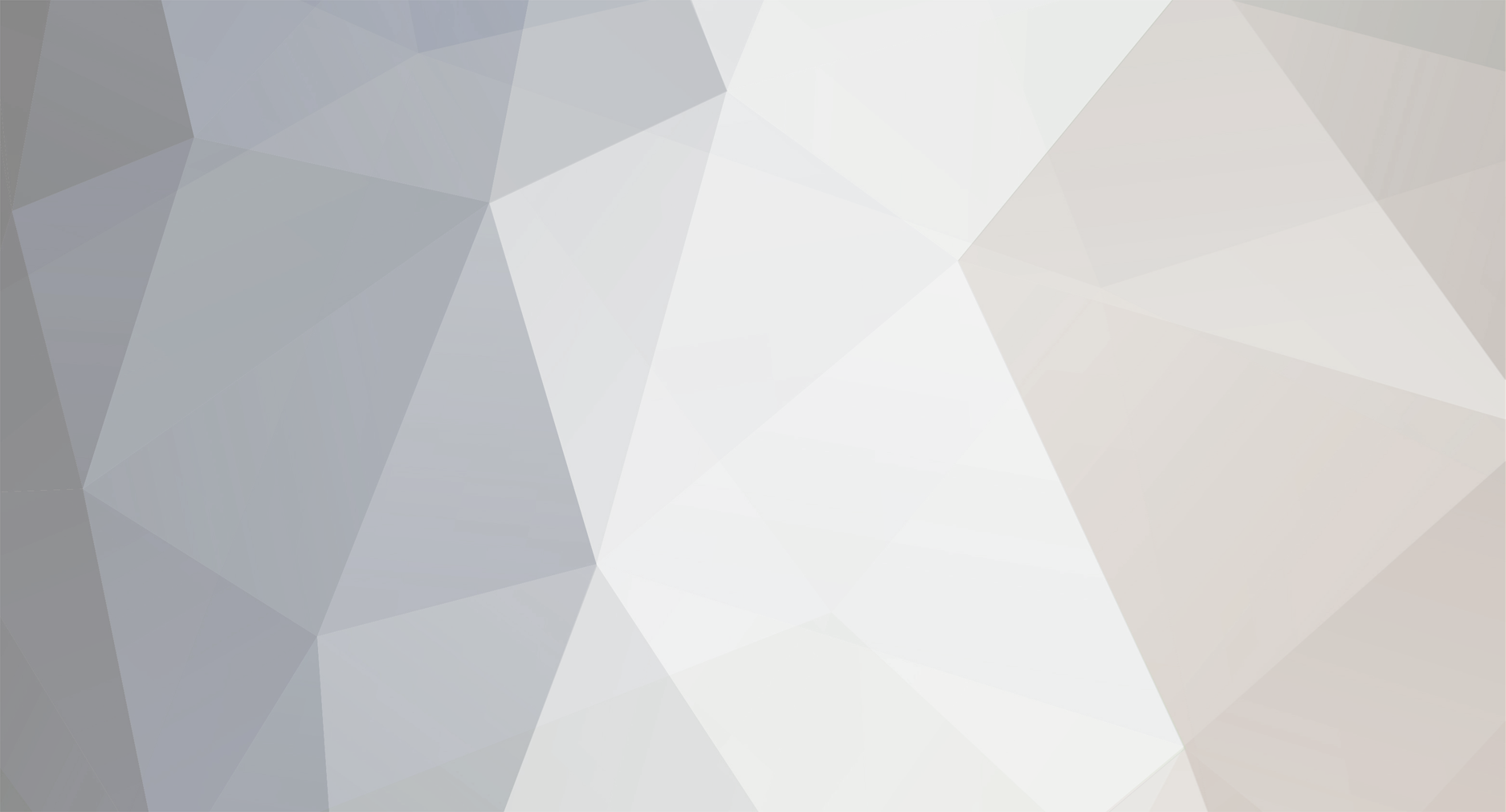
Barney
-
Posts
70 -
Joined
-
Last visited
Content Type
Profiles
Forums
Gallery
Blogs
Events
Articles
Store
Downloads
Posts posted by Barney
-
-
I brought some kiln dried 4x2" from a builders merchants, twisted all over the shop after only a few weeks.
-
What was a British Pound worth in 1930?Value of £1 from 1930 to 2017£1 in 1930 is equivalent in purchasing power to about £62.13 in 2017, an increase of £61.13 over 87 years. The pound had an average inflation rate of 4.86% per year between 1930 and 2017, producing a cumulative price increase of 6,113.29%.
