. More adjustments needed... I also made a start on running pipe for the air system, as well as hunting down antifreeze (Just in time, too; because by mid-October it was already getting to -1 on that industrial estate! Mind you, after a few minutes running that engine, the air temp sensor -- currently draped by the gear lever -- was reading 25Β°C. I suppose it's like the song goes, "She's not too cold in winter, but she cooks me in the heat") Did some other checking of sensors and things while I was poking around, and I seem to have gained an occasional loss of RPM sync at or below 700rpm; but maybe I clobbered the sensor bracket while I was wrestling the radiator in, and it's getting a marginal signal. Bodywork also continued, with excavating more rust-flakes out from the inside of the front 'cheek', and sloshing rust-killer in there to try slow down the misery.
-
21 September 2023 Fresh off crippling myself with a lot of walking on a trip to London (No, I didn't walk to London, but there was a lot of walking while I was there!), I had a short task list: Get more welding gas. (Ouch. It'd gone up 50% since last time.) Get the 1/2UNC bolts for the gearbox, and get that bolted up solid. Re-resealed the PTO cover on the gearbox, and re-refilled it with oil. Adjust the clutch linkage rod so that the pedal actually works the clutch, now that the gearbox was in and the clutch disc can't fall out. So, I mentioned in the previous post that I'd ordered bolts based off the measurements of the stud in the bellhousing. It turns out that stud is 1/2UNF. The other three bolts, however, are 1/2UNC. Having at least the nut meant that I could stab the gearbox into place and leave it there while I went on my jaunt to London to meet up with friends, safe in the knowledge that it wouldn't just fall out. On my return, and armed with the proper bolts, I could finish installing the gearbox properly. And seeing as I was already laying on the floor down there, I fiddled about with the little magnetic pickup switch I was going to use for my reverse light switch -- hence the hole I mentioned I drilled in the side of the gearbox, previously -- but unfortunately the angle of sensitivity was a bit too much so it was active the whole time it was screwed into the gearbox. (I ended up replacing it with a common plunger-type switch.) It's a Vauxhall/Alfa/etc part. Easily replaceable should I need to. And seeing as I was already scrunched up in an agonised mess near the gearbox, and the gearbox was in, it seemed only reasonable to put the top cover on! It's such a fun fishing game! Got to plop it on from up top after removing the floor panel that the gear-levers stick through, and hooking it down and around to the top of the box. Then, your assistant has to hold the top cover level and ensure that the tang on the bottom of the gearstick lands in the slot in the selectors while you finish feeding the gearstick down. ...if you don't have an assistant to help you, just feed it down from on top, plop it down onto the gearbox, then climb down to crawl under the wagon and try to lift the lid back up because the sealant has already grabbed it; then with your arms squeezed into a nice tight space, try to hold the gearstick upright and get the tang into the selectors while lowering the lid back into the sealant. Repeat three times until it all lines up just right, and bung the bolts in. Check you can select gears before fully tightening the cover, just in case. Refit the floor panel you took out, and: Tada! Three sticks again! And at that point, with the gearbox back together, it'd be rude not to check if it worked, right? So might as well connect up the propshaft! With that, a quick test was in order. Just a quick one, mind. Put the truck in 1st gear, bump the starter, truck rolls forwards: Check. Dip the clutch, truck rolls back to its original location: Check. And, while we're at it, do the reverse lights work? Of course they do! Never had a doubt! Great success! Now I only have to finish the exhaust (At least the bits that are significantly easier to do with the radiator out for access.), repair that bracket on the radiator, refit the radiator and fill the cooling system with coolant/antifreeze, chase all the leaks out, move all the junk from under the truck, get it out far enough to put back wheels on it, and I can drive it round the industrial estate! Chopping and welding ensues... And more welding... Which eventually results in this wiggly mess... There'll be enough room to squeeze a pair of 2" diameter pipes in through there, but it's going to be tight. This is all self-inflicted because I wanted the swoopy shiny exhaust pipes. π€£ But even though they're nowhere near complete, they're at least pointing the exhaust away from my wiring and whatnot, so we could make THIS happen:
-