-
Very nice Steve but rather OTT for just a breather, me thinks.
-
Steve,
Just a quick thought on making a setting tool.
Piece of flat plate with mandrill screwed in, upright on edge of plate with stop screw a 90 degs to mandrill, adjust stop screw and pull bits out until they touch the stop screw and tighten the grub screws.
I guess that the tool originally had something like this but it had been lost in its 50 plus's years of life. We used a depth micrometer.
John
-
Hi again Steve,
This video shows a similar valve re-cutter and will give you some idea what the tool was like but this one appears to have only one cutting bit but then the seats are smaller. It is a lot more substantial than the one we had and it didn't align with the follower bore.
John
-
Hi Steve,
Herewith, a rough, very rough, sketch of the vintage valve re-seating tool that I'm sure you could easily make.
I understand it came to us from a closed down garage that specialised in horizontal stationary engine generators, Blackstone and the like, that were in many of the big Lord of the Manor houses in Norfolk; a few were still around on the early 1970's when I joined the garage but I never worked on one.
If the valve face is off centre then the more cutting bits the better, so I have shown four but it will be very fiddly to get all four to cut, although even if those that don't cut just act as a guide that will be helpful.
I remember that we had to turn up guides and mandrills for some engines.
Hope this helps.
John
-
1
-
-
Hi Steve again,
Some further thoughts on the three way cutter.
The mandrill was held tight in the guide by a nut on the bottom and there was a very fine thread on the top end.
The cutter was slid into the mandrill and then a ball thrust washer and knurled nut gave the pressure to cut but only hand turned.
It was fiddly to set up so mostly only one bit actually done the cutting.
We also had a similar tool, also hand turned, for replacing burnt out inserts and for fitting new steel inserts on seats that were too deep to recut, or were too deep after recutting.
This tool only had a single cutter but came with an assortment of different size heads and it was necessary to choose one that didn't leave too much overhang on the cutter. Again, easy to use and cut brilliantly.
John
-
Hi Steve,
In the garage we had a three way fly cutter for seats larger than the VibroCentric could do and this was sufficient for the occasional extra large seats we got. The heads were cast iron in those days so cutting a new seat was easy.
Easy to make, it just used round HSS bits held in with two grub screws so no need to cut square holes.
Lorry looking great now.
John
-
Sorry, duplicated post.
John
-
21 hours ago, andypugh said:
But would a 1934 British car be using Unified threads? (Unlikely, Unified threads were invented during WW11)
I feel you are overthinking this, Andy. Singer would have chosen the thread on the basis of material to be used, the duty that the component is to perform, and ability to manufacture. Any comparison with a thread designation decided upon by the Americans nearly twenty years after the Singer components manufacture is can only be pure coincidence.
-
1" 16-UN - Unified Extra Fine Thread, which is used for special purposes.
The flank angle is 60°. -
Moving on one from Richard Farrant's post may I suggest that having found the area of the leak by pressurising the tank that you re-slosh the tank and pressurise it again with the slosh in the leak area. Hopefully this will force the slosh into the hole and seal it.
John
-
3
-
-
Sorry, re-thought this post and decided it might cause more problems than it would solve so decided to delete it.
-
Hi Steve
I have always set the ring gaps to those that I was taught during my training and have never had any problems.
For bores 2 to 3" - 2 thou per inch of bore pro rata
For bores 3 to 4" - 3 thou Ditto
For bores 4 to 5" - 4 thou Ditto
Sorry but I can't give any info on ring temps.
Hope this helps.
John
-
Congratulations to you all on getting the engine running.
Re; Tight engine
I am supprised to see that they still make 'Running In Oil' which should help ease a tight engine. Morris Lubricants supply what they call 'Classic Running In Oil' available in stright grades 30sae and 40sae.
Re; Acceleration problem
I seem to remember that there is a spring controlled govenor on the camshaft, is this coming in too soon and stopping the engine accelerating; weak or soft springs prehaps.
John
-
1 hour ago, 8_10 Brass Cleaner said:
Dad would be delighted. I can't wait to see it run.
Out of interest, the war dept wagons will have been required to be registered when new in the heavy motor index. Were they registered by the maker in Hampshire?. Were they HO xxxx? Or perhaps OT xxxx?
I understood the Caernarfon number was in the post 1921 series? From memory dad got the copies of the registration documents from the record office. Do you have them?. The wagon had been bought by the quarry immediatley post war.
According to the Chiltern Vehicle Preservation Group website the origin of the CC registration is
CC - Bangor (Caernarvonshire) and ran with a prefix letter to 1974)
The Old Classic Car website says the CC reg ran from Jan 1904 to Mar 1934
John
-
Steve,
I found this supplier for copper tube in a selection of wall thickness. The 1 1/4" tube is available in 6swg, almost 4mm, 10swg, approx 3mm and 13swg, approx 2mm. I don't know anything about the company and have no connection with them.
http://johnhoodandcompany.co.uk/materials/copper/copper-tube
Hope this may help if you have to go for a heavy wall tube.
John
-
37 minutes ago, andypugh said:
It is possible that you have under-estimated the wall thickness of the part on the other lorry. Thick-wall tube is far easier to bend without buckling. Get some 1 3/8 solid copper bar and drill a 1/2" hole down the middle :-)
Many moons ago in the plumbing trade thick wall copper tube was known as Soft Copper Coil and was available in sizes from 1" up to 3" o/d, if I remember correctly. It was used for underground water mains and came in a coil which you unrolled along the trench. With the advent of plastic underground pipe I don't know if this is still available or if you could by it in short lengths. Someone like Grahams Plumbers and Builders Merchants or Alreco non ferris metal suppliers might be able to help.
John
-
Steve,
You have got the right idea except that the wooden formers are not strong enough to contain the sideways expansion of the tube, they need to be made in steel with a groove that is about 1/4" deeper than half the diameter of the tube. The former needs to be a good tight fit on the tube.
Hope this helps. John
-
I found this video on YouTube and it gives a good lesson on brazing steel; this is the way I was taught.
You will notice that the plates are set 1/16" apart and when he turns it over you will see that the braze has formed a nice fillet and has not run down the plates.
Steve said he placed a ring of brazing rod around the joint and tried to melt it into the joint as you would do for silver solder but bronze is of a much thicker viscosity and it won't run into close fitting joints.
I remember at senior school we made a garden rake in the metalwork class. This required the round bar tines to be threaded into a length of flat bar. We were instructed to make the threads a rattling good fit because we were to braze them in. The teacher made up the spelter, as it is called, by mixing what looked like chips from brass that had been turned in the lathe and borax into a paste. I can't belive this was all that was in the mixture but when spread over the top of the thread and heated to a dull red with a Flamefast town gas and compressed air torch it melted into the joint without any problems.
John
-
I have noticed that Bright Drawn Mild Steel angle has a sharp angle in the bottom and on the top edges, Black Mild Steel is rounded.
Merry Christmas all.
John
-
Rubbish post, sorry.
John
-
Steve,
The tank looks really Grrrrrrrrrrrreat.
Just a thought, considering that the paint had difficulty adhering to the outside of the tank how do you propose to clean the inside of the tank to get the 'Slosh' to stick?
What would worry me, if I was doing this, is if I couldn't adequately cover all the surfaces inside the tank would the petrol get behind the coating and start to peel it off and block the pipes or filters.
John
-
Steve said
I had a go but could not get the solder to run. This could have been the solder which, I believe, was of the lead-free persuasion. I don't have much confidence in that either. Can anyone offer any suggestions on using this combination?
Just some general information.
Most plumbing fluxes now come in two types, potable water and heating systems/general purpose. Potable plumbing solder is lead and cadmium free and uses silver as a replacement which raises the melting point by about 15 dgs. I find that it joints brightly cleaned copper very well but no hope of a good joint when soldering ferrous metal with potable flux. Leaded solder wire 3mm o/d (general purpose) is still available on eBay.
Fluxite and Laco are good all round rosin based paste fluxes which works well on ferrous metal and for tinning things like braided vehicle earth straps and big lugs. Rosin solder is not corrosive so works well on electrical joints and PC boards that cannot be washed clean after soldering.
Bakers No3 liquid flux is acid based and brilliant for ferrous metals but is not recommended for non-ferrous metals. Note, wash the finished joint in water to remove all traces of acid.
I prefer Fluxite but I like to use Bakers for work where it is not possible to get the components as clean as I would like. Fluxite, Laco and Bakers No3 are also available on eBay.
My old school metalwork teacher spent some time in the REME in North Africa during WW2 and he said that when they ran out of flux they used Camel Piss; is there a zoo near you?
John
WW1 Peerless lorry restoration
in Pre WW2 vehicles
Posted
I tried to cut some new 3/4'' boiler sight glass tube for my steam loco oil feed but had no success so took it to some gem stone suppliers and cutters at Lenwade, Norfolk and asked them to cut it. They cut five before they made a good job of the two I needed, the glass just broke away around the outside edge and although they would have sealed on the O rings ok the cutter was not happy with his work. The cutter said that cutting glass is more difficult than cutting diamonds because it is so brittle.