With September fast approaching (that last photo being from the 28th of August), the next big thing was getting the engine in. After all, wouldn't want to miss my self-imposed deadline, now would we? In the dying days of August, Pedals drilled and tapped for grease nipples, at the pivot shaft. The brake pedal appears to have some sort of fibrous bushing in it, but the clutch pedal is just the plain cast-iron bore on the shaft. There are oil-holes drilled into the pedals already -- I just reused those existing oil-holes but drilled them out to take a 1/4UNF grease nipple -- but they were packed solid with grot. Then there was just some ends to put on ground cables (N/S Chassis ground to main ground lug; Engine ground to main ground lug.) and ran an Anderson socket out to the N/S, too, underneath the spare wheel carrier; makes it a little more convenient to put a charger on, what with there being a door and a battery-box lid in the way now. Also useful for jumpstarting stuff, too, I guess? September 2023 The big day! Big tidy-up. Moved a load of wheels out of the way, packed tools up so I could close the locker I was using as a table, generally shuffled stuff about and swept up; all to make a clear path for the main event: ... dragging a very heavy engine around the workshop This was the most nerve-wracking part... taking the turn with the off-camber out into the yard. An hour passed between this pic and the previous. That's how frustratingly-slow things were going, at this point. I got the back end of the engine fed into the engine bay, and slowly scooted back... then the bellhousing hit the front diff. Apparently my second build of the stand was somehow ... shorter? I suppose that means there's room to add casters if I decide I need to keep it around. Once the bellhousing hit the diff, things started to get really sketchy. ... like, really sketchy. Jack the whole stand up on the trolley jack until I could push a board under one side; jack it up a bit further until I could push a board under the other side. Repeat until it was sitting high up enough that the engine cleared the bellhousing. Shove, bar, and drag with ratchet-straps until things start to line up. Occasionally bench-pressing the bellhousing upwards a little bit to line boltholes up enough to get bolts through. So close! And, another hour later... At this point, the rear mounts have all their bolts in (though not tightened yet), and the front crossmember is supporting the weight of the engine; though I still needed to dig up the bolts that hold the front mount in. Hence the little block of wood under the front of the engine. But, this was a major milestone. I set myself the deadline of having the engine in by the start of September; well, it was the start of September, and the engine was in. Still needed to think about what to prioritise for next steps, but it included getting the engine mounted solidly, putting the clutch in, sorting the exhaust headers that I didn't think about before building, so on and so forth. I certainly slept well that night! The Next Day... With the engine fitted into the truck, and now with all the mounting bolts tightened (Other than the front ones, anyway.), I decided to stick the various manifold bits on just for a laugh. They fit better than I expected! Now, admittedly, my expectations were "not at all", what with me having forgotten about the existence of the front axle while building them, so there's that... Looks pretty good, eh? ...except it doesn't bolt up to the head, because the bottom of it is hard against the top of the diff casing. But the good news is the front half bolts up lovely! But points directly at the diff cover. It's to keep the diff oil warm, in cold climates, y'see! I also hooked up the various electrical plugs and the power & ground leads, and by that point could crank the engine over from the button on the dash. My warning lights for oil and alternator weren't working yet, and that was next on the list as far as electricals go. The oil warning light turned out to be a stuck switch. The alternator warning was a little more involved, in that I'd cut the wire to extend it when I relocated a bunch of wiring so that it didn't pass in front of the engine (All of it runs behind, now that I know better, y'see) ... and I'd just never reconnected it. With those two items fixed, and having chopped the manifolds down so they could be bolted up and at least keep hot exhaust off the wiring and whatnot, I refit the original inlet manifold just for testing purposes. Though, I'd mislaid the throttle linkage (I've since found it, but I'm not using it anyway once I've got my own built.) so I didn't have anything connected to the pedal, nor did I have a fuel supply readily to hand, but I wanted to hear it all work so... Marvellous, I've not killed it. The following day, I made a start on putting the clutch in. Man that thing's heavy and awkward, especially when you've got to feed it up into the flywheel housing. But, I succeeded in getting it hoisted up and onto the dowels; new bolts had been procured prior, though I'd totally forgotten to get a set of imperial allen keys, so I didn't get the clutch entirely tightened down for a little while after. I did, however, get the front engine mount installed and bolted up; though, with new bolts because I couldn't find the old ones. The originals are 7/16UNF, and I just got 7/16UNC ones instead. I think I did later find the originals, but I didn't think it was particularly worth faffing around prying the engine up to put the old bolts back in... I also managed to notice a bit of an oil-leak at the pushrod cover on the side of the engine, where I'd disturbed my gasket when I relocated my ignition coil-pack. (The last thing I did before Christmas this year was strip all of that back off to re-seal it. Hopefully successfully...) 12 September Clutch fork was refitted, and the gearbox was finished up (Mostly just drilling and tapping the top cover mounting flange where I'd repaired the broken casting.) before I capped it off with a CV boot to act as a gaiter for where the gear lever goes into the top cover. At which point, thinking I was ready to go, I discovered I could not locate my gearbox mounting bolts, despite knowing I'd put them in a labelled bag. So I measured up the thread on the stud that sticks out of the bellhousing, and ordered some to match that. (This turned out to be a mistake.) Well, unable to put the gearbox back in, I thought I'd at least have some fun running the engine. So I stuck a length of radiator hose on the bottom inlet, and filled it with water, as a total-loss cooling system. Which is when I discovered I'd not sealed or tightened the top of the thermostat housing, so it all started leaking out and when I ran the engine it sprayed it everywhere But that was an easy fix, so I got a few more runs with the lash-up total-loss cooling system, since I didn't want to fit the radiator before I'd sorted out my exhaust manifolds. I did some playing around with ignition timing, including building up a tune based off the mechanical advance curve listed in the manual, and a gentle approximation of the vacuum advance curve data I could find. It didn't like that very much, so I reverted back to the 'soft' initial table I'd made up. It will need tuning properly by someone who knows what they're doing, but that's for the future; for now, it's set up with safe values so that I can run it without damage.
-
August 2023! So, I pick up those funny aluminium stubs that have been kicking around, and decide I'm going to do something with them. And the plan is something like so: Now, that's not fully completed. There's still some noodling I've got to do with mounting points for hold-down bolts and whatnot, but that gives you a general idea. Process is pretty simple: drill a hole on the wonk (approximately 35 degrees), open it out with the burr and fettle until the injector bung sits just nice, gas weld it in, clean up all the flux and knobbly bits of excess aluminium, and it's good. (ish.) I still need to trim the excess of the injector bung where it sticks into the manifold, and make sure that's all nice; but that can be done at a later date. As mentioned, I still have additional mounting points that need to go on and whatnot; but I have to see where all of that lands, before I start making them permanent. I have a plan: it's a dynamically adjustable adaptive plan using flexible reactive feedback mechanisms. (Namely, I have a rough idea of where I'm going, but I'm otherwise making it up as I go along. π) -- August continues to rumble on, and so do I. Though, not as quickly as I'd like. That's a little more closed-in, though not completely done. But there's enough that's done enough to get a quick coat of paint, and get a better idea of how it's all going to look. And the engine hump, too! Now, painting the driver's footwell was never going to happen all the way; but at least I could use up some paint, on the bits I'm fairly sure I'm not going to have to cut or weld... And once that'd dried, I decided to spend some time in the Captain's Chair. Rumours of there being "vroom-vroom" noises can neither be confirmed, nor denied. With the passenger's step/sill done enough that the door's not going to be in the way, I might as well refit it. Every part that's off the floor, and on the truck, is one less part to trip over! The step/sill bit is ... definitely lower than it should be. I think this is partially because I've not got the structure at the front edge to fully locate it, and also because I've stepped on it a few times before I got it welded up and must've squashed it down without noticing. No matter, that can be fixed easily enough (I hope!) with some strategic prying before finishing out the structure that holds it all up. I'm not too worried about perfect door gaps, because they seem to be all over the place on RLs anyway, but I'd like it to be better than that. Something far more pressing that needs to be sorted, however, is this: I forgot about the retaining stop/catch/thing. So I'm going to have to burn some of my new paint anyway to get that fitted back in, but it's not the end of the world. Following on from that, more engine-bay painting ensued! Followed by the weilding of rivnuts, to give me somewhere to attach wiring to! Originally, there were little steel tabs that folded over the wiring to hold it in place, but they've broken off after countless times of getting caught on my clothing as I climbed in and out... More painting followed, using up the rest of the paint in the pot: Also, some pondering about the slots in the dash. When I got the truck, they were filled solid with what appeared to be either sealant or thoroughly perished rubber; but they look in the right sort of place to be used as defrost vents for the windscreen